Unter Hochdruck leicht gemacht
Hennecke etabliert Kundencenter für großserientaugliche RTM-Anwendungen
Aufgrund der wachsenden Anforderungen an Effizienz und Ökologie nimmt das Interesse an Leichtbaulösungen im Automotive-Bereich besonders in der jüngeren Vergangenheit stetig zu. Ein Verfahren steht dabei besonders im Fokus: das Resin Transfer Moulding (RTM).Mit umfangreichen Investitionen in ein neues RTM-Center bietet die Hennecke GmbH sowohl interessierten Kunden als auch Rohstoffpartnern ab sofort genügend Spielraum, um Hochleistungs-Bauteile zu fertigen, zu testen und bis zur Serientauglichkeit zu entwickeln. Die Hennecke-Composite-Spezialisten können dabei mit einer entscheidenden, verfahrenstechnischen Weiterentwicklung der RTM-Technologie punkten, die hinsichtlich des Automatisierungsgrades und der Zykluszeit eine uneingeschränkte Großserientauglichkeit sicherstellt: das High-Pressure-RTM-Verfahren (HP-RTM).
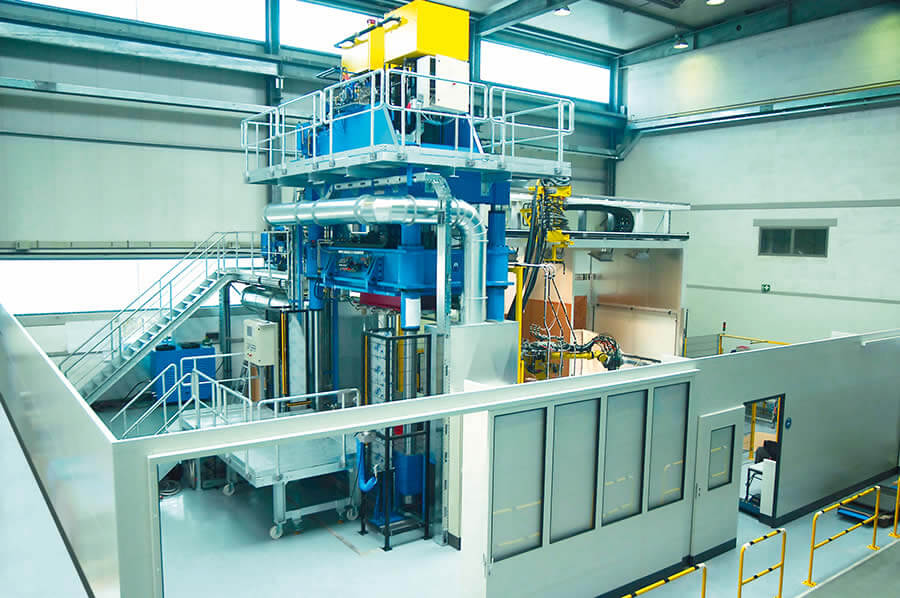
Die stark steigende Nachfrage nach Verbundwerkstoffen im Allgemeinen und Leichtbaulösungen im Speziellen dokumentiert die Hennecke GmbH durch stetige Forschungs- und Entwicklungsarbeit und den modularen Ausbau des Produkt-Portfolios. Auf diese Weise gelingt es dem Composite-Spezialisten in regelmäßigemAbstand, neue Produktionsverfahren und Anwendungsfelder bei der Herstellung und dem Einsatz von Verbundwerkstoffen zu identifizieren. Dies war bereits bei der PUR-CSM-Technologie so, die mittlerweile mehr als eine feste Größe bei der Herstellung von leichten und zugleich belastbaren PUR-Produkten mit Glas- oder Naturfaserverstärkung – auch in Form von Sandwich-Konstruktionen – darstellt.
Um im Automobilbau zukünftig eine weitere Steigerung der Effizienz und Energiebilanz zu gewährleisten, ist neben neuen Antriebskonzepten vor allem die Senkung des Fahrzeuggewichtes ein unverzichtbarer Baustein. Im Motorrennsport sorgt Leichtbau seit Langem für gesteigerte Performance beziehungsweise geringeren Verbrauch und hält deshalb zunehmend Einzug in die Serienproduktion von Kraftfahrzeugen. Im Karosseriebereich begegnen die Automobilbauer diesen Anforderungen mit faserverstärkten Strukturbauteilen, die neben dem geforderten geringen Gewicht auch die notwendigen Auflagen in puncto Crashverhalten erfüllen. Hierfür kommt meist das Resin-Transfer-Moulding-Verfahren (RTM) zum Einsatz. Dabei werden Harzsysteme unter niedrigem Druck in das geschlossene Werkzeug injiziert.
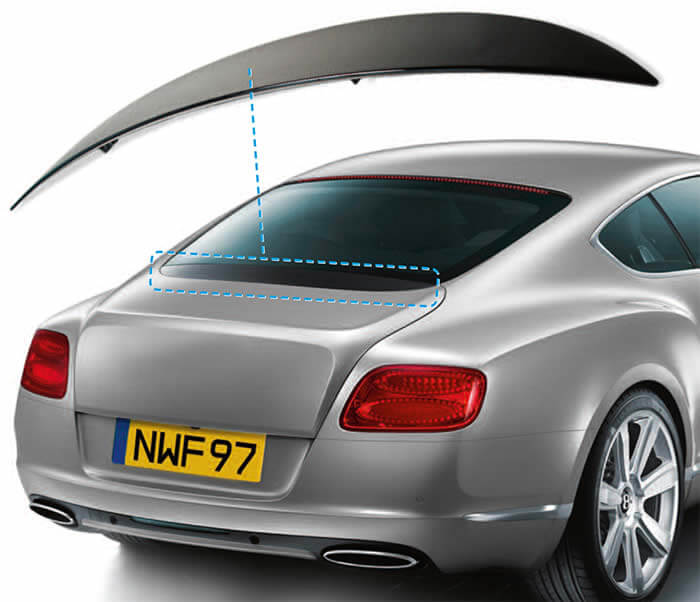
Aufgrund der weitestgehend manuellen Verarbeitung ist die Herstellung dieser Hightech-Bauteile im klassischen RTMVerfahren jedoch teilweise durch extrem lange Verfahrenszeiten geprägt. Deswegen sucht die Industrie momentan händeringend nach großserientauglichen Fertigungsmethoden,mit denen sich auch hohe Stückzahlen adäquat realisieren lassen. Eine gesteigerte Automatisierung alleine kann die Zykluszeit jedoch nur bedingt optimieren. Gefragt ist eine Lösung, welche die spezifischen Aushärtezeiten von Bauteilen entscheidend verkürzt.
Mit dem sogenannten High-Pressure-RTM-Verfahren (HP-RTM) hat sich die Hennecke GmbH dieser Problemstellung angenommen und bekannte Wege der Polyurethan-Verarbeitungstechnik neu beschritten. Im Mittelpunkt des HP-RTMVerfahrens steht dabei eine Aufgabenstellung, die innerhalb der PUR-Verarbeitung bestens bekannt und etabliert ist: die sekundenschnelle Hochdruck- Injektion von reaktivem Gemisch in eine Bauteilform. In Verbindung mit dem passenden Rohstoffsystem sorgt das beim HP-RTM-Verfahren für eine beschleunigte Reaktion und somit extrem kurze Aushärtezeiten. Zusätzlich kommt die jahrzehntelange Erfahrung der Hennecke GmbH im Bereich der Hochdruck-Dosierung zum Tragen. Beispielsweise bei Mischköpfen, die jederzeit hochqualitative und reproduzierbare Ergebnisse liefern. Durch den Einsatz der patentierten Hennecke-Gleichdruckdüse ist darüber hinaus ein kontrollierter Injektionsdruck gewährleistet – ganz gleich, ob RTM-Rohstoffsysteme mit oder ohne Füllstoff verarbeitet werden.
Von diesen und weiteren Vorteilen können sich Kunden und Rohstoffhersteller zukünftig am Hennecke-Stammsitz in Sankt Augustin selbst überzeugen. Mit der Entscheidung, ein RTM-Center für Versuche, Entwicklungen und Abmusterungen zu etablieren, stellt die Hennecke GmbH jedoch nicht nur ihr Equipment zur Verfügung, sondern auch das Know-how erfahrener Prozessingenieure. „Wir möchten unsere Kunden bei der Realisierung ihrer Ideen und Vorhaben bereits vor dem Kauf einer Verarbeitungsanlage optimal unterstützen und damit letztlich auch bei der Investitionsentscheidung zur Seite stehen“, betont der Hennecke-Geschäftsführer Alois Schmid. Diese enge Zusammenarbeit mit Geschäftspartnern rund um den Globus ist ein Grund für die Innovationskraft im Bereich neuartiger Technologien oder Anwendungen. Auch die Kooperation mit Rohstoffherstellern ist für Hennecke gute Tradition,wie JensWiniarz weiß, der bei Hennecke für den Vertrieb von Composite-Spray-Moulding (CSM) und neuen Technologien verantwortlich ist: „Bereits innerhalb unseres Kundencenters für die Polyurethan-Sprühtechnik CSM konnten wir erfolgreiche Rohstoff- Systeme testen und gesprühte Produkte auf PU-Basis entwickeln. Hier wird das Kundencenter für RTM-Anwendungen nahtlos anknüpfen.“
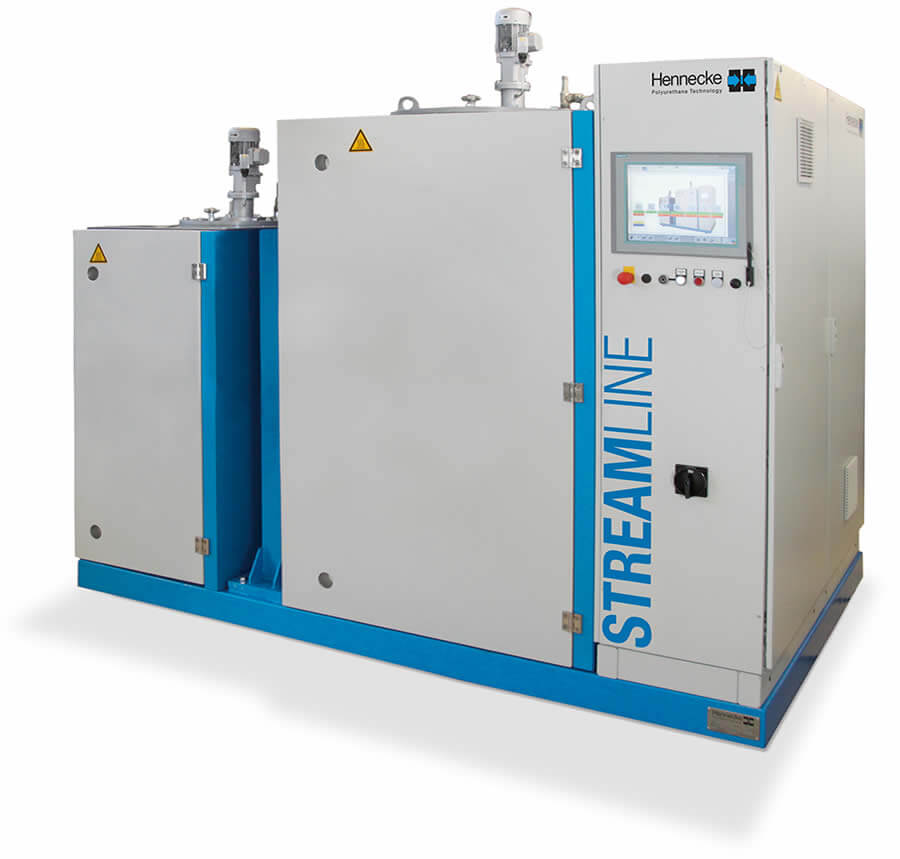
Download - Ausgabe 111 (PDF)
Zur Betrachtung benötigen Sie den Adobe® Reader®, den Sie hier kostenlos herunterladen können.