Fit for exterior components in large-scale production:
PUR-CSM PREG
The issue of lightweight construction cannot be ignored by any automotive manufacturer today. The number of innovative composite parts in vehicles is growing year by year. The automobile supplier Fehrer Composite Components has developed for the new "smart fortwo" a new lightweight roof in a sandwich construction. Thanks to very short cycle times and using an optimised overall process, Hennecke machine technology is making sure that the lightest vehicle roof construction currently available on the market can be produced economically on a large scale.
Hennecke's expertise gained from more than 90 high-volume production lines for load floors and sliding roofs in paper honeycomb sandwich structure all over the world is being concentrated in the first exterior sandwich component which is mass produced. The innovative lightweight roof developed by Fehrer Composite Components for the new smart fortwo consists of a material mix of polyurethane, glass fibre and paper honeycomb and is coated with a thermoplastic outer skin. It provides the same stability as the plastic standard roof of its predecessor but it is 30 percent lighter.
Compared to traditional composite parts, the individual layers are not bonded in a complex, multi-step process, but in a single operation. This so-called "one-shot process" is becoming more and more popular. Products are manufactured to be as close to their final contours as possible, and in terms of surface finish can be demoulded without requiring further processing. The part also represents a first for Fehrer Composite Components. With the lightweight construction for the smart fortwo, the vehicle interior specialist is providing an outer body part in mass production for the first time. The component is produced in the Fehrer plant in Großlangheim and delivered directly to the smart assembly line in Hambach where it is installed onto the vehicles.
The realisation of such high-quality fibre-composite components on a large scale illustrates how the Hennecke specialists manage to combine state-of-the-art processing systems, long-standing process expertise and innovative high-pressure injection technology into optimally equipped overall systems with much higher performance than conventional metering machines.
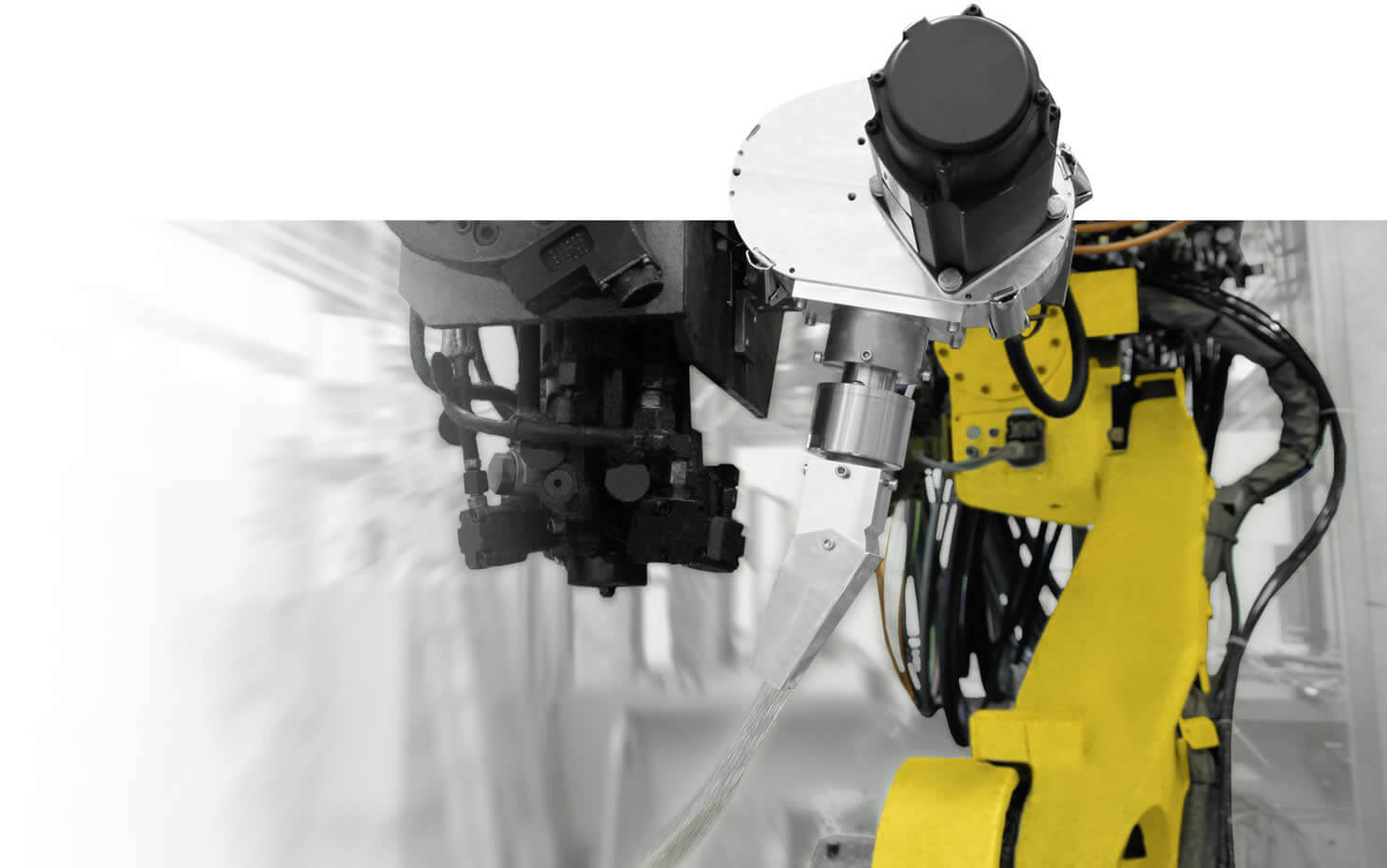