PU applications in battery technology
Maximum performance and safety for the heart of electromobility
The mobility revolution also benefits from Hennecke‘s know-how. Electric drives are becoming increasingly popular in cars, but the transport industry is also starting to rethink things. A key element in this technological change is the battery: it forms the heart of every electric vehicle and largely determines its range, safety and service life. But the demands on batteries are high. They must be robust, withstand external influences, offer efficient thermal management and at the same time meet the highest safety standards. This is where the versatile polyurethane applications come into play, which are being co-developed by Hennecke, a leading provider of PU technologies. “Our solutions make a decisive contribution to maximizing the performance and safety of batteries in electric vehicles,” says Jens Geuer, Head of R&D Process Technology at Hennecke’s Sankt Augustin site.
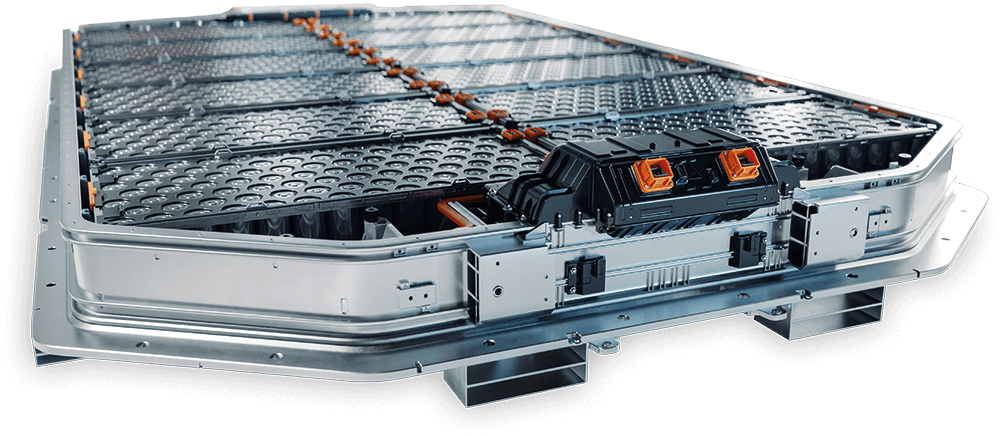
Robust protection against external influences
Due to their weight and size, batteries in electric vehicles are usually installed in the underbody of the vehicle. This position is ideal for the vehicle’s center of gravity, but makes them vulnerable to external impacts, be it from stones being thrown up, bumps in the road or accidents. Effective underbody protection is therefore essential.
For cars and vans, modern underbody systems are used that consist of particularly light and at the same time very robust materials such as carbon fiber or glass fiber fabrics. These materials are processed using the wet compression moulding (WCM) process. The fiber fabric is soaked with a polyurethane or epoxy resin reactive mixture and shaped into the desired form. The result is a lightweight but high-strength and crash-relevant protection for the battery that does not increase the weight of the vehicle unnecessarily and thus helps to reduce environmental pollution. The JETLINE is particularly suitable for the production of these underbodies, as it is tailor-made for the efficient production of fiber-reinforced structural components using WCM. An additional alternative is the STREAMLINE MK2, which offers a wide range of process-related applications and also enables the WCM process. The great advantage of these two methods is that they use fiber orientations that are defined in advance and determined by simulation. This enables manufacturers to precisely simulate the crash-relevant impact behavior and implement it in the finished component.
Efficient thermal management
One of the biggest challenges in developing batteries for electric vehicles is thermal management. Batteries must operate within an optimal temperature range to ensure high performance and a long service life. Too high temperatures run the risk of overheating, while low temperatures severely affect the vehicle‘s range. Efficient temperature management is crucial to not only maximize performance, but also extend battery life and minimize the need for replacement, saving resources and reducing environmental impact. Hennecke uses the Composite Spray Moulding (CSM) process, in which insulating cooling loops are applied to the underbody using a polyurethane spray process. The spray coat is usually applied by high-pressure metering machines from the TOPLINE series, which are specifically designed for the PU Composite Spray Moulding process. Another option for implementation is the RIM process (Reaction Injection Moulding). Both processes ensure a precisely defined foam layer that has excellent insulation properties and thus enables precise temperature control of the batteries. This leads to more efficient battery performance and a longer service life, which also promotes the sustainable use of resources.
The battery – the heart of an electric vehicle
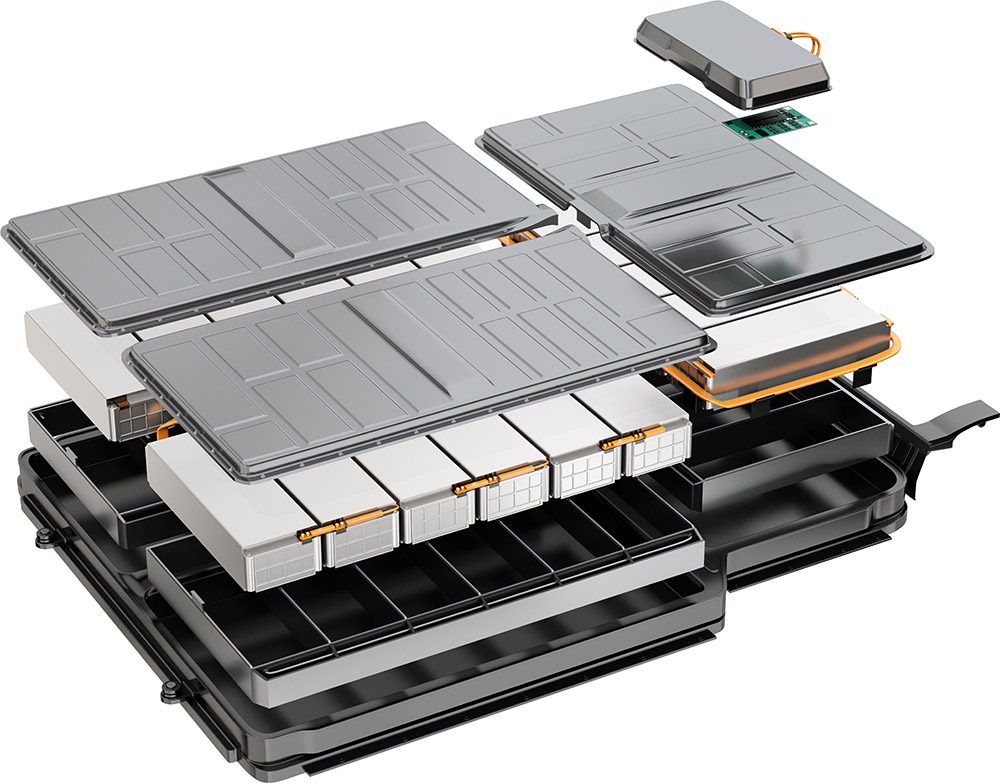
Precision and safety in battery production
Another critical element in battery production is the safe and precise connection of the individual battery components. Highly reactive two-component raw material systems are used to do this, which are applied in tiny amounts in so-called adhesive beads. This task requires the highest precision, as the adhesive bonds must be extremely resilient in order to meet the mechanical and thermal requirements. In addition to improving safety and performance, high-precision dispensing also enables a reduction in material usage. By using the adhesive in the exact amount required, material waste is minimized, which not only saves costs but also helps to conserve resources. This efficient use of materials reduces the ecological footprint of production and supports the sustainable goals of manufacturers. “In the machine portfolio, the new MICRO SERIES is ideally suited to this demanding task. Thanks to its special ability to apply even the smallest quantities with high precision, it ensures that the batteries are bonded safely and precisely,” explains Jens Geuer. This precise application not only ensures the structural integrity of the batteries, but also promotes a more sustainable production method.
„Battery technology is developing rapidly. But Hennecke is always at the forefront, offering innovative solutions to new challenges.“
Steve Tetzlaff,
Regional Sales Manager at Hennecke
Fire protection and secure sealing
A risk with batteries that should not be underestimated is the occurrence of fire. To prevent a fire from spreading from one cell to the others, PU casting technology with a fire-retardant foam system is ideal. Using a high-pressure metering machine such as the TOPLINE MK2, the battery block, which often contains hundreds of individual battery cells, is completely filled with foam and sealed with a high-density foam system. The polyurethane foams not only offer effective fire protection, but also contribute to the structural integrity of the battery housing by completely filling it and sealing it against external influences. Several variants are available in which the polyurethane system can be injected into either an open or a closed mold.
Cable grommets: protecting the vehicle‘s lifelines
In addition to the batteries themselves, protecting the electrical wiring in electric vehicles also plays an important role. The so-called cable grommets, which serve as a connection between different cable harnesses, must be particularly robust and durable. Hennecke relies on the proven high-pressure metering technology of the MK2 series to produce polyurethane cable grommets that meet the highest requirements. These cable grommets are not only water and gas-tight, but also ensure that the cable harness is securely fixed, even under difficult conditions.
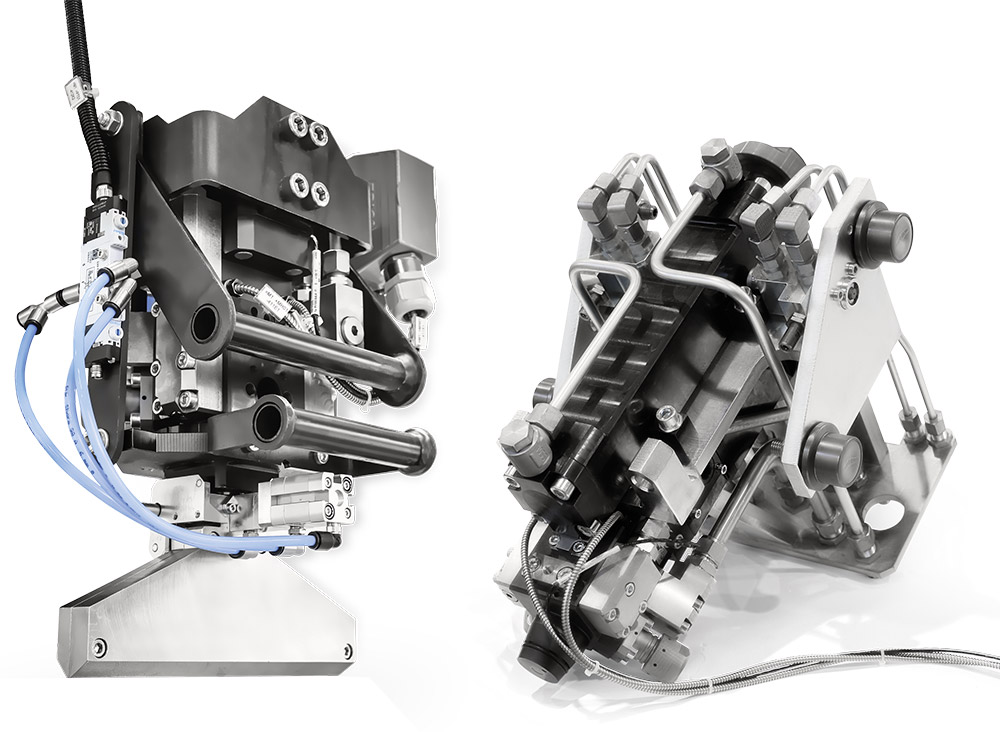
Mixhead technology for WCM and HP-RTM applications.
Always one step ahead
“Battery technology is developing rapidly. But Hennecke is always at the forefront, offering innovative solutions to new challenges,” reports Steve Tetzlaff, who, as Regional Sales Manager at Hennecke, is in constant contact with customers and users in the industry. The versatile applications of polyurethane in battery technology make a decisive contribution to the safety and performance of electric vehicles and make Hennecke an indispensable partner for the mobility industry. Manufacturers can therefore rely on longlasting, safe and efficient solutions that play a key role in shaping the future of electromobility.
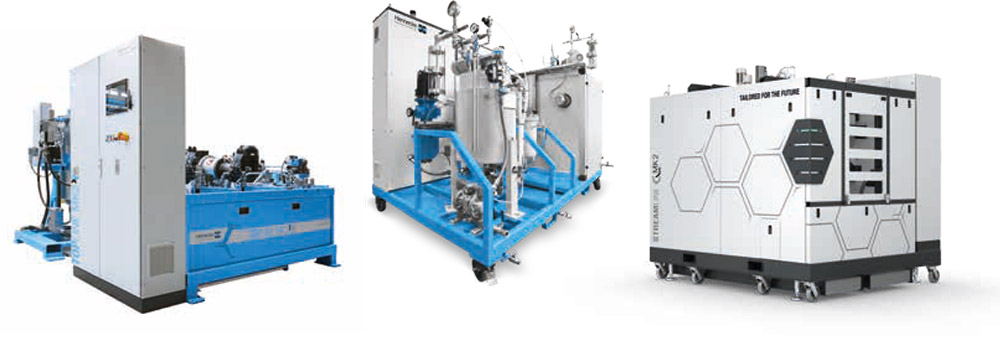