Nord-Stream-Pipeline
Teamwork unter Hochdruck
Wenn zwei leistungsstarke Unternehmen kooperieren, sind beste Ergebnisse vorprogrammiert. So geschehen zwischen der Hennecke GmbH und der Allseas Group S.A. Beide Firmen kooperierten eng zusammen und entwickelten eine Technik, die sich Tag für Tag unter härtesten Bedingungen bewährt.
Die Rede ist vom Nord-Stream-Projekt, in dessen Rahmen eine Offshore-Gasleitung von der Bucht von Portovaya nahe Wyborg/Russland bis zur deutschen Ostseeküste nahe Greifswald verlegt werden soll. Die Nord-Stream-Pipeline wird aus zwei jeweils etwa 1.224 kilometerlangen parallelen Pipelinesträngen bestehen.
Dies heißt, dass rund 200.000 Pipelinerohre verschweißt und etwa 200.000 Schweißnähte ummantelt werden müssen. Der offenzellige PUR-Hartschaum Elastopor H wird dieser Aufgabe am besten gerecht. Ein Produkt, das ein führender Rohstofflieferant in den vergangenen zwei Jahren hinsichtlich Festigkeit und Verarbeitungsgeschwindigkeit weiterentwickelt und optimiert hat.
Die Nord-Stream-Pipeline wird Russland und die Europäische Union durch die Ostsee direkt verbinden und jährlich bis zu 55 Milliarden Kubikmeter Erdgas zu Unternehmen und Privatpersonen transportieren. Der erste Pipelinestrang soll 2011 planmäßig in Betrieb gehen, der zweite 2012.
Die Verlegearbeiten laufen auf Hochtouren. Im April diesen Jahres stach die „Castoro Sei“ von Saipem S.p.A. zum Bau der Pipelines in See. Seit August ist das Verlegeschiff „Solitaire“ der Allseas Group im Einsatz. Mit an Bord: Polyurethan sowie Hennecke-Technik, bestehend aus zwei TOPLINE HKs 1400/1400 mit Tanklagersteuerung. Die „Solitaire“ hat in der Vergangenheit bereits mehrere Verlegerekorde hinsichtlich der Verlegegeschwindigkeit und Verlegetiefe aufgestellt.
Spezielle Technik für speziellen Anwendungsfall
Das optimierte Elastopor H wurde in den beiden vergangenen Jahren entwickelt. Die eingesetzten Polyurethan-Systeme bestehen aus zwei flüssigen Komponenten, die auf der „Solitaire“ mittels Hennecke-Hochdruck-Reaktionsgießmaschinen auf Druck gebracht, mit dem Mischkopf MT 26 vermischt und in den Muffenhohlraum eingefüllt werden. Beim MT 26 handelt es sich um einen neuen Mischkopf, der speziell für Hartschaum entwickelt wurde. Als Anbaumischkopf erzielt er eine Austragsleistung von 1 bis max. 3 kg/s. Außerdem ist er mit besonderen Gleichdruckdüsen ausgerüstet, die eine Veränderung der Austragsleistung unter gleichen Druckverhältnissen erlauben.
Dank seiner guten Fließfähigkeit verteilt sich das PUR-System gleichmäßig und schnell im Hohlraum. Damit der PUR-Hartschaum keinen Auftrieb erzeugt, ist er offenzellig eingestellt und saugt sich unter hydrostatischem Druck voll Wasser. Entscheidend ist hierbei die Formstabilität. Der PUR-Hartschaum zeichnet sich durch eine hohe Rohdichte von 160 Kilogramm pro Kubikmeter aus, die die anspruchsvollen physikalischen Eigenschaften sicherstellt. Diese Eigenschaften sind erforderlich, um die Schweißnähte vor Anker- und Netzschäden zu schützen.
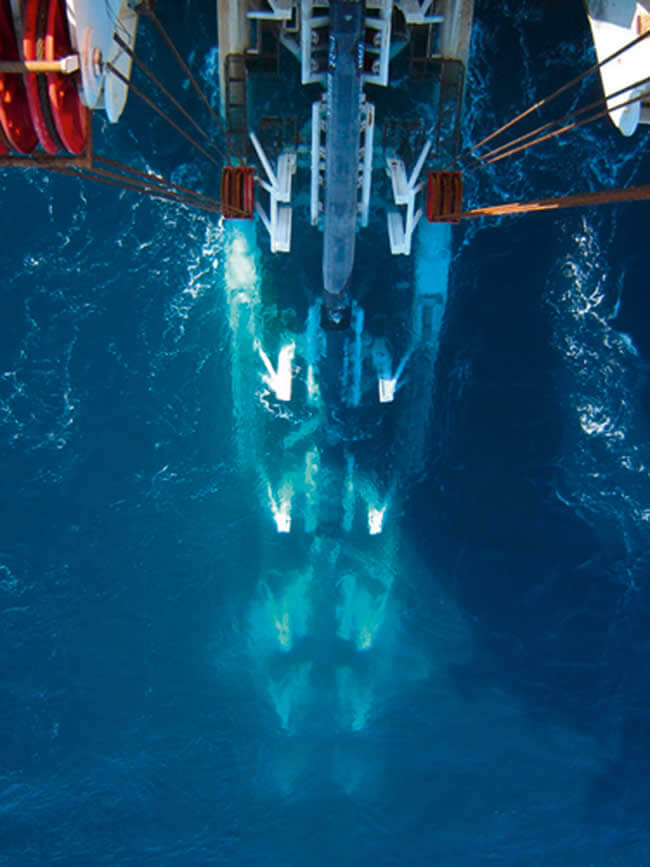
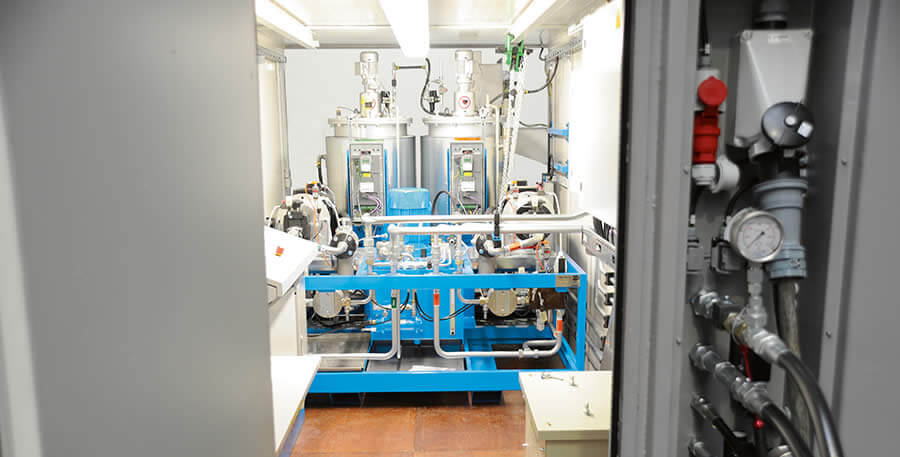
Hennecke und Allseas – ein starkes Team
Die in der Schweiz ansässige Allseas Group wurde 1985 gegründet und ist eines der größten Unternehmen für Offshore-Rohrverlegearbeiten und Unterwasser-Baumaßnahmen weltweit. Allseas betreibt sechs Spezialschiffe, die hausintern entwickelt wurden.
Auf der letzten K-Messe trat Allseas mit einer Anfrage nach einer speziellen Maschine an Hennecke heran. Diese sollte mobil für ein Schiff ausgerüstet werden können, über eine Austragsleistung von 3 kg/s verfügen, für Rohstoffsysteme mit Mischungsverhältnissen von 50 bis 100 bzw. 100 bis 150 geeignet sein und einen eigenen Kühlkreislauf bei einer Umgebungstemperatur von minus 30° Celsius bis plus 50° Celsius besitzen.
Nach gemeinsamen Beratungen fanden dann die Hennecke- und Allseas- Spezialisten in der HK 1400/1400 mit dem Mischkopf MT 26 die beste Lösung. Um den geforderten Austragsleistungen gerecht zu werden, wurde die Hochdruck-Reaktionsgießmaschine mit Frequenzumrichtern ausgestattet. Außerdem wurde für diesen speziellen Anwendungsfall die Prozessdatenerfassung eingeführt. Um ein evtl. Einfrieren der Leitungen zu verhindern, wurden diese zwischen den Mischköpfen und Maschinen mit einer Begleitheizung ausgerüstet. Auch sitzt die Maschine fest in einem Container, um die Betriebsfähigkeit unabhängig von den anfallenden Umgebungstemperaturen sicherzustellen. „Die gesamte Lösung wurde Schritt für Schritt gemeinsam mit dem Kunden entwickelt“, betont Dieter Müller, Regional Sales Manager bei Hennecke. „Die Schwierigkeit“, so Müller weiter, „bestand darin, dass die Maschinen, die sonst an einem festen Ort stehen, sich jetzt entlang der Rohrleitungen mit allem Zubehör bewegen. Dieses Problem haben wir damit gelöst, dass die Maschinen in einen temperierten Container installiert wurden.“
Nach wie vor steht Hennecke in laufendem Kontakt zu Allseas, um die Maschinen den wachsenden Anforderungen anzupassen. Auch wurden und werden von Hennecke Mitarbeiter für das spezielle Arbeiten auf See ausgebildet.
Allseas hat bereits zwölf Leitungsprojekte mit Hennecke-Technik erfolgreich realisiert, darunter in der Nordsee, im Atlantik, im Roten Meer, im Mittelmeer und in Argentinien beim Verlegen einer Pipeline durch die Magellan-Straße. Das Unternehmen schätzt nach eigener Aussage vor allem die Zuverlässigkeit der Hennecke-Technik und die Reproduzierbarkeit der Ergebnisse. Angesichts der Dimension des Nord-Stream-Projektes muss das Vertrauen zwischen ausführender und liefernder Firma stimmen. Ebenso die Qualität und die Verfügbarkeit der Technik, damit die engen Zeitvorgaben eingehalten werden können.
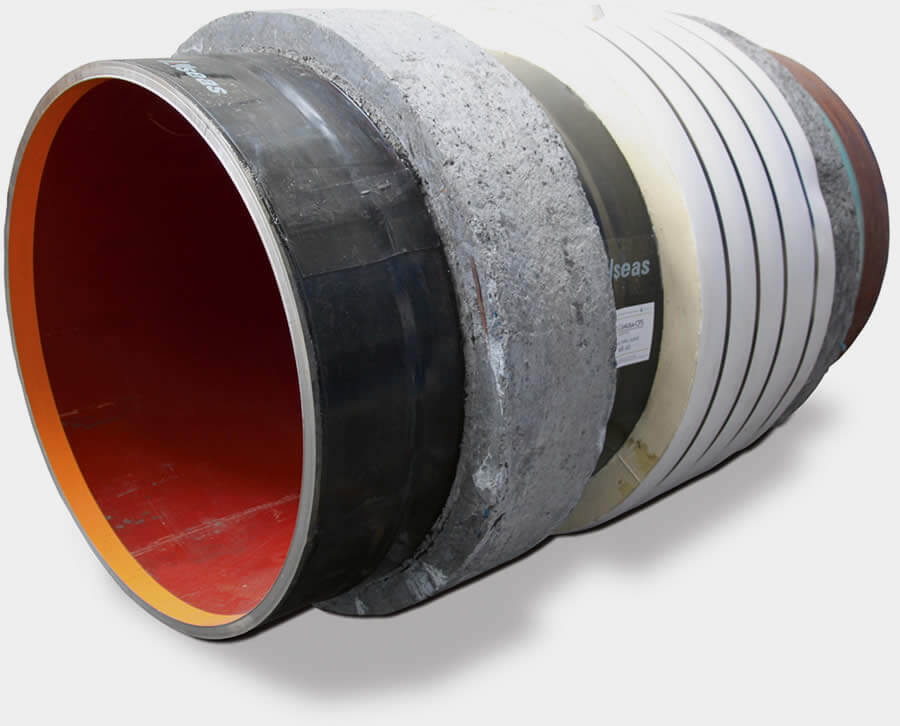
Fest und sicher auf dem Meeresgrund
Die Rohrverbindungen der Nord-Stream-Pipeline (pipe joints) sind jeweils zwölf Meter lang und bestehen aus besonders haltbarem, für Unterwasser-Anwendungen geeigneten Stahl.
Ihr Durchmesser beträgt 48 Zoll und sie sind mit einem Anti-Korrosions-Coating aus Polyethylen beschichtet. über dem Coating wird das Rohr mit einer eisenarmierten Betonschicht ummantelt, die zwischen 60 und 110 Millimeter dick ist. Diese Ummantelung schützt die Pipeline vor mechanischen Schädigungen und verhindert durch ihr Gewicht ein Aufschwimmen der Rohrleitung.
Alle acht Minuten ein Schuss
Verschweißt werden die Stahlrohre robotergesteuert während des Verlegeprozesses. Danach wird über die Schweißstelle ein Schrumpfschlauch gezogen und die Unterbrechung des Betonmantels mit einer Hülle verschlossen. Der dadurch entstehende Hohlraum wird nun mit Elastopor H aufgefüllt. Bis zu 45 kg passen in eine solche Muffe. Da rund 200.000 Muffen gefüllt werden müssen, heißt das für die HK-Maschine, dass alle acht Minuten ein Schuss ansteht, 24 Stunden am Tag, 7 Tage die Woche – bis die Verlegearbeiten abgeschlossen sind. Auf der K-2010 wird Hennecke ein Field Joint (Rohr mit PUR-Muffe) präsentieren.
Download - Ausgabe 210 (PDF)
Zur Betrachtung benötigen Sie den Adobe® Reader®, den Sie hier kostenlos herunterladen können.