Production of load floors for Pimsa Otomotiv:
Hennecke celebrates the commissioning of the 100th PUR-CSM PREG line
Hennecke had already laid the foundation stone for the development of a pioneering polyurethane spray technology in 1998 in order to establish an efficient, modular product range from it in 2004 under the generic term PUR-CSM (Polyurethane Composite Spray Moulding). This product range implements highly flexible plant concepts in several areas of automotive and non-automotive applications. A key area of the CSM product portfolio, the so-called "PREG" sandwich load floor technology, is currently celebrating a special anniversary. The Hennecke customer and vehicle interior specialist, Pimsa Otomotiv, headquartered in the Turkish city of Kocaeli, received the globally 100th PUR-CSM PREG line and thus entered the proud group of owners that promote lightweight construction in vehicles with the large-scale production of composite products on a paper core basis.
The focus for all suppliers and OEMs on the market is on lightweight automotive construction not least due to the increasingly stringent emission standards. In addition to more efficient units or alternative drive concepts, weight is a decisive factor for the energy efficiency of all vehicles. The polyurethane specialist Hennecke identified the increasing significance of lightweight construction solutions at an early stage and is now the global market leader for PREG plant technology as a constituent part of PUR-CSM technology. The term "PREG" is the abbreviated form of the well-known Prepreg technology, whereby a glass fibre mat is impregnated in the preliminary process stages. Hennecke has developed this concept further and generated an active spray application from the pre-impregnation of the glass fibre mat, which is used immediately before the moulding process. Various aspects play a decisive role here with regard to large-scale production. For example, the Hennecke experts can rightly be proud of the globally unique self-cleaning and patented spray-moulding technology, which can also implement any desired shot interruptions and local reinforcements.
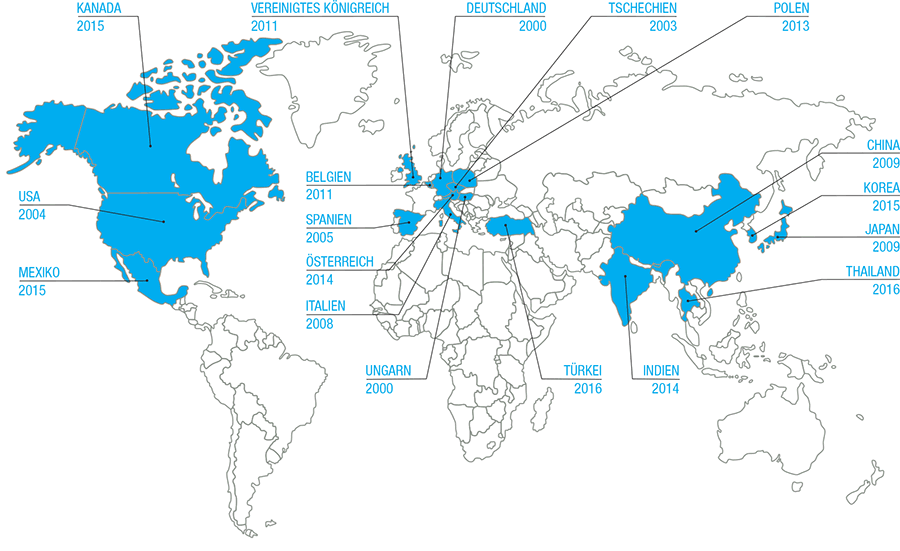
The sum of the benefits also helped to convince the Pimsa Otomotiv company, which produces load floors for large European OEMs using Hennecke technology. Pimsa Otomotiv was founded in the Turkish city of Istanbul in 1975 and was one of the first companies in the Turkish automotive industry at the time to specialize in the manufacture of products from polyurethane. Seating foam, steering wheels and armrests count among their first products. Due to the high product quality and the increasing use of polyurethane in the automotive industry, but at the latest since Turkey's entrance into the European Customs Union, the automotive supplier has grown just as quickly as its product portfolio. In 2012, Pimsa Otomotiv moved into its new "LEED Certified" factory and office building in the Turkish city of Kocaeli. With its continuously growing organizational structure and through cooperation with important European suppliers, Pimsa Otomotiv provides services for a wide range of customers in all European core markets. The current product portfolio includes, amongst other things, PU floor mats, sound proofing elements, interior and exterior trimming, door trimming, sunvisors and load floors for passenger and commercial vehicles. The quality of the products is documented by the company using the highest quality standards in accordance with the ISO standard and in the framework of high demands placed by large automotive groups such as Toyota, Mercedes and Ford.
Like many other PUR-CSM systems on the market, the PREG system technology installed within the Pimsa production is highly standardized and, to a large extent, automated. High-capacity robots place the prefabricated paper sandwich preforms in a spray booth fully automatically, using a gripper specially developed for the process. Following that, state-of-the-art mixhead technology provides a highly efficient spray coat in connection with the patented PUR-CSM spraying technology. The exact surface weight requirement for the later lightweight construction plays an enormous role in this step. Hennecke relies on the self-cleaning tried and tested round jet spray technology. In competition, the PUR-CSM technology often had to be benchmarked against standard spray applications and was always able to demonstrate a further unique selling point in the process: the homogeneous distribution of the reactive PUR mixture. This brings significant savings on raw material for Pimsa Otomotiv.
In addition to the specific quality of the end product, this represents a further competitive advantage for the PUR-CSM technology in general and the PUR-CSM PREG technology in particular. After the successful spray coat, the robots pass the components into a press. Special moulds facilitate a close contour finished part production. Often, several finished components are produced directly in one mould stroke. Cycle times of under 60 seconds therefore facilitate Pimsa Otomotiv's series applications for the mass market.
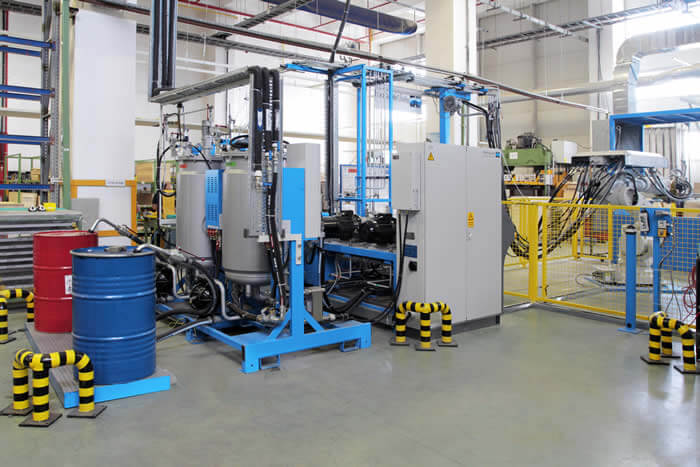
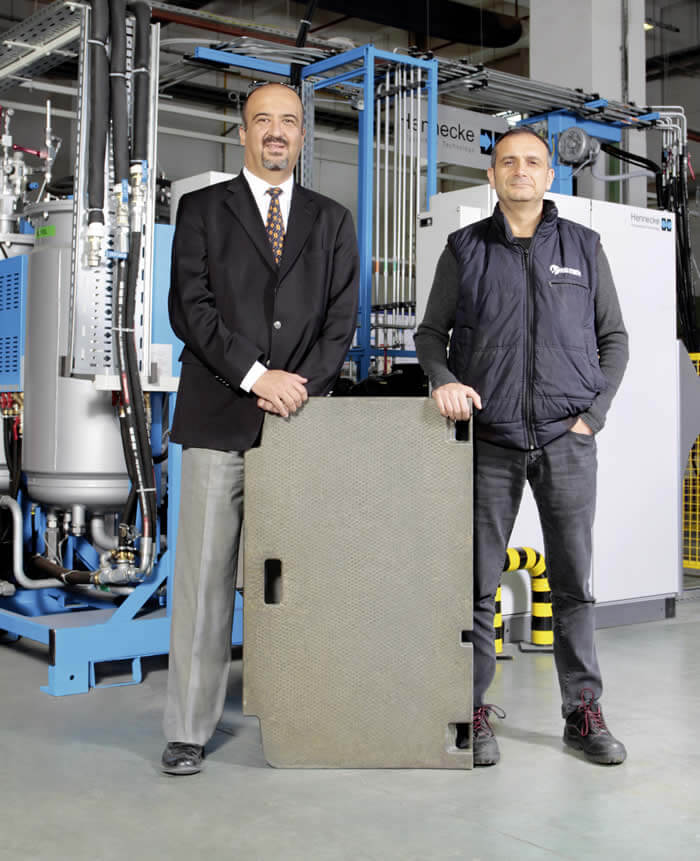
Adnan Özyegit, Assistant General Manager of Pimsa Otomotiv, is also convinced about the benefits: “When it comes to being a key player in the automotive industry at global scale just as in our case, saving raw material is a clear competitive advantage for us. In addition, Pimsa’s sustainable performance in providing the high-quality products at pricewise competitive edge through our lean and innovative approach, starting from scratch in design stage up until our products are delivered to the production line of our customers at the right time, quality and quantity make Pimsa Otomotiv stand out from its competitors. We have deeply investigated almost all relevant systems before investing in PREG technology and finally decided that Hennecke would be the best choice to conform our standards to provide the best solution for our customers. In the light of what we have achieved so far it proves to be satisfactory and reassures our confidence in Hennecke technology.”
Therefore, it is no wonder that the PUR-CSM spray-moulding technology has become established as the standard for producing load floors, parcel shelves or sun shading elements for sliding glass roofs since the turn of the millennium. “However, this does not mean that the end of technological development is in sight,” says Jens Winiarz, Head of Sales for Composites & Advanced Applications for Hennecke: “Hennecke's customers, such as Pimsa Otomotiv, will undoubtedly continue to present components in the field of PREG technology which will fully convince the industry professionals when it comes to lightweight construction.”
Like him, Adnan Özyegit is also certain that the development potential for PREG products has not yet been exhausted: “As it’s well known and respected worldwide, we’re a highly PUR oriented NVH parts manufacturer company and yet we started to divert our expertise to the composite field of applications trying to provide cutting edge NVH and trim solutions for our customers. In line with this strategy, it is for sure that Pimsa Otomotiv will produce even more high-performance PREG products in the future. As one of the leading automotive supplier in Turkey, Pimsa Otomotiv is always committed to providing innovative products with an impressive property matrix. Currently, we see numerous opportunities in PREG components.”
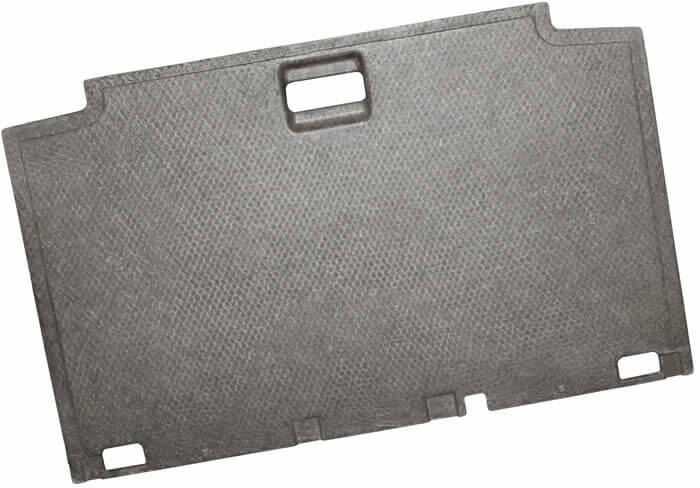
PUR-CSM PREG exterior applications
The first large-scale application for exterior components will be used in the roof model for the new "smart fortwo". The predecessor model already relied on glass fibre-reinforced polyurethane for this component. However, the PUR-CSM PREG technology was able to once again save significant weight, causing the conventional long glass fibre technology that had previously been used for this component to be discontinued. Fiat Chrysler Automobiles (FCA) were also persuaded by this benefit: The roof module for the new Jeep® Renegade is also realized in a sandwich construction with a paper honeycomb core.