High pressure meets lightweight
Hennecke establishes customer center for high-volume RTM applications
Due to increasing requirements for efficiency and ecology interest in lightweight solutions for the automotive industry has been growing in recent times. The focus is especially on one process: Resin Transfer Moulding (RTM). Thanks to comprehensive investments in a new RTM center, Hennecke GmbH now offers sufficient scope to potential customers as well as raw material partners to manufacture, test and develop high-performance parts until they are suitable for mass production. The Hennecke composite specialists can score with an important further development of the RTM technology that ensures unlimited suitability formass production in terms of automation and cycle time: the High-Pressure RTM process (HP-RTM).
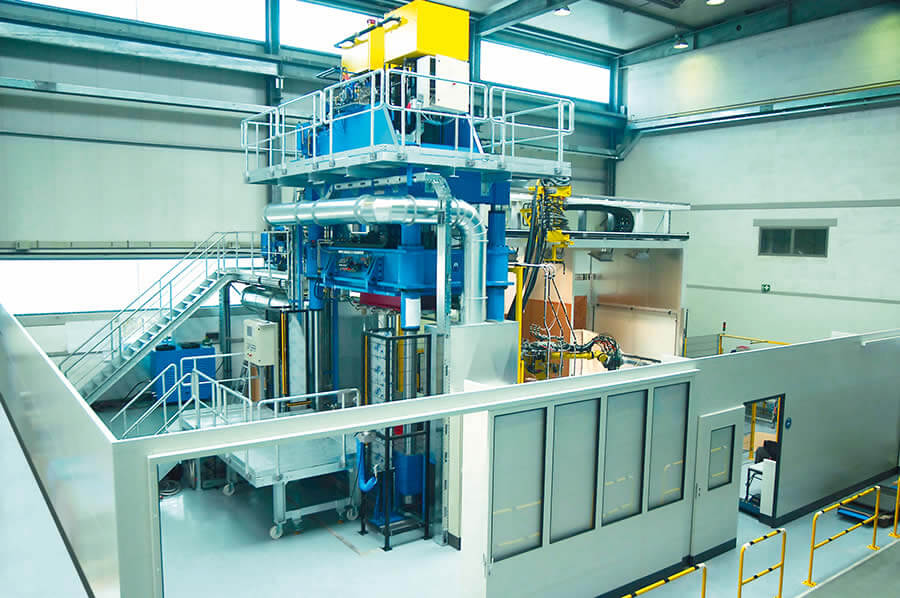
Hennecke GmbH has been documenting the strongly growing demand for composites in general and lightweight solutions in particular with constant research and development and the modular expansion of its product portfolio. Thus the composite specialists regularly succeed in identifying new manufacturing processes and fields of application for producing and using composites. This already applied to PUR-CSM technology, which has become firmly established in the production of lightweight and high loadbearing glass- or natural fibre-reinforced PU products – including sandwich structures.
Apart from new drive concepts, reduced vehicle weight is an indispensable element to ensure more efficiency and a better energy balance in future automobile manufacture. In motor racing, lightweight construction has long provided for improved performance and less consumption so that it has increasingly found its way into automobile mass production. In the car body sector, automotive manufacturers meet these requirements by using fibre-reinforced structural components that are convincing both in terms of low weight and crash behaviour. In most cases, the Resin-Transfer-Moulding (RTM) method is used for this application.
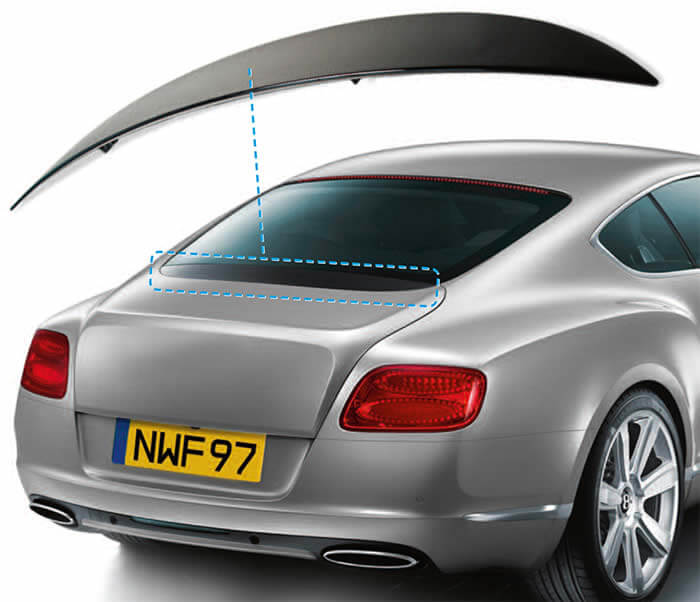
In the process, resin systems are injected into the closed mould at low pressure. Because of the great amount of manual work involved, the manufacture of such high-tech parts in the classical RTM method is partly characterized by extremely long process times. This is why the industry is desparately searching for manufacturing methods that are suitable for mass production and an adequate implementation of high volumes. However, increased automation alone can only optimize cycle time to some degree. The aim is to find a solution which decisively reduces the specific curing times of parts.
By introducing the so-called High-Pressure RTM process (HP-RTM), Hennecke GmbH has tackled this problem and pursued familiar paths in polyurethane processing technology in a new way. The focus of the HP-RTM method is on a task that is well-known and tried and tested in PU processing: the high-pressure injection of reactive mix into a mould within seconds. In combination with the appropriate raw material system, the HP-RTM process provides for accelerated reaction and extremely short curing times. In addition, Hennecke GmbH's decades-long experience of high-pressure metering takes effect. This applies to mixheads for instance, which furnish high-quality and reproducible results at all times. Moreover, the use of the patented Hennecke constant-pressure injector ensures a controlled injection pressure - no matter whether RTM raw material systems with or without filler are being processed.
In future, customers and raw material suppliers will have the opportunity to find out more about these and further advantages at Hennecke's headquarters in Sankt Augustin.
However,with the decision to establish an RTM center for testing, development and mould trials, Hennecke GmbH provides not only its equipment, but also the know-how of experienced process engineers. Hennecke Managing Director Mr. Alois Schmid points out: "We intend to optimally assist our customers with the implementation of their ideas and plans before they purchase a processing plant and support them in their investment decision-making process". This close cooperation with business partners around the globe is one reason for Hennecke's innovative strength in the area of new technologies or applications. According to Jens Winiarz, Hennecke's responsible Sales Manager for Composite Spray Moulding (CSM) and new technologies, close cooperation with raw material suppliers is one of Hennecke's good traditions: "In our customer center for CSM polyurethane spray technology, we have already tested successful raw material systems and developed PU-based sprayed products. The RTM center will carry on this way.“
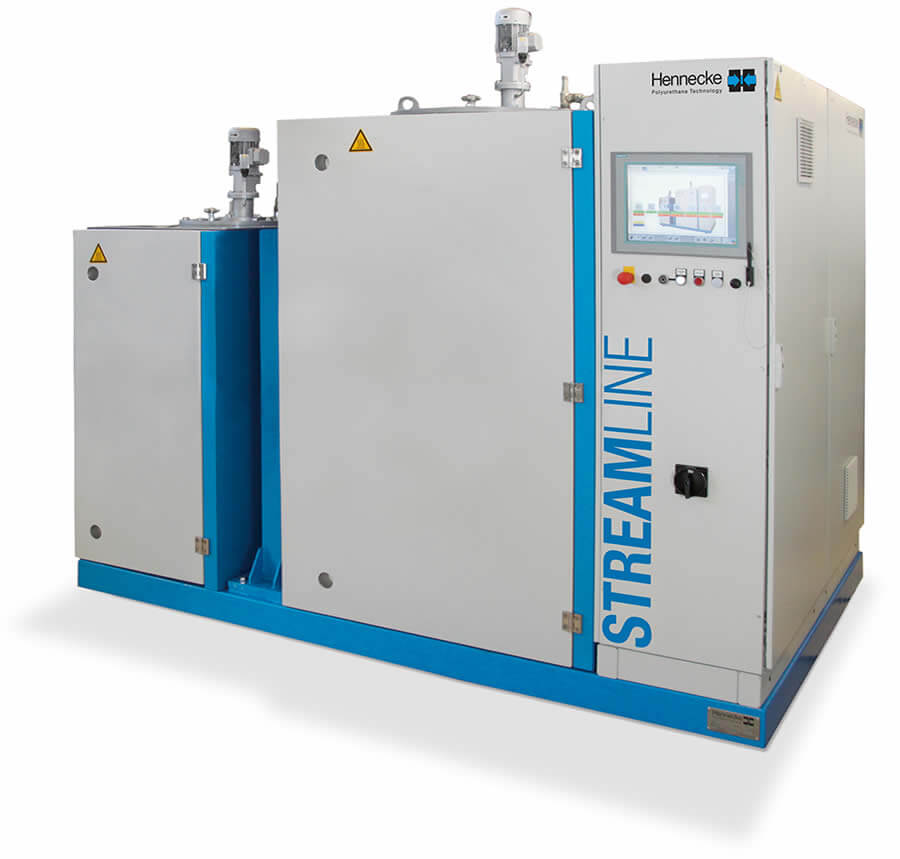