Flexible and efficient
The economic production of foamed moulded parts for car seats
An important element in the overlap between man and automobile is the car seat, which is expected to be comfortable and safe. Foamed moulded parts made from polyurethane help to ensure this. WKH production systems, used by Johnson Controls or Lear Corporation, demonstrate how these moulded parts can be produced economically when there is a large number of car models but smaller quantities and increasingly shorter cycles.
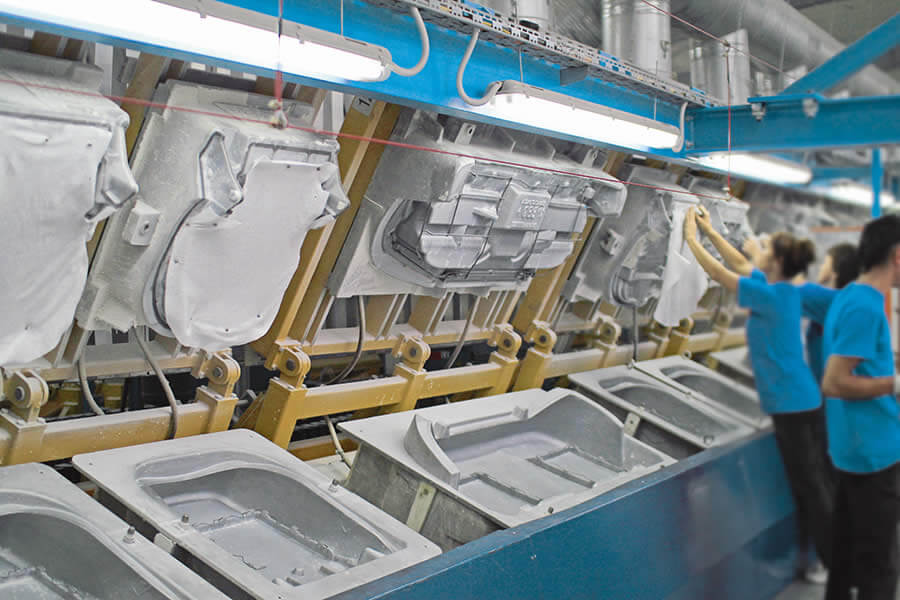
The main use of Hennecke oval conveyors is to produce PU foam parts for car seats and backrests, as well as smaller parts such as armrests, headrests and side bolsters. As in many other areas of car manufacture the number of variations is also growing in seat production. Flexible production technology for manufacturing moulded foam, as is provided by Hennecke WKH oval conveyors, is the solution for this challenge. “The current situation in the production is as follows: To make seats for various manufacturers and car types that have different formulations on one system. Thus the plant’s capacity utilization is optimized,” says Nils Boigk, moulded foam specialist at Hennecke.
In WKH oval conveyors (with horizontal carriage chain), the mould carriers perform the mould closing and opening movements and absorb the forces that arise from the process. The mould carriers move continuously in a chain in the oval. The insertion, foam injection and removal take place on the long side and then the foam cures on the back straight. The mould carriers can be automatically moved in or out during production so the moulds can be changed.
Ergonomic assembly
The first operation is the application of release agent in the open mould. In many cases this is done by hand. “When systems have very fast cycles, one or two robots are used for dispensing the release agent,“ says Boigk. The second step is for the operators to place inserts such as clips, wires, fleece elements or foam pads. "There can be up to 30 different parts depending on the mould configuration of the plant", explains Boigk. To enable an ergonomic assembly, the moulds are inclined towards the operator. Once all inserts are in place the bottom part moves back into the horizontal position so that it can be filled with foam by one or two robots. The system recognizes the mould and automatically adjusts the formulation and amount of foam. Depending on the type of seat the foam is produced in mono or dual hardness technology. “The use of foaming robots has been designed in a very flexible manner. One robot can fill a mould or two robots can fill a mould together,“ says Boigk. The foaming plant has an output of ca. 500 g/s and the weight of the foam parts can range from 800 grams to five kilograms depending on the system.
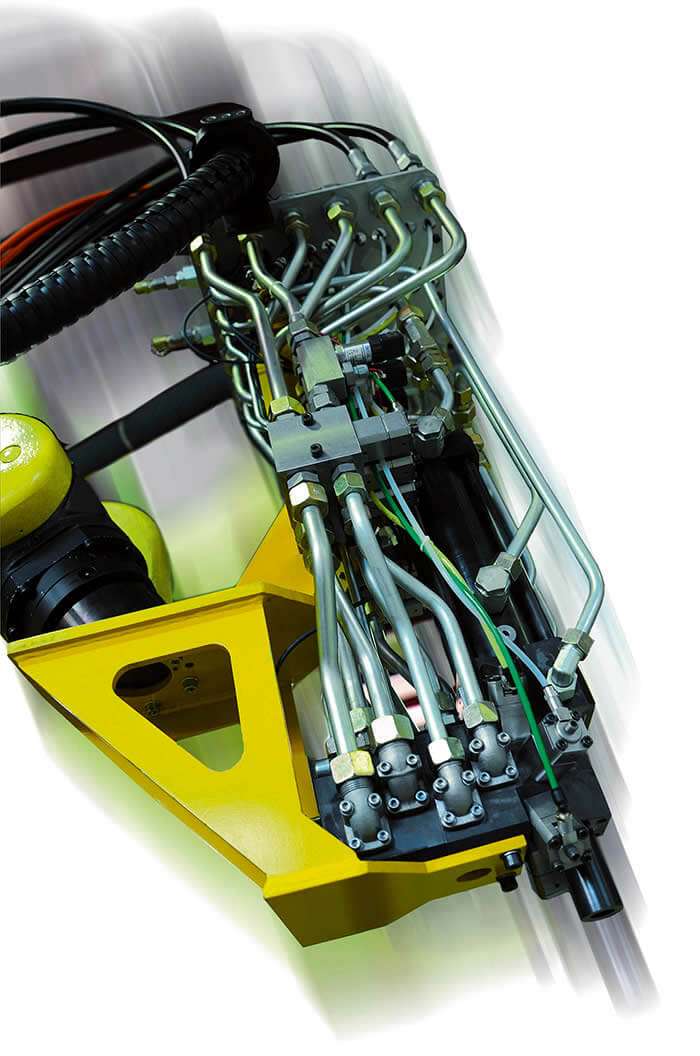
The lid is either closed hydraulically, mechanically by skids or via a closing station. “We have optimized the opening and closing by skids and users are very pleased with this,” says Boigk. “It is a purely mechanical process that does not cause any wear and requires little maintenance. However, the closing operation depends on the speed of the plant. This is not a problem for most users as the systems always run at full capacity.”An air cushion under the mould ensures there is a parallel stroke of about 20 millimetres and thus provides the appropriate clamping force against the foam that creates pressure from within. The foam then cures on the back straight. At the end, shortly before the bend, there is a brief intermediate ventilation as the air cushion deflates so that gas residues can be removed. In or after the bend the lid opens completely so that the workers can take out the finished foam parts. “When we remove the parts we are very dependent on the operators’ skills with their hands as undercuts are very often left in the moulds,” says Boigk. “It takes a lot of skill to take the foam parts out of the mould without any breakage or tearing.” The plant manufacturer is currently working with car seat makers to increase the automated processes in the oval conveyors. “Apart from removing the parts carefully, the biggest challenge is placing the inserts. Because of the great variety of materials and types of inserts the limits of robots and gripping systems are quickly reached.” In the last step, the mould is blown dry with compressed air so that it is again ready for the application of release agent. Depending on the size of the foam part the cycle ranges from nine to 20 seconds.
Constant pressure
The plant manufacturer has developed the MT 22-6 mixhead to meet the high demands of customers such as Johnson Control and Lear. “This mixhead is the high-end solution for the production of foamed automotive seating,” reports Boigk. The mixing system is suitable for six main components that can be switched separately. Hennecke’s patented constant pressure injector technology ensures that the foam is discharged with constant pressure Thus, the quality of the foam is always of an equally high standard regardless of fluctuations in output. The mixhead can also be switched very fast, in about 500 milliseconds, so that it can be cleaned in between and formulations can be changed within the production process. “The optimization of our internal workflow regarding costs and processing times has led to strong demand in the market,” says Boigk. “The new mixhead has convinved many users. With the generous variation of formulation from one shot to the next we have taken the flexibility of our lines even further.”