All from a single source
Manufacture of polyurethane cable grommets with Hennecke high-pressure metering machines
Cademy GmbH based in Ennepetal, Germany, specializes in turn-key manufacturing solutions for the manufacture of polyurethane cable grommets in vehicle wiring harnesses.
At the beginning of 2018, the company built a new facility. The heart of the new building is the laboratory with a Hennecke HIGHLINE metering machine.
Each vehicle has a main cable set that runs through the entire vehicle. Even in a compact car it can consist of up to 1.6 kilometers of cables weighing up to 70 kilograms and up to eight meters long when rolled out. This highly complex product is mainly manufactured manually by specialized suppliers. Delivered just-in-time to the vehicle manufacturer, the highly complex lifeline of modern vehicles is usually installed in a single operation.
Openings between the passenger compartment and the engine compartment are particularly critical areas in the automobile. The biggest challenge here is to ensure a watertight and gastight installation of the cable harness. An exact and geometrically accurate foaming of the cable harness using polyurethane ensures completely reliable sealing and high durability at this critical position.
This so-called cable grommet is longitudinally watertight due to the initially liquid polyurethane, which penetrates between the cables. This way, no water can enter the vehicle interior even under extreme precipitation. The grommet also assures a completely secure positioning of the cables, since the individual cables and the grommet are permanently connected with each other in the foamed cable harness.
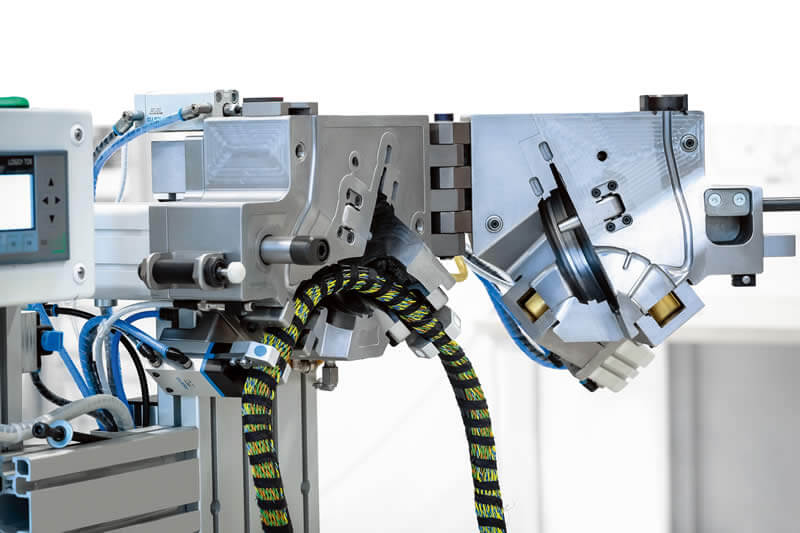
The mould for foaming the cable harness provides the outer shape of the cable grommet. It is designed so that the transition between the grommet and opening is completely tight and the harness is firmly positioned in the vehicle body. The cable grommet is often used to pre-form the bulky cable harness, for example to permanently fit a 90-degree angle. Between two and four different cable grommet moulds are used for each harness for one vehicle type. Cademy supplies the complete manufacturing solution for the production of polyurethane cable grommets to automotive suppliers. These customers of Cademy supply all well-known car manufacturers worldwide. The company's expertise lies in the development and production of the very specific moulds that are used to foam the cable harnesses, as well as in the offer of delivering turnkey production solutions as a general contractor.
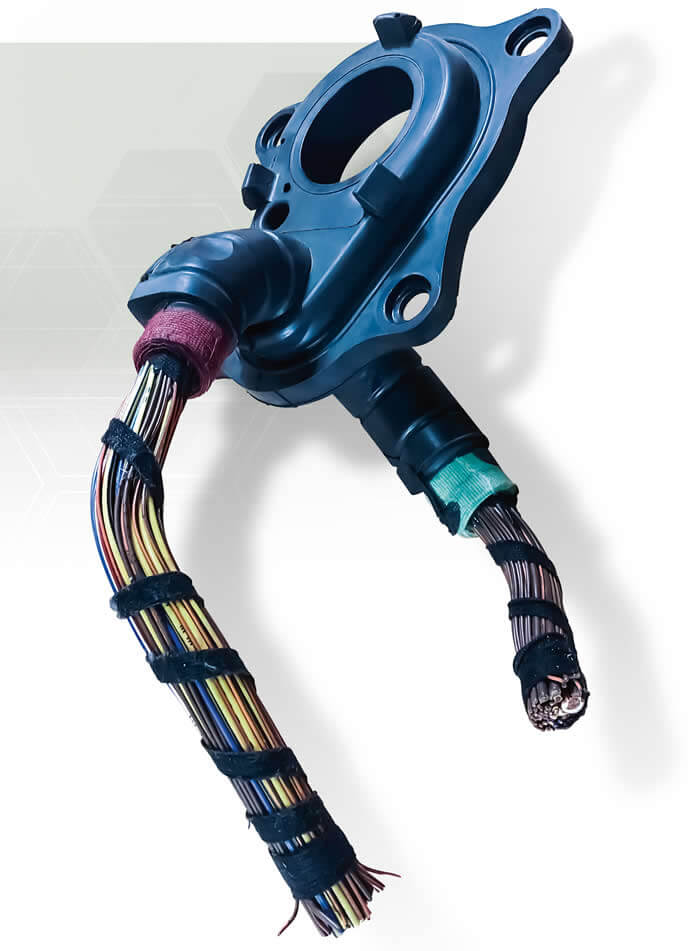
Interview with the CEO of Cademy GmbH from Ennepetal, Michael Faupel
INNOVATIONS:
Mr. Faupel, what is the historical background of Cademy?
Michael Faupel:
The origins of the Cademy GmbH go back to the beginning of the seventies. Sohl Modell- und Formenbau was founded in 1972. In the mid-eighties, the company started to develop and manufacture moulds for cable foaming with my father Walter Faupel as manager. In 1997 I started my own business with my own design office. Over time, my father and I began to work very closely together. Around the year 2000 we first had serious thoughts about combining the expertise in cable foaming and my design skills into a joint project. In 2003 we finally joined forces and founded the Cademy GmbH.
INNOVATIONS:
Cademy moved to a newly built factory early in 2018. What was the background story there?
Michael Faupel:
We have grown steadily step by step since 2003. We finally reached a point where the old location just got too small. Our customers' projects had grown so big that the old premises were no longer big enough. The heart of our new business is our laboratory. This is where customer acceptance of the moulds takes place. Construction and mould manufacture are located directly in the laboratory, so that these tests can now be carried out very quickly.
INNOVATIONS:
The laboratory includes a new Hennecke HIGHLINE metering machine. Why did you choose this machine?
Michael Faupel:
We are general contractors and make the selection of metering machines according to our customers' wishes. Since we deliver most of the manufacturing solutions with a Hennecke metering machine, it makes sense that this machine type is also used in our laboratory.
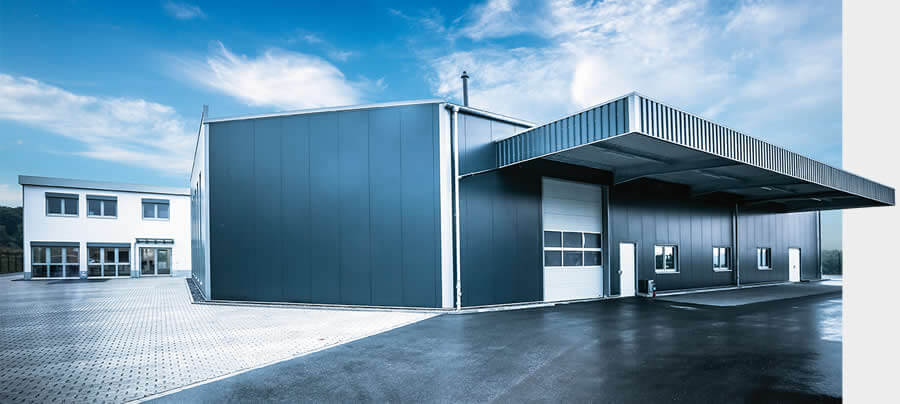