Keeping the production in sight:
PURTRONIC ensures intuitive control during the manufacturing of moulded foam products
Hennecke's WKH oval conveyor systems offer the ideal solutions for the requirements of an economical production of polyurethane foam parts for vehicle seats and backrests. High flexibility, mould change without downtime and an outstanding and constant product quality characterize this plant. Hennecke does not make any compromises with the interface between human and machine so that the user can fully exploit the potential of the WKH plant technology: The plant visualization PURTRONIC allows intuitive and efficient operation and offers users ideal support in the daily production process.
Apart from the production of polyurethane moulded foam parts for vehicle seats and backrests, smaller dimensioned parts such as armrests and headrests are also manufactured with the flexible WKH plant technology.
Because the users are often confronted with the requirement to realize products for different manufacturers and vehicle types with various formulations and because the total amount of seat types is increasingly rising, it is often necessary to carry out a mould change.
For this application, Hennecke offers its oval conveyor plant concepts with an automatic in- and outfeed station QCD (Quick-Connect- Disconnect), which allow the exchange of mould carriers during running production and at a conveyor speed of up to 15 m/min. This makes it possible to retrofit, prepare and maintain the mould carriers A offline without having to interrupt production. In order to make this flexible and complex type of production possible, Hennecke uses top-quality control components, which are perfectly designed for the series production of moulded foam products.
The automatic monitoring, controlling and logging as well as secured reproducibility of all relevant process parameters provide the polyurethane processors with an outstanding and constant product quality at all times – even at high production rates. The plant operators are optimally supported by the intuitive visualization PURTRONIC, which is based on industrial computer components and relies on Windows®-OS software. Production is profoundly supported and accelerated by the complex, software-technical data acquisition and processing.
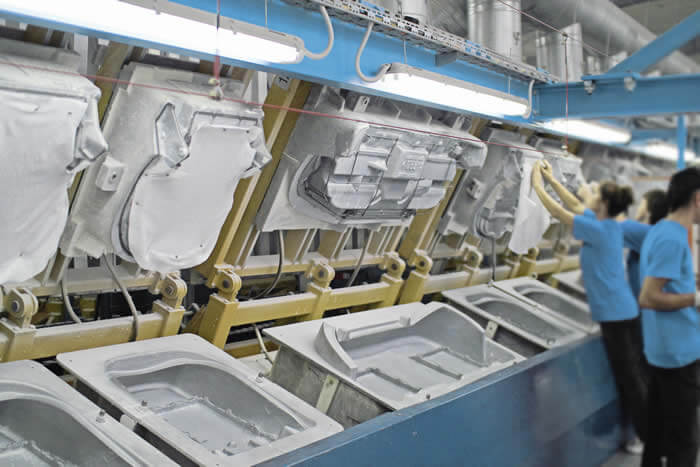
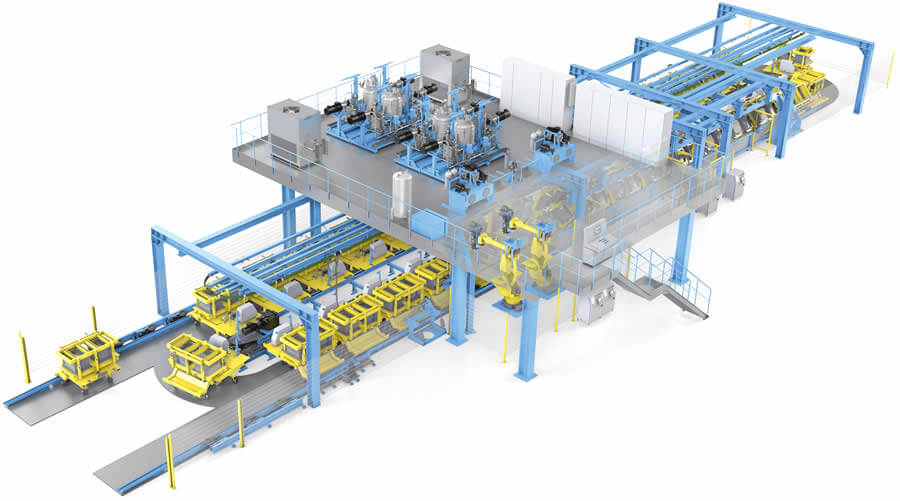
The process control center (PCC), which is visible on every PURTRONIC screen display, provides the operator with a simple and clear system and user data management. This makes working with the plant more intuitive and efficient. From here the operator can control all relevant plant components including the process parameters, which can be visualized for all components in clearly structured diagrams. The PCC also provides access to the process monitoring and documentation systems through pre-configured tables and graphical displays, which are specifically adapted to the respective application. For example, the overview of the entire running production including all mould carriers can be displayed. A parallel presentation of all wet part data gives the user a clear overview thanks to the holistic display. Despite the extensive and complex process data density, all screen displays remain clear and easy to read for the user. The Easy User Management system ensures safety during production. Every user can be individually allocated an access level for parameter changes. Thanks to the use of RAID and UPS systems, the PURTRONIC also ensures that the hardware is provided with the necessary system safety.
When it comes to manufacturing polyurethane mouldings, it is common that the operator tries to continuously optimize the production and foam parts by fine tuning all parameters. The menu item "Touch & Find" makes it easy for the user to monitor and, if appropriate, adjust the pressures, parameters, values and times of the plant. The overviews were optimized with this in mind and display very detailed facts to the operator. When entering metering packages the user can choose to enter them either in proportions (percent) or individual quantities (gram). The plausibility of all entered values is thereby checked automatically.
The extensive data memory on an SQL server is helpful during the optimization of production. Here, the PUR processor finds relevant information in tables and graphical displays with the option of exporting them into common file formats (such as MS Excel). These prepared production data give the plant operator the best possible foundation to further increase the efficiency of the plant.
The Hennecke software developers considered it particularly important that the operator is provided with a user interface which allows him to adapt the visualization to his own needs. For example, three configurable hot keys of the PCC serve the purpose of selectively loading frequently used submodules and returning to the previous screen. The numerous integrated shortcut tags in the respective visualizations help the user to quickly reach the desired screen. If problems still develop, the operator can directly access the 360°SERVICE portal by Hennecke via the PURTRONIC, in order to find a solution as quickly as possible using the online support, for example.
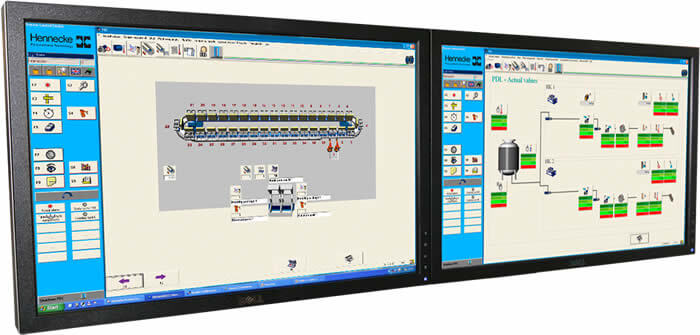
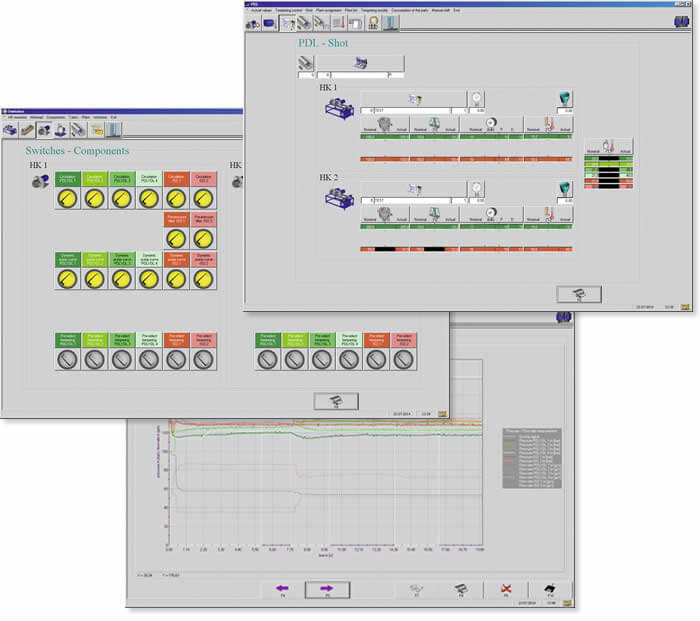