Service-Consulting
Hennecke‘s new service to increase efficiency, quality and sustainability
One company is struggling with inexplicable quality fluctuations in production, another manufacturer is suffering from a consistently high scrap rate. And the next one wants to know how to optimize its existing systems to save energy and raw materials. To meet all of these challenges, Hennecke has expanded its service portfolio to include the Service Consulting product. This means that a broad range of customers have access to in-depth expert knowledge and tailor-made solutions that can be used to achieve sustainable competitive advantages.
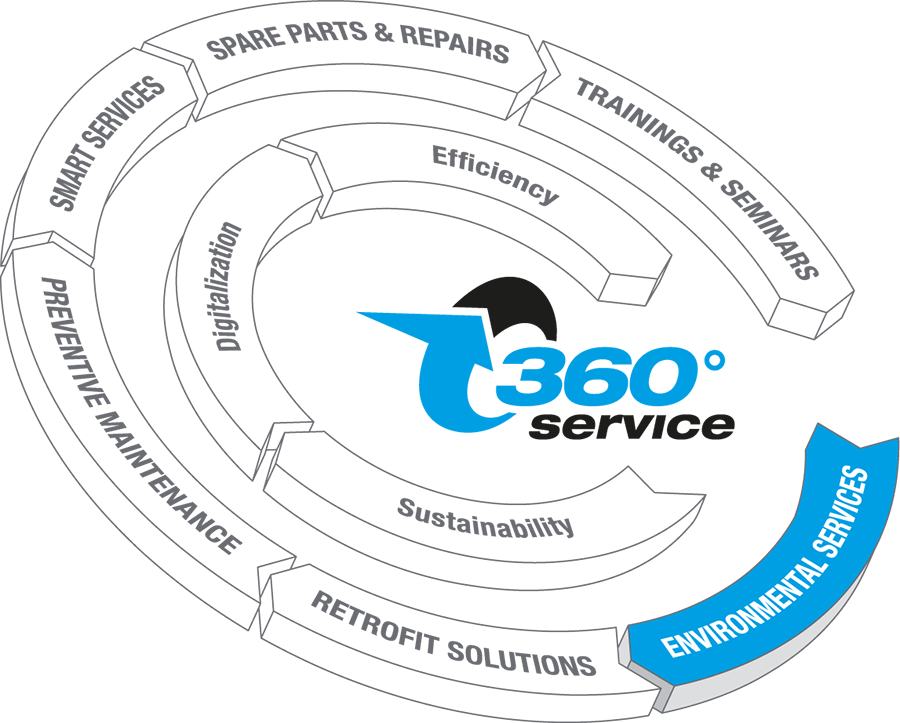
With the introduction of Service Consulting in the area of 360°ENVIRONMENTAL SERVICES, the expert in polyurethane machine and plant technology is making its know-how available to its customers for process optimization and production reliability. “Regardless of whether it is about specific production problems, general resource efficiency or the optimization of machine performance – we have decades of experience and in-depth knowledge in all areas of PU applications. We would like to make this available to our customers even after commissioning,” explains Nils Baumann, Sales Specialist Customer Value Service at Hennecke, the new offer in the sustainably oriented portfolio of 360°Service.
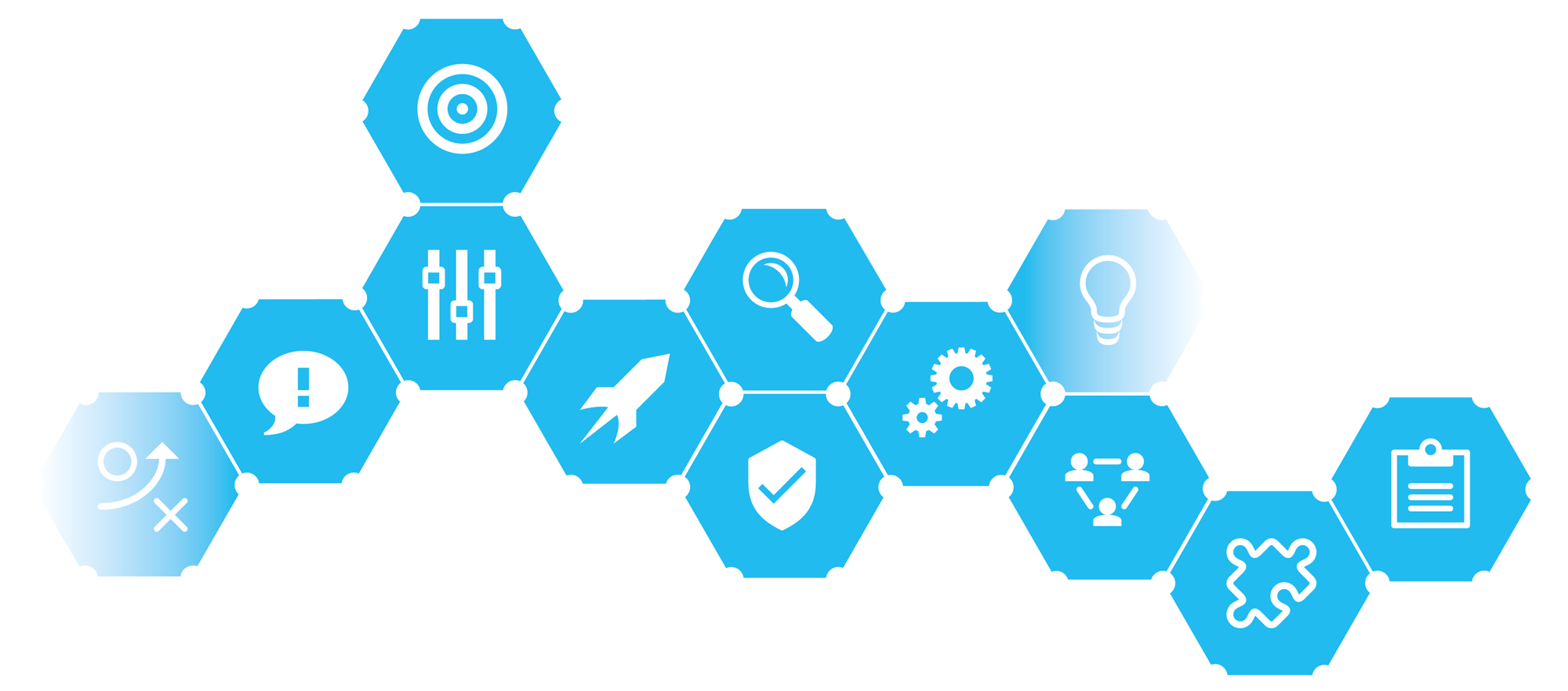
Process analysis from start to finish
Nils Baumann reports on a producer who was struggling with a scrap rate of over 30 percent and was unable to locate the error. The situation was particularly urgent because scrap caused high losses every day in highly complex components. Hennecke’s experts were called in to conduct a detailed analysis of the production process and determined that the error was in a completely different location than the manufacturer had previously assumed. This enabled them to develop helpful solutions in the area of the specific design of the molds from a third-party provider, among other things, and thereby drastically reduce the scrap rate. Due to the enormous cost savings from eliminating the error, the investment paid for itself within a very short time.
Individual and tailor-made solutions
“The countless production scenarios of polyurethane processors are as varied as the problems that arise,” explains Martin Krupp, R&D process engineer at Hennecke. That is why there are no standard solutions. Thanks to the profound, interdisciplinary know-how of the PU specialists, highly specific and customized solutions are developed. “These include precise machine settings, using and conditioning raw material systems, advising on environmental influences, and training operators,” says Krupp.
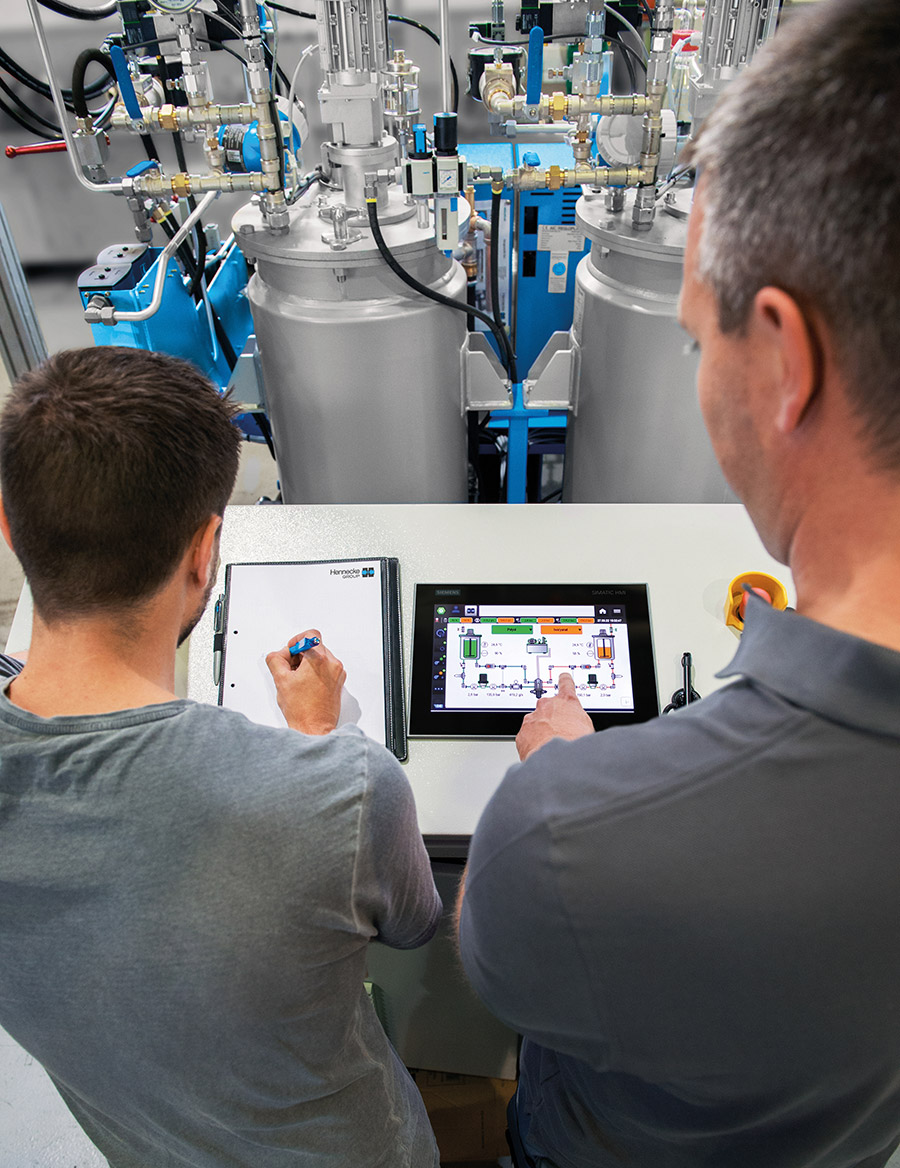
Optimizing production processes
The Service Consulting focuses on improving product quality, reducing production costs and at the same time increasing production stability. Through a comprehensive and holistic analysis of the entire production process – both in process technology and in chemical processes – and the interdisciplinary know-how of the service specialists, solutions are found that are often outside the producers‘ field of vision. This was also the case with another PU processor, says Nils Baumann: They only achieved optimal results within a small production window of around two hours. Before and after this, defects accumulated and product quality fluctuated considerably over the course of the day. The process analysis by the Hennecke specialists covers both process technology and chemical processes. They quickly identified the fluctuating ambient temperatures as the primary cause, as these have a significant influence on the extremely reactive media. “The next step was to analyze the chemicals, examine the mixing ratios and determine the optimal parameters of the system in terms of pressure and temperature,” reports Nils Baumann. With the detailed specifications provided by the external experts, the manufacturer was able to adapt its process technology, condition the raw materials accordingly, and train the operating personnel to achieve consistently high product quality ever since.
Comprehensive range of services
The new service from Hennecke offers comprehensive optimization of machine performance, advice on innovative core components, sustainable process improvements and the identification and elimination of avoidable production costs and sources of error. The offer also includes tool optimization, chemical advice and increasing production stability. This leads to more efficient and sustainable production, which helps users to reduce their costs. “The focus is on reducing the use of raw materials, saving energy, avoiding cuttings and rejects and minimizing disposal costs,” explains Jens Geuer, Head of R&D Process Engineering at Hennecke. The savings achieved in this way amortize the service costs in a short time.
Independent process consulting also for beginners
For this reason, the Service Consulting team is also requested even if there are no specific problems. As external experts, they look at the production process objectively and independently. “Because even what was good for many years can now often be made even more efficient, more economical and simply better thanks to new findings and innovative retrofit solutions,” says Jens Geuer. Service Consulting thus ensures sustainably optimal quality and at the same time extends the best possible use of the existing system technology. In addition, the experienced team also supports companies in their search for an optimal solution if they do not yet have a concrete idea of which machine or process solution is suitable for them due to a lack of experience or unclear production requirements. The goal is always a highly efficient and resource-saving production process that gives customers a sustainable competitive advantage.
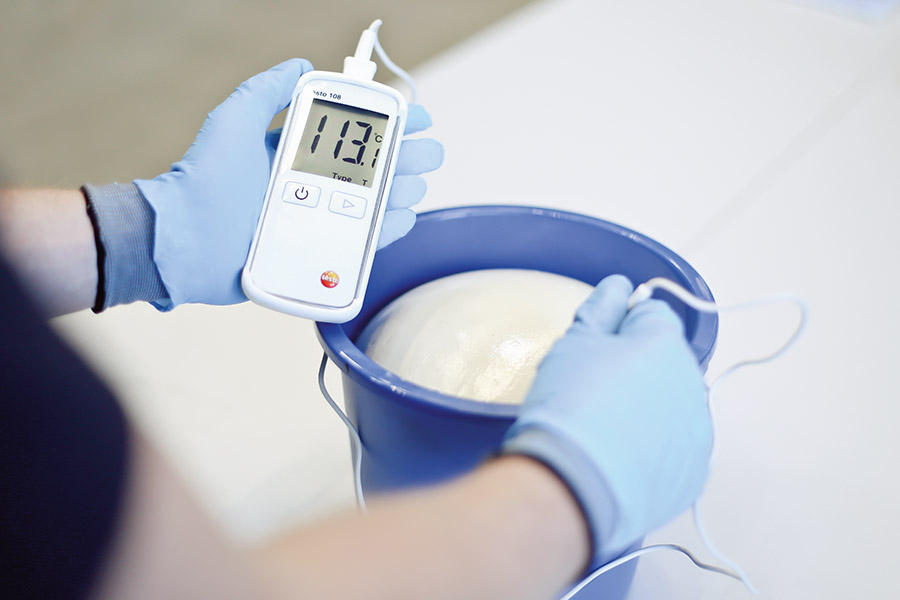
Consulting process: Security for customers
“Companies that use Hennecke‘s Service Consulting are on the safe side and always benefit from the offer,” assures Nils Baumann. In a non-binding and free preliminary discussion, a service specialist will gather details about the existing initial situation. Only when there is a concrete prospect of success will a transparent offer with a detailed description of the service be drawn up, which the company can accept and thus commission the service. Of course, absolute confidentiality is guaranteed. After the process analysis and evaluation, the customer receives his individual solution proposals. A detailed final report ensures a stable and cost-efficient production process in the long term.