Efficient air conditioning technology
thanks to PU insulation
Hennecke recently completed a major capital equipment installation for Trane to produce residential air handlers with Polyurethane foam insulation. For over 100 years, Trane (part of Ingersoll Rand) has been a worldwide leader in the production and sale of heating, ventilating, and air conditioning systems for both residential and commercial applications. Recently, Trane decided to introduce a new line of air handling units (AHUs) for residential applications. The new “Hyperion”AHUs have many innovative technological advancements from earlier systems. One of these enhancements is in using PU foam as an insulating barrier within the cabinets and doors of the AHU.
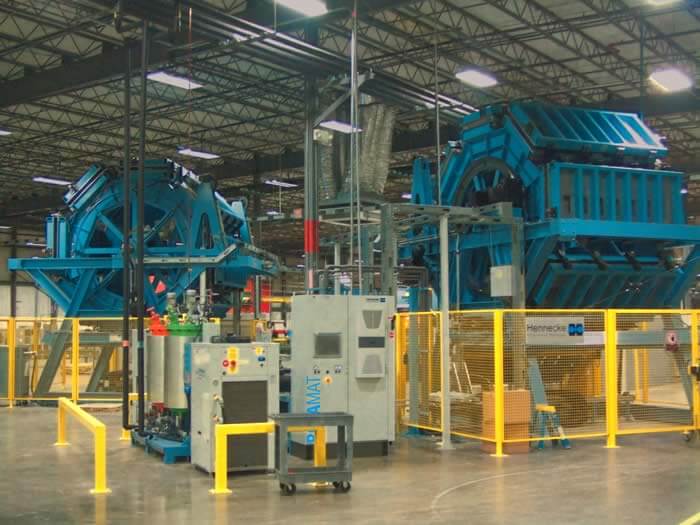
Historically, mineral wool has been the insulation material used within AHUs. However, use of PU instead of mineral wool has several benefits:
- PU can be poured automatically into the AHU, whereas mineral wool must be applied manually within the AHUs, which is both costly and a potential safety and health hazard (having production employees working with a glass fiber product and working within metal enclosures to apply that product)
- PU (due to its flowability) completely seals the cabinet, increasing efficiency of the AHU
- PU maintains its insulation value (“R” value) through the life to the AHU, whereas mineral wool has virtually zero “R” value once it is wet, which oftentimes happens from “sweating”, leaks, during installation, etc.
- PU adds to the structural stability of the end product, whereas mineral wool does not.
In part due to these reasons, Trane decided to switch from mineral wool to PU foam to increase the quality of their AHUs. However, Trane was a newcomer to using PU foam insulation and needed a partner to work with them every step of the way from design to full-scale production. Hennecke became that partner of choice. Hennecke supplied all the new capital equipment required for the conversion to PU foam. This equipment included “wet” end equipment and “dry” end equipment.
The wet end equipment included bulk chemical storage systems as well as chemical metering systems. The dry end equipment included foam fixture devices for the cabinets (oval conveyors) and for the doors (ROTAMAT).
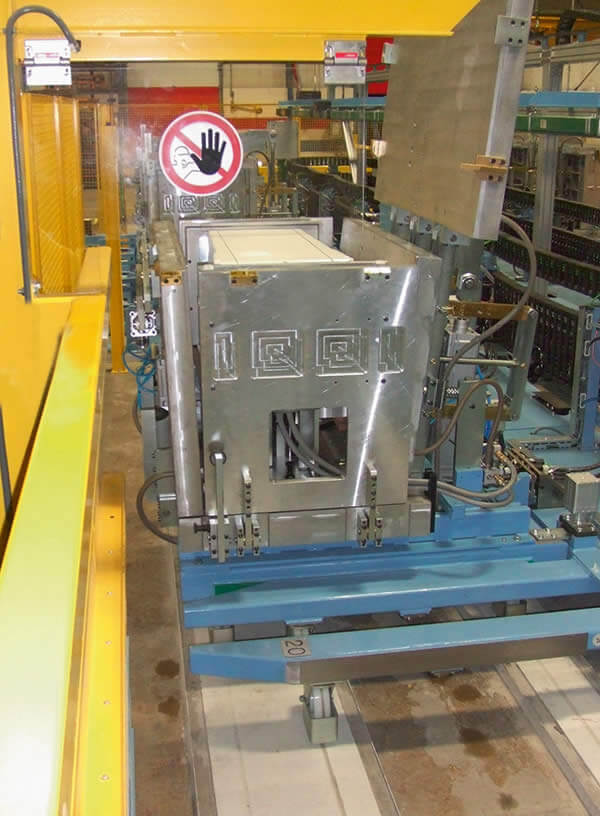
Trane decided to utilize a two part polyurethane foam. The poly side is pre-mixed with the blowing agent and all other additives. Both the poly blend and the iso are received in tanker truckloads. Hennecke supplied the unload skids, bulk chemical storage tanks, closed loop temperature conditioning systems, chemical transfer skids, and all controls for the bulk system. Additionally, Hennecke designed and installed the bulk system pipe loop to supply chemicals to all four lines within the facility. Each line incorporates a Hennecke TOPLINE HK 270R metering system with MX mixhead to meter the foam into the cabinets and doors. These metering systems include day tanks with closed loop temperature control of the chemicals, metering pumps with variable frequency drives and magnetic couplings, flow meters, pressure and temperature sensors, and all the other high quality components typical of Hennecke metering equipment.
For production of cabinets, Hennecke supplied two oval conveyor lines. These lines include universal foam fixture devices with profile-specific tooling mounted in each fixture. The lines operate automatically and continuously – the only operator involvement during normal production is manual loading of non-foamed cabinets and manual unloading of foamed cabinets which have been cured by the time they reach the unload area of the oval conveyor line. Hennecke utilizes optical sensors to ensure a cabinet has been loaded into a tool prior to foaming (to prevent pouring foam into a fixture that does not contain an actual cabinet). Hennecke also utilizes RF tags to determine which part is being foamed. This information is used to automatically adjust the metering system parameters to ensure the correct foam fill for each unique sized cabinet. The mixhead is mounted on a robotic arm and line tracking is used to properly position the mixhead to the pour hole of the cabinet as the line runs continuously in order to complete the foam fill. The oval conveyor lines have a convenient quick change load and unload area for changing out cabinets in rapid fashion if necessary.
For production of doors, Hennecke supplied two RotaMats to allow for closed mold pouring of the preformed doors. A ROTAMAT is a vertically operational foam fixture device that takes up much less floor space than a typical turntable sized for the same part capacity requirements. Each station of the ROTAMAT can accept several individual door molds. As with the oval conveyor lines, the ROTAMAT lines operate automatically and continuously, with the only operator involvement being the loading of non-foamed doors and the unloading of cured foam doors. Also as with the oval conveyor lines, Hennecke incorporated optical sensors to ensure a door has been loaded into a mold prior to foaming and RF tags to determine which part is being foamed in order to automatically adjust metering system parameters to the unique part requirements. The mixhead is mounted on a linear actuator to position the mixhead at the pour hole location of each of the doors prior to foaming. Changing of molds within the ROTAMAT is extremely simple and fast via bolt connection with centering pin.
Hennecke utilized state-of-the-art Allen Bradley controls for all the equipment within the plant, with remote log-in and troubleshooting and with data highway communications to Trane’s internal plant production management system.