From the idea to the product
The TECHCENTER as the key to product development
The Hennecke technical center offers a comprehensive platform that supports customers from the initial concept phase to series production. The development of new products in particular requires much more than just pure manufacturing technology. This highly specialized center combines the latest manufacturing technologies with in-depth process engineering and chemical know-how to realize innovative product ideas.
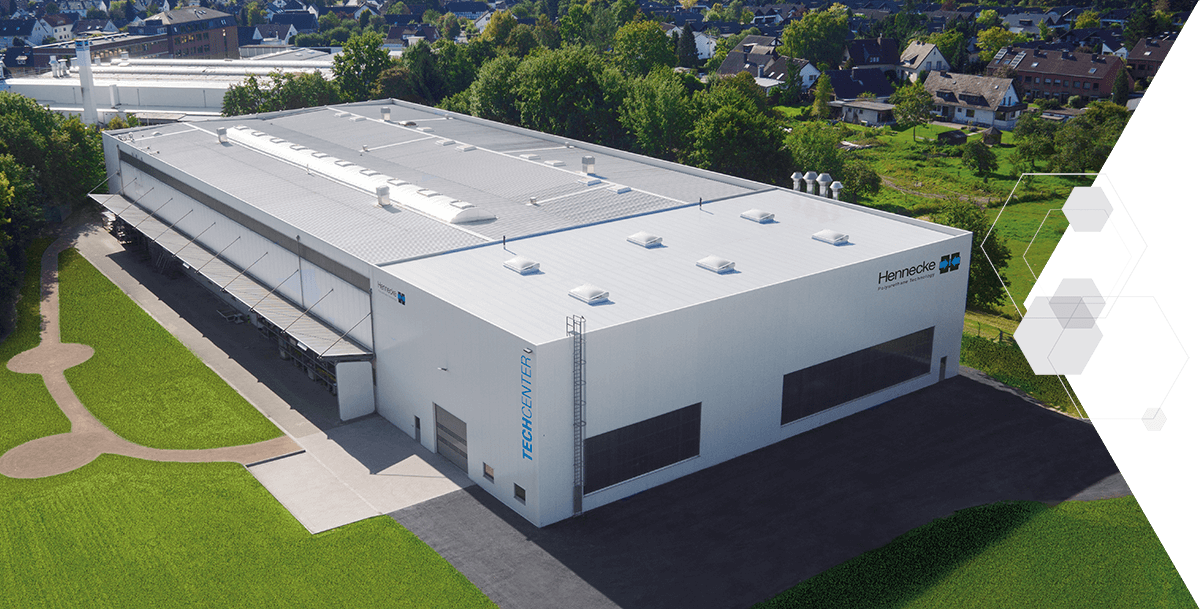
Development partner for customer requirements
Hennecke‘s TECHCENTER is geared towards processing a wide range of requests. Customers from the polyurethane industry as well as companies from outside the industry turn to the PU specialists to overcome technical challenges. The range of tasks is diverse: Often it involves the substitution of materials – keyword “vegan leather” – or the implementation of new regulatory requirements, for example when a flame-retardant material can no longer be used and an alternative is required. ESG requirements are also of increasing interest, for example to produce pure products that facilitate recycling and increase sustainability or in the area of effective insulation. “We regularly receive requests that require both technical and chemical expertise,” explains Sven Strobel, Process Engineer at Hennecke and project coordinator. “We see ourselves as development partners: Our job is to work on these complex issues in an interdisciplinary manner and to jointly develop processes that meet the specific requirements of our customers.”
Interdisciplinary expertise
The Technical Competence Center offers customers significant added value through the collaboration of a multidisciplinary team that consists of process engineers as well as chemists. “With seven employees, we have more than 150 years of combined know-how in PU technology and cover all relevant aspects of material and process development,” says Sven Strobel. This indepth expertise enables the development of tailor-made solutions based on a deep understanding of both the process engineering and chemical processes. “Our strength lies in the interdisciplinary collaboration between our on-site specialists and our network of external partners such as raw material suppliers and tool manufacturers,” adds Jens Geuer, Head of R&D Process Technology. “This combination of different areas of expertise enables us to develop precise and efficient solutions.”
“Our strength lies in the interdisciplinary collaboration between our on-site specialists and our network of external partners such as raw material suppliers and tool manufacturers.”
Jens Geuer,
Head of R&D Process Technology
The TECHCENTER is equipped with state-of-the-art process technology that covers almost all PU processing technologies, including rigid, flexible and integral skin foams, elastomers and epoxy resin systems. Specialized applications such as RIM, RRIM, SRIM and HP-RTM are also developed and optimized in the technical center. The laboratory furthermore enables detailed material analyses and the fine-tuning of formulations.
5-stage process for series production
In order to efficiently meet the different requirements of customers, Hennecke has developed a structured 5-stage process that covers the entire development cycle from the initial idea to product series readiness. Of course, the company attaches particular importance to the highest level of confidentiality and the protection of its customers‘ intellectual property throughout the entire process.
Foundation for innovative strength
Hennecke‘s technical center offers comprehensive equipment for the development and optimization of PU applications on an area of 1000 square meters. In addition to the latest process and process technology, the laboratory also enables material analysis and optimization. The services include process development, raw material testing under near-series conditions as well as product development and optimization. Customers benefit from an interdisciplinary approach that combines all relevant specialist knowledge to create tailor-made solutions. The TECHCENTER is of course not just a service unit, but also forms the backbone for the continuous development of Hennecke‘s own products and technologies. “The innovation center is the core of our research and development,” explains Thomas Scheffler, Vice President Corporate Development. “Not only do we develop customized solutions here, we also create all new processes and machines that strengthen our own innovative power.”

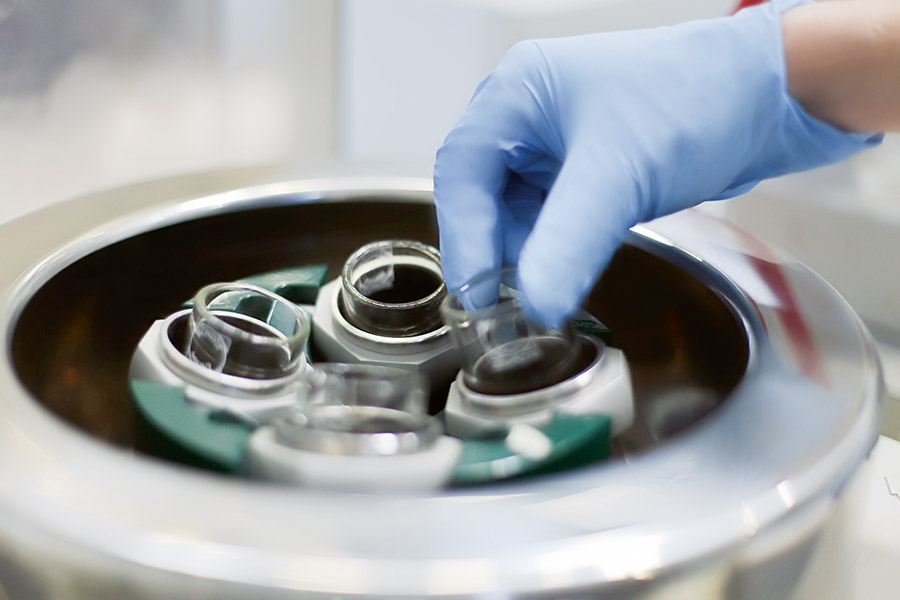
Series production in five stages
Requirements analysis and idea generation
In the first phase, the customer‘s requirements are recorded and analyzed in detail. This includes the evaluation of specific challenges and the feasibility test. Typical examples of application include the substitution of an existing material, the production of pure products or the development of new components.
Process and material development
This phase includes the development and adaptation of processes as well as the selection of suitable materials. This includes a check of which production facilities and processes can be used optimally and which chemical requirements are necessary. Close cooperation between all those involved is necessary in order to define the limits of the planned application.
Integration and partnerships
The development process is expanded by integrating specialized partners such as toolmakers and raw material suppliers. Kick-off meetings serve to coordinate between all those involved to ensure that the material and process requirements are optimally met. The TECHCENTER plays a central role in evaluating feasibility and carrying out initial technical tests.
Validation and prototyping
The fourth step involves validating the developed processes by producing and testing prototypes. This includes using various technical processes to produce sample components. These are then subjected to a series of tests, also with the support of selected partners, to ensure suitability for series production and compliance with all essential specifications.
Production integration and system installation
In the final phase, the production process is refined to such an extent that smooth integration into series production is guaranteed. The system technology is adapted to the customer‘ s specific requirements and prepared for use in production. Then, the finished production system is handed over to the customer, accompanied by comprehensive instruction and support during the start-up phase.
Hennecke supported the Singapore-based company Keshet Agritech Pte. Ltd. in the development of an innovative insulation application based on rigid polyurethane foam.
“All contact persons at Hennecke were important companions for us during the entire process. They have shown remarkable flexibility, which is crucial for a project with a high degree of innovation and specific challenges due to its scale. The expertise of the Hennecke team played a crucial role in conducting pioneering trials as our product is a unique development. Their valuable suggestions, creative working methods and daily hands-on involvement have been instrumental in achieving the desired results. The machines used in Hennecke’s TECHCENTER also proved to be extremely efficient and met our requirements in terms of processing different component sizes and polyurethane quantities.”
Serene Lim,
Sustainable Capital Management at Keshet Agritech Pte. Ltd.