A very special type of ELASTOLINE F
A rarity on the market
The name puralis stands for decades of experience in the area of semi-finished products and moulded parts made from cast elastomers.
Located in the Schwarzheide Chemical Park, the company was initially unable to find an appropriate partner when it wanted to upgrade a very sophisticated casting system from a manual to a largely automated production process, but this all changed with the use of an ELASTOLINE F from Hennecke GmbH.
Schwarzheide, August 2011: Four men congratulate each other. One is puralis Project Manager Alexander Augat, the second is puralis Manager Jürgen Lemke, the third puralis CEO Oliver Schmid, and the fourth is Matthias Klahr, Head of Sales for elastomer metering machines at Hennecke GmbH. The four are very satisfied that they have completed their challenging project successfully by putting the ELASTOLINE F into operation. The plant had already been put to the acid test at Hennecke HQ in Sankt Augustin-Birlinghoven.
The run-up: puralis confided to Hennecke at the ELASTOLINE DAYS 2010 that it wanted its manufacturing processes to be more automated regarding special applications so that production could become even more customized. A very fruitful technical partnership then developed between Hennecke and puralis GmbH, which employs some 45 people at its HQ in Schwarzheide. The comprehensive standards that were required of the system were defined in a specification and Thomas Beck (mechanical design) started running complex and detailed trials in the lab to configure the ordered production system appropriately with regard to pump output and other parameters.
One particular requirement was the manufacture of a complex cast elastomer, a one-shot system. This five-component cast system calls for very high metering precision and for exact temperature control of the components. Hennecke met the special requirements straight to the point.
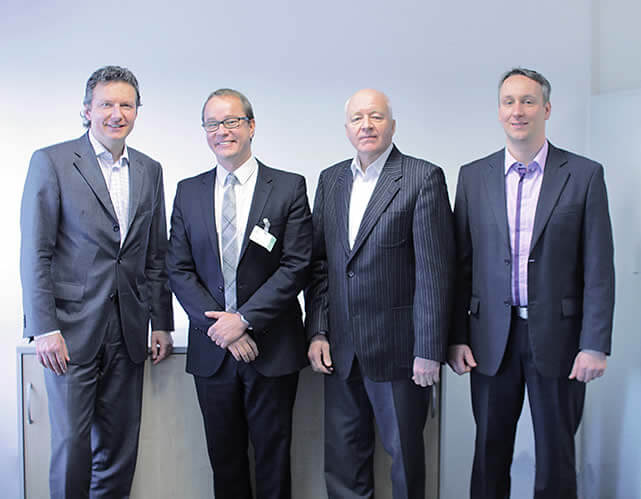
Made-to-measure pump units and mixheads
A metering pump that can meet even the highest and most difficult requirements regarding wear-and-tear of the isocyanate metering line was developed. Hennecke worked in close cooperation with longstanding pump suppliers to reach a satisfactory lifetime. The pump is easy to maintain, appropriate for the materials and a novelty on the market. The same is true for the MEL/4C+ mixhead whose mixing chamber and injector adjustment were tailored to the particular application. Because the requirements of the MDI isocyanate are very high when it comes to filtering and cleanliness during processing, Hennecke consulted longstanding filter suppliers to configure the filters individually.
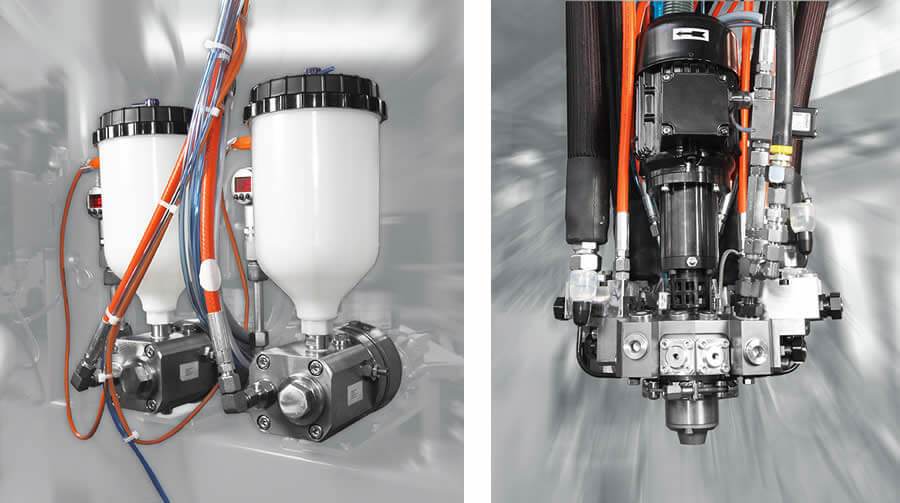
Eight-component system that seeks its equal
Apart from the five reactive components of the one-shot system, the ELASTOLINE F was also equipped with two colour components and a cleaning component. This corresponds to a very customer-specific configuration that is rarely seen on the market. The ELASTOLINE F is designed for 15kg/min, which enables parts weights of over 30 kgs and a great product range. puralis mainly makes high-quality cast elastomer parts for the construction machinery industry (e.g. strippers, mixing shovels), for harbour and ship construction (fenders), as well as for pipe and pipeline technology (e.g. scrapers and screw conveyors). Cylinders, clutches and gaskets for different industrial applications can also be made. puralis and Hennecke plan to continue their successful cooperation and develop their win-win situation. Hennecke has acquired a new distinguished customer and puralis now has a reliable machine builder with comprehensive expert know-how. Another plant is in the final stage of negotiation.
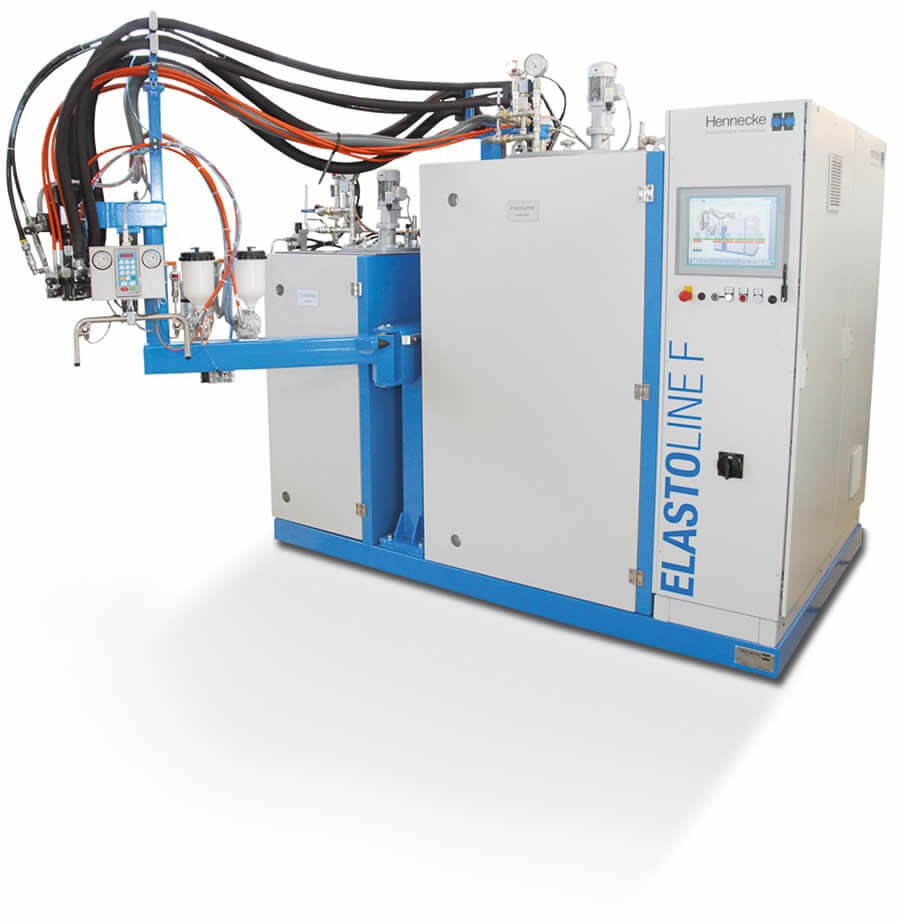
ELASTOLINE – known for decades
The ELASTOLINE series machines are for processing cast systems and raw materials based on PUR. They fulfill the highest requirements and guarantee high-quality end products with excellent dynamic properties. ELASTOLINE F is a flexible engineering design that can perfectly be adapted to customer requirements when it comes to processing raw material systems based on MDI and TDI. The ELASTOLINE V is particularly good at processing NDI systems (e.g. Vulkollan®) thanks to its high-quality temperature control design for optimal component conditioning.