HP-RTM technology in Hennecke style:
Shorter curing times in the production of extremely light high-performance components
The demand for High Pressure RTM (HP-RTM) in the field of lightweight automotive construction has been increasingly growing. Hennecke GmbH & Co. KG is already in an excellent technological position with the STREAMLINE high-pressure metering system for HP-RTM applications as is proven by its impressive automotive serial applications. Nevertheless, the Hennecke process experts are pushing the envelope of what is feasible step by step. The reduction of the specific cycle time plays a decisive role in this as it already did in the course of the processrelated combination of highpressure technology and the traditional RTM process. With the VARIOCAST technology the lightweight construction specialists of Hennecke GmbH & Co. KG are now able to further reduce the demould times for HP-RTM components. This especially meets the demands of users within the field of series production.
Due to increasing requirements for efficiency and ecology interest in lightweight solutions, especially for the automotive industry, has been growing in recent years. The main focus is on components that until now have been realized using the resin injection process in closed moulds. Today, a combination of high-pressure technology and the conventional RTM process is increasingly being used in the production of such high-tech components. With the High-Pressure-RTM process (HP-RTM), Hennecke has broken new ground in polyurethane processing technology. In addition to various already existing carbon structural components for car body applications, developers are increasingly focused on automotive accessories. The best example of this is a high-performance rim manufactured as a carbon-aluminium hybrid design or a pure carbon product. Apart from a high-end surface structure, such rims offer an enormous weight reduction of between 25 and 30 percent over conventional rims made of forged aluminium. The result is not only lower consumption, but also noticeably improved driving dynamics. Besides, developers do not need to worry about the stability of these safety-relevant components because damages do not affect the structure and the rims can easily be repaired by using special resins.
Because of the great amount of manual work and the comparatively long process times involved, it is hardly conceivable that such high-performance parts could be mass-produced by the traditional RTM method. With the HP-RTM process, its degree of automation and the specific cycle time, the Hennecke specialists have created a tool that offers considerable advantages in terms of efficiency and product quality, especially when it comes to producing large volumes economically. In the process, Hennecke can draw on decades of experience in high pressure metering and mass production applications. The result is increased performance – not only in the end product:
- High-pressure injection of the reactive mixture into the mould within a few seconds
- Accelerated reaction and extremely short curing times thanks to high-pressure mixing and highly reactive resin systems
- Specially adapted systems with a variable range of properties due to close cooperation with raw material suppliers
Suitable machine systems of the STREAMLINE series have long been permanent fixtures on the market for lightweight applications based on fibre-reinforced structural components. A reason for this are the high-quality components and equipment features that are even part of the basic configuration of the state-of-the-art processing systems.
The flow metering system, for instance, is density-independent and thus allows for an exact metering process. This is complemented by a highly efficient heating concept with a component temperature control of up to 130 °C and the effective evacuation of the raw materials in the day tanks.
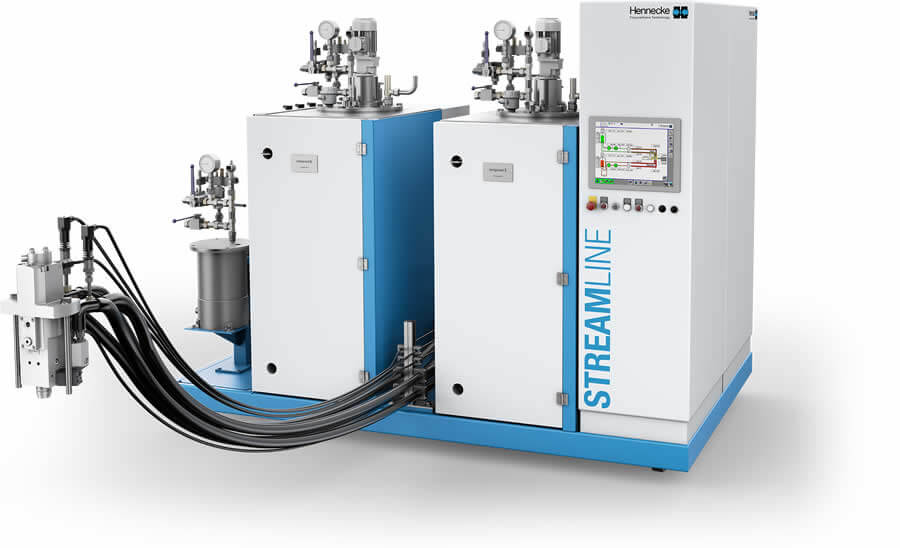
Not by chance Hennecke distinguishes itself as an experienced partner in the field of raw material processing. While "traditional" polyurethane metering machines only process a few pre-formulated components, particularly large-scale Hennecke plants often meter more than 50 individual components with extreme mixing ratios and integral formulations, e.g. during the production of foam products or sandwich panels. Exactly this expertise now forms the basis for adding a useful additional function to the metering machines of the STREAMLINE series: the separation of the activator components by means of an individual additive line (VARIOCAST technology).
Here, the STREAMLINE does not perform the metering according to a defined output but in accordance with a time-dependent function. But why is this function particularly interesting for HP-RTM applications? In order to further reduce the curing time and thus the associated demould time, the injected mix can be time-dependently controlled. The advantage is that, depending on the level of the additional activation, the basic raw material has a specific start time and an individual curing time related hereto, which is significantly shorter compared to a fixed activation. Thanks to VARIOCAST, demould times can be reduced for long shot sequences. This is an indispensable advantage particularly in the framework of large-scale production of lightweight components, for instance, in the automotive industry. As of now, Hennecke customers can include the equipment feature VARIOCAST as an option during the purchase of a STREAMLINE metering machine or they can retrofit their STREAMLINE machines with this feature.
In addition, Hennecke offers extensive support for newcomers to this technology, also addressing fundamental questions such as: How do you build a mould? Where do you position the mixhead? And where do you properly vent using the specifically developed evacuation module? A team of experts will be by your side to get the process started as easy as possible. Even after the start of production, Hennecke STREAMLINE customers will continue to benefit from an extremely extensive support. The online upgrade, for example, allows future control developments to be integrated on demand into the control system. For this purpose the full control of all functions – up to online operating support via menu-guided process input - is available.
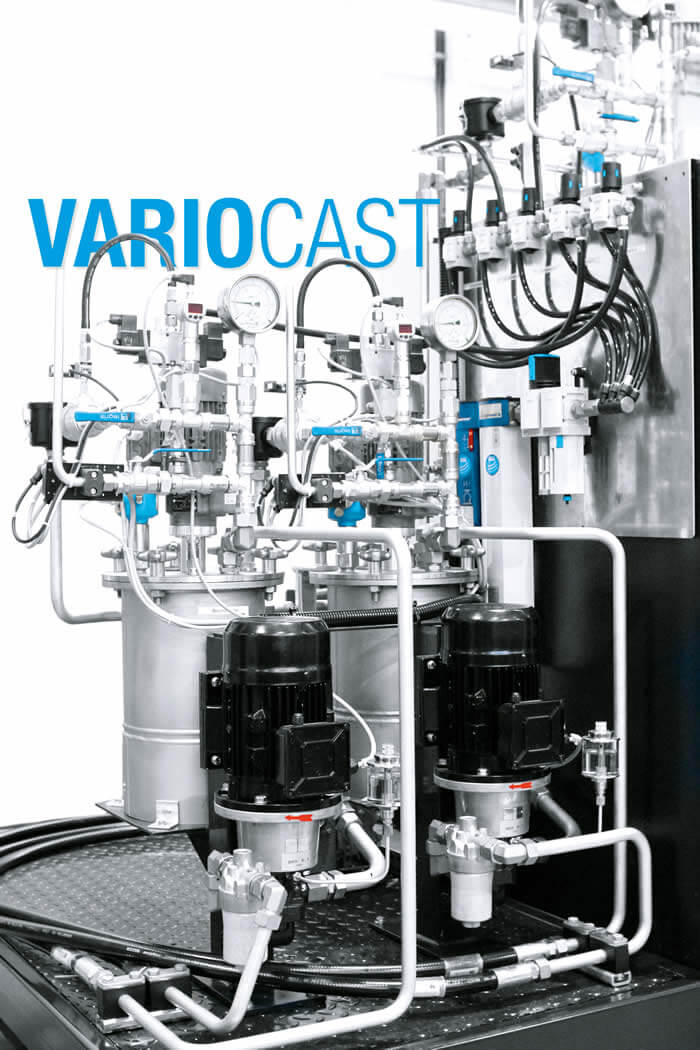