New standards for an extremely broad range of applications
A double premiere for the MT-A mixhead series and the new generation of FLEXJET constant pressure injectors
Mixheads make a significant contribution towards quality and efficiency in the production of polyurethane products. The development and manufacture of these mixheads requires a high level of expertise and many years of experience. Over the years Hennecke has successfully become the world leader in this area. Every mixhead bearing the name Hennecke Polyurethane Technology is a 100% in-house product which earns the label Made in Germany. Now, after around ten years, Hennecke has considerably enhanced the well-known MT mixhead series whilst maintaining its proven construction features. The new MT-A mixheads have an impressive functional design and offer a wide range of applications in process technology. Equipped with a smart sensor module, the MT-A series is also well-prepared for the spectrum of tasks linked to Industry 4.0.
Due to their high precision and durability, the high-pressure MT mixheads have been proven in all applications for ten years and are therefore very well-established in the sector. Operators even use Hennecke MT mixheads in other manufacturers' metering machines. One of the main reasons for the development of the MT series was the change in the raw materials processed by the MT mixheads. Today, many processors use aggressive raw material systems with significantly higher viscosities and greater chemical reactivity. For the new parts of the MT-A mixheads for two and multi-components, Hennecke now uses further optimized materials and high-quality coating processes which have been extensively tested by the company under many different production conditions.
The high-quality materials and surface treatments provide for high durability, even under difficult production conditions. Another new feature of the mixhead is an innovative cleaning and lubrication concept. An enlarged opening to the spacer tube affords generous access without dead space and facilitates manual cleaning. Even surfaces also make this working step much easier. Besides manual cleaning, the customer can choose between two options: integrated minimal lubrication inside the spacer tube or circulation lubrication of the entire spacer tube area.
The real eye-catching features of the two-component MT-A mixheads are the integrated sensor technology for process monitoring and the improved hose line management through standard integrated bulkhead plates. If required, the mixhead system can be quickly and easily separated from the machine. Operation of the two-component mixhead has been considerably improved thanks to a new ergonomic operator panel with optimal fully graphic display. The operator can retrieve further information about the process parameters and the temporal operating sequences of the metering process. The operator panel is integrated directly into the handle. However, Hennecke has done even more for the ergonomics of hand-held applications: due to optimal weigh equilibrium, the mixhead suspension is balanced in the center of gravity, for both vertical and horizontal attachment. The two-component mixheads of the previous series can be directly replaced by the new MT-A mixheads. No modification work is required.
The multi-component mixheads, for example the four and sixcomponent models for moulded foam applications, have been optimized for highly automated, large-scale production and can be used for an extremely wide range of applications, as well as for the straightforward processing of diverse raw material viscosities. For highly viscous polyols in particular, due to the reduction of pressure losses when feeding the material, there is more pressure energy available to the injectors for mixing. In addition to the mixing chamber, the mixing injectors also play a significant role in the effective mixing of polyurethane systems with high-pressure impingement mixing technology at the highest possible rate of efficiency.
The new FLEXJET constant pressure injector generation represents a Hennecke development that fulfills better than ever all the requirements of modern polyurethane systems in terms of metering accuracy, mixing quality and service life of the components. Its user and repair-friendly design also facilitates maintenance and servicing. This results in reduced operating and maintenance costs. There is nothing standing in the way of a simple replacement: like the two-component mixheads, the FLEXJET injectors are 100% compatible with the respective predecessor MT mixhead models.
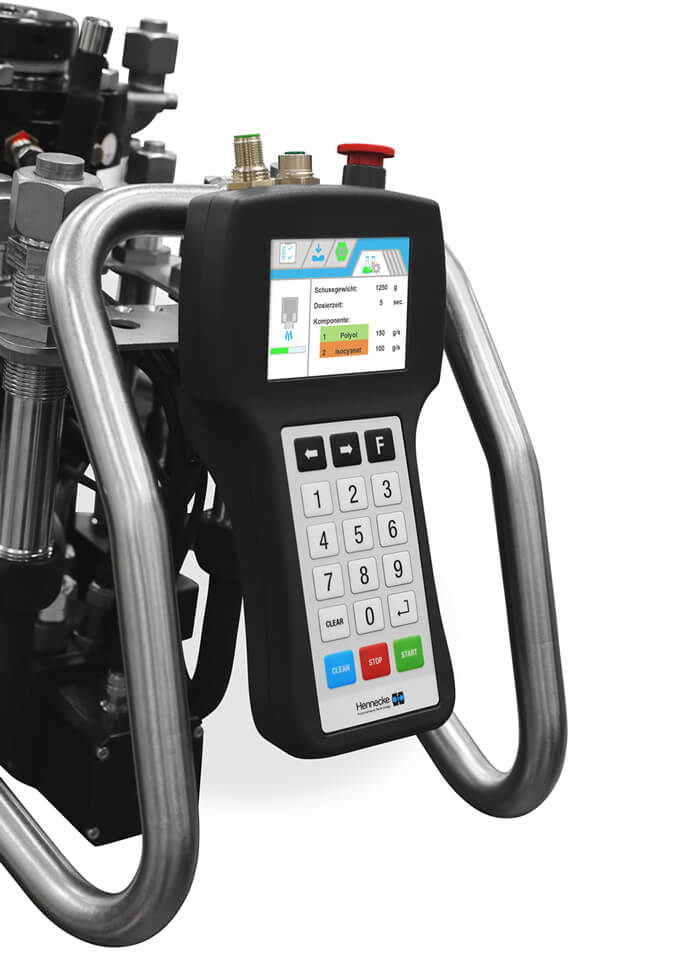
Besides reworking the established spring-loaded injectors (FLEXJET SL), there is a new version which is specially tailored to meet the requirements of the technically challenging multi-component mixing technology: the FLEXJET GL injectors. The hermetic sealing of the media-carrying piping system is a special feature of this injector series.
Hennecke is planning an individual retrofit concept for the introduction of the new mixhead and injector generation which will be tailored to meet customer requirements with the customer service department. The first models in the MT-A series – the MT-A 18-2 and the MT-A 22-6 MF – and the new FLEXJET constant pressure injectors will be available from Q1 2020.
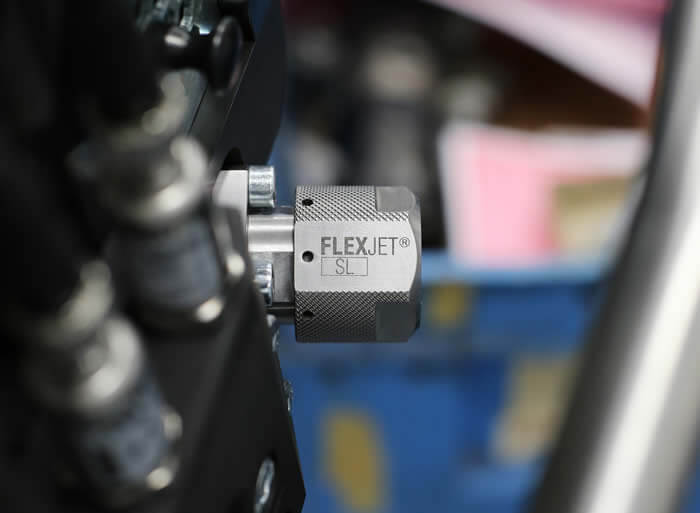
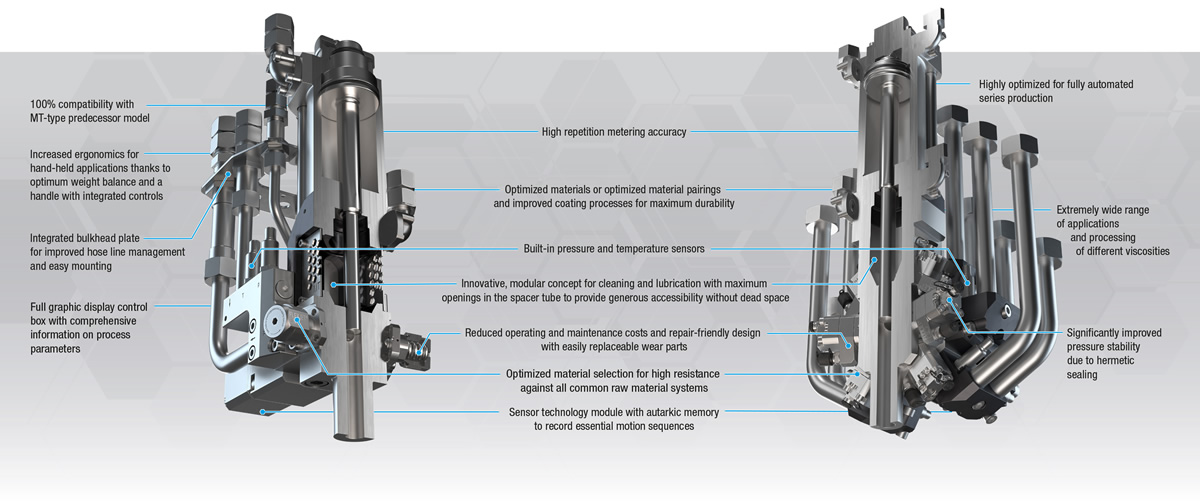