Unter Hochdruck leicht gemacht:
Boom bei der Herstellung von Composite-Bauteilen im Automotive-Bereich
Das Anwendungsfeld von Faserverbundwerkstoffen (Composites) beginnt oftmals dort, wo das Eigenschaftsprofil üblicherweise verwendeter Materialien die Anforderungen nicht mehr erfüllt. Bei der Herstellung von Automobil-Ladeböden treffen die spezifischen Eigenschaften von Leichtbau-Composites mit Polyurethan-Matrix genau ins Schwarze: komplexe Geometrien mit hoher Festigkeit und geringem Bauteilgewicht. Mit einer Marktabdeckung von mehr als 90 Prozent spielt die PUR-CSM-Technologie (Polyurethan Composite Spray Moulding) ihre Alleinstellungsmerkmale in diesem Anwendungsfeld voll aus und gilt als Synonym für zuverlässige Produktionsbedingungen bei uneingeschränkter Großserientauglichkeit.
Composites oder Verbundwerkstoffe beschreiben allgemein einen Werkstoff, der aus mindestens zwei einzelnen Komponenten besteht. Den inneren Zusammenhalt des Verbundes gewährleistet die sogenannte Matrix-Komponente. Ein oft genutzter Anwendungsfall im Bereich von Composites ist der dreischichtige Sandwichaufbau, welcher seinen Einsatz vorzugsweise im automobilen Leichtbau findet, wo ebene und schalenförmige Platten hohen Biegebeanspruchungen widerstehen müssen. Hierbei besteht die obere und untere Deckschicht aus einem Faserverbundwerkstoff, der für die Biegefestigkeit des Verbundes verantwortlich ist und den dabei auftretenden Druckund Zugspannungen widersteht.
Die Fasern fungieren dabei als Verstärkungskomponente und sind durch eine Gewebekonstruktion oder durch ein verfestigtes Vlies miteinander verbunden. Im Automobilbereich sind es vor allem Materialien wie Carbon oder Glas, die wegen ihrer enorm hohen Festigkeitswerte eingesetzt werden. Aufgrund der Wirtschaftlichkeit wird Carbon jedoch vor allem im Highend-Segment und Glas eher in seriellen Anwendungen eingesetzt. Die Matrix-Komponente funktioniert im Faserverbundwerkstoff als Fixierung der Verstärkungskomponente. Dabei umschließt sie die Fasern, sorgt für den Zusammenhalt des Verbundes zwischen Kern und Deckschicht und ermöglicht eine gleichmäßige Kraftableitung auf die Fasern sowie den wirksamen Schutz vor äußeren Einflüssen.
Im Automobilsektor ist, maßgebend durch die hohe Stückzahlanforderung, eine geringe Fertigungstaktzeit Voraussetzung. Deshalb wird zur Fixierung der Glasfaservliese vorzugsweise Polyurethan (PUR) verwendet, das aufgrund der steuerbaren Schäumeigenschaften zudem den Leichtbau begünstigt. Zusätzlich erfüllt es durch die schnelle Reaktion die geforderten kurzen Taktzeiten. In der Sandwichkonstruktion übernimmt die PUR-Matrix neben der Fixierung des Glasvlieses gleichzeitig die Anbindung des Kerns aus Papierwabe an die Deckschichten. Der Kern selber kann aus verschiedenen Geometrien und Materialien bestehen. Gerade im seriellen Automobilbau werden häufig Papierwaben als Kern von Sandwichkonstruktionen eingesetzt. Dies begründet sich insbesondere in der hohen Festigkeit und dem geringen Gewicht. Zudem ist Papier sehr gut recyclebar. Durch diesen Materialverbund werden Composites konstruiert, welche die positiven Eigenschaften der Einzelkomponenten nutzen und steigern, während sie gleichzeitig die unerwünschten Eigenschaften überdecken. Beim Endprodukt steht das in diesem Fall für hohe Bauteilstärken und eine hohe Festigkeit bei gleichzeitig geringem Gewicht.
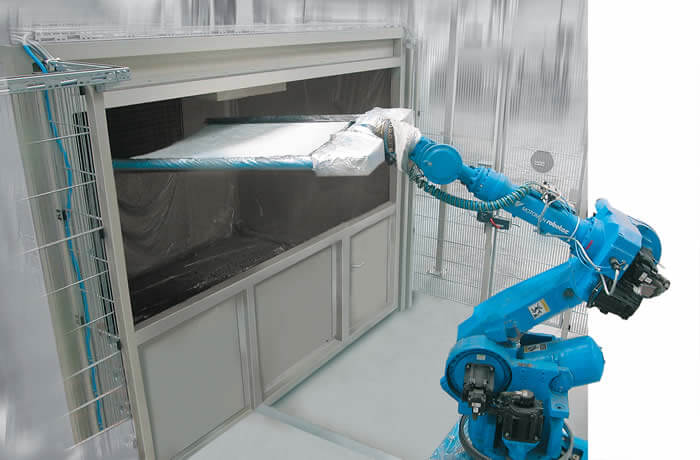
Effizienter Produktionsprozess mit PUR-CSM
Ein großes Anwendungsfeld für Composites und Sandwichkonstruktionen in seriellen Anwendungen stellt der Ladeboden im Kofferraum dar. Ausgangspunkt für die Produktion dieser Ladeböden ist die Herstellung des Sandwich-Rohlings. Dabei wird eine Papierwabe in ein Glasvlies eingeschlagen. Das „Know-how“ innerhalb der Herstellung liegt allerdings im Polyurethan-Auftrag. Für einen effizienten Auftragsprozess ist die PUR-CSM-Technologie unerlässlich.
Die Vorteile entstehen vor allem in der sehr gleichmäßigen und reproduzierbaren Verteilung des Polyurethans und der Fasern, was unter anderem im Hinblick auf den Verzug sowie den geringen Materialeinsatz und somit auch für das Bauteilgewicht von großer Bedeutung ist. Mittels der CSM-Sprühtechnik werden die Faserhalbzeuge hierbei zunächst ein- oder beidseitig mit einem thermisch aktivierten PUR-System benetzt. Dies ermöglicht dem Verarbeiter eine vergleichsweise lange, offene Zeitzum eigentlichen Sprühauftrag. Hierdurch ist ein gezielter Materialauftrag in bestimmten Bauteilbereichen (Kanten, Rand, Krafteinleitungsbereiche), die Herstellung von sehr großen Bauteilen oder auch die Verwendung von Werkzeugen mit Zwei- oder Dreifach-Kavität wesentlich einfacher zu realisieren. Andererseits erfolgt durch die thermische Aktivierung in einem beheizten Werkzeug bei Bedarf eine rasche Aushärtung im Bereich von 45 bis 90 Sekunden, wobei die Formgebung zum fertigen Bauteil durch Verpressen erfolgt. Durch die Möglichkeit, je nach Anlagenkonfiguration bis zu drei Werkzeugträger mit einer CSM-Sprüheinheit bedienen zu können, ermöglicht der Einsatz von PUR-CSM die Fertigung von bis zu 2.000 Bauteilen pro Tag. Ein Novum, welches durch das Alleinstellungsmerkmal „Selbstreinigung“ der CSM-Sprühtechnik erst möglich wurde. Ein weiterer Grund für die uneingeschränkte Großserientauglichkeit dieser Bauteile ist sicherlich auch darin begründet, dass die PUR-CSM-Technologie alle Vorzüge mitbringt, um Kundenwünsche verschiedener OEMs kosten- und technologieeffizient zu realisieren. Ein wesentliches Alleinstellungsmerkmal ist beispielsweise die, von der klassischen CSM-Technik bekannte Möglichkeit der Schussunterbrechung, welche auch bei dieser Variante der CSM-Sprühtechnik erhalten bleibt. Dies ist vor allem im Hinblick auf den Zeitbedarf zur Programmierung des Sprühprozesses sowie hinsichtlich eines sehr gleichmäßigen Materialauftrages und somit höchster Bauteilqualität und eines reduzierten Materialverbrauchs von entscheidendem Vorteil.
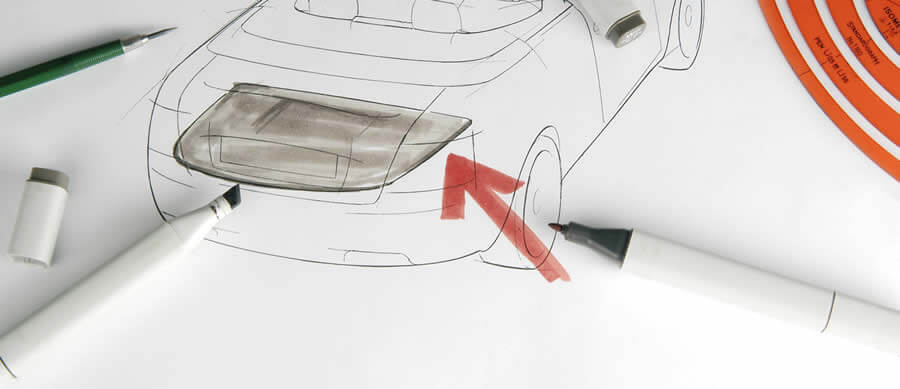
Fertigung von Composites mit komplexen Geometrien
Auch bei der Fertigung von komplexen Geometrien kann die PUR-CSM-Technologie ihre Vorzüge bei der Herstellung von Composites ausspielen. Im Bereich des Ladebodens setzen die Hersteller bei neuen Fahrzeugkonzepten zunehmend auf gesteigerte Variabilität in Form von zusätzlichem Stauraum. Um diesen zur Verfügung zu stellen, werden verstärkt 3D-Mulden und Ablagen in die Formgebung integriert. Eine Aufgabe, die ebenfalls durch die Sandwichtechnologie bestens umgesetzt werden kann. So erhalten heutzutage Ladeböden zusätzliche Funktionalitäten wie Klappentechnik, Ablagemulden oder auch Wendetechnologien. Hierbei kann ein Ladeboden beispielsweise sowohl eine edle Veloursoberfläche erhalten als auch eine „Tropfwanne“ für schmutziges Transportgut.
Alles aus einer Hand: schlüsselfertige Anlagentechnik von Hennecke
Die Summe der Vorteile lässt die Nachfrage nach LeichtbauComposites in den vergangenen Jahren stetig steigen. So konnte Hennecke weltweit bereits mehr als 40 Produktionsanlagen für die Produktion von Ladeböden und Dachmodulen im Markt platzieren. Eine Marktabdeckung von mehr als 90 Prozent spricht für sich und macht die PUR-CSM-Technologie zum Standard,wenn es um hohe Festigkeit und geringes Bauteilgewicht bei Automobil-Ladeböden geht. Dabei ist der Erfolg jedoch nicht alleine auf die Prozesstechnik zurückzuführen. Hennecke tritt als Generalunternehmer auf und ist in der Lage die gesamte Prozesskette, bestehend aus Pre-Formling, Robotertechnik, Presse sowie Sprühkabine und Sicherheitstechnologie, schlüsselfertig zu liefern. Hierbei stellen auch spezielle Anforderungen, wie zum Beispiel die Berücksichtigung einer ergonomischen Produktion, keine Hürde dar. Daneben setzt der erfahrene Maschinenbauer in allen Projektphasen auf Kundenservice. So können Testläufe und Abmusterungen im hauseigenen CSM-Technikum bereits vor einer Investitionsentscheidung durchgeführt werden.
Download - Ausgabe 112 (PDF)
Zur Betrachtung benötigen Sie den Adobe® Reader®, den Sie hier kostenlos herunterladen können.