PUR-Anwendungen in der Batterietechnik
Maximale Performance und Sicherheit für das Herzstück der Elektromobilität
Die Mobilitätswende profitiert auch vom Hennecke Know-how. Der E-Antrieb setzt sich bei PKWs zunehmend durch, aber auch die Transportbranche fängt an umzudenken. Ein zentrales Element für diesen technologischen Wandel ist die Batterie: Sie bildet das Herzstück eines jeden Elektrofahrzeugs und bestimmt maßgeblich dessen Reichweite, Sicherheit und Lebensdauer. Doch die Anforderungen an Batterien sind hoch. Sie müssen robust sein, äußeren Einflüssen standhalten, ein effizientes thermisches Management bieten und gleichzeitig den höchsten Sicherheitsstandards entsprechen. Hier kommen die vielseitigen Polyurethan-Anwendungen ins Spiel, die von Hennecke als führendem Anbieter von PUR-Technologien mitentwickelt werden. „Unsere Lösungen tragen entscheidend dazu bei, die Performance und Sicherheit der Batterien in Elektrofahrzeugen zu maximieren“, so Jens Geuer, Leiter F&E-Verfahrenstechnik bei Hennecke am Standort in Sankt Augustin.
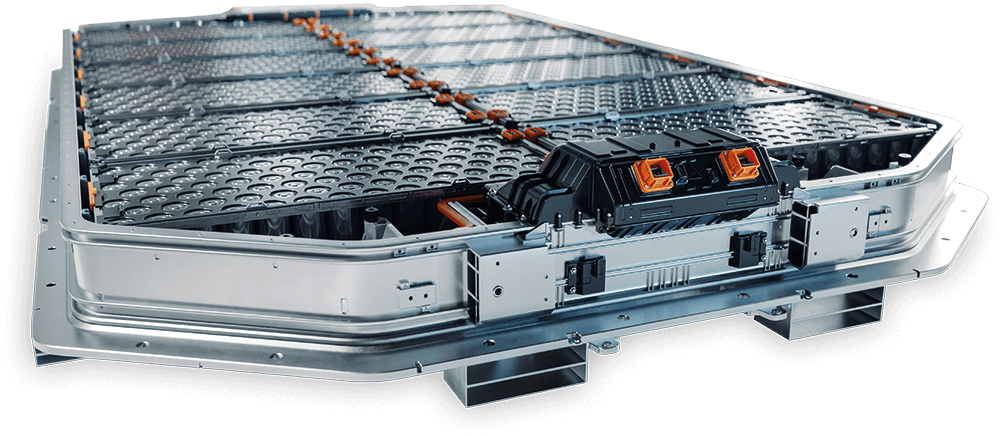
Robuster Schutz vor äußeren Einwirkungen
Batterien in Elektrofahrzeugen sind aufgrund ihres Gewichts und ihrer Größe meist im Unterboden des Fahrzeugs verbaut. Diese Position ist ideal für den Schwerpunkt des Fahrzeugs, macht sie jedoch anfällig für äußere Einwirkungen, sei es durch aufwirbelnde Steine, Unebenheiten auf der Straße oder bei Unfällen. Ein wirkungsvoller Unterbodenschutz ist daher unerlässlich.
Bei PKWs und Kleintransportern kommen hierbei moderne Unterbodensysteme zum Einsatz, die aus besonders leichten und gleichzeitig sehr robusten Materialien wie Carbonfaser- oder Glasfasergelegen bestehen. Diese Materialien werden im Nasspressverfahren (Wet Compression Moulding bzw. WCM) verarbeitet. Dabei wird das Fasergelege mit einem Polyurethan- oder Epoxidharz- Reaktivgemisch durchtränkt und in die gewünschte Form gebracht. Das Ergebnis ist ein leichter, aber hochfester und zudem Crash-relevanter Schutz für die Batterie, der das Gewicht des Fahrzeugs nicht unnötig erhöht und somit zur Reduktion von Umweltbelastungen beiträgt. Für die Herstellung dieser Unterböden eignet sich besonders die JETLINE, die maßgeschneidert für die effiziente Herstellung von faserverstärkten Strukturbauteilen mittels WCM ist. Eine zusätzliche Alternative stellt die STREAMLINE MK2 dar, die ein breites verfahrenstechnisches Einsatzspektrum bietet und ebenfalls das WCM-Verfahren ermöglicht. Der große Vorteil dieser beiden Methoden ist, vorab definierte und durch Simulation bestimmte Faserorientierungen zu verwenden. Damit können Hersteller das Crash-relevante Aufprallverhalten präzise simulieren und im fertigen Bauteil umsetzen.
Effizientes thermisches Management
Eine der größten Herausforderungen bei der Entwicklung von Batterien für Elektrofahrzeuge stellt das thermische Management dar. Batterien müssen in einem optimalen Temperaturbereich betrieben werden, um hohe Leistungsfähigkeit und lange Lebensdauer zu gewährleisten. Bei zu hohen Temperaturen besteht die Gefahr der Überhitzung, während bei niedrigen Temperaturen die Reichweite des Fahrzeugs stark beeinträchtigt wird. Ein effizientes Temperaturmanagement ist entscheidend, um nicht nur die Leistung zu maximieren, sondern auch die Lebensdauer der Batterien zu verlängern und den Bedarf für einen Austausch zu minimieren, was Ressourcen spart und die Umweltbelastung verringert. Hennecke setzt hier auf das Composite Spray Moulding (CSM)-Verfahren, bei dem isolierende Kühlschleifen mittels Polyurethan- Sprühverfahren auf den Unterboden aufgebracht werden. Der Sprühauftrag erfolgt meist durch Hochdruck-Dosiermaschinen der Baureihe TOPLINE, die speziell auf das PUR-CSM-Verfahren abgestimmt sind. Eine weitere Option zur Realisierung stellt das RIM-Verfahren (Reaction Injection Moulding) dar. Beide Verfahren sorgen für eine exakt definierte Schaumschicht, die über hervorragende Isolationseigenschaften verfügt und somit eine präzise Temperaturkontrolle der Batterien ermöglicht. Im Ergebnis führt dies zu einer effizienteren Batterieperformance und einer längeren Lebensdauer, was den nachhaltigen Einsatz von Ressourcen zusätzlich fördert.
Die Batterie – Das Herzstück eines Elektrofahrzeugs
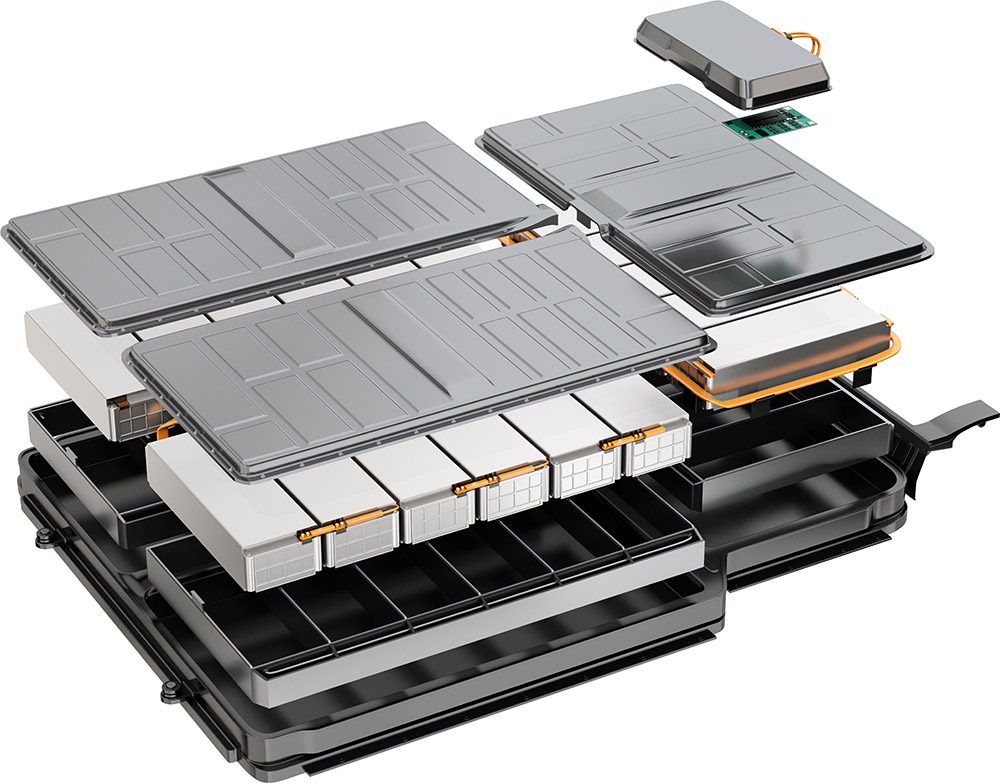
Präzision und Sicherheit bei der Batterieproduktion
Ein weiteres kritisches Element in der Batteriefertigung ist die sichere und präzise Verbindung der einzelnen Batteriekomponenten. Hierfür werden hochreaktive Zweikomponenten-Rohstoffsysteme verwendet, die in kleinsten Mengen dosiert in sogenannten Kleberaupen aufgetragen werden. Diese Aufgabe erfordert höchste Präzision, da die Klebstoffverbindungen extrem belastbar sein müssen, um den mechanischen und thermischen Anforderungen gerecht zu werden. Neben der Verbesserung von Sicherheit und Leistung ermöglicht die hochpräzise Dosierung auch eine Reduzierung des Materialverbrauchs. Durch den gezielten Einsatz des Klebstoffs in der genau benötigten Menge wird Materialverschwendung minimiert, was nicht nur Kosten spart, sondern auch zur Schonung von Ressourcen beiträgt. Diese effiziente Nutzung von Materialien verringert den ökologischen Fußabdruck der Produktion und unterstützt die nachhaltigen Ziele der Hersteller. „Im Maschinen- Portfolio eignet sich die neue MICRO SERIES hervorragend für diese anspruchsvolle Aufgabe. Durch ihre besondere Fähigkeit, auch kleinste Mengen mit hoher Genauigkeit aufzutragen, sorgt sie für eine sichere und präzise Verklebung der Batterien“, erklärt Jens Geuer. Durch diese präzise Anwendung wird nicht nur die strukturelle Integrität der Batterien gewährleistet, sondern auch eine nachhaltigere Produktionsweise gefördert.
„Die Entwicklungen in der Batterietechnik sind rasant, aber Hennecke agiert stets am Puls der Zeit, um innovative Lösungen für neue Herausforderungen zu bieten.“
Steve Tetzlaff,
Regional Sales Manager bei Hennecke
Brandschutz und sichere Versiegelung
Ein nicht zu unterschätzendes Risiko bei Batterien ist die Entstehung von Bränden. Um zu verhindern, dass ein Feuer von einer Zelle auf die anderen übergreift, bietet sich die PUR-Gießtechnik mit einem brandhemmenden Schaumsystem an. Mit einer Hochdruckdosiermaschine wie der TOPLINE MK2 wird der Batterieblock mit den oftmals hunderten einzelnen Batteriezellen mit einem hochdichten Schaumsystem vollständig ausgeschäumt und versiegelt. Die Polyurethan-Schäume bieten nicht nur einen effektiven Brandschutz, sondern tragen hierbei auch zur strukturellen Integrität des Batteriegehäuses bei, indem sie dieses vollständig ausfüllen und gegen äußere Einflüsse abdichten. Dabei sind verschiedene Varianten verfügbar, bei denen das Polyurethansystem entweder in eine offene oder in eine geschlossene Form injiziert werden kann.
Kabeltüllen: Schutz der Fahrzeug-Lebensadern
Neben den Batterien selbst spielt auch der Schutz der elektrischen Verkabelung in Elektrofahrzeugen eine wichtige Rolle. Die sogenannten Kabeltüllen, die als Verbindung zwischen verschiedenen Kabelsträngen dienen, müssen besonders robust und langlebig sein. Hennecke setzt hier auf die bewährte Hochdruckdosiertechnologie der MK2-Baureihe, um Polyurethan-Kabeltüllen herzustellen, die den höchsten Anforderungen gerecht werden. Diese Kabeltüllen sind nicht nur wasser- und gasdicht, sondern sorgen auch für eine sichere Fixierung des Kabelbaums, selbst unter schwierigen Bedingungen.
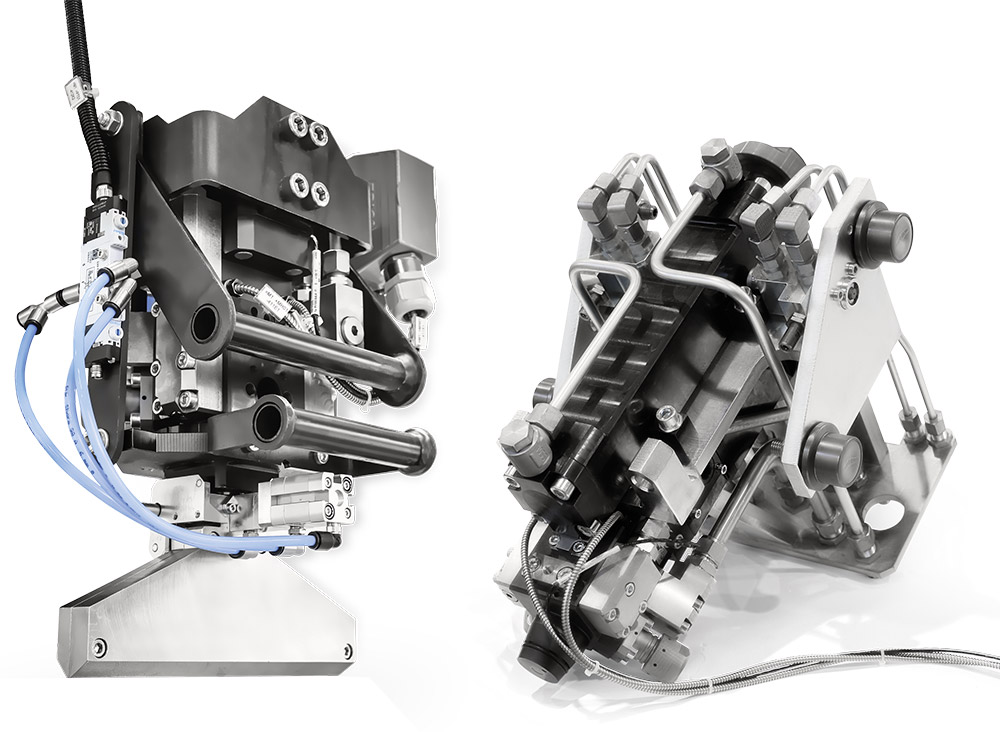
Mischkopftechnik für WCM- und HP-RTM-Anwendungen.
Immer einen Schritt voraus
„Die Entwicklungen in der Batterietechnik sind rasant, aber Hennecke agiert stets am Puls der Zeit, um innovative Lösungen für neue Herausforderungen zu bieten“, berichtet Steve Tetzlaff, der als Regional Sales Manager bei Hennecke im steten Austausch mit Kunden und Anwendern der Branche ist. Die vielseitigen Anwendungen von Polyurethan in der Batterietechnik leisten einen entscheidenden Beitrag zur Sicherheit und Performance von Elektrofahrzeugen und machen Hennecke zu einem unverzichtbaren Partner der Mobilitätsindustrie. So können sich Hersteller auf langlebige, sichere und effiziente Lösungen verlassen, die die Zukunft der Elektromobilität maßgeblich mitgestalten.
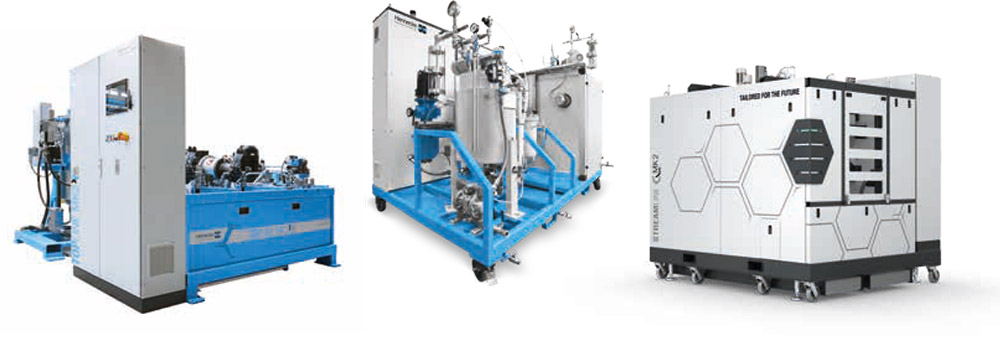
Download - Ausgabe 124 (PDF)
Zur Betrachtung benötigen Sie den Adobe® Reader®, den Sie hier kostenlos herunterladen können.