Innovative Industry Meeting:
International Polyurethane Conference 2015
A location steeped in history, 15 technical presentations, a top-class political discussion and the ceremonial opening of the Hennecke TECHCENTER: This year's International Polyurethane Conference drew more than 200 representatives from the polyurethane industry to Bonn and Sankt Augustin. Participants were invited to this established industry gathering by the Specialist Association for Foamed Plastics and Polyurethanes e.V. (FSK) and Hennecke GmbH, bringing together a range of expertise and a strong drive for innovation. This was a suitable occasion for Hennecke GmbH to hold the official opening of its state-of-the-art application technology center.
The former plenary chamber of the old parliament building in Bonn provided the numerous representatives of the national and international polyurethane industry with a fascinating setting for exciting presentations and lively discussions from the very first day of the event. One of the highlights of the morning was the presentation of the new Hennecke foaming plant type KTT for producing refrigerator doors, which has been in operation at the Giengen site of BSH Home Appliances GmbH since the beginning of the year. The novelty in this plant is an innovative concept in which the curing places are arranged vertically and disconnected from the curing line.
Appropriately for the old parliament building, the afternoon began with a political debate. Here Ilka von Boeselager (CDU state parliament faction), Prof. Ernst Ulrich von Weizsäcker (Co-President of The Club of Rome), Johannes Remmel (North Rhine-Westphalian environment minister) and Dr. Dietmar Kopp (from the German Federal Ministry for Economic Affairs and Energy), among others, discussed in an engaged and well prepared manner, how much environmental law the processing of plastics and polyurethane in Europe and in Germany is tolerating in global competition. The final highlight at this special location was the awarding of the Innovation Prize "Polyurethane" by the FSK. Among the winners this year was Evonik Industries AG, Essen. The speciality chemical company was recognised for its innovative pultrusion process. In this, all stages in the process of a conventional sandwich construction and of the pultrusion are consolidated into just one step. The prize for the "unusual application idea and employment of a material" went to the electrically co-powered penny-farthing of BASF SE, Ludwigshafen. This bicycle was intended to show the benchmark at which, plastics, including PU, will be set to in future. Mara Freigang, a graduate of interior design at the University of Applied Sciences Mainz, got to enjoy a prize in the category "Idea and Design" for her modular storage system "eGo".
The second day of the event took place in Hennecke's company premises at St. Augustin. The highlight of this was the ceremonial opening of the new application technology center TECHCENTER, where Hennecke is pooling its research capabilities into a total area of more than 1,000 square metres at its company headquarters, and is thereby significantly expanding its developmental capacities (see page 10). Adjacent to the new application technology center, the visitors were informed about the project InCar®plus in a specially provided show truck.
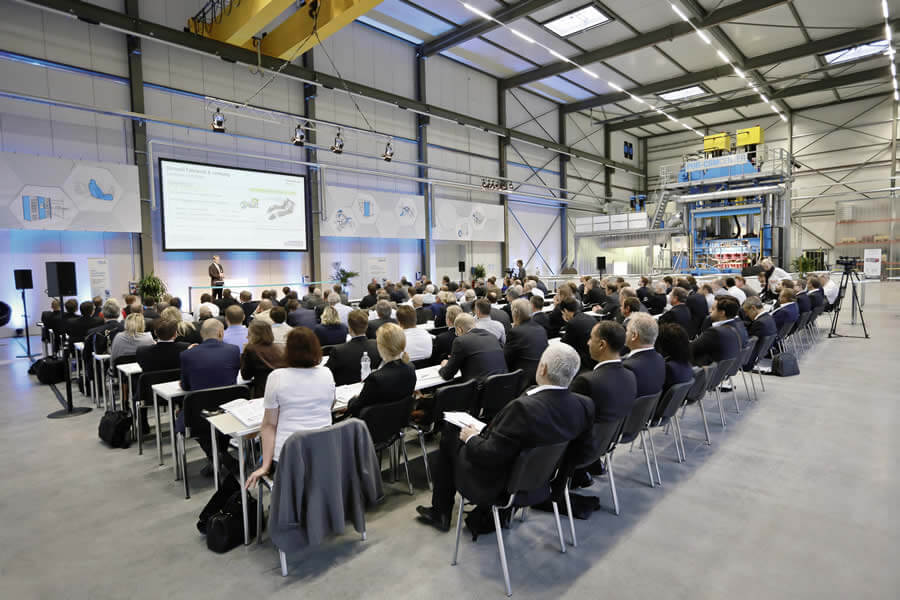
The realisation of future expectations and challenges in lightweight construction can only be achieved through joint innovations based on creative research, development and the implementation of combined thermoplastic and reactive systems. A long-standing partnership is a basic requirement for this, beginning in R&D with joint application technology optimisations, through to customer service. The successful work together with Hennecke confirms this way for us.
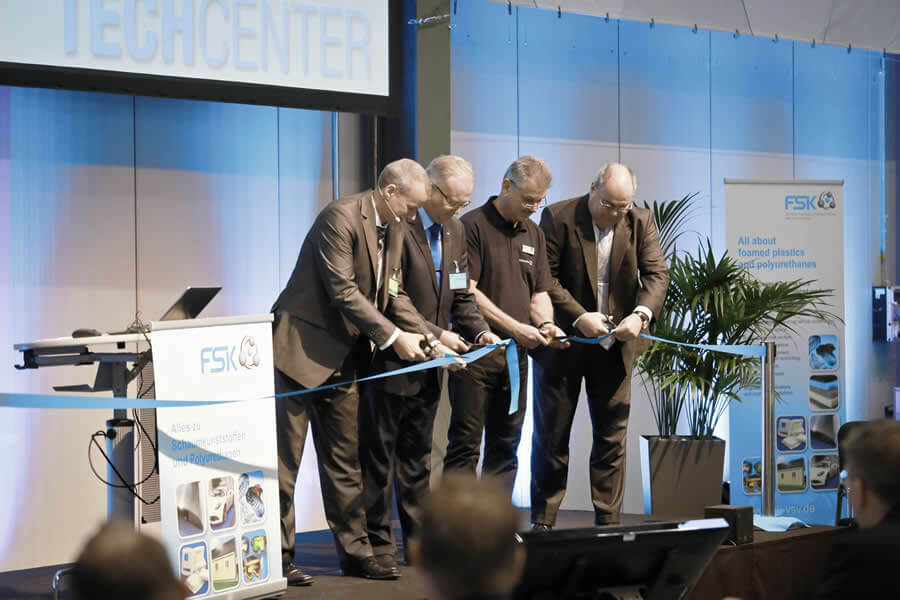
The new TECHCENTER has really impressed me. I am of course delighted that one of our machines stands here as a visible sign of our good work together. Now we can advance the area of high pressure RTM and the combination of polyurethane and injection moulding even further.
This project with ThyssenKrupp Steel Europe AG is substantially optimising efficiency in the fields of drive, chassis and bodywork through the use of intelligent lightweight construction. On display were a wide variety of lightweight parts, including among others, a car door with a steel-plastic-hybrid construction. In his presentation Andreas Keutz, from Research and Development at Thyssen Krupp Steel Europe AG, explained how the innovative door concept was put into practice in cooperation with Hennecke.
Along with other interesting presentations from the companies ENGEL AUSTRIA GmbH, MAGNA STEYR AG and Audi AG, which primarily focused on solutions in the lightweight automotive construction, the participants were also able to experience live demonstrations at the opening. Among them was the production of a trunk floor for a mid-range vehicle using PUR-CSM spray technology as well as the production of a fibre composite component in the INSITU process (see page 12). In addition, the factory tours inside the Hennecke production facilities were especially popular. On this occasion, the participants gained a detailed insight into the production of mixheads and the final assembly of metering machines, among other things.
With the new TECHCENTER we can now test and implement ideas for steel-plastic combinations in the field of automotive lightweight construction, faster, and more efficiently.
In his welcome speech, Rolf Trippler, the Managing Director of Sales at Hennecke GmbH, traced the historic arc of the company from its foundation to today. Jens Winiarz, Head of Sales for CSM and new technologies, presented the innovations and milestones. His presentation showed the multifaceted nature and innovative power of "Fascination PUR" in an impressive way. With the new TECHCENTER, Hennecke has now reached another milestone in its company history.
"One of the trends that has become apparent in polyurethane technology in recent years is the search for new combinations of processes," explained Jürgen Wirth, Head of the TECHCENTER. "In our new application technology center, a range of state-of-the-art machines from highly diverse fields of PU expertise is available in order to create new processes and products together with our application specialists."
With the new TECHCENTER we now have the opportunity to considerably reduce our time-to-market.
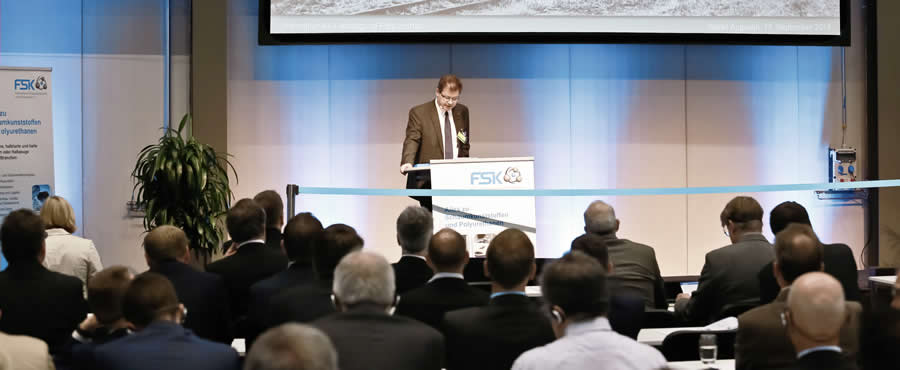
Guarantor of the technological leadership in the PU sector: the Hennecke TECHCENTER
At Hennecke's new TECHCENTER, customers will be able to draw on state-of-the-art polyurethane processing technology for all applications across a surface of more than 1,000 square metres.
Hennecke offers innovative systems and technologies that are geared to meet customer requirements in all conceivable applications. Without intensive and continuous research and development, this would not be possible. From the machinery and plant manufacturer's point of view, it is thus logical to establish a new application technology center at Sankt Augustin headquarters which places the focus on specific customer requirements on the one hand and in-house research on the other hand. Apart from product development and product optimisation, the comprehensive service portfolio of the Hennecke TECHCENTER comprises process development and raw materials testing under close-to-production conditions. Moreover, training, demonstrations to customers and matching tests will be carried out in the state-of-the-art application technology center. The process and machine technology available in the TECHCENTER covers high and low-pressure metering machines with up to six components and a large output range. It also includes plant technology for all processing variants in the area of polyurethane spray moulding (PUR-CSM) as well as systems engineering for the production of fibre-reinforced structural components (HP-RTM). In addition, machine and plant technology for various injection, moulded foam and insulation foam applications is provided to the customer.
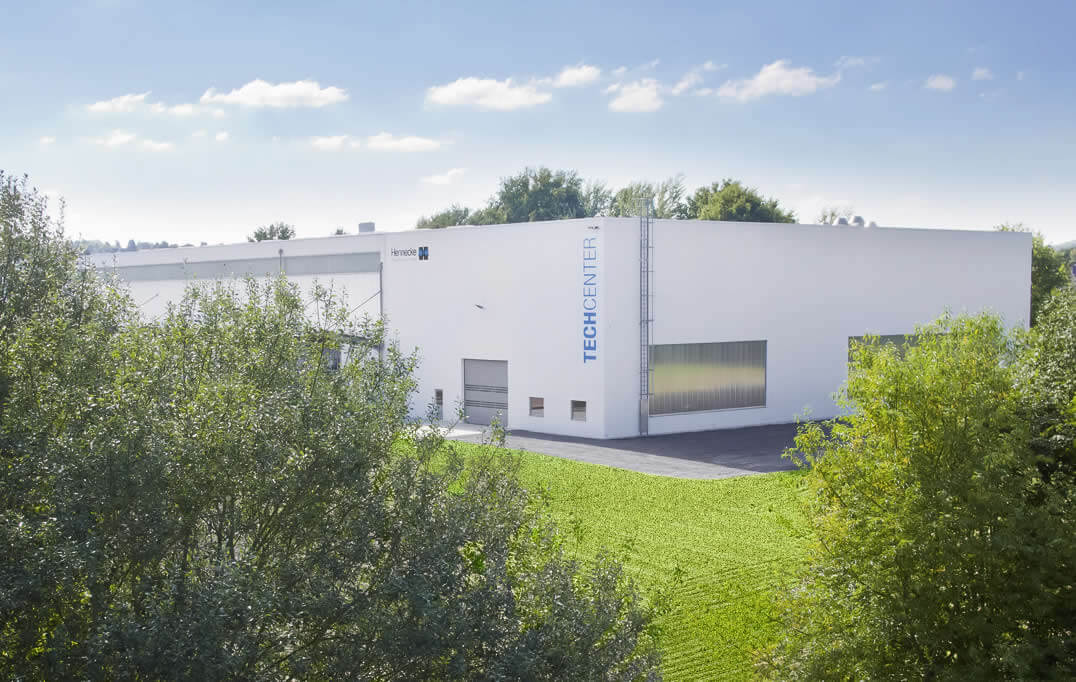
Process and machine engineering at the Hennecke TECHCENTER
We can demonstrate the following technologies at the Hennecke TECHCENTER:
- Processing of rigid, flexible and integral skin foams, elastomers as well as epoxy resin systems and reactive thermoplasts
- RIM, RRIM, SRIM, PUR-CSM fibre composite clearmelt®, Skinmelt, Sprayskin and HP-RTM applications
- Hand or robotically operated pouring of reaction mixture into open and closed moulds
The following machine and plant technology is permanently available at the Hennecke TECHCENTER*
- High-pressure reaction casting machines for a reaction mixture output of 10 to 1,500cm³/s (outputs below 10cm³/s are also possible depending on the application)
- Metering machines with up to six individual components that can be temperature-controlled, evacuated or gas-loaded
- Processing of all common blowing agents (plant modifications are possible depending on vapour pressure and flammability of the blowing agents)
- Processing of fillers in the batch technique with a carrier component
- Low-pressure reaction casting machine with up to eight individual components (four main and four additional components)
- Heatable casting table for elastomer processing
- Mould carrier with clamping plate dimensions of 1,600*1,140mm (clamping force of up to 60t, max. opening stroke of 1,900mm, +/-30° swivelling)
- Handling robot with a carrying capacity of 130kg
- Spray booth with robot for small parts with dimensions of approx. 1,000*1,000mm
- PUR-CSM-CENTER** (Polyurethane Composite Spray Moulding) with press (3*2m clamping plate dimensions, clamping force of up to 600t, large-format spray booth with handling devices, mobile handling robot with 130kg carrying capacity)
* If required, other machine and plant combinations can be demonstrated in the Hennecke TECHCENTER by arrangement.
** PUR-CSM process variants: PUR-CSM-SANITARY for solvent-free reinforcement of bath tubs and shower trays, PUR-CSM-PREG for manufacturing extremely high load-bearing lightweight composites and PUR-CSM-SKIN for realising high-quality polyurethane spray skins.