New piston metering devices HT500evo and HT30evo
Processing abrasive fillers in polyurethane systems
The material polyurethane has a very broad, customisable profile of characteristics. Additives such as powder or fibrous fillers can extend this again. Fillers are thus used for reinforcement, noise absorption or as a flame retardant. In general, solid fillers have an abrasive effect in the processing machine. Common metering units for liquid components which are equipped with high-speed piston pumps cannot withstand the high abrasiveness of solid fillers long-term. Hennecke has developed the new metering device HT500evo with a low-wear plunger pump especially for processing main components containing fillers. But Hennecke also has a suitable solution prepared for processors who need to meter small quantities of fillers as auxiliary components into multi-component high-pressure mixheads. The PUR specialists show how users can utilise the HT30evo, for example, to efficiently process abrasive colour pigments as additional components or as main components for low output rates. Both devices are constructed in such a way that they can produce for a long time under these highly abrasive conditions with high precision and repeat accuracy.
Particularly due to the increased demands of fire protection, many polyurethane processors are being faced with the challenge of switching from liquid to solid and therefore abrasive flame retardants. Without the use of solid flame retardants, fulfilling current fire protection regulations would not be possible when manufacturing polyurethane products. In many sectors, such as the construction sector, for rail vehicles or aviation, the other common liquid, halogenated flame retardants no longer suffice and must be supplemented by non-halogenated flame retardants. Such flame retardants are mostly inorganic and are therefore found in solid form.
With the high-pressure piston metering machine TOPLINE HT for filled PUR systems, Hennecke's portfolio has already included a successful wear-resistant and reactionless continuous metering system with a tandem plunger-piston pump for extreme requirements for many years. For polyurethane processors who have always produced exclusively with liquid flame retardants and must now switch to solid additives – but for whom investing in a TOPLINE HT is not practical – Hennecke has added an efficient metering unit with a very attractive price-performance ratio to its product programme with the low-wear HT500evo. As opposed to conventional devices with high-speed piston pumps, the HT series is equipped with slow-running plunger-piston pumps.
The HT500evo is suitable for processing main components containing fillers for parts weighing up to three kilos. One of the main applications of this device is the production of comfort flexible foam, which is, for example, used for seats and cushions in vehicles, especially in public transportation.
Fire protection regulations have recently intensified especially in the rail transportation sector, so producers have to switch to solid additives. Another area of application of the HT500evo is rigid foam applications, as for insulation in the construction industry. The fire protection class required here, B2, can also only be achieved with solid flame retardants.
Hennecke offers the HT500evo as an independent 2-component metering machine or as a module device for retrofitting an existing TOPLINE metering machine. In addition to processing polyols with solid flame retardants – for example, ammonium polyphosphate, melamine resin and expanded graphite – the HT machine is also particularly suitable for processing polyols made of renewable raw materials, recycled polyols, polyols with fillers such as PUR regrind or abrasive fillers such as glass fibres, calcium carbonate, barite, abrasive colour pigments and highly viscous raw material systems.
Hennecke also has decades of experience in the processing of additives which are processed as additional components via a high-pressure multi-component mixhead. The new HT30evo is used, for example, to meter abrasive pigment colours or chemically aggressive or filler-containing additives to the reactive main components in a high-pressure mixhead. Like with its "big brother", the HT500evo, Hennecke offers the extremely compact unit in two different versions: as an add-on with the appropriate pump table (with and without control) or partially integrated into a heating cabin for processing high-temperature components.
All variants of the HT30evo are fitted with a PLC interface for integration into the metering machine and have important equipment features even in the standard scope of delivery. The device is equally suitable for components of high and low viscosity. Even particularly low output rates are no problem for the HT30evo. Despite differing ranges of application, the two new piston metering devices have one thing in common: high quality components and first-class processing ensure long product life even in harsh production conditions. For all metering machines, Hennecke offers an extensive mixhead portfolio particular to each respective application.
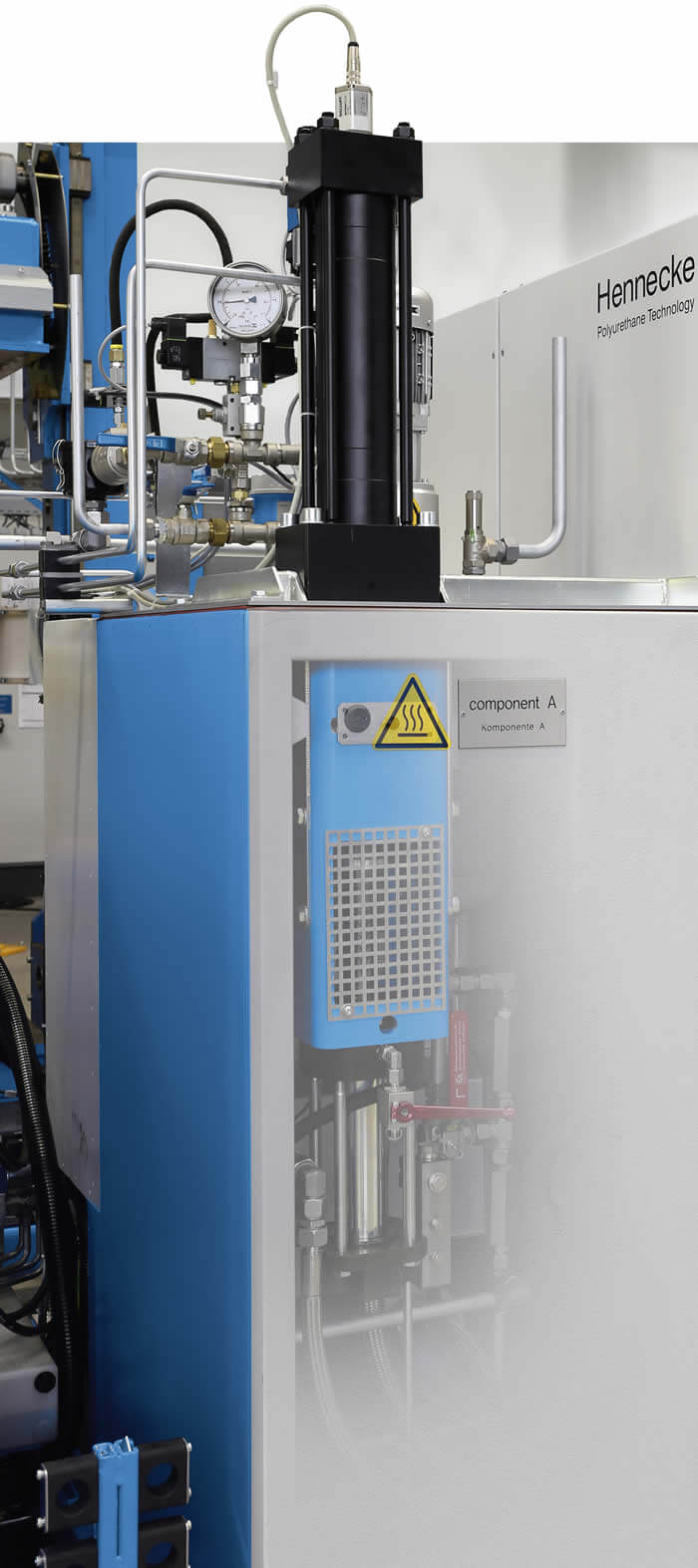
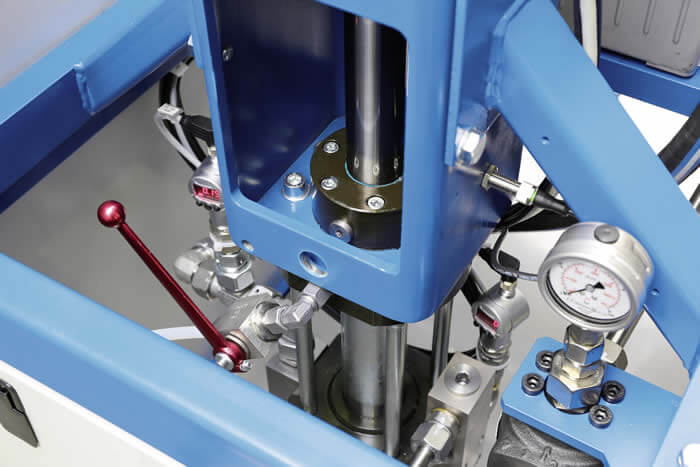
The new piston metering devices impress with high-quality parts and first-class workmanship
Technical data: | HT30evo | HT500evo |
Output | 5 - 30 cm³/s | 100 - 500 cm³/s |
Stroke volume | 450 cm³ | 3300 cm³ |
Working pressure | 200 bar | 200 bar |
Filler particle size | up to 200 μm | up to 350 μm |
Component temperature | up to 80°C (120°C)* | up to 60°C |
*integrated in heating cabin |
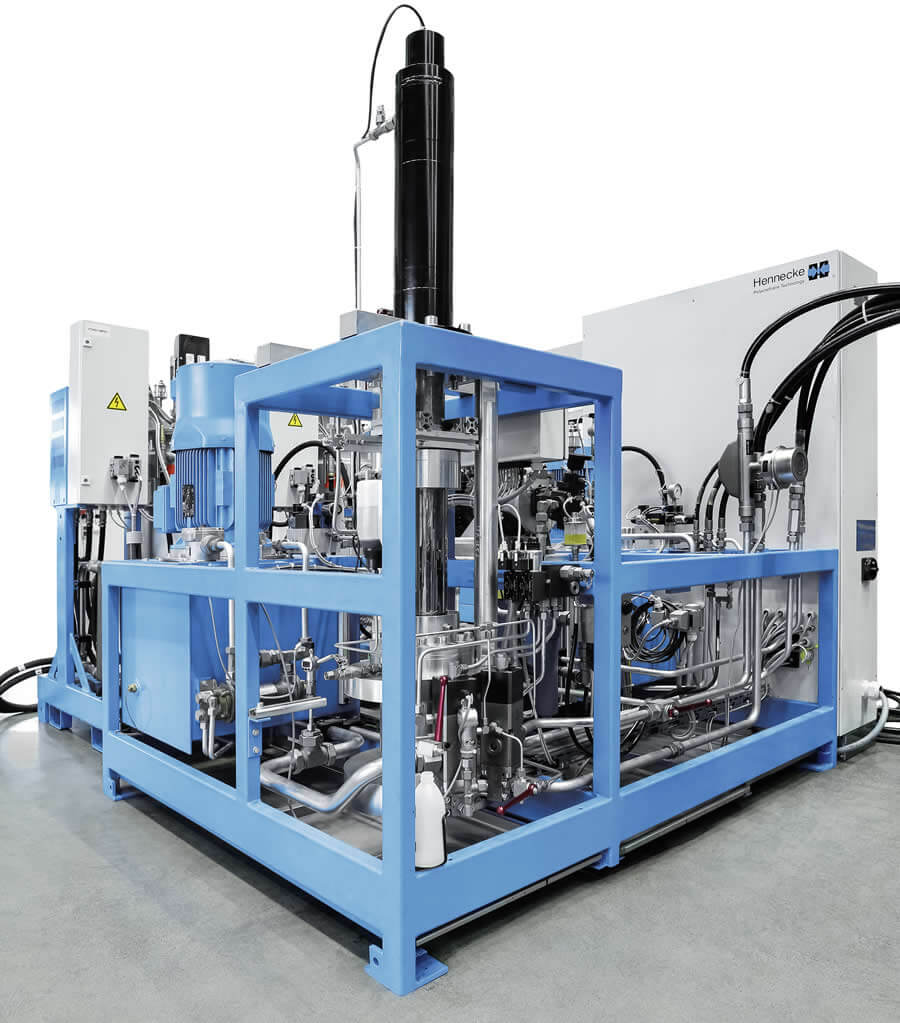