Fit for the fourth generation
Premixing station LAMBDAMAT for the exact metering of blowing agents in a batch process
With the LAMBDAMAT blowing agent metering device, Hennecke offers a precise and reliable premixing station for blowing agent loading of the polyurethane components in a batch process.
At the same time, the LAMBDAMAT is mainly designed for the use of HFO formulations. With the phase-out of older established blowing agents by many users, the fourth generation of blowing agents is now moving into focus.
Hydrofluorocarbon blowing agents (HFCs) are expected to be phased out worldwide by 2030 at the latest, based on the Kyoto Protocol. Some countries already prohibit the use of these blowing agents in certain applications. Hydrofluoroolefin blowing agents (HFO) - also called fourth generation - are used as successors. They have very good lambda values, have no ozone depletion potential (ODP) and a very low global warming potential (GWP).
In order to achieve the desired property spectrum in the production of hard and integral foams, it is necessary to condition the raw material systems used by adding blowing agents in various applications. The LAMBDAMAT is able to process all common blowing agents for the production of hard and integral foams. The HFOs that are environmentally friendly in terms of their ODP and GWP play a key role here. The LAMBDAMAT metering units process the blowing agents in a batch process. The proportion of blowing agents in the component stream can be adjusted with extreme precision and to a largely optional ratio. The specific amount of blowing agent can be adapted flexibly to the respective application.
As users no longer have to rely on existing formulations from polyurethane suppliers, usage of the advanced premixing station quickly pays off and the processor can respond flexibly and promptly to changing production requirements. In addition, certain pre-mixed raw material combinations do not have a very long shelf life and their property spectrum deteriorates with the storage time. With the LAMBDAMAT, the processor can pre-mix the raw materials as needed and process them directly. In addition, by using the new HFOs, users can achieve far better insulation properties than is possible with traditional HFCs. This creates additional savings potential due to lower component thicknesses or ensures effective optimization of product properties with the same component strength. The HFOs provide another advantage for integral foams, for example for gearshift knobs and steering wheels in the vehicle interior. The blowing agents ensure a very high-quality surface of the components.
The LAMBDAMAT machine frame is ergonomically designed and extremely easy to maintain thanks to its perfect accessibility to all components. Thanks to the plug-and-play design, the LAMBDAMAT can also be integrated into customer-supplied production solutions at any time. The integration is also planned as a stand-alone solution in tank storage and third-party systems. The LAMBDAMAT has state-of-the-art control and drive technology in combination with a practical operator panel for convenient retrieval and input of machine parameters. Using the graphics-capable touch display and a robust foil-laminated keyboard, users can control and monitor all system components with just a few operating steps and comprehensively log selected functions. This way, manufacturers can trace up to 200 metering operations, for example.
The machine control system also allows the provision of different formulations or mixing ratios. This means up to four different concentrations of blowing agents are available to the production, without additional investments in other metering devices. This is used for example when different components with different properties are produced in parallel. In addition, the machine control system also has interfaces for integration into higher-level production systems if required.
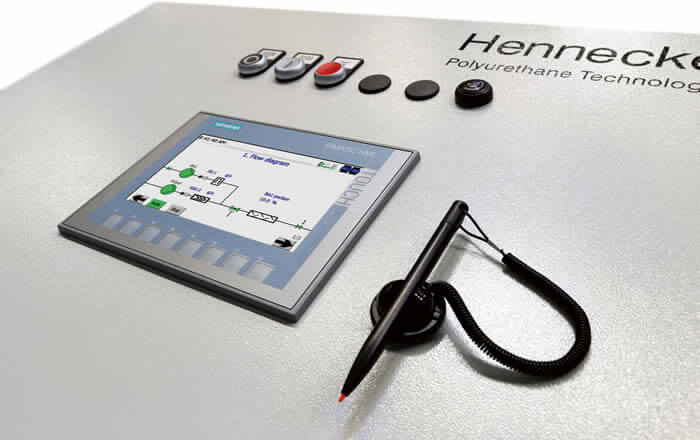
The LAMBDAMAT is also an alternative for manufacturers with lower production volumes, for whom the use of pentane as blowing agent is too costly. Pentane is a proven technology as a CFC substitute. The blowing agent also produces very good lambda values, has no ozone depletion potential and a very low global warming potential.
It is inexpensive, but also highly flammable. However, by using Pentane Process Technology, processing of the blowing agent is possible without any risk. However, the fire protection equipment is associated with costs and is usually only worthwhile for larger quantities. If you want to produce components in smaller quantities that should have the same or better properties as those produced with pentane, the HFOs now offer a real alternative. Although the new blowing agents are more expensive than pentane, the investment cost is considerably lower than when using pentane-process technology, for example.
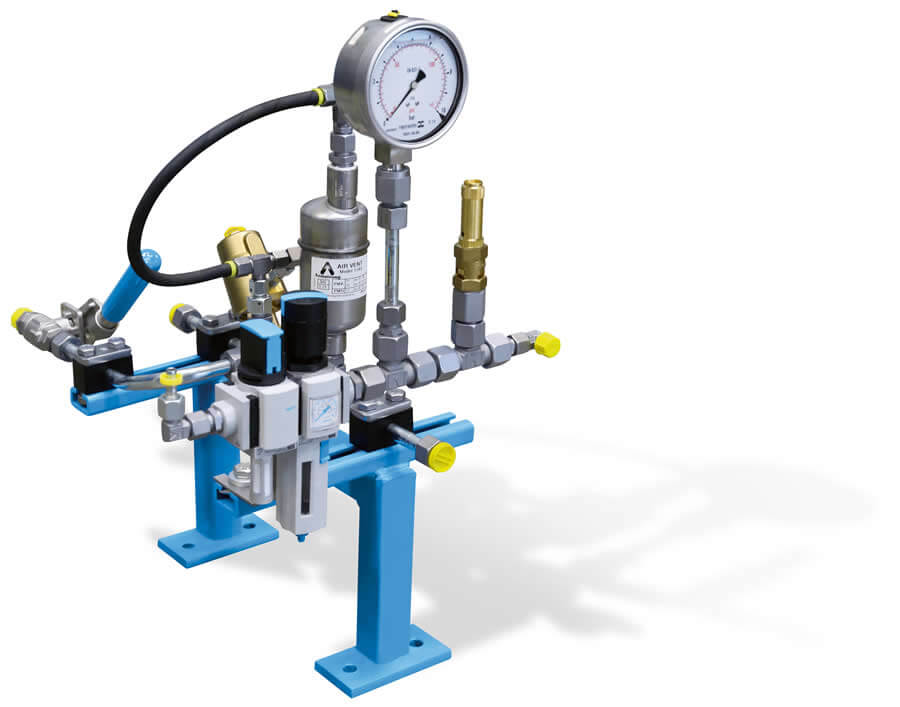