Flexibel und effizient
Wirtschaftliche Herstellung von geschäumten Formteilen für Automobilsitze
Eine wesentliche Komponente in der Schnittstelle zwischen Mensch und Automobil ist der Fahrzeugsitz. Er soll komfortabel und sicher sein. Dafür sorgen unter anderem geschäumte Formteile aus Polyurethan. Wie diese Formteile wirtschaftlich bei einer großen Anzahl von Fahrzeugmodellen bei gleichzeitigem Rückgang der Modellstückzahlen und immer kürzer werdenden Produktionszyklen hergestellt werden können, zeigen Produktionsanlagen vom Typ WKH, wie sie bei Johnson Controls oder der Lear Corporation zum Einsatz kommen.
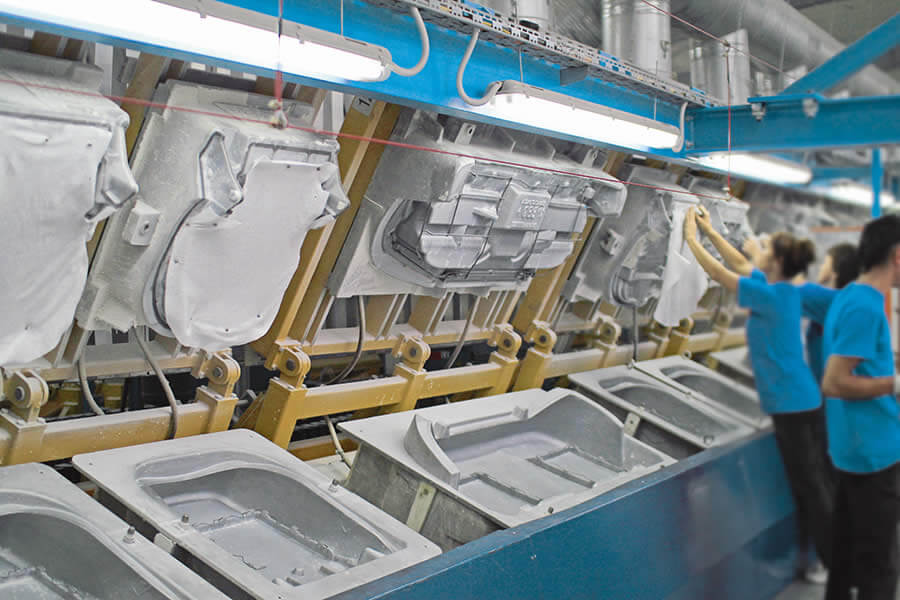
Das Haupteinsatzgebiet von Hennecke-Ovalförderanlagen ist die Produktion von PUR-Schaumteilen für Sitze und Lehnen in Fahrzeugen. Auch kleine Teile wie Armauflagen, Kopfstützen und Sidebolster werden so produziert. Wie in vielen anderen Bereichen der Fahrzeugteileproduktion werden auch bei der Sitzherstellung die Variantenzahlen höher. Flexible Produktionstechnik für die Form- schaumherstellung, wie sie Hennecke mit den WKH-Ovalförderanlagen anbietet, ist die Lösung für diese Herausforderung. Nils Boigk, Formschaumspezialist des Unternehmens, erklärt: „Die aktuelle Situation in der Produktion ist folgende: Sitze verschiedener Hersteller und Fahrzeugtypen mit unterschiedlichen Rezepturen auf einer Anlage herzustellen. Durch diese Produktionsweise lässt sich die Auslastung der Anlage optimieren.“ Bei den Ovalförderern der Baureihe WKH (Wagenketten horizontal) führen die Formenträger die Werkzeugschließ- und Öffnungsbewegungen durch und nehmen die verfahrensbedingten Kräfte auf. Die Formenträger laufen kontinuierlich in einer Kette im Oval. Auf der einen Längsseite findet das Einlegen, Schaumeintragen und die Entnahme statt und auf der Gegengerade härtet der Schaum aus. Um Formen zu wechseln, lassen sich die Formenträger automatisch bei laufender Produktion ein- und ausschleusen.
Ergonomische Bestückung
Der erste Arbeitsschritt an der Anlage ist der Trennmittelauftrag in der geöffneten Form. In vielen Fällen geschieht das von Hand. „Bei Anlagen mit sehr schnellen Zykluszeiten kommen für den Trennmittelauftrag ein bis zwei Roboter zum Einsatz“, sagt Boigk. Als zweiten Arbeitsschritt legen Werker die Einleger ein. Das können je nach Sitz Clipse, Drähte, Fleece-Elemente und Schaumpads sein. „Hier kommen je nach Formbestückung der Anlage bis zu 30 verschiedene Teile zusammen“, erläutert Boigk. Für die ergonomische Bestückung werden die Formen dem Bedienpersonal zugeneigt. Nachdem alle Insertteile an ihrem Platz sind, verfährt das Unterteil wieder in die horizontale Lage, um von einem oder zwei Robotern mit Schaum gefüllt zu werden. Die Anlage erkennt die Form und stellt die Rezeptur und die Menge des Schaums automatisch ein. Je nach Sitztyp wird der Schaum in Mono- oder in Dual-Hardness-Technik ausgeführt. „Der Einsatz der Schäumroboter ist sehr flexibel konzipiert. Es kann je ein Roboter eine Form füllen oder zwei Roboter füllen gemeinsam eine Form.“ Die Schaumanlage hat eine Austragsleistung von ca. 500 g/s und die Gewichte der Schaumteile reichen je nach Anlage von 800 Gramm bis fünf Kilogramm.
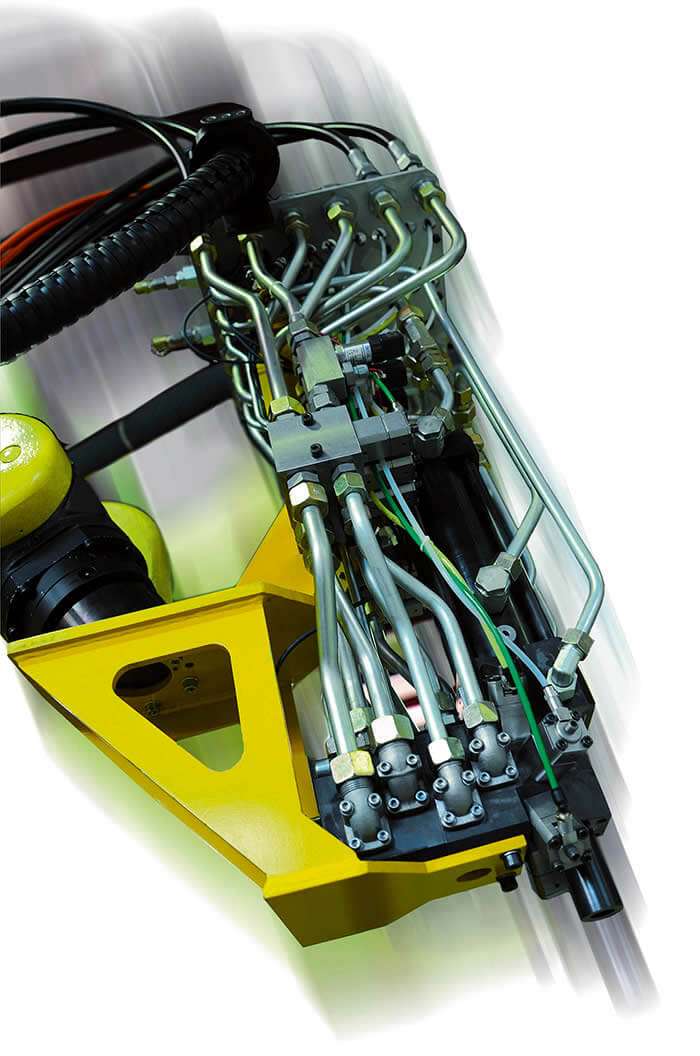
Das Schließen des Deckels erfolgt entweder hydraulisch, mechanisch über Kufen oder über eine Schließstation. „Das Schließen und Öffnen durch die Kufen haben wir optimiert, das kommt auch bei den Anwendern sehr gut an,“ sagt Boigk. „Das ist ein rein mechanischer Vorgang, der keinen Verschleiß verursacht und wenig Wartung braucht. Der Schließvorgang ist somit jedoch von der Geschwindigkeit der Anlage abhängig. Für die meisten Anwender ist das kein Problem, da die Anlagen immer unter voller Auslastung laufen.“ Ein Luftkissen unter der Form sorgt für einen Parallelhub von etwa 20 Millimetern und bringt so die notwendige Zuhaltekraft gegen den von innen drückenden Schaum auf. Auf der Gegengerade härtet der Schaum aus. Am Ende, kurz vor der Kurve, erfolgt durch Ablassen des Luftkissens ein kurzes Zwischenlüften, um Gasreste aus der Form zu bringen. In oder nach der Kurve öffnet sich der Deckel vollständig, damit der Mitarbeiter das fertige Schaumteil entnehmen kann. „Wir sind bei der Entnahme auf das handwerkliche Geschick der Mitarbeiter angewiesen, denn es sind sehr oft Hinterschnitte in den Formen,“ sagt Boigk. „Es erfordert viel Gefühl, das Schaumteil aus der Form zu zerren, ohne dass es zerreißt.“ Der Anlagenbauer arbeitet zurzeit mit den Sitzherstellern daran, den Automationsanteil an den Ovalförderanlagen weiter zu erhöhen. Dazu Boigk: „Die größte Herausforderung ist – neben der gefühlvollen Entnahme – das Einlegen der Insertteile. Durch die Vielzahl der verschiedenen Materialien und Formen der Einlegeteile kommen Roboter und Greifersysteme schnell an ihre Grenzen.“ Im letzten Arbeitsschritt wird die Form mit Druckluft ausgeblasen und ist wieder bereit für den Trennmittelauftrag. Die Zykluszeit auf einer Anlage beträgt je nach Größe des Schaumteils zwischen neun und 20 Sekunden.
Konstanter Druck
Für die hohen Ansprüche von Kunden wie Johnson Control und Lear hat der Anlagenbauer den Mischkopf MT 22-6 entwickelt. „Dieser Mischkopf ist die High-End-Lösung für die Automotive-Sitzschaumproduktion“, berichtet Boigk. Das Mischsystem ist für sechs individuell schaltbare Hauptkomponenten ausgelegt. Die patentierte Hennecke-Gleichdruckdüsentechnologie sorgt dafür, dass der Schaum mit konstantem Druck ausgetragen wird. Dadurch bleibt auch bei schwankender Austragsleistung die Qualität des Schaums immer auf dem gleichen hohen Niveau. Der Mischkopf hat für Zwischenreinigungen und Rezepturumstellungen sehr schnelle Umschaltzeiten von ungefähr 500 Millisekunden. „Die Optimierung unserer internen Abläufe im Unternehmen hinsichtlich Kosten und Durchlaufzeiten hat zu einer starken Nachfrage im Markt geführt,“ sagt Boigk. „Auch der neue Mischkopf hat viele Anwender überzeugt. Mit der freizügigen Rezepturvariation von Schuss zu Schuss haben wir die Flexibilität unserer Anlagen noch weiter vorangetrieben.“
Download - Ausgabe 111 (PDF)
Zur Betrachtung benötigen Sie den Adobe® Reader®, den Sie hier kostenlos herunterladen können.