Auf den Kopf gestellt
Seitenwände für LKW-Anhänger in Sandwich-Bauweise
Sandwich-Elemente mit Polyurethan-Kern sind seit langer Zeit bewährte Bauteile und kommen auch abseits der Baubranche in unzähligen Anwendungen zum Einsatz. Die diskontinuierliche Fertigung dieser Panels erfolgt üblicherweise liegend und abgedichtet in einer Presse. Der südamerikanische Pressen-Spezialist Iturrospe mit Sitz in Rosario (Argentinien) stellt diese Vorgehensweise jedoch regelrecht auf den Kopf. Iturrospe fertigt sogenannte A-Frame-Pressen, in denen Wandelemente für LKW-Trailer aufrechtstehend im „Freischaumverfahren“ hergestellt werden. Hennecke liefert hierfür das PUR-Know-how sowie das dazugehörige Nassteil in Form einer TOPLINE HK 1250.
Sogenannte Koffersattel-Anhänger kommen zum Einsatz, wenn es um den Transport von temperaturempfindlichen Waren geht. Die bis zu 17x3 Meter großen Seitenwände werden in Sandwich-Bauweise hergestellt. Für hervorragende Isolationswerte zeichnet sich ein Kern aus Polyurethan verantwortlich, der je nach Anwendung in unterschiedlichen Dicken hergestellt wird. Die Außenhaut ist aus Aluminium ausgeführt und die Innenseiten können entweder aus Aluminium, Kunststoff oder Verbundmaterial bestehen. Die Dicke des dazwischen eingetragenen PUR-Schaums reicht von 38 mm bis zu 150 mm. Der Einsatzbereich der verschiedenen Versionen der Kofferaufbauten reicht von normalen Transportaufgaben bis hin zur Tiefkühllogistik.
Während solche großen, flächigen Bauteile bei herkömmlichen Pressen liegend geschäumt und anschließend gepresst werden, greift Iturrospe bei seiner so genannten A-Frame-Doppelpresse auf ein unkonventionelles Verfahren zurück: das Schäumen bei aufrechtstehender Presse. Dabei stehen die Seitenteile aufrecht und leicht geneigt an den beiden Schenkeln. Der große Vorteil hierbei ist der geringe Platzbedarf im Vergleich zu herkömmlichen Pressen. Daneben erleichtert der Aufbau die Zugänglichkeit und die gesamte Handhabung der extrem großen Bauteile erheblich. Um eine optimale Produktionsauslastung zu gewährleisten, wird die Aushärtezeit auf der einen Seite genutzt, um auf der anderen Seite bereits das nächste Panel für den Schäumvorgang vorzubereiten. Die stehende Seitenwand wird im „Freischaumverfahren“ gefüllt. Hierbei steigt der Schaum über die gesamte Höhe der Seitenwand. Die Presse ist während des Schäumvorgangs nach oben hin offen. Der Schaum nutzt also letztlich nur sein eigenes Gewicht als Gegendruck. Bei herkömmlichen Pressen setzt man stets geschlossene Formen ein, um eine möglichst gleichmäßige Dichteverteilung zu erreichen. Diese wichtige Eigenschaft wird bei A-Frame-Doppelpressen mittels spezieller Rohstoffsysteme sichergestellt. Bei der neuen A-Frame-Doppelpresse lässt sich die äußere Pressenseite über Spindelantriebe nach hinten fahren und mit Hydraulikzylindern ein Stück weit aufklappen. Das obere Drittel dieser Seite der Presse ist in weitere Bereiche unterteilt, die ebenfalls hydraulisch einzeln auf- und zuklappbar sind. Dadurch ist es möglich, mit dem Mischkopf in die Presse einzutauchen. Bei der Produktion legen die Bediener mithilfe eines Krans die vorbereiteten Innen- und Außenseiten in die Presse ein. Die Spindelantriebe fahren die äußere Pressenseite auf die genaue Position für die gewünschte Wanddicke. Die Pressenseite und ihr oberes Drittel bleiben dabei aufgeklappt. Auf der Arbeitsplattform oben auf der Presse ist ein Verfahrsystem aufgebaut, auf dem der Hennecke-Mischkopf servomotorisch angetrieben und etwa zu einem Drittel in die Form eingetaucht die gesamte Strecke abfahren kann, um das reaktive Gemisch mit bis zu drei Kilogramm pro Sekunde in die Seitenwand einzutragen. Die Verfahrgeschwindigkeit des Mischkopfs richtet sich nach der gewünschten Stärke des Sandwich-Elements. Dem Mischkopf nachfolgend klappen die einzelnen Segmente des oberen Drittels der Pressenseite ein. Ist der Mischkopf am Ende der Strecke angekommen und aus der Presse herausgefahren, klappt die gesamte Außenwand zu. Wenn die Presse geschlossen ist, fahren oben auf der Presse Verschlussdorne aus, die sich mit der anderen Presseseite mechanisch verriegeln und den in der Form entstehenden Druck aufnehmen. Je nach Ausführung der Anhängerwand dauert ein Produktionszyklus 20 bis 40 Minuten.
Iturrospe ist das einzige Unternehmen weltweit, das A-Frame-Doppelpressen fertigt. Zwar wurden in der Vergangenheit ähnliche Konzepte in Einzelbauweise umgesetzt, der große Nachteil dieser „selbst gebauten“ Pressen war jedoch die weitgehend fehlende Automatisierung. So wird beispielsweise der Mischkopf bei diesen Konzepten noch von Hand geführt. Nun können Kunden weltweit auf ein modernes und hoch automatisiertes Konzept von einem erfahrenen Pressenhersteller mit erstklassiger Dosiertechnik von Hennecke zurückgreifen.
Das Herzstück der ganzen Anlage ist die Hochdruck-Dosiermaschine vom Typ TOPLINE HK 1250 mit 500-Liter-Arbeitsbehältern. Sie stellt das reaktive PUR-Gemisch bereit und sorgt für die optimale Komponenten-Vermischung und eine präzise Austragsleistung. Obwohl die Presse eine außergewöhnliche Lösung ist, wird für die Dosierung eine Standard-Maschine mit Standard-Mischkopf vom Typ MXL eingesetzt. Durch den modularen Aufbau der Maschine ist der Anwender jederzeit in der Lage, flexibel auf Produktionsbedürfnisse zu reagieren und kann die Produktionskapazität und das Produktionsverfahren nach dem Plug-and-play-Prinzip anpassen. Dies gilt beispielsweise auch für eine problemlose spätere Erweiterung auf das umweltfreundliche Treibmittel Pentan. Bei der Entwicklung der Dosiermaschine hat Hennecke ebenfalls besondere Aufmerksamkeit auf die Anwenderfreundlichkeit gelegt. Bei der aktuellen Maschinengeneration hat das Unternehmen die Serienausstattung deutlich aufgewertet. Dadurch können Anwender eine Vielzahl von Anwendungsfällen ohne jegliche Kompromisse in Sachen Qualität abdecken. Ein echtes Multitalent für alle Fälle – eben auch für alle unkonventionellen Fälle.
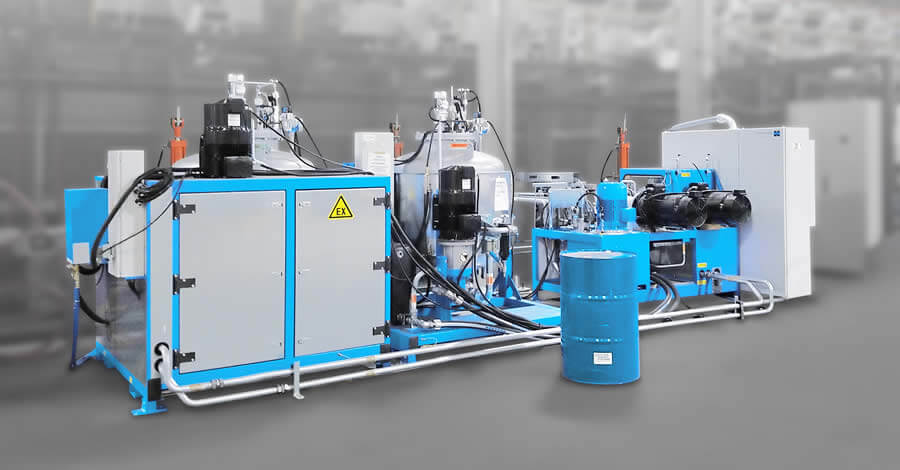
Download - Ausgabe 217 (PDF)
Zur Betrachtung benötigen Sie den Adobe® Reader®, den Sie hier kostenlos herunterladen können.