High pressure meets lightweight –
the production of composite parts is booming in the automotive industry
The use of fibre composites often starts when the characteristics of other materials no longer meet the customer's requirements. In the manufacture of car load floors, the specific properties of light composites combined with a polyurethane matrix completely meet the mark: complex geometries that are extremely stable and very light. Covering over 90 percent of the market, PUR-CSM technology (Polyurethane Composite Spray Moulding) makes full use of its unique selling points in this area of application and is known for providing reliable production conditions that are perfectly suited for large volumes.
Composites or composite materials in general describe a material that consists of at least two components. What is known as the matrix component guarantees that the compound's interior is coherent. A three-layer sandwich structure is often used in composites, especially in the field of automotive lightweight construction in which flat and shell-shaped panels have to resist high bending loads. The top and lower facings are made of a fibre reinforced composite that ensures the compound's flexural strength and resists the pressure and tension stress that arise. The fibres function as reinforcement components and are connected to each other by a fabric construction or a solid mat.
In the automotive area, materials such as carbon or glass are mainly used because of their extremely high strength values. For reasons of cost, carbon is usually applied in the high-end of the market whereas glass features in serial applications. The matrix component in the composite serves to fix the reinforcement component. It wraps the fibres and makes sure that the composite between the core and the facing is cohesive. It also allows for a consistent force distribution to the fibres as well as an efficient protection against outside influences. In the automotive industry, a short production cycle time is required to meet the demand for large quantities. For this reason, polyurethane (PU) is preferably used for fixing glass fibre mats because its controllable foaming properties facilitate lightweight construction.
Thanks to its fast reaction, it also meets the short cycle times required. In a sandwich construction, the PU matrix not only fixes the glass mat but also links the core, which is made out of a paper honeycomb structure, to the facings. The core itself can be composed of different geometries and materials. In serial automobile manufacture, paper honeycombs are often used as the core of sandwich structures.This is particularly because of their high strength as well as their low weight. Moreover, paper is very easy to recycle. This combination of materials allows for the manufacture of composites that exploit and boost the positive characteristics of the individual components while cancelling out unwanted features. End products thus benefit from high component strength and stability combined with low weight.
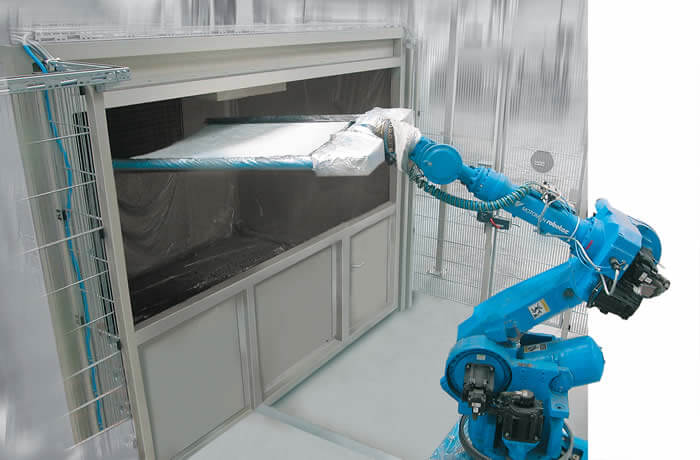
Efficient production process with PUR-CSM
Composites and sandwich constructions are often used to manufacture the load floors of car trunks in serial applications. Sandwich blanks form the point of departure for making these load floors. A paper honeycomb is wrapped in a glass mat. The „know-how“ in the production process, however, is focused on the PU application. For an efficient coating process, PUR-CSM technology is indispensable.
The advantages consist above all in the very even and reproducible distribution of the polyurethane and the fibres, which, among other things, has a significant effect on the warpage behaviour and contributes to reducing the required amount of material and thus the weight of the component. CSM spray technology is used to wet the semi-finished fibre products on one or both sides with a thermally activated PU system. This enables the processor to go on spraying for a comparatively long and open amount of time. The focused output in certain areas of the components (edges or areas where force is applied) makes it considerably easier to manufacture very large parts or use moulds with two or three cavities. On the other hand, if necessary curing can take place very rapidly (from 45 to 90 seconds) thanks to the thermal activation of a heated mould while the design of the finished part takes place through compression. Because one CSM spray unit can serve up to three mould carriers depending on the plant configuration, the use of PUR-CSM enables the manufacture of up to 2,000 parts per day. This is a novelty that has been made possible by the unique self-cleaning function of CSM spray technology. Another reason why these parts are particularly appropriate for mass production is because PUR-CSM technology has every advantage necessary for realizing the customer needs of various OEMs when it comes to cost and technology efficiency.
A major selling point, for instance, is the possibility to interrupt the shot – a feature that customers already know from classic CSM technology and that remains unchanged in the present variant of CSM spray technology. It offers a distinct advantage particularly with regard to the time required for programming the spraying process and the very uniform material application, resulting in top component quality and reduced material consumption.
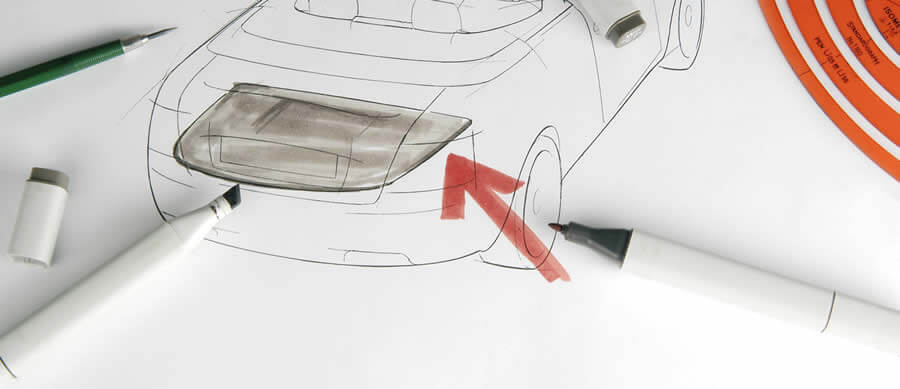
Manufacturing composites with complex geometries
When complex geometries are manufactured PUR-CSM can also make the most of its advantages in producing composites. Carmakers are more and more interested in variability when designing load floors, in the form of additional storage space. More 3-D hollows and parcel shelves are being integrated into the design to make this possible. Sandwich technology is the best suited to the task. Load floors are thus acquiring more functions than before such as hinge technology, parcel shelf hollows or even perfecting technologies. A load floor can thus be given a sophisticated velour surface or a „drip tray“ for transporting dirty objects.
One-stop - turnkey systems technology made by Hennecke
The sum total of advantages means that the demand for light composites has risen steadily in the past years. Hennecke has put some 40 production systems for making load floors and roof modules on the market. The fact that the company enjoys over 90 percent of the market share speaks for itself and means that PUR-CSM is the standard technology when it comes to high stability and low weight of car load floors. The success does not rest entirely on the process technology. Hennecke presents itself as a generalist and can thus deliver everything along the process chain on a turnkey basis, from preform, robot technology, press and spray booth to safety technology. No problems are presented by special requirements such as ergonomic production either. Moreover, the experienced machine manufacturer is on hand at all phases of the project to serve the customer. Test runs and checks in Hennecke's in-house CSM technical laboratory can be conducted before any decision is made on an investment.