Well insulated:
polyurethane-insulated pipes with wide application range
Hennecke has been a renowned supplier of systems and process technology for the manufacturing of polyurethaneinsulated pipes for more than two decades. A long-term customer of Hennecke is the world leader in the production of pre-insulated pipes LOGSTOR A/S. Together with LOGSTOR A/S Hennecke has repeatedly developed new innovative systems for pipe insulation over the years. As part of the latest pipeline project of the Danish district heating and pipeline specialist, hot bitumen sand is to be transported in Canada.
Manufactures pre-insulated pipe systems in ten factories across six countries. Apart from being used in district heating technology, they are also deployed in on and offshore applications for transporting oil and gas products, in the process industry as well as in shipbuilding. Many of the pipes are manufactured continuously rather than individually by means of Hennecke's continuous process. As a first step in this process, the inner pipes are fixed continuously. At the same time, a vapordeposited PE foil is pre-formed into a U-shape. In the next step a mixhead pours the polyurethane foam onto the foil, which is subsequently closed so that it envelopes the inner pipe. Afterwards, the pipe, foil and rising foam pass through a calibrating unit for curing. The foam-insulated pipe is then run through an extruder in which the polyethylene outer pipe jacket is applied. The pipe is drawn uniformly during the entire manufacturing process. The polyurethane foam only has to rise, as opposed to the traditional process, which requires a flow path over the length of the pipe. As a result, an even density distribution and insulation is achieved. After the cooling and curing process is completed, the continuous pipe can be cut to the desired lengths.
The insulated pipes from LOGSTOR are not only used for transporting gas and oil, but also for bitumen sand. Rising oil prices and technological progress are making the extraction of crude oil from bitumen sand increasingly viable. The energy company was contracted by TransCanada Pipelines for the Northern Courier Pipeline Project in Canada. The 24 inch pipeline for the project is 90 kilometers long and its purpose is the transport of bitumen sand between the Fort Hills Mine and the East Tank Farm, located north of Fort McMurray, Alberta. In order to make the bitumen sand ready for transport, it must be heated. This makes an insulation of the pipeline mandatory in order to prevent the mixture from cooling down too much.

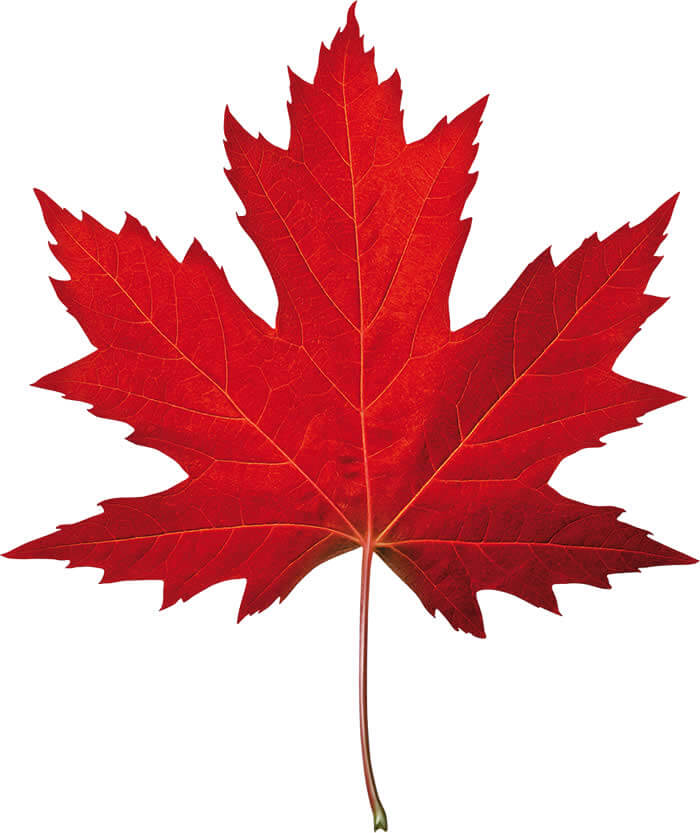
Contrary to the standardized pipes for district heating applications, individual specifications must be met for each order in the case of oil pipelines. In order to be able to compete for the contract in Canada multiple specification pipes were required. As Hennecke's own technical center can only produce pipes at a length of six meters, LOGSTOR manufactured various specification pipes at a length of 21 meters each using existing Hennecke system technology, which were checked and approved by TransCanada Pipelines.
Hennecke now supplies LOGSTOR with two continuous systems specifically designed for the pipeline specification, which make it possible to continuously apply an up to 120 millimeters thick insulation layer onto a rotating pipe. The maximum length of the manufactured pipes is up to 24 meters and the diameter is up to 610 millimeters.
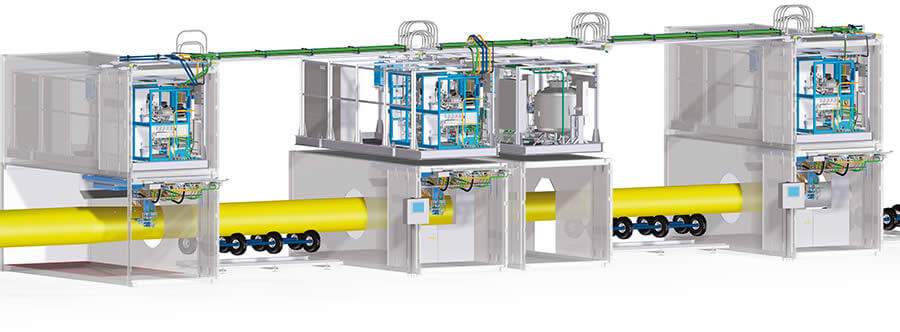
Thus, about 450 kilograms of insulating foam is applied to each pipe. In order to adapt the raw material ideally to the ambient conditions, pentane and the activator have to be metered online to the polyol in very small quantities. The focus here is on a homogeneous foam quality over the entire pipe length.
LOGSTOR also uses the Hennecke technology for manufacturing district heating pipes. The energy company's pre-insulated pipe systems with their particularly effective insulation are specifically designed to limit energy loss in district heating and cooling systems to the absolute minimum.
District heating and cooling – especially when based on cogeneration – can contribute to a significant reduction of the CO2 emission. The expansion of the district heating network in Europe offers a particularly great potential. For example, only about 13 percent of the German population are connected to a district heating network. The technology for economically insulating the pipes for the network is definitely available at Hennecke.
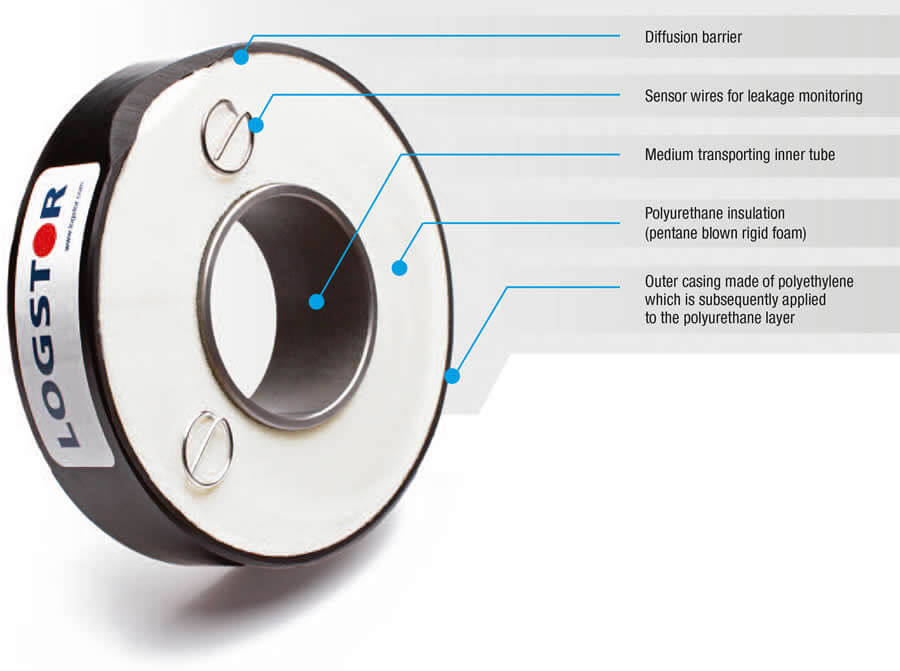