The new generation steel sandwich panel lines
Within the Hennecke GROUP, three strong brands have joined forces and pooled their expertise. The new generation of the PANELMASTER STEEL sandwich panel production line is the impressive result of combined know-how from the brands Hennecke-OMS, Hennecke Polyurethane Technology and Hennecke Roll Forming Technology. Put simply: it brings together the best of three worlds.
Global efforts are currently focusing on how energy can be used as efficiently as possible. Building insulation offers huge potential for making savings. Here polyurethane rigid foam has the lowest thermal conductivity of all insulating materials used in practice. As a result, steel sandwich insulation panels with a core structure made of PIR have long since become the standard choice for constructing industrial buildings and cold storage houses. The PANELMASTER STEEL from the sandwich panel specialists Hennecke-OMS enables continuous production of panels with different facings, thicknesses, and profiles. In order to fulfil the specific requirements of a growing market, particularly with regards to premium products made at high production speeds, the company has now introduced an extensively reworked generation of production lines.
All from a single source
For decades, sandwich panel production has been part of the core business of the individual companies in the Hennecke GROUP. Even before the merger with the present-day Hennecke-OMS, for this product line, the brand name Hennecke became the absolute standard and the Italian subsidiary a center of excellence. “For the new product generation, it was all about combining the three market leaders’ expertise and adopting a common approach to meeting our customer’s demands for turnkey solutions – one that is solid as a whole and in the detail. A stateof- the-art production line has emerged seamlessly and entirely from a single source,” says Pierpaolo Azzalin, Head of Sales at Hennecke-OMS. Every detail of the production line has been analyzed and evaluated in an intensive development process involving engineering and sales experts from the three companies.
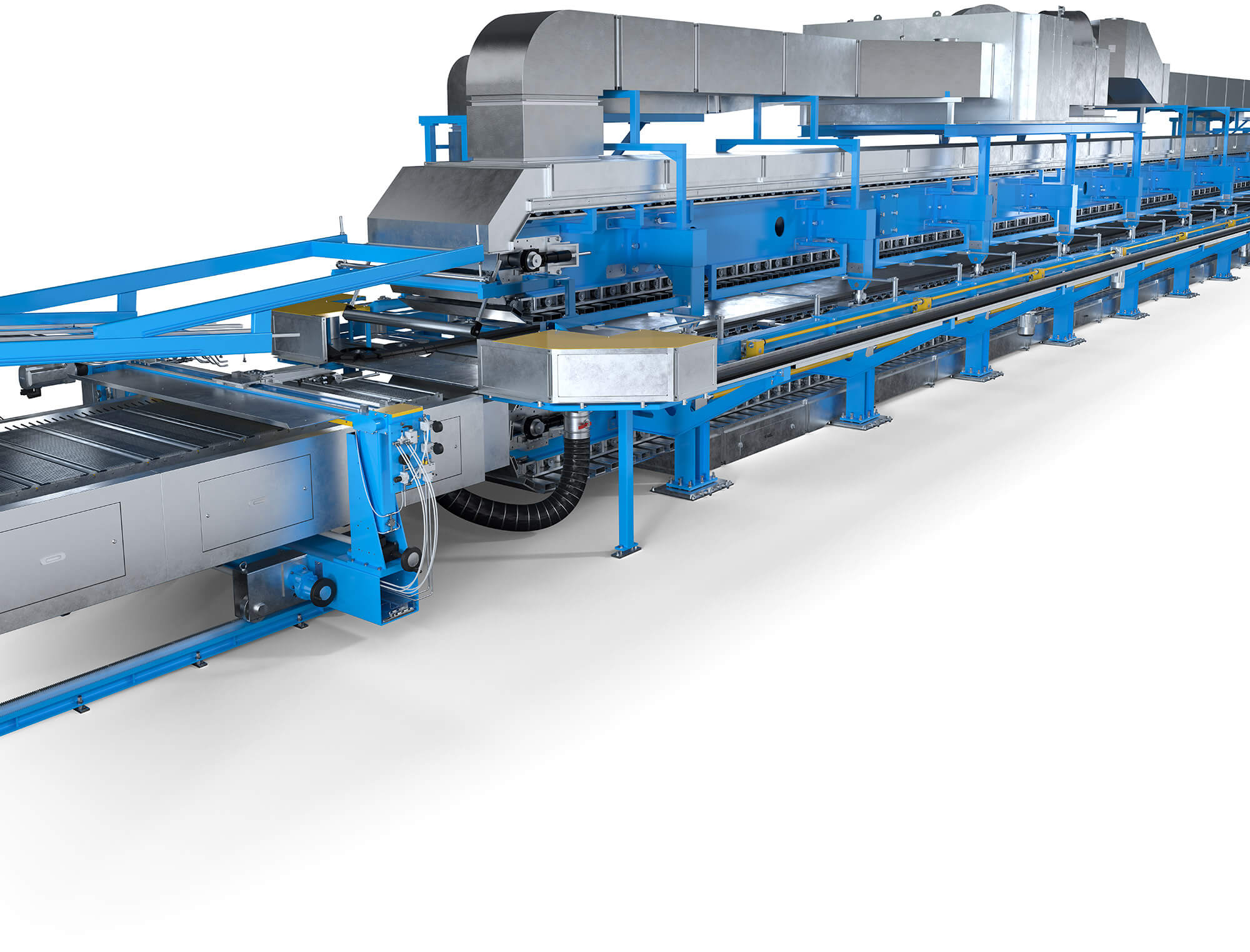
Accumulated competence for top-class quality
Hennecke GmbH Roll Forming Technology is the specialist in the upstream part of the PANELMASTER STEEL – the coil handling, and processing and profiling the metal facings. The controls also had to be reworked, a task that was led by Hennecke-OMS, ensuring that the entire line is operated with one standardized and comprehensive system. Leading-edge electronics and top computer performance ensure that the line operates with maximum safety and production adjustments can be made quickly and mostly automatically.
A brand new centerpiece
Particularly the middle section of the production line, the centerpiece of the PANELMASTER STEEL, is proof of how the combined expertise from within the Hennecke GROUP takes the new generation to the next level. The formidable expertise of the Italian Hennecke GROUP subsidiary can be clearly seen in the double plate conveyor, which is crucial for product quality. The highly precise and robust elements have been manufactured inhouse. Expertise came from the German headquarters to enhance the side conveyor guides and develop an energy-saving heating system for precise process temperature control. “Here we combined the greatest expertise in raw material preparation for high-pressure processing. This is a prime example of how excellent production lines can be improved even more by pooling specialist knowledge,” says Andreas Fischer, Senior Sales Manager Hennecke Roll Forming Technology. The next section of the approximately 150-meter PANELMASTER STEEL line includes the fully automated units for cooling, stacking, and packing the sandwich panels. Here the panels are examined, assessed and combined with one another to achieve maximum quality, efficiency, and cost effectiveness.
Reliable, efficient, and cost-effective
The new generation of production lines pays off especially for the customer. The existing line comprising different, independent areas has been reconsidered and redesigned as a whole. “This brings many customer benefits,” explains Andreas Fischer. “The operational sequences are all synchronized with one another, which ensures seamless, continuous production with no downtimes.” State-of-the-art technology and electronics provide savings in both energy and raw material use. In addition, the specialist knowledge about the entire production line is completely in-house and virtually all component parts have been developed and manufactured within the company. This means great production reliability as well as independence from suppliers and external factors. The customer profits here from having one single contact for all enquiries and concerns.
“The first steel sandwich panel lines from the new generation have been constructed and delivered to the customer, where they are already proving their worth,” reports Pierpaolo Azzalin. In the future, he expects around six lines to be produced per year.
THE NEW GENERATION HIGHLIGHTS
- Continuous coil handling and preparation, processing and profiling of the metal facings
- Complete equipment for metering, storing, transporting, and monitoring the raw materials and additives
- Well-planned arrangement of individual units for the customers’ most diverse product specifications
- Proven high-pressure technology for the foaming portal and mixheads ensures uniform cell structure and efficient raw material yield
- High-precision and robust double plate conveyors and innovative side conveyor guides for consistently high product quality
- Energy efficient heating and cooling
- Comprehensive control system including panel management, process data recording and graphics for evaluation and analysis