Project R.A.C.E.
Serial production of complex, structural hollow parts
The KTM 1290 Super Duke R impresses with its powerful 1300cc, 170 HP V-engine and its unbelievable acceleration. This motorcycle is a high-performance machine and therefore the ideal application for ultra-lightweight high-performance components. In cooperation with top industry partners, Hennecke will for the first time present a high-pressure RTM lightweight construction process live at the K show. In the future, this will bring fiber composite parts to efficient series applications where high performance is required.
Carbon components are already widely used in motorsport. In the R.A.C.E. project (Reaction Application for Composite Evolution), Hennecke and its partners have now made an important development step in the industrialization of the new CAVUS technology from KTM Technologies, which will allow even complex fiber composite hollow parts to be produced with the automated high-pressure RTM process. They can be implemented in many further integrally manufactured fiber composite hollow parts as, for example, in roof constructions, structural components, or even monocoque geometries. Now, a structural component for the Super Duke R is to be produced using the CAVUS technology. The motorcycle license plate holder to be substituted consists of a hollow and clad steel structure to save weight on the one hand and to accommodate for wiring for turn signals and the license plate light on the other hand. At the same time, the part has to be very stiff, because enormous stresses occur during operation. The traditional license plate holder weighs more than 765 grams, however with the project R.A.C.E., Hennecke and its partners produce the part with increased performance and a total weight of only 265 grams. This alone is a weight saving of over 60 per cent! Stefan von Czarnecki, Director of Sales and Business Development of KTM Technologies, explains the company's claim in the field of lightweight construction: "For us, competitive lightweight construction is a central focus in the development of high-performance products.
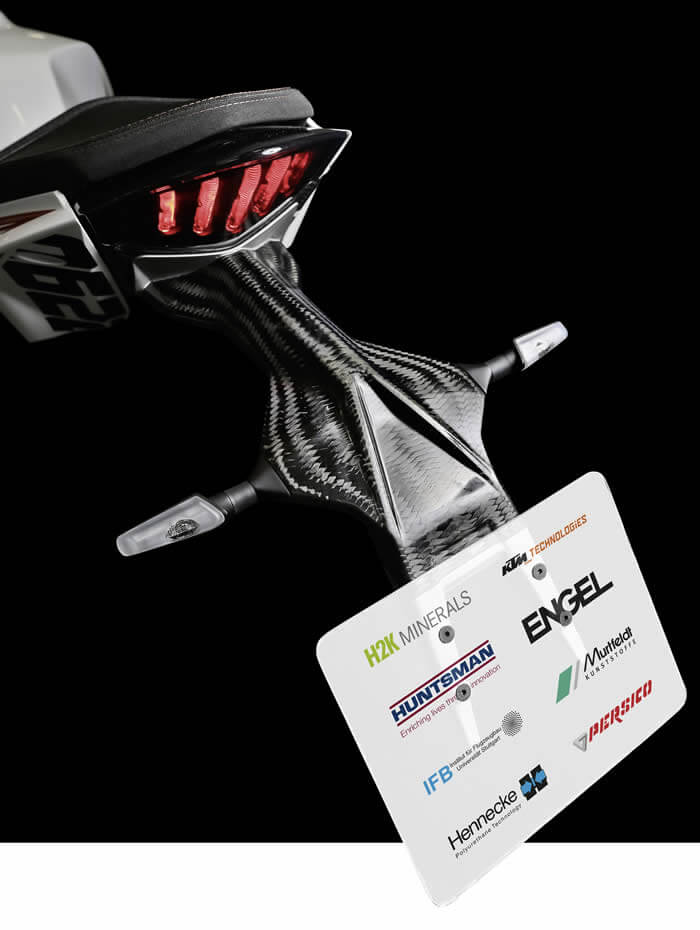
With an innovative team, we realize parts in new technologies where we are constantly pushing the limits of what is possible for our customers. We at KTM technologies also rely on powerful partners for our development projects in order to retain our leading position in lightweight construction in the future. "The challenge for the new license plate holder lies in the interaction between the right layout coupled with a production-ready design of the component and the combination of efficient processes based on the innovative CAVUS technology from KTM Technologies. CAVUS denotes the automated process chain for the production of complex structural hollow parts: from the core production and the manufacture of the preforms with carbon fibers e.g. in braiding technology through the HP-RTM process to the release of the core material. This opens up completely new creative possibilities for design and function. The process starts with the sand core. Just like in the construction of a sandcastle, one needs a binder to give the sand a solid form. Ivo Herzog, Managing Director from H2K Minerals, explains how stable such a core structure is under pressure: "H2K Minerals is able to produce pressure-resistant complex geometries using sand.
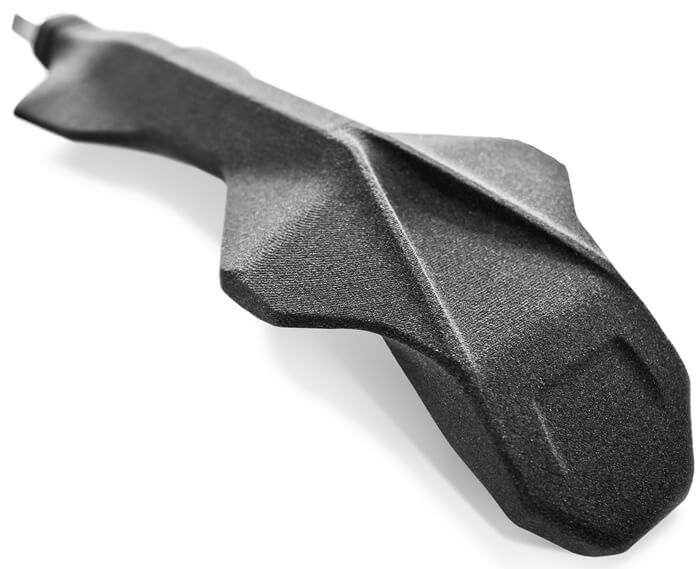
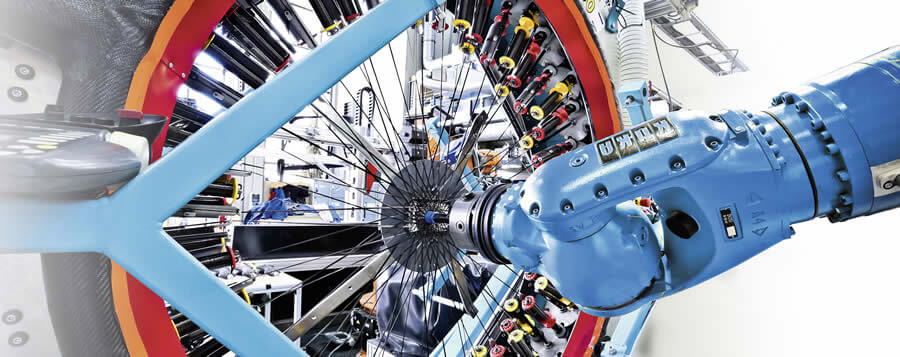
The sand cores will withstand an enormous injection pressure up to 500 bar. The binder used is water-soluble. At the end of the process, it can be flushed out easily in an eco-friendly manner with regular water and without any use of solvents."
The second part in the process is the tailor-made carbon preform. Dr. Stefan Carosella, Head of Composite Material from the Institute of Aircraft Design Stuttgart, explains the production: "It is a braiding process, in which the carbon fibers are woven around the sand core. In the process, the position, angle, and orientation of each individual fiber is extremely important in order to properly absorb forces that are acting on the part."
Up to now, the resin injection process Resin Transfer Molding (RTM) has been used to produce long and endless fiber-reinforced flat components. Here, non-impregnated reinforcement fibers in the shape of a prefabricated and contour-aligned preform are placed in a mould. The fibers can be interwoven or directional. After closing the mold, it is flooded with a reactive resin system. After the component has cured, it can be removed from the mold. Hennecke was able to significantly optimize this process in terms of cycle time by developing the HP-RTM technology.
In the R.A.C.E. project, the matrix material Vitrox® from the company Huntsman is used. This is an RTM polyurethane material with the so-called Snapcure effect. Snapcure enables quick and sudden hardening of Vitrox®. "The R.A.C.E. project is an excellent platform where high-speed PU-matrix materials such as Vitrox® can demonstrate their full performance," says Hubert Reitberger, Product Manager Advanced Composite Resins from Huntsman Polyurethanes. "Self-releasing systems with outstanding mechanical properties combined with optimized curing times are the key to mass production with a short cycle time."
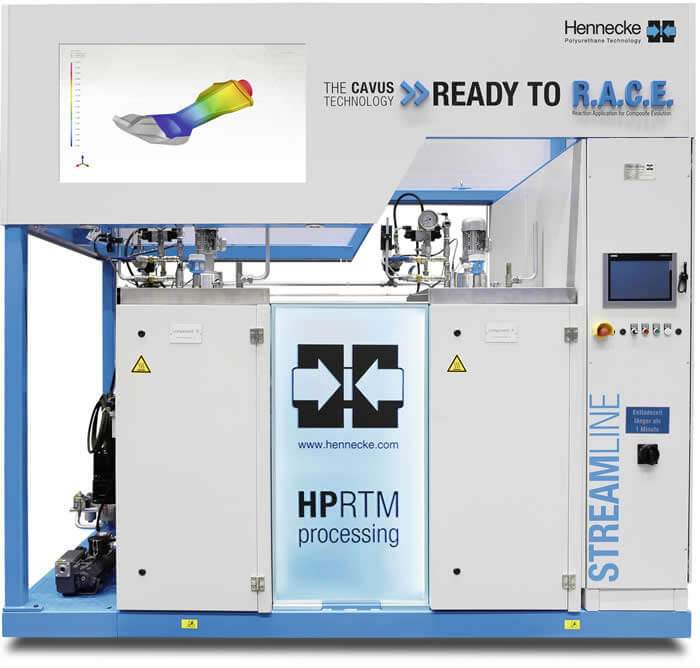
The HP-RTM process starts with the automated insertion of the prefabricated preform by a robot. The press then closes the mold and the injection process starts. The entire curing process takes just 125 seconds. With the elast 400 from the company ENGEL, the process is performed with an extremely compact press. "ENGEL machines are characterized by highest precision, energy efficiency and reliability," says Matthias Mayr, Head of Application Engineering & Project Management at the Center for Lightweight Composite Technologies from ENGEL. "Combined with our automation capabilities, they are the ideal basis for an effective mass production in the area of HP-RTM processing. We have integrated an elast 400 into the production cell which is best suited for both automated and laboratory operation."
High demands are also made on the mold, Gaetano Donizetti, Sales Manager at the company PERSICO, reports: "To withstand the carbon fibers, the aim is to realize a robust, and highly polished surface. This enables the production of high-quality components and surfaces. For this, the ability to demold and the injection points have to be chosen correctly."
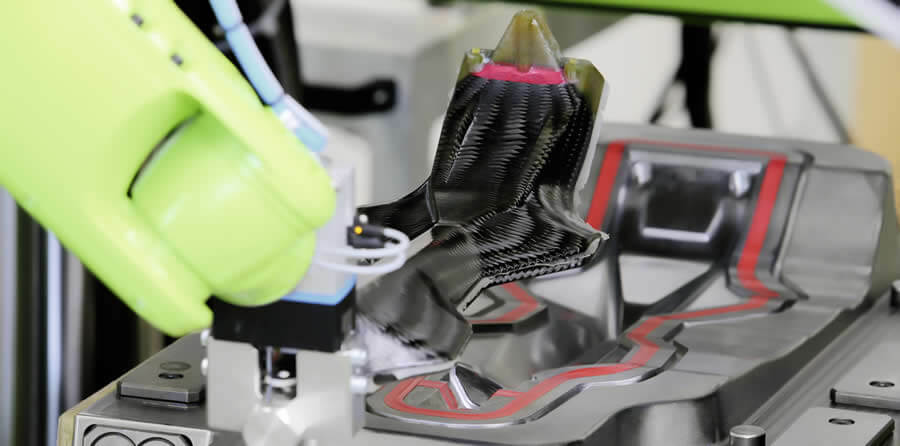
The innovative sealing in this mold is new to the world. It has to resist an internal mold pressure of about 100 bar for long periods of time. Here, a new sealing material from Murtfeld is used. "For the first time in the R.A.C.E. project, Murtfeldt Plastics is proud to present a sealing material that can withstand internal mold pressures of more than 100 bar for long periods and is still resistant to damage from residue materials or even carbon fiber," says Ralf Burghoff, Technical Assistant to the Management from Murtfeldt. "Murlock® is another key to high-volume rates of high-pressure RTM processes."
Finally, the metering machine plays an important role. The Hennecke STREAMLINE realizes precise injection of the raw material system in seconds. Karolin Jacobs, Mechanical Design Metering Machines from Hennecke: "The STREAMLINE machine offers a wide range of special features which significantly influence the HP-RTM process. Pressure control, sensors in the mixhead outlet, hydraulically controlled back-pressure function and mold filling monitoring - to compensate for weight fluctuations in the preform - are essential to the perfect component."
The project R.A.C.E. is an impressive demonstration of how a decisive development step in the series production of fiber composite hollow parts on the basis of CAVUS technology can be performed through joint efforts of highly specialized project partners. For Rolf Trippler, Managing Director Sales at Hennecke GmbH, project work is therefore an important part of the self-image of the polyurethane specialist: "Hennecke has consistently extended its technology leadership in many applications also through close cooperation with various industry leaders. The R.A.C.E. project represents this in an impressive way. Hereby I would once again like to thank all parties involved for the successful implementation of the project."