One technology – double benefit for customers
Hennecke slabstock lines increase both raw material yield and foam quality
Slabstock foams are not all the same and not all slabstock lines are equal.
The difference lies in how precisely raw materials are mixed with each other, how the reactive mix is poured and how the top crust formation is minimized and transformed into usable foam.
Hennecke has developed a very special technology, with which it holds a leading position in the global market.
Low or high-pressure technology?
Users who are new to slabstock foam production will pose this question, as will those still using low-pressure systems and thinking of switching over to high pressure. Whatever the case, all users have to face the fact that 80 or 90 per cent of slabstock foam production costs are made up of the raw materials, whereas the other 10 to 20 per cent go on machines, production halls, energy and sales. That's why it makes perfect sense to save money on raw materials in order to reduce operating costs.
Leading slabstock foam producers that have experience with both low and high-pressure systems are opting for Hennecke high-pressure technology, which involves mixing isocyanate into the mixing chamber at high pressure. This results in a better mixing quality of the raw materials and a higher reaction efficiency factor than if low-pressure technology is used.
Up to 4 per cent of isocyanate can be saved, corresponding to savings of 100,000 euros at an isocyanate price of 2.5 euros a kilo based on an annual slabstock production of 3,000 tons – this money can be invested elsewhere. These calculations were made during tests and trials and have since been confirmed by operator companies who have switched from low to high-pressure Hennecke technology (see box). Another advantage of highpressure metering is that the cell size can be better controlled. If the isocyanate injection pressure is high there is a fine cell structure, whereas if it is low the cell structure will be coarser.
Making a profit with high pressure
Example calculation: | |
Annual slabstock production: | 3,000 tons |
Tonnage of ISO: | ca. 1,000 t → 1,000,000 kg |
Material costs of ISO: | ca. 2.50 EUR/kg |
Total ISO costs: | 2,500,000.00 EUR |
| |
4 % ISO savings: | 100,000.00 EUR/year |
Trough or liquid laydown process?
Depending on how the reactive mixture is introduced to the foaming process, a distinction is made between using the trough or laydown process in practical applications.
As the name indicates, if the trough process is used the reactive mixture moves from the trough to the conveyor. As the cells grow during this process, they move upwards and bend over the edge of the trough, which results in an irregular cell structure. Moreover, there is already reacting foam above the reactive mix in the trough so that air bubbles cannot escape and will later be found in the foam structure as pinholes and voids.
Hennecke's liquid laydown process works differently. The reactive mix is poured onto a sheet of paper, which is on the conveyor, and the reaction takes place upwards and downwards, thus allowing the foam to form a regular cell structure. Because the reactive mixture is poured onto the conveyor from above, air bubbles can escape before the reaction takes place so that pinholes and voids are kept to a minimum. Moreover, a top paper sheet is placed on the reactive liquid during the liquid laydown process which separates the top of the block from air humidity,meaning that a thinner top skin is formed and the block has a better shape than if the trough process had been used.
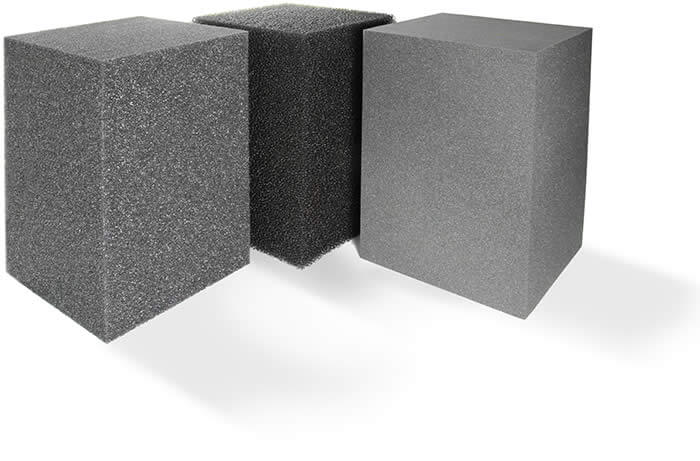
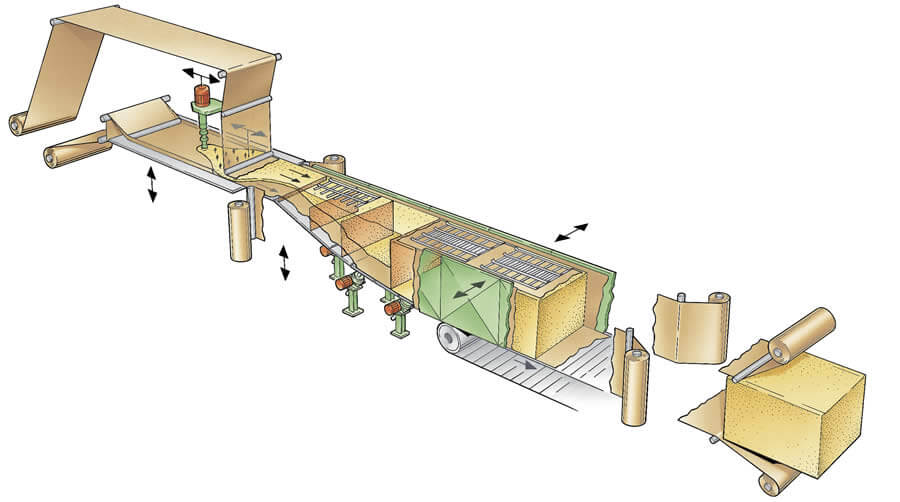
RS or flat-top system?
As was mentioned at the start, 80 to 90 per cent of the costs in slabstock foam production consist of the raw materials, which is why many slabstock producers strive for a higher material yield. The RS system, in which the shape of the block is achieved by lifting a laterally moving plastic sheeting, has its limits because a top crust that cannot be used forms on the surface.
But if the Hennecke flat-top system is integrated, blocks with an almost plane-parallel rectangular effect are achieved by sliding mats onto the upper surface of a block. The top crust is minimized to a thin top skin and transformed into usable foam. In addition, there is an important synergy effect as the foam rises because of the moving top paper that keeps the reaction heat within the slabstock and allows for more intensive foam reaction beneath the block surface. The top skin is also thinner and the material yield is higher. Thus the user can save up to 3 per cent on raw materials (see box). Moreover, by covering the block on all four sides air humidity is prevented from entering during the maturing process. As a result, there is a higher degree of hardness and a uniform hardness distribution is achieved.
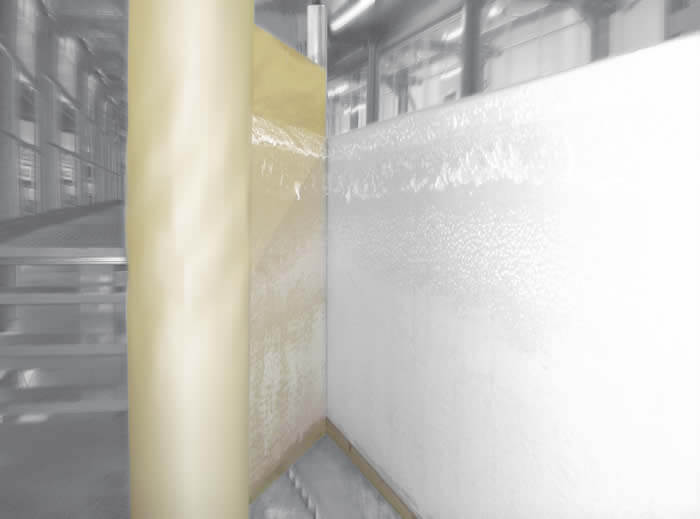
Higher material yield thanks to Hennecke flat-top system
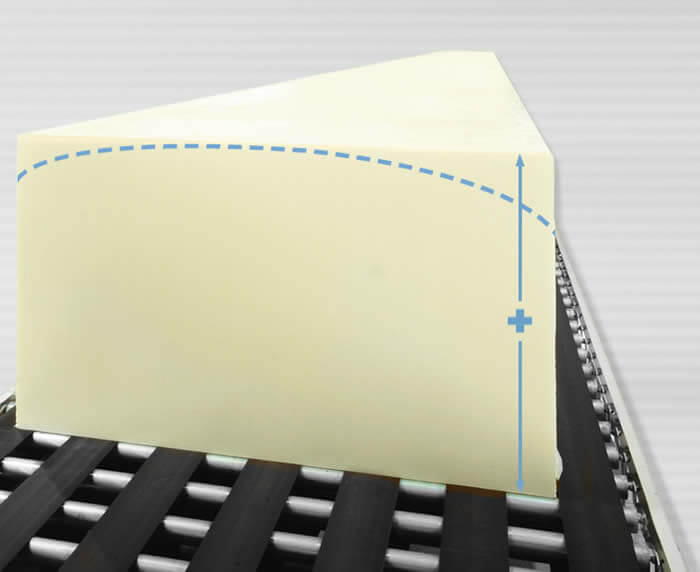
Example calculation: | |
Annual slabstock production: | 3,000 tons |
Material costs per kg of foam: | ca. 2 EUR |
Total material costs: | 6,000 EUR |
| |
Savings at 3%:: | 180,000.00 EUR |
Further advantages
Flexible applications
As an option, Hennecke slabstock lines can (also subsequently) be equipped with NovaFlex® technology for producing CO2-blown flexible slabstock foams with low densities. NovaFlex®-MultiFill also allows functional fillers, such as melamine or CaCO3 to be processed. Operator companies can thus react flexibly to the demands of the market and environment, and produce special foams in a profitable manner.
Faster liquid laydown
A new, electrically height-adjustable mixer for MULTIFLEX lines that is delivered with the outlet as a unit offers users a better foam cell structure because the reactive mixture is discharged faster. This results in foams that are practically free of pinholes and voids.
New dimensions of freedom
A new screw-type stirrer for the continuous MULTIFLEX, QFM and UBT slabstock lines, which reduces the mixing chamber pressure, enables the foamer to have more influence on cell size, meaning there is more freedom in cell control.