Neue Dimensionen bei der PUR-Verarbeitung unter Einsatz der Hochdruckmischtechnik:
Hennecke-Mischköpfe der Baureihe MT
Polyurethan-Formteile werden in der Regel im Hochdruckverfahren hergestellt. Zur Anwendung kommen hierbei Mischersysteme, die nach der sogenannten Hochdruck-Gegenstrom-Mischtechnik arbeiten. Mit der Mischkopf-Baureihe MT verfügt Hennecke über ein praxisgerechtes Lineup hocheffizienter Umlenkmischköpfe, die völlig neue Maßstäbe innerhalb der Hochdruck-Vermischung von Polyurethan setzen.
Hochdruck-Gegenstrom-Mischersysteme wurden bereits in den frühen sechziger Jahren des vergangenen Jahrhunderts entwickelt. Das Arbeitsprinzip wurde dabei nahezu unverändert beibehalten. Die heute meist verwendeten Hochdruckmischer sind Umlenkmischköpfe, die über eine zylindrische Mischkammer und ein rechtwinklig dazu angeordnetes Auslaufrohr verfügen. Im Gegensatz zu Rührwerk- oder Statik-Mischern bietet die Hochdruck-Gegenstrom-Mischtechnik die Möglichkeit, selbstreinigende Mischer zu verwenden. Das ist ein großer Vorteil, da weder Rohstoff verloren geht, noch Lösemittel zur Reinigung eingesetzt werden müssen. Die Selbstreinigung der Mischer wird dadurch erreicht, dass die Mischkammer und alle Bereiche, die mit Reaktionsgemisch benetzt werden, geometrisch vergleichsweise einfach ausgeführt sind. Damit soll sichergestellt werden, dass sie mittels einer einfachen Kolbenstange mechanisch zu reinigen sind. Kehrseite der relativ einfachen zylindrischen Geometrie: die Gestaltungsmöglichkeiten, um die Mischkammer strömungstechnisch zu optimieren, sind stark eingeschränkt. Die Entwicklungsingenieure von Hennecke haben sich aber gerade das zur Aufgabe gestellt und im Zuge dessen die altbewährte Hochdruck-Gegenstrom-Mischtechnik komplett infrage gestellt, um einen neuen Umlenkmischkopf zu entwickeln, der bei unveränderter Selbstreinigungsfähigkeit die Mischeffizienz deutlich verbessert. Resultat ist die Hennecke-Mischkopfbaureihe MT mit Baugrößen, die von 5 g/s bis zu 5000 g/s Reaktionsgemisch verarbeiten können und dem Kunden in Versionen für Zwei-, Vier- und Sechs-Komponenten zur Verfügung stehen.
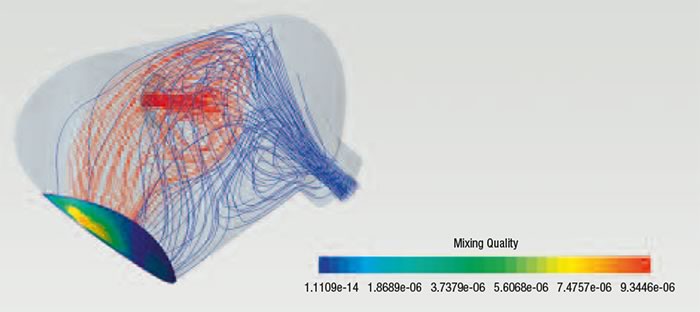
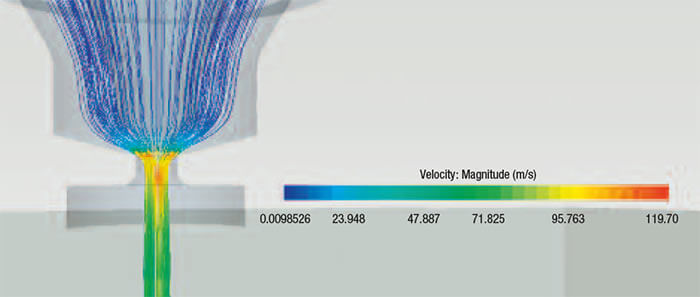
Zentraler Schwerpunkt der Entwicklung war es, bei weitgehend gegebener Geometrie der Mischkammer die verbleibenden geometrischen Freiheitsgrade zu identifizieren und wesentlich zu optimieren. So galt es beispielsweise, Parameter wie das Verhältnis zwischen Durchmesser und Höhe der Mischkammer sowie die Lage und Winkelstellung der Mischdüsen zu optimieren. Gelöst wurde diese Aufgabenstellung mit unzähligen Modellversuchen und Strömungs-Simulationsrechnungen. Unter Beteiligung des Fraunhofer-Institut für Algorithmen und Wissenschaftliches Rechnen (SCAI) konnten letztlich die Parameter so lange variiert werden, bis das Optimum gefunden war. Im Labor der Hennecke GmbH sind die Prototypen mit repräsentativen Polyurethan-Systemen unter realen Produktionsbedingungen ausgiebigen Testläufen unterzogen worden. Das Resultat kann durchaus als Quantensprung in der Hochdruck-Mischtechnik bezeichnet werden. So wurde der Gesamtwirkungsgrad der neuen Mischkopf-Generation wesentlich verbessert, was dem Endanwender gleich in mehrfacher Hinsicht zugute kommt. Der nötige Energieaufwand bei der Formteilherstellung sinkt signifikant.
Wenn man bedenkt, dass eine normale Dosieranlage zur Herstellung beispielsweise von Pkw-Sitzkissen mit einer Leistung von ca. 15 KW allein für die Bewältigung der Mischaufgabe arbeitet, versteht man auch, wie sich die effiziente Mischtechnik spürbar auf die Stückkosten eines Sitzkissens auswirkt. Aber auch, wenn die Energiekosten nicht primär im Fokus stehen, ergibt die Wirkungsgradverbesserung ein deutlich weiteres Prozessfenster, in dem ein großes Spektrum von Produkten bei höchster Qualität prozesssicher hergestellt werden kann und auch die Ausschussrate erheblich sinkt. Mit der MT-Baureihe verfügen Anwender nun über ein Mischersystem, welches den aktuellen Stand der Wissenschaft und Technik widerspiegelt.
Ein moderner Mischkopf muss selbstverständlich nicht nur in verfahrenstechnischer Sicht optimiert sein. Nicht zu Unrecht wird der Mischkopf in einer Polyurethan-Anlage als „Herzstück“ bezeichnet. Fällt der Mischkopf aus, erliegt die Produktion. Besonders deutlich wird dies innerhalb der Automobilzulieferindustrie, wo Produktionsanlagen zur Sitzherstellung beispielsweise im Drei-Schicht-Betrieb eingesetzt werden, wobei die Anlage in weniger als 15 Sekunden einen fertigen Sitz ausbringt, der wiederum aus mindestens drei Schaumzonen besteht. So ist es üblich, dass Mischköpfe in derartigen Anlagen mehrere Millionen Einzeldosierungen pro Jahr absolvieren müssen.
Die Mischkopfkonstruktion, die Auswahl der Werkstoffe und deren Behandlung sowie die Fertigungsqualität sind hier besonders gefordert. Bei der Konstruktion folgten die Hennecke-Ingenieure einer einfachen Formel: Wenig Einzelbauteile, die nur in den funktionsbedingten Bereichen feinst bearbeitet werden müssen, ergeben eine robuste, langlebige Konstruktion mit geringen Fehlermöglichkeiten und damit ein extrem attraktives Life-Cycle-Costing. So gelang es in der neuen Konstruktion, die Anzahl der Einzelteile um rund ein Drittel zu reduzieren, wobei die Komplexität jedes einzelnen Teils einfach gehalten wurde. Kern bildet das Mischkopfgehäuse mit seinen hochpräzisen Bohrungen für die Mischkammer, dem Gemischauslauf und den Mischdüsen. Dieses Gehäuse, in dem sich die Funktionsschieber im ausgehärteten Reaktionsgemisch bewegen, unterliegt der größten Beanspruchung und bildet damit die wesentlichen Verschleißzonen. Durch Einsatz von extrem hochfesten Werkstoffen, kombiniert mit einer speziellen Oberflächenhärtung und einer verschleißhemmenden Beschichtung, erreichen die Mischköpfe der Baureihe MT in vielen Anwendungen mehrere Millionen „Schuss“. Eigens zur Fertigung dieser Mischkopfgehäuse hat Hennecke in ein neues Bearbeitungszentrum investiert, um die hochgesteckten Qualitätsanforderungen zu erfüllen und die Fertigungsqualität dauerhaft zu sichern.
Um Polyurethansysteme mit der Hochdruck-Gegenstrom-Mischtechnik bei einem möglichst großen Wirkungsgrad effizient mischen zu können, müssen neben der Mischkammer natürlich auch die Mischdüsen betrachtet werden. Die Mischdüsen haben die Aufgabe, den Druck, mit dem die reaktiven Komponenten dosiert werden, in Geschwindigkeit umzusetzen. Eine optimale Mischdüse sollte die Reaktionskomponente beim Materialdurchgang demnach bei einer geringen Druckdifferenz auf eine maximal hohe Geschwindigkeit beschleunigen. So wird erreicht, dass die Flüssigkeitsstromfäden der Reaktionskomponenten eine lange Wegstrecke in der Mischkammer zurücklegen und dabei auf den Reaktionspartner treffen. Mit der Neuentwicklung der Mischdüsen für die MT-Mischkopfbaureihe konnte der Wirkungsgrad, also die Umsetzung von Druck in Geschwindigkeit, um rund 30 Prozent gesteigert werden.
Durch eine stufenlose Verstellung der Mischdüsen-Öffnung können die MT-Mischköpfe über einen weiten Austragsleistungsbereich betrieben werden. Die Umstellung von einer kleinen Austragsleistung zu einer deutlich größeren erfolgt bei nahezu konstantem Druck, wodurch Mengenänderungen wie auch Rezepturwechsel (Veränderung des Mischungsverhältnisses) extrem schnell erfolgen können.
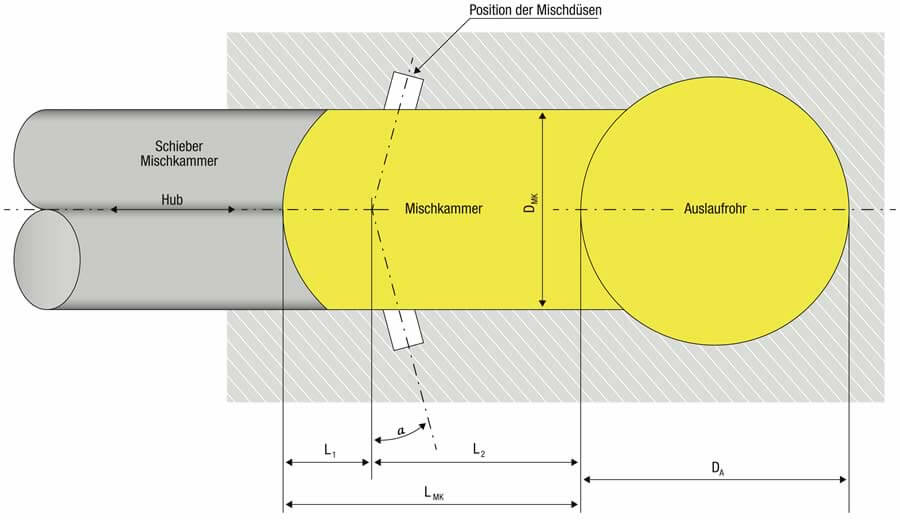
Download - Ausgabe 114 (PDF)
Zur Betrachtung benötigen Sie den Adobe® Reader®, den Sie hier kostenlos herunterladen können.