Eine Technologie – zweifacher Kundennutzen
Hennecke-Blockschaum-Anlagen steigern Rohstoffausbeute und Schaumstoffqualität
Blockschaum ist nicht gleich Blockschaum und Blockschaum-Anlage nicht gleich Blockschaum-Anlage.
Der Unterschied besteht darin, wie präzise alle Rohstoffkomponenten miteinander vermischt werden, wie das reaktive Gemisch aufgetragen und die Deckschwarte minimiert und in verwertbaren Schaum umgewandelt wird.
Hennecke hat eine ganz spezielle Technologie entwickelt und nimmt damit auf dem Weltmarkt eine Führungsposition ein.
Nieder- oder Hochdrucktechnologie?
Vor dieser Frage stehen vor allem Neueinsteiger in die Blockschaum-Produktion sowie Nochbetreiber von Niederdruckanlagen. Ob Neu- oder Umsteiger, beide müssen sich mit der Tatsache auseinandersetzen, dass 80 bis 90 Prozent der Blockschaum-Produktionskosten auf Rohstoffe entfallen und nur 10 bis 20 Prozent auf Maschinen, Produktionshalle, Energie und Verkauf. Deshalb liegt es auf der Hand, in erster Linie Rohstoffe einzusparen, um die Betriebskosten zu senken.
Führende Blockschaum-Produzenten, die sowohl Erfahrung mit Nieder- als auch Hochdruckanlagen haben, setzen deshalb auf die Hennecke-Hochdrucktechnologie. Bei der Hochdruckvermischung wird das Isocyanat mit hohem Druck in die Mischkammer eingedüst. Die Vermischungsqualität der Rohstoffe ist besser und die Reaktion hat einen höheren Wirkungsgrad als bei der Niederdrucktechnologie.
Im Ergebnis werden bis zu vier Prozent an Isocyanat eingespart. Dies entspricht bei einer jährlichen Blockschaumstoff-Produktion von 3.000 Tonnen und einem Isocyanat-Preis von ca. 2,50 EUR/kg einer Einsparung von 100.000 EUR – Geld, das nun für andere Investitionen zur Verfügung steht. Diese Werte wurden im Rahmen von Versuchen erhoben und von Anlagenbetreibern bestätigt, die von der Nieder- auf die Hennecke-Hochdrucktechnologie umgestiegen sind (s. Kasten). Ein weiterer Vorteil der Hochdruckdosierung ist die Steuerbarkeit der Zellgrößen. Ist zum Beispiel der Isocyanat-Einspritzdruck hoch, sorgt das für eine feine Zellstruktur. Ist er gering, fällt die Zellstruktur grob aus.
Mit Hochdruck in die Gewinnzone
Beispielkalkulation: | |
Jahres-Blockschaum-Produktion: | 3.000 t |
ISO-Tonnage: | ca. 1.000 t → 1.000.000 kg |
ISO-Materialkosten: | ca. 2,50 EUR/kg |
Gesamt-Iso-Kosten: | 2.500.000,00 EUR |
| |
4 % Iso-Einsparung: | 100.000,00 EUR/Jahr |
Trog- oder Liquid-Laydown-Ausführung?
Je nachdem,wie das reaktive Gemisch dem Schäumprozess zugeführt wird, unterscheidet man in der Praxis zwischen dem Trog- und dem Liquid-Laydown-Verfahren.
Beim Trog-Verfahren bewegt sich das reaktive Gemisch – wie es der Name schon sagt – aus dem Trog auf das Band. Während dieses Prozesses, in dem die Zellen wachsen, werden diese nach oben bewegt und über die Trogkante gebogen. Die Folge ist eine unregelmäßige Zellstruktur. Außerdem befindet sich über dem reaktiven Gemisch im Trog bereits reagierender Schaum. Möglichen Luftblasen wird somit der Weg versperrt, den Schaum zu verlassen. Diese Luftblasen finden sich später als Pinholes und Lunker in der Schaumstruktur wieder.
Anders verhält es sich beim Liquid-Laydown-Verfahren von Hennecke. Das reaktive Gemisch wird auf ein Papier, das auf dem Band liegt, gegossen, und die Reaktion erfolgt nach oben und unten, sodass der Schaum eine regelmäßige Zellstruktur bildet. Da die reaktive Mischung von oben auf das Band gegossen wird, können mögliche Luftblasen vor Beginn der Reaktion das Gemisch verlassen. Pinholes und Lunker werden so auf ein Minimum reduziert. Zudem wird beim Liquid-Laydown-Verfahren Deckpapier auf die reaktive Flüssigkeit gelegt. Das Papier trennt die Blockoberseite von der Luftfeuchtigkeit,wodurch die Oberhaut dünner und die Blockform besser ausfällt als beim Trogverfahren.
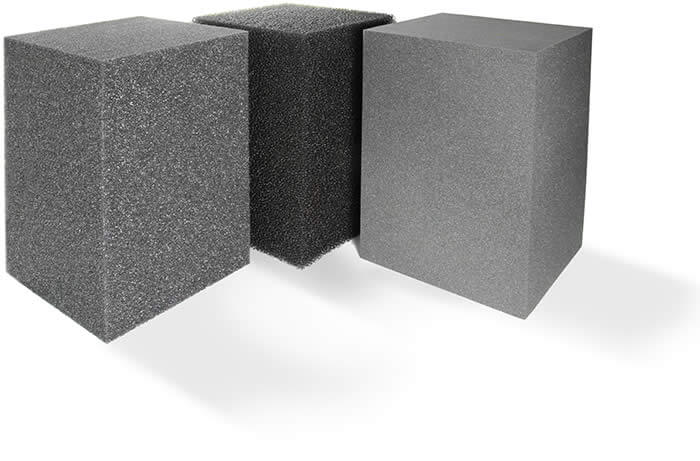
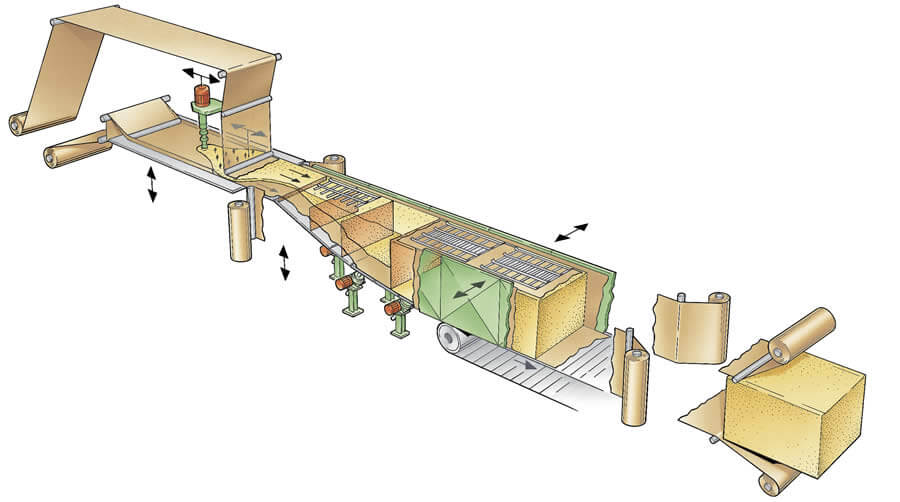
RS- oder Rechteckblock-System?
Wie bereits eingangs erwähnt, schlagen bei der Blockschaum-Produktion die Rohstoffkosten mit 80 bis 90 Prozent zu Buche. Deshalb streben viele Blockschäumer eine höhere Materialausbeute an. Das RS-System, bei dem die Blockform über das Anheben einer seitlich mitlaufenden Kunststoffbahn erzielt wird, stößt dabei an seine Grenzen. Bei diesem Verfahren bildet sich auf der Blockoberfläche eine Deckschwarte, die nicht verwertet werden kann.
Dagegen entstehen durch die Integration der Hennecke-Rechteckeinrichtung, bei der Matten auf der Blockoberseite gleiten, Blöcke mit fast planparallelem Rechteckeffekt. Die Deckschwarte wird auf eine dünne Oberhaut minimiert und in verwertbaren Schaum umgewandelt. Darüber hinaus ergibt sich während des Aufsteigens des Schaumes durch das mitlaufende Deckpapier ein wichtiger Synergieeffekt: Das Papier hält die Reaktionswärme im Block und sorgt für eine intensivere Schaumreaktion unter der Blockoberfläche. Auch deshalb ist die Oberhaut dünner beziehungsweise die Materialausbeute größer. So können bis zu drei Prozent des gesamten Rohstoffverbrauches eingespart werden (s. Kasten). Außerdem wird durch das Abdecken des Blockes nach allen vier Seiten verhindert, dass auch beim Nachreifen Luftfeuchtigkeit eindringt. Dadurch wird eine höhere Härte und eine gleichmäßige Härteverteilung erzielt.
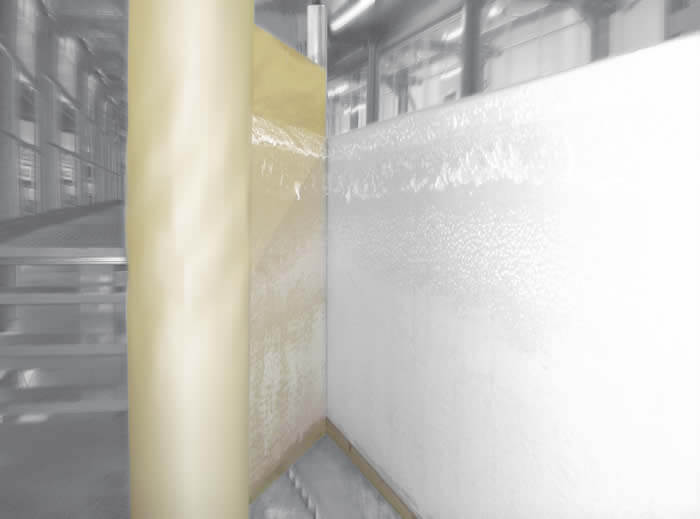
Höhere Materialausbeute durch Hennecke-Rechteckeinrichtung
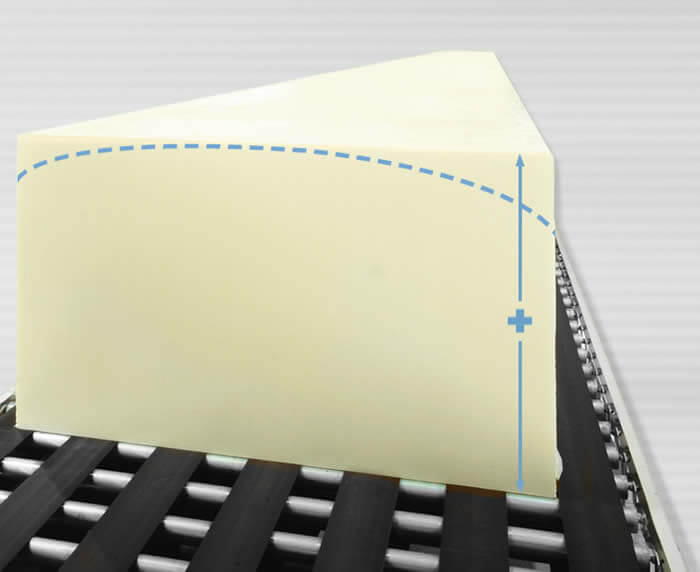
Beispielkalkulation: | |
Jahres-Blockschaum-Produktion: | 3.000 t |
Materialkosten je kg Schaum: | ca. 2,00 EUR |
Materialkosten total: | 6.000,00 EUR |
| |
Kosteneinsparung bei 3%: | 180.000,00 EUR |
Weitere Vorteile
Flexible Anwendungen
Optional werden Hennecke-Blockschaum-Anlagen mit der NovaFlex®-Technologie zur Herstellung von CO2-getriebenen Blockweichschaumstoffen mit niedrigen Rohdichten ausgestattet – auch nachträglich. NovaFlex®-MultiFill erlaubt zusätzlich die Verarbeitung funktioneller Füllstoffe, wie zum Beispiel Melamin oder CaCO3. Anlagenbetreiber können so flexibel auf aktuelle Markt- und Umweltanforderungen reagieren und auch Spezialschäume profitabel produzieren.
Schneller Gemischaustrag
Ein neuer, elektrisch höhenverstellbarer Mischer für MULTIFLEX-Anlagen, der als Einheit mit dem Auslauf ausgeführt ist, bietet dem Kunden eine bessere Zellstruktur im Schaum, da das reaktive Gemisch schneller ausgetragen wird. Das Ergebnis sind nahezu pinhole- und lunkerfreie Schäume.
Neue Freiräume
Ein neuer Schraubenrührer für die kontinuierlichen Blockschaum- Anlagen MULTIFLEX, QFM und UBT, der den Mischkammerdruck reduziert, ermöglicht dem Schäumer eine zusätzliche Einflussnahme auf die Zellgröße. Dadurch ergeben sich neue Freiheitsgrade bei der Zellsteuerung.
Download - Ausgabe 211 (PDF)
Zur Betrachtung benötigen Sie den Adobe® Reader®, den Sie hier kostenlos herunterladen können.