Innovative lightweight solutions
Engel Austria and Hennecke form a development alliance
When analyzing the basic elements and requirements for „forward-looking lightweight construction in the automotive industry“, the following features are indispensable:
- Fibre composites tailored to requirements
- Mass production capability
- Cost optimization
In the present case, these keywords form the basis of a development alliance between the injection moulding expert Engel and the HP-RTM-specialist Hennecke. Fibre composites that are tailored to meet individual requirements are a classic product which is processed by the RTM method. With the development of the HP-RTM process, Hennecke has been able to significantly optimize the cycle time of a common production process by using reactive plastic systems. The HP-RTM method focuses on a task that is well-known and tried and tested in the area of PU processing: the highpressure injection of a reactive mix into a mould within a few seconds. Combined with the suitable raw material system, the HP-RTM process allows an accelerated reaction and extremely short curing times to be achieved. On top of this, Hennecke GmbH's decades of experience in high-pressure metering are apparent. For example, in a processoptimized mixhead series for HP-RTM applications that delivers top-quality and reproducible results at all times. Moreover, the use of Hennecke's patented constant pressure injector ensures a stable homogeneous injection pressure. The extremely innovative filling process in a closed control loop and all other tasks of this new production method are implemented by Hennecke's STREAMLINE machine series.
Now Hennecke addresses the issue of mass-producing fibre composite parts together with Engel. For it is not always necessary to manufacture parts in complete fibre fabric structure. Within a part, the fibre fabric is often only required at places where forces actually have to be absorbed. Afterwards, the final moulding process can take place completely by thermoplastic injection moulding and in high-quality design, also when the parts are demoulded without being processed further.
Recognizing this, both companies have decided to cooperate on developing possible technology combinations and to expand their technical centers for lightweight applications. „In composite products, various types of materials are coupled to bring out the positive properties. For the manufacturing process, this ideally has to start with mechanical engineering“, says Jens Winiarz, Head of Sales of CSM and New Technologies at Hennecke GmbH. Both Engel´s site in Sankt Valentin (Austria) with its Technology Center for lightweight composites and Hennecke's site in Sankt Augustin (Germany) with its well-known PUR-CSM Center are equipped with the relevant injection moulding and HP-RTM technology. Each of the two companies installs state-of-the-art machine technology at the other location to make sure that development work, future customer trials, pre-series sampling and raw material optimization can be carried out there. „The basic condition for successful lightweight solutions is to ensure that material, design and processing interact perfectly. This is why cooperating with partners along the value-added chain is particularly important for this topic of the future. Our long-standing, close partnership with Hennecke allows development processes to be accelerated, especially when it comes to new challenges“, explains Peter Egger, Head of the Technology Center for lightweight composites of Engel Austria.
The two companies are convinced that their alliance will provide great added value to the customer. Especially because the interaction of fibre composites tailored to requirements on the one hand and process optimization on the other hand are the key to largescale production with short cycle times in the trend towards lightweight construction.
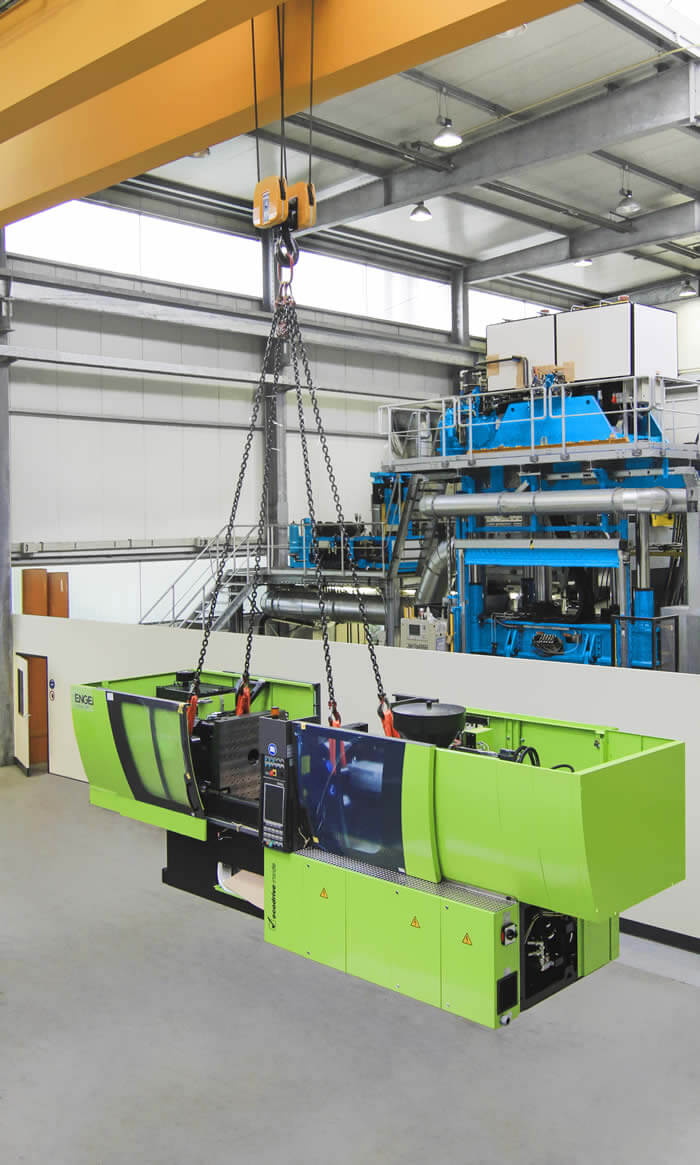