Modular and with many new features
Premiere of the SMARTFLEX continuous slabstock systems for cost-efficient production of high-quality flexible foams
Hennecke is presenting the latest addition to its slabstock line portfolio at the 2019 K show: The new SMARTFLEX is fitted entirely with high- quality and standardized plant components and offers an impressively great price-performance ratio. On their stand at the K show, the PU specialists are exhibiting the wet part of the plant, with a focus on the many new features of the SMARTFLEX, including the new visualization and control software FOAMWARE.
In order to be competitive on the market, processors must be able to offer their customers high-quality products with a wide range of specific properties. The combination of precise high-pressure metering and a powerful stirrer mixer makes Hennecke's continuous slabstock lines the perfect partner in the efficient processing of all commercial materials. Here the MULTIFLEX is Hennecke's best-selling slabstock line, guaranteeing the processor a highly efficient raw material yield and extremely good foam qualities in the continuous production of slabstock foams. Thanks to extensive standardization and an entirely modular design, Hennecke has been able to combine important distinctive features of the MULTIFLEX series with noticeably shorter assembly times in a new production system: the SMARTFLEX. This plant concept is aimed at polyurethane processors who have not yet been able to invest in the comparatively more complex MULTIFLEX system.
Hennecke achieves the fast assembly times through a consistently modular assembly and disassembly concept. The wet part of the SMARTFLEX is fully assembled at the Hennecke site in Sankt Augustin and all pump sets and electronic parts are parameterized and commissioned. The system is then disassembled into larger modules and transported to the customer in standard containers. The final assembly can then be carried out in a simplified process on site by a Hennecke technician. In this way, the assembly and disassembly of the SMARTFLEX is quicker than for example with the MULTIFLEX. The modular SMARTFLEX plant concept is also impressive from a qualitative point of view: The material flows through the mixer from bottom to top, which means it is possible to fill the mixing chamber before the foaming begins, so that the mixture expels any remaining air and thus prevents the formation of air bubbles which could damage the metering and mixing system. The mixer is mounted directly on to the feed table, which allows for a very short pipe line between the mixer and the dispenser. The dry part is the same as in the conventional foaming systems, with the exception of the feed table.
Hennecke's proven polyurethane technologies are of course also used in the SMARTFLEX. Through high-pressure technology and the liquid laydown technique, processors can achieve a highly efficient raw material yield and the best foam qualities in the continuous manufacture of slabstock foams. The rectangular block system is a significant part of this process and is offered into two different variants in the new SMARTFLEX: the classic Flat-Top system and the new Block-Shape system with side foils and an additional, optional foil on the block. Hennecke has also put its long-standing experience in continuous slabstock foam production to good use in the paper guiding system.
The lower paper is wound up underneath the laydown table. The paper is directed and turned up so that a deflection plate is formed. This MIXGUIDE system is also used in NOVAFLEX® processes. For this purpose, the MIXGUIDE deflection plate is pushed all the way to the front of the feed table. The system is designed for a maximum of 20 additives, eight polyols and four isocyanates. The additives are strictly installed with a rise so that the lines can easily be ventilated. This ventilation of the additive lines is important because recirculation lines have been intentionally omitted in favor of shorter pressure build-up times when starting the pumps. Non-return valves are installed directly behind the pumps. In the standard configuration, the additive lines are secured at 40 bar in order to be able to use the new SMARTJECTOR injectors. Additives with a large output range are stored in a tank farm. Tin is added directly to the mixing chamber via an injector, as is usual. In the SMARTFLEX systems, only the flow rates of the water, methylene chloride, isocyanate and tin are measured. Isocyanate, additives with a large output range and the polyols have a recirculation line. Here the polyol volume flow is measured as the total polyol amount. This concept primarily serves as a safety function. Measurement of individual flows is offered as an option. Isocyanate is pumped under high-pressure as usual and metered into the mixing chamber using two combi-injectors.
The visualization and control software FOAMWARE is also new and has been deployed for the first time in the SMARTFLEX system. As a platform for the future, Hennecke is using the Visual Studio development environment for the new software and the high-quality Siemens industrial PC technology for the hardware. Further features of the new control system: integration of the complete functionality in a new development system, standardization of the basic functionalities, modular operating concept, extensive retrofit options, newly developed functions, maximum degree of freedom for the future through customized modules and visualization on mobile devices. The intuitive software will be successively rolled out in all Hennecke slabstock systems. Presentation of the plant at the K show is also forward-looking. Using augmented reality, visitors will be able to submerge themselves in the world of the SMARTFLEX and take a good virtual look at the dry part.
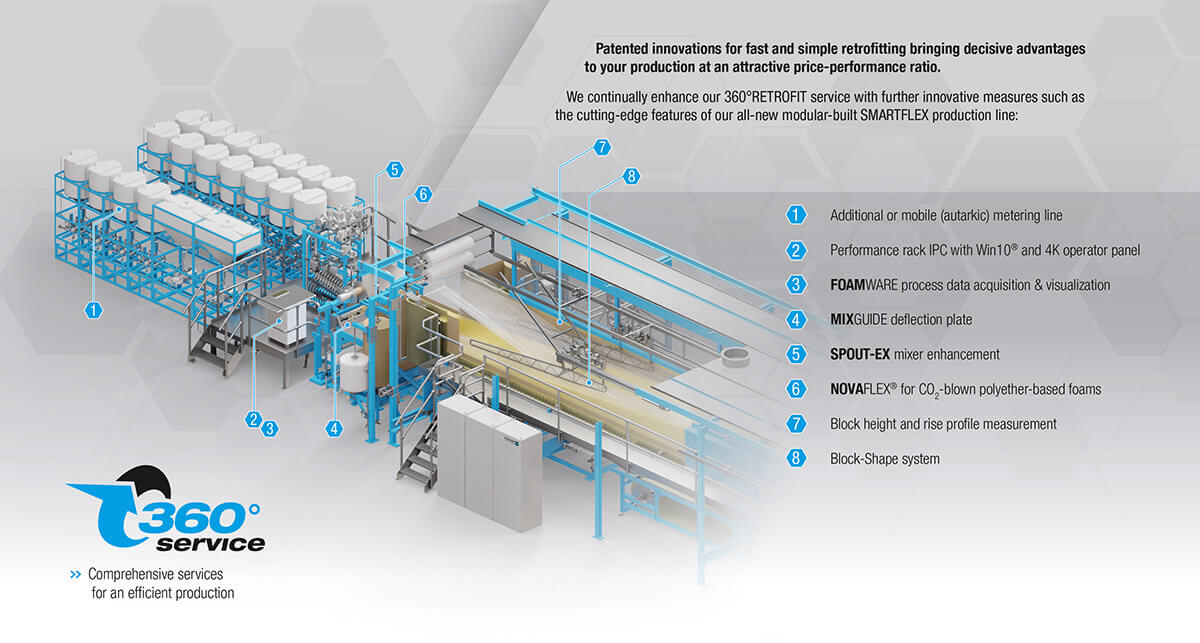