NEXT-GEN-STORE
Hennecke is revolutionizing sales and machine configuration
The NEXT-GEN Store is the first online configurator for polyurethane metering machines and is setting new standards for digital sales channels in the area of capital goods. Similar to a vehicle configurator, which allows you to put together your dream car exactly according to your own requirements and wishes, this now is also available for Hennecke’s metering machines. At a time when transparency and flexibility are crucial for purchasing decisions, Hennecke offers a comprehensive solution with the NEXT-GEN Store and at the same time takes a significant step towards digitizing the polyurethane industry.
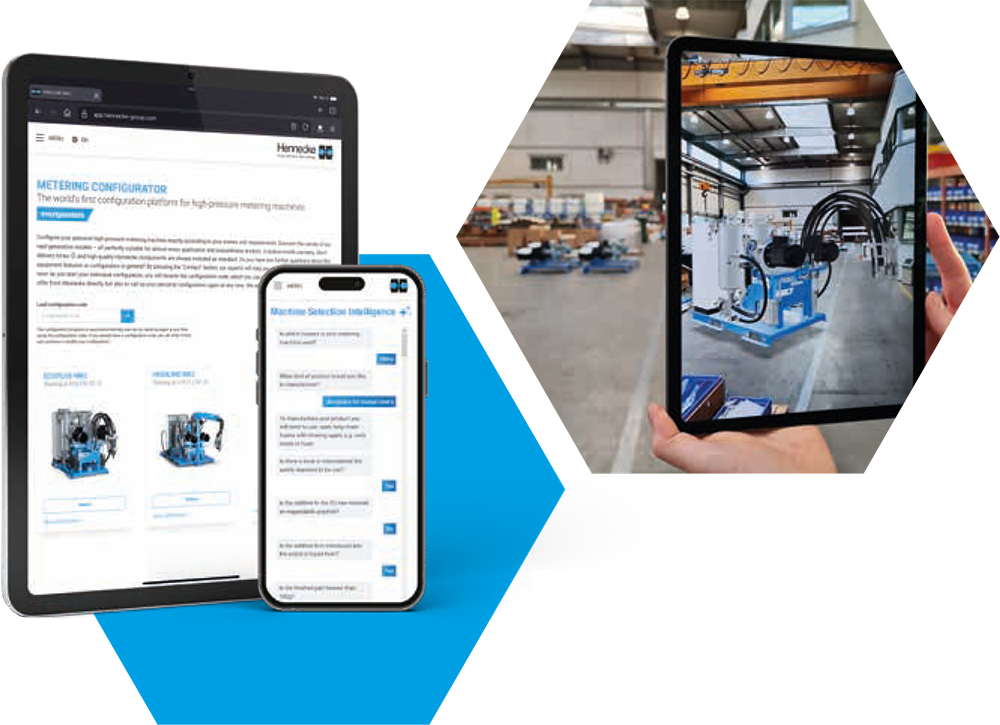
Hennecke‘s pioneering role
Online trading is already an established standard for numerous consumer goods. In the area of capital goods, however, this is still the exception and a rarity in global mechanical engineering. Reason enough for Hennecke to take on the pioneering role in this field too. The NEXT-GEN-Store can be accessed directly from the start page of the Hennecke website and, thanks to its fully responsive design, can be used optimally on PCs and laptops as well as on all mobile devices. Hennecke also makes it extremely easy for its global customers to access the offer: “We have deliberately decided to allow access to the platform without registration in order to allow all customers and partners worldwide to easily explore our metering machines and their numerous features as well as the pricing,” explains Torsten Spiller, Director Global Marketing & Communication at Hennecke.
Gradual expansion of the machine range
The NEXT-GEN Store was launched at the beginning of the year with the high-pressure metering machine ECOPLUS MK2. The HIGHLINE MK2 was recently added, and in the fourth quarter of 2024 the range will be supplemented by the new entry-level metering machine IMPACT MK2. “Our top class will follow at the beginning of 2025 with the TOPLINE MK2. With its extensive equipment options and versatile application possibilities, this model is a real challenge,” reports Jens Winiarz, Senior Director Sales Metering & Composites at Hennecke. Hennecke is deliberately also addressing younger target groups who gather information online on their own and make purchasing decisions independently. “The digital natives are well informed and know exactly what they need and want – and in the beginning that is usually not a sales talk with a customer advisor,” adds Torsten Spiller.
AI-supported machine selection
A central element of the NEXT-GEN Store is the AI-controlled Machine Selection Intelligence, underlining Hennecke´s leading position in digital transformation. This smart tool enables the user to specify the desired semi-finished product or end product to be manufactured before configuring a specific machine series, whereupon the artificial intelligence asks further targeted questions in order to specify the area of application and find the right metering machine. “The AI identifies the right machine, the right mixhead and the right nozzles within seconds,” explains Jens Winiarz enthusiastically. The AI is particularly helpful for users who are unsure which machine best meets their requirements. The Machine Selection Intelligence uses extensive databases of components and raw materials to recommend the ideal machine system. By asking specific questions, for example whether the product requires special features such as fire protection properties, the tool guides the user to the right solution with just a few inputs. This enables the metering machines to be precisely tailored to the customer’s needs, because the system finds the optimal result for almost every PU product with its individual properties.
Focus on user-friendliness and transparency
In addition to the upstream, intelligent selection, the platform naturally offers a simple and quick configuration of the machines. The first step is to select the country in which the metering machine is to be used. This is essential, as the guidelines and specifications can differ greatly from country to country. “We are very proud that we have managed to set up a single global NEXT-GEN Store despite the regionally different machine versions,” says Jens Winiarz. The platform provides extensive details about the technical specifications of the machines and the possible configurations. Step by step, it informs the user for example about options that can be used to save energy and which options reduce maintenance costs. User-friendly additional options can also be configured directly, such as the optional REMOTE HMI function, which allows a difficult-to-access machine to be conveniently controlled via Wi-Fi using a mobile device or even a smart TV.
Efficient ordering process
For the entry-level models IMPACT MK2 and ECOPLUS MK2, the platform immediately shows the final price of the individually assembled machine – a clear sign of Hennecke’s commitment to maximum transparency. In addition, customers are immediately informed about the expected production times, which enables them to plan better. After defining the individual settings and features, the user receives their own configuration code, which can be used to call up the desired configuration at any time.
Your next-gen metering machine in just a few steps
1. GENERAL INFORMATION
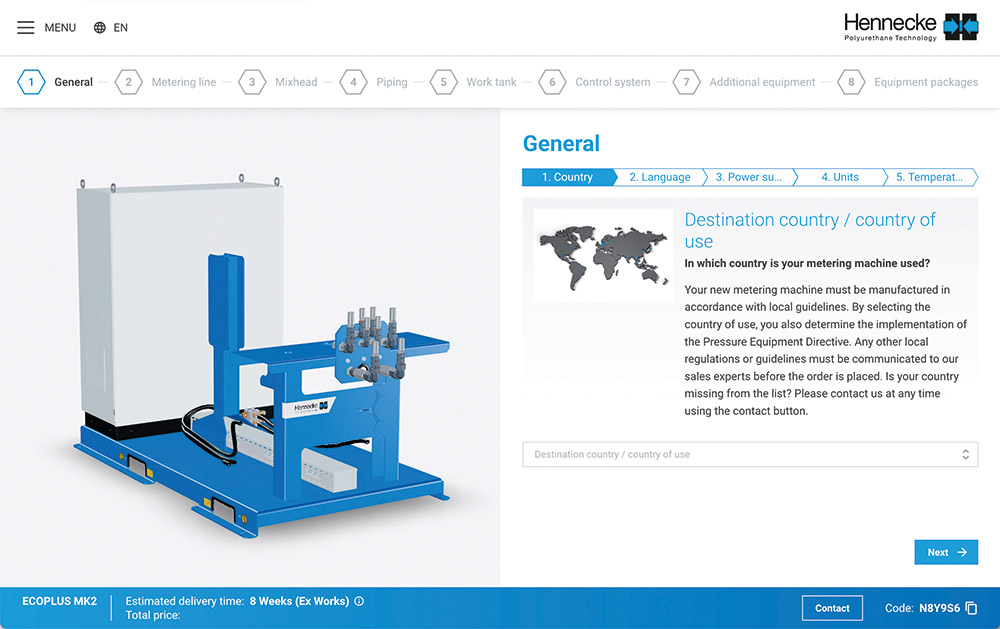
2. METERING LINE
3. MIXHEAD
4. PIPING
5. WORK TANK
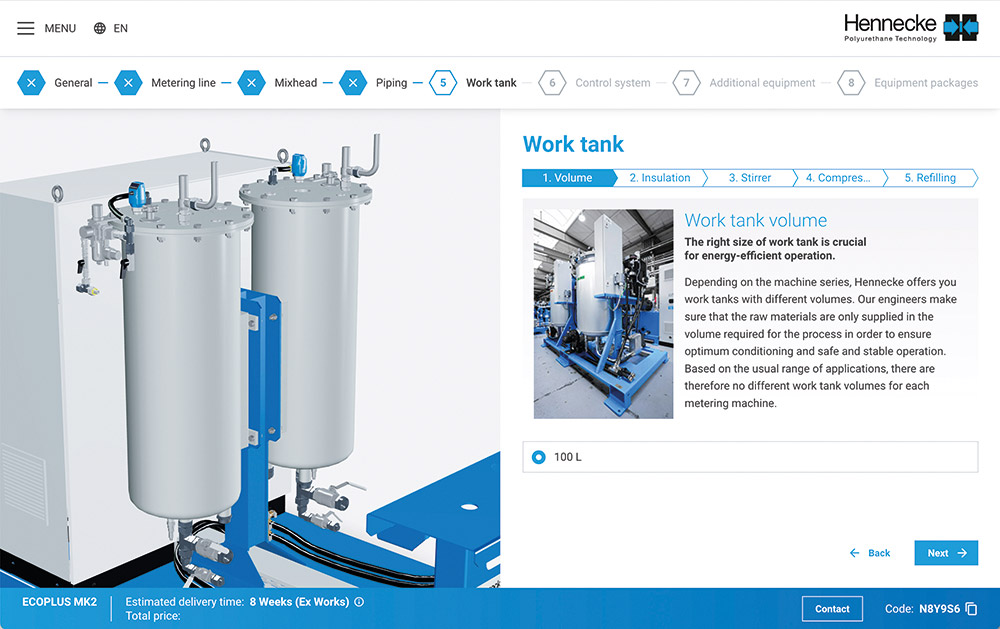
6. CONTROL SYSTEM
7. ADDITIONAL EQUIPMENT
8. EQUIPMENT PACKAGES
9. CONFIGURATION COMPLETED
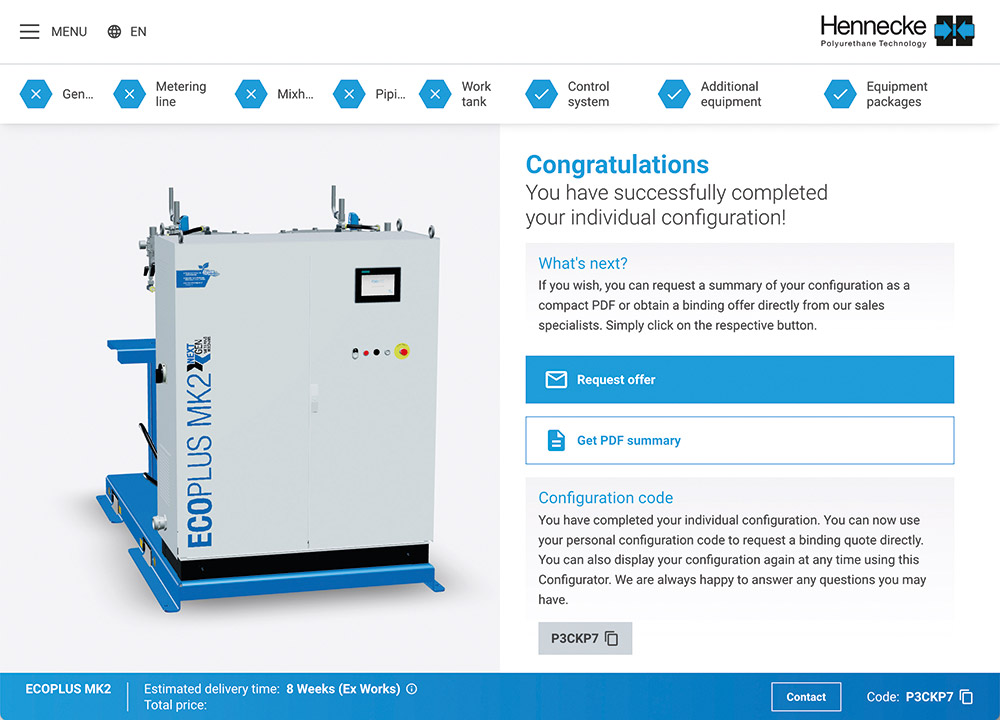
Numerous customer benefits
The NEXT-GEN Store gives users a quick, location- and time-independent overview of Hennecke’s metering machines and a comprehensive comparison of the standard machines and their functions. During configuration, a corresponding 3D model is created in real time. This is crucial for another innovative highlight of the store: the ability to view the individually configured machine system directly at the intended location at the customers own production using Augmented Reality (AR). The image is accurate to the centimeter. This makes planning much easier and minimizes the risk of making wrong decisions, as the machine is visualized true to scale at the planned location. “The platform speeds up the ordering process considerably. Once the customer has configured their machine system, it usually takes less than two days to receive an order-ready quotation,” explains Jens Winiarz. And if a customer cannot find a required function or has a question, Hennecke’s metering machine specialists can be reached at any time via a contact button for the individual configuration.
The NEXT-GEN Store is therefore more than just an online configurator – it is part of the digital transformation in mechanical engineering. Hennecke will continuously expand its range and, in addition to integrating further metering machines, will also increase the range of functions in order to make the selection and purchase process as simple and efficient as possible. The polyurethane experts are familiar with new standards: not only in the machine technology itself, but also when it comes to modern and transparent sales.