Nord-Stream-Pipeline
Teamwork under high pressure
When two high-performing companies come together, the best results are already in the making. And this goes for Hennecke GmbH and the Allseas Group S.A. The two firms have cooperated closely together and developed a technology, which is proving itself day after day in the hardest of conditions.
We are talking about the Nord Stream project – an offshore gas pipeline that will stretch from Portovaya Bay near Vyborg in Russia to the German Baltic coast near Greifswald. The Nord Stream Pipeline consists of two 1,224-kilometre long parallel pipes. This means that some 200,000 pipes have to be welded and some 200,000 weld joints have to be sheathed.
The open-cell PU rigid foam Elastopor H is the right tool for the job. It is a product that a leading raw materials supplier has further developed and optimised in the past two years with regards to solidity and processing speed.
The Nord Stream Pipeline will join Russia and the European Union directly via the Baltic Sea and will transport up to 55 billion cubic metres of natural gas to companies and private individuals. The first pipe is due to start operating in 2011 and the second in 2012.
The laying work is already underway at full speed. In April this year, Saipem S.p.A.’s “Castoro Sei” was set to sea to begin the construction of the pipelines and Allseas' “Solitaire” pipe laying vessel has been hard at it since August. Polyurethane from one of the major raw materials suppliers as well as Hennecke technology in the form of two TOPLINE HKs 1400/1400 with tank farm control are also on board. In the past, the Solitaire has already broken several pipelay records in terms of laying speed and depth.
Special technology for special applications
The optimised Elastopor H was developed over the past two years. The PU systems used consist of two liquid components, which are pressurised by Hennecke high-pressure foaming machines on the “Solitaire” itself and mixed by the MT 26 mixhead before being used to fill the hollow space in the fitting. The MT 26 is a new mixhead that has been especially designed for rigid foam. As an add-on mixhead it has an output of between 1 and max. 3 kg/s. Moreover it is equipped with constant pressure nozzles that allow the output to be varied without the pressure conditions changing.
Thanks to its good flow properties, the polyurethane system is quickly and uniformly distributed throughout the hollow space. In order to prevent the polyurethane rigid foam from being buoyant, it is configured to be open-celled so that hydrostatic pressure causes it to fill up completely with water. Its dimensional stability is crucial here. The material stands out with its high density of 160 kilograms per cubic metre, which maintains the exacting physical properties of this product. These characteristics are needed to protect he weld joints from anchor and net damages.
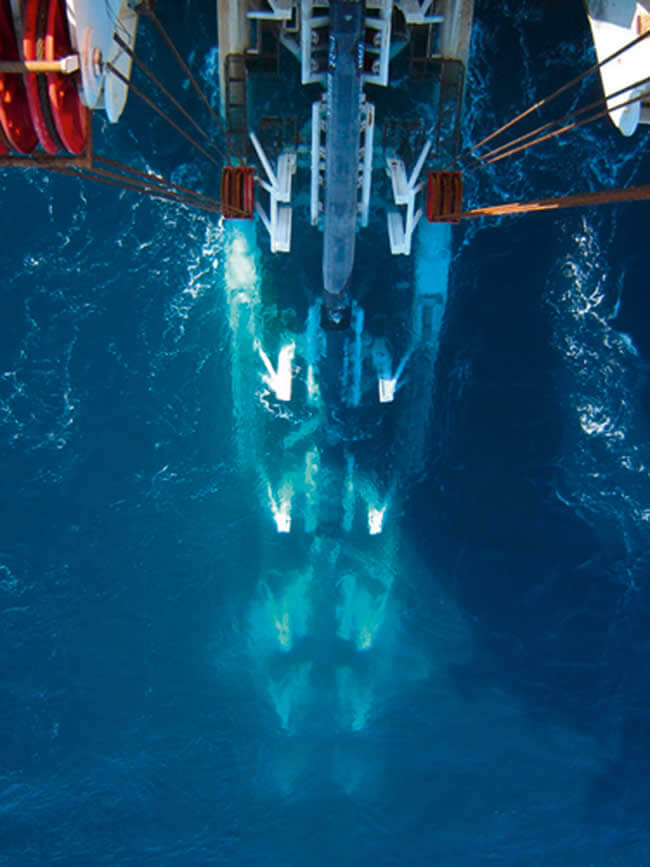
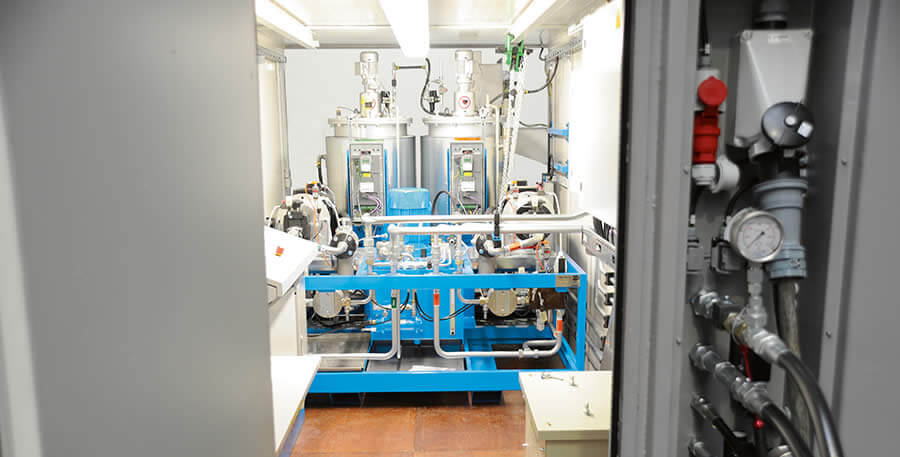
Hennecke and Allseas – a strong team
Founded in 1985, the Swiss-based Allseas Group is one of the major offshore pipelay and subsea construction companies in the world, operating six specialised vessels, which were designed in-house.
At the last “K” trade fair Allseas approached Hennecke with an enquiry about a special machine that had to be mobile so that it could be fitted onto a ship. It also had to have an output of over 3 kg/s and be suited to raw materials systems with mixing ratios of 50 to 100 to 150. Moreover, it had to have its own cooling circuit for ambient temperatures of between minus 30 and plus 50 degrees Celsius.
At their meetings, the Hennecke and Allseas specialists decided that the HK 1400/1400, fitted with an MT 26 mixhead, was the best solution. In order to attain the necessary output the high-pressure foaming machine was fitted with frequency converters. Process data acquisition was also introduced for this special application. Trace heating was fitted to the pipelines between the mixheads and machines to prevent the pipes from freezing. The machine itself has been embedded in a container to ensure that it operates independent of the ambient temperature. Dieter Müller, Hennecke’s Regional Sales Manager, says that “the whole solution was developed step-by-step with the customer. The difficulty was that the machines, which are usually stationary had to move along the pipes, with all the equipment. We solved the problem by putting the machines in containers with temperature control.” Hennecke is still in constant contact with Allseas, adjusting the machines according to need. Hennecke employees have been trained and continue to be trained for special work at sea.
Allseas has already successfully realised 12 pipeline projects with Hennecke technology, including in the North Sea, the Atlantic, the Red Sea, the Mediterranean and in Argentina where a pipeline was laid through the Strait of Magellan. The company has said it especially values the reliability of Hennecke technology and the fact that results can easily be reproduced. Given the dimension of the Nord Stream project, there has to be a high level of confidence between the executing and supplying companies. Moreover, quality and availability of the technology play a key role in ensuring that tight schedules are met.
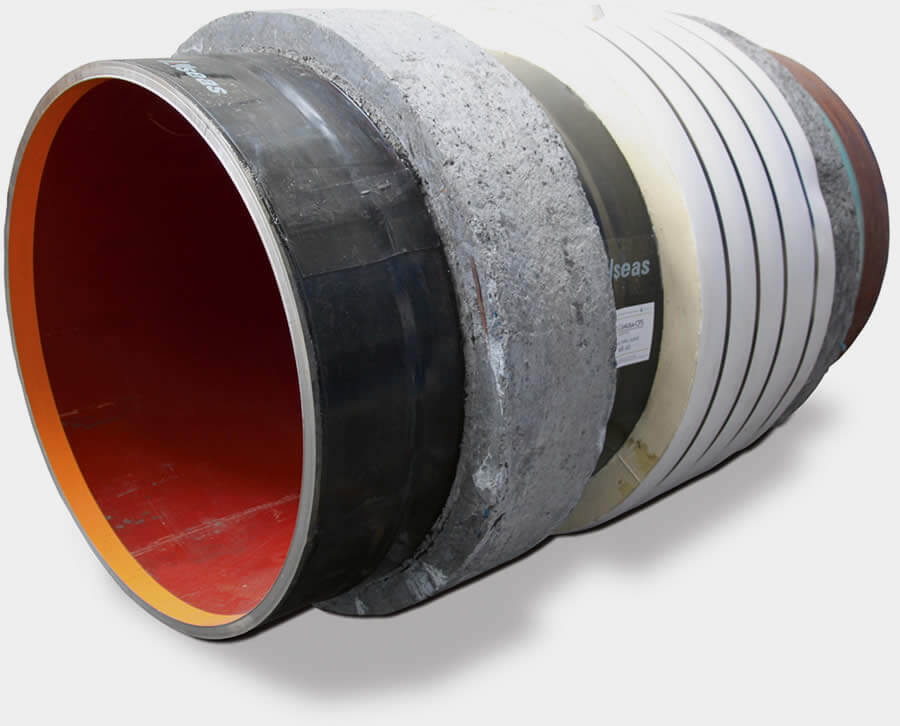
Safe and sound on the seabed
The Nord Stream pipe joints are each 12 metres long and are made out of an especially durable steel that is appropriate for underwater applications. They have a diameter of 48 inches and are provided with a polyethylene anti- corrosion coating. The pipe is sheathed by a layer of steel-reinforced concrete that is between 60 and 110 mm thick. This sheathing protects the pipelines from mechanical damage and prevents the pipes from floating up because of their weight.
One shot every 8 minutes
The steel pipes are automatically welded during the pipe-laying process. Shrink tubing is then pulled over the weld site and the interruption of the concrete sheathing is sealed with a sleeve. The hollow space that is formed is then filled with Elastopor H. Up to 45 (!) kgs can fit into such a fitting. Some 200,000 fittings have to be filled, meaning that HK machines are performing one shot every 8 minutes, 24 hours a day and 7 days a week until the pipe laying operation is over.
Hennecke will present a field joint (pipe with PU fitting) at the 2010 “K” Trade Fair.