New dimensions for PUR processing with high-pressure mixing technology:
Hennecke's MT mixheads
Moulded polyurethane parts are mostly manufactured using a high-pressure process. In this application, mixer systems are employed which operate according to the so-called high-pressure impingement mixing technology. With the MT mixhead series, Hennecke has a practice-oriented lineup of high-efficiency deflection mixheads, which set completely new standards within the high-pressure mixing of polyurethane.
High-pressure impingement mixing systems were already developed in the early sixties of the past century. The operating principle has been kept almost the same. The high-pressure mixers most often used today are deflection mixheads, which contain a cylindrical mixing chamber with an outlet pipe that is arranged at a right angle. Contrary to stirrer or static mixers, the high-pressure impingement mixing technology provides the option of using self-cleaning mixers. This is a major advantage, as neither raw material is lost, nor is solvent required for cleaning. The self-cleaning of the mixers is achieved by the relatively simple geometric design of the mixing chamber and all the areas that are wetted out with reaction mixture. This is to ensure that they can be cleaned mechanically using a simple piston rod. The downside of the relatively simple cylindrical geometry: the design options for optimizing the flow of the mixing chamber are very limited. That is precisely what Hennecke's development engineers have set as their task. They have consequently questioned the entire concept of the proven high-pressure impingement mixing technology in order to develop a new deflection mixhead which significantly improves the mixing efficiency while keeping the same self-cleaning ability. The result of this is the Hennecke MT mixhead series with sizes which can process reaction mixtures from 5 g/s to 5000 g/s and are available to the customer in two-, four- and six- component versions.
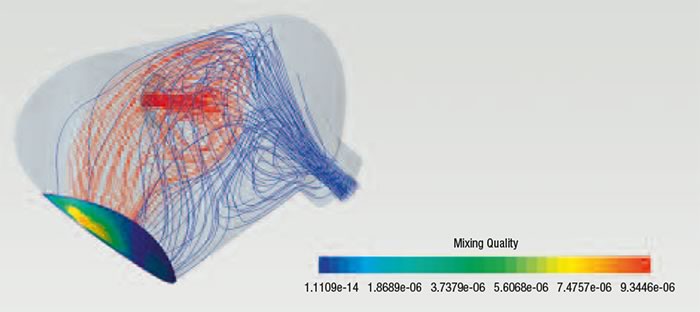
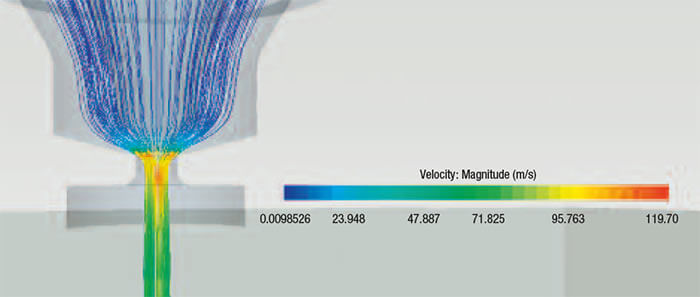
The core focus of the development process was to identify and significantly optimize the remaining geometrical degrees of freedom for a mixing chamber with a mostly fixed geometry. For example, the target was to optimize the parameters such as the relation between the diameter and height of the mixing chamber as well as the position and angularity of the mixing nozzles. This task was solved with numerous model experiments and flow simulation calculations. With participation of the Fraunhofer Institute for Algorithms and Scientific Computing (SCAI) the parameters were ultimately varied until the ideal setting was found. The prototypes were elaborately tested with representative polyurethane systems under real production conditions in the laboratory of Hennecke GmbH. The result can indeed be seen as a quantum leap in high-pressure mixing technology. The total efficiency of the new mixhead generation was significantly improved, which benefits the end user in several respects. The required energy for the production of moulded foam parts is significantly lower. Considering that a normal metering system for the manufacture of, for example, car seat cushions requires the power of approx. 15 KW simply for executing the mixing task, it is understandable how the efficient mixing technology can substantially affect the unit costs of a seat cushion. Even without the energy costs being a primary factor, the efficiency improvement results in a considerably wider process window, in which a large range of products can be manufactured reliably and at the highest quality with the scrap rate also decreasing significantly. The MT series now provides users with a mixer system, which reflects the current state of the art.
A modern mixhead must, of course, not only be optimized in terms of process technology. It is not without reason that the mixhead is considered the "heart piece" in a polyurethane plant. If the mixhead stops working, the production is at a standstill. This becomes particularly evident within the automotive supplier industry where production systems for seat manufacturing are operated, for example, in three shift operation. The system produces a finished seat in less than 15 seconds, which consists of at least three foam areas. It is usual that mixheads in such systems have to perform several million individual metering operations each year.
This means that the mixhead design, the selection of the materials and their treatment as well as the manufacturing quality are particularly challenged. For the design, the Hennecke engineers followed a simple formula: few individual components which only need to be finely machined in the functional areas, resulting in a robust, durable design with low error possibilities and an extremely attractive life cycle costing. It was possible to reduce the number of individual parts for the new design by about a third, with the complexity of each individual part kept simple. The core is formed by the mixhead housing with its high-precision bores for the mixing chamber, the mixture outlet and the mixing nozzles. This housing, in which the function sliders move in the hardened reaction mixture, is subject to the highest stress and thus forms the major wear areas. The application of extremely high-strength materials, combined with a special surface hardening and wear-resistant coating, enables MT mixheads to achieve several million "shots" in many applications. Specifically for the manufacture of these mixhead housings, Hennecke has invested in a new machining center to ensure that the high quality requirements are met and the manufacturing quality is secured in the long term. In addition to the mixing chamber, the mixing nozzles have to be taken into consideration in order to be able to effectively mix polyurethane systems using the high-pressure impingement mixing technology at the highest possible efficiency level. The mixing nozzles have the task of converting the pressure with which the reactive components are metered into speed. An ideal mixing nozzle should therefore accelerate the reaction component during the material passage with a low pressure difference to a maximum high speed. This means that the liquid stream threads of the reaction components have to cover a long distance in the mixing chamber and come into contact with the reaction partner. With the new development of the mixing nozzles for the MT mixhead series, the efficiency rate, thus the conversion of pressure into speed, was increased by approx. 30 percent. An infinite adjustment of the mixing nozzle opening allows the MT mixheads to be operated over a wide output range. The transition from a small output to a significantly higher output takes place at an almost constant pressure level, which is why quantity or formulation changes (mixing ratio alterations) can be carried out extremely quickly. The output or formulation change is performed during the cleaning stroke for the outlet pipe in less than one second.
This results in the possibility for the user to produce a wide range of products with only one mixhead at high efficiency. In the case of the four- or six-component mixheads, there is a further possibility of selecting or deselecting individual reaction components or other additives between the shots. The variation of products and product properties is therefore almost limitless with Hennecke's MT mixing system. Even if the user only has one production line.
The number of advantages when using the MT series can also be confirmed by Hennecke customers: the MT mixhead was the clear winner of a professionally designed comparison test of high-pressure mixheads used for the manufacture of refrigeration appliances. As part of the test operation, two-component mixheads from different manufacturers were closely examined under exactly the same conditions over a period of six months in production. Here, the Hennecke MT mixhead received the top mark for all significant assessment criteria (laminar discharge, mixing quality, leak-tightness as well as susceptibility to faults).
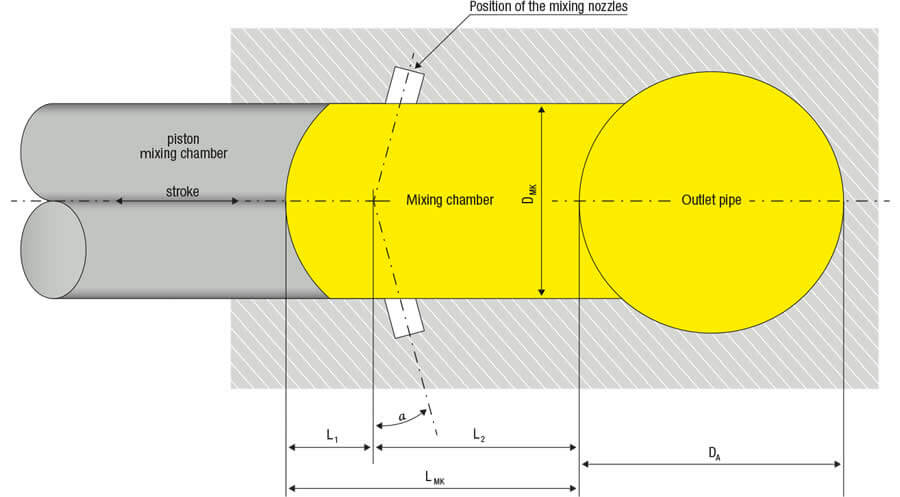