Turned on its head
Side walls for truck trailers in sandwich construction
Sandwich elements with a polyurethane core are tried and tested components which have countless applications, even outside of the construction industry. These panels are usually fabricated in a discontinuous manner and sealed in a press. However, the South American press specialist Iturrospe, headquartered in Rosario (Argentina), turns this methodology completely on its head. Iturrospe fabricates so-called A-frame presses, in which wall elements for truck trailers are produced upright by means of a "free-rising foam method". Hennecke provides the requisite PU know-how, as well as the wet part, in the form of a TOPLINE HK 1250.
When it comes to transporting temperature-sensitive products, box semi-trailers are used. The side walls, with dimensions of up to 17 m x 3 m, are produced as a sandwich construction. A polyurethane core, fabricated in different thicknesses to suit the particular application, achieves outstanding insulation values. The outer skin is produced from aluminium and the inside can consist of either aluminium, plastic or composite liner. The thickness of the PU foam inserted in between ranges from 38 mm up to 150 mm. The various box configurations are used for a range of applications, which encompass regular transport tasks through to refrigeration logistics.
While such large, flat parts are conventionally foamed lying horizontally on presses and then compressed, Iturrospe, with its A-frame double press, goes for an unconventional method: foaming with an upright press. The side parts stand upright and slightly inclined on the two legs. A huge advantage is that these presses require less space than conventional ones. This configuration also makes the extremely large parts more accessible and generally easier to handle. To guarantee optimum production capacity utilization, the curing time is used to prepare the next panel for the foaming process. The upright side wall is filled using the "free-rising foam method". During this process, the foam rises over the entire height of the side wall. During the foaming process, the press is open at the top. And so ultimately, the foam only uses its own weight as counter pressure. With conventional presses, closed moulds are always used in order to achieve a largely uniform density distribution. With A-Frame double presses, this important characteristic is ensured by means of specialised raw material systems.
In the new A-frame double press, the outside of the press can be moved backwards using spindle drives, and opened slightly with hydraulic cylinders. The upper third of this side of the press is divided up into further sections, which can also be opened and closed hydraulically.
This allows the mixhead to be lowered into the press. During production, the operator inserts the pre-prepared inner and outer sides into the press using a crane. The spindle drives move the outside of the press into the exact position for the desired wall thickness. During this process, the side of the press and its upper third section remain open. On the work platform at the top of the press there is a transport system, which drives the Hennecke mixhead using a servomotor, and which can move the submerged mixhead up and down throughout the entire upper third of the mould, in order to inject the reactive mixture into the side wall at up to three kg per second. The rate of travel of the mixhead depends on the required thickness of the sandwich element. Following the mixhead, the individual segments of the upper third of the side of the press close into place. Once the mixhead has reached the end of the section and been removed from the press, the entire outer wall closes. When the press is closed, locking pins are extended at the top of the press, mechanically locking the other side of the press and absorbing the pressure produced in the mould. One production cycle takes 20 to 40 minutes, depending on the design of the trailer wall.
Iturrospe is the only company in the world to fabricate A-frame double presses. Although similar concepts in single-piece construction have been realized in the past, the big drawback of these "self-built" presses was the widespread lack of automation. For example, these designs often still require the mixhead to be guided by hand. Now, customers worldwide can rely on a modern and highlyautomated concept from an experienced press manufacturer with first-class metering technology from Hennecke.
The core component of the plant as a whole is the TOPLINE HK 1250 high-pressure metering machine with 500 litre work tanks. These supply the reactive PU mixture, ensuring the optimal mixing of the components and a precise output. Although the press is an extraordinary solution, a standard machine with a standard MXL mixhead is used for metering. Due to the modular structure of the machine, the user is able to flexibly react to production requirements at all times and can adjust the production capacity and production process according to the plug-and-play principle. This is also important, for example, for subsequently expanding to the environment-friendly blowing agent pentane at a later time. During the development of the metering machine, Hennecke also paid particular attention to user-friendliness. With the latest generation of machines, the company has significantly upgraded the standard equipment. As a result, users can cover a wide range of applications without having to make any compromises whatsoever in terms of quality. A genuine all-rounder for all situations - even unconventional ones.
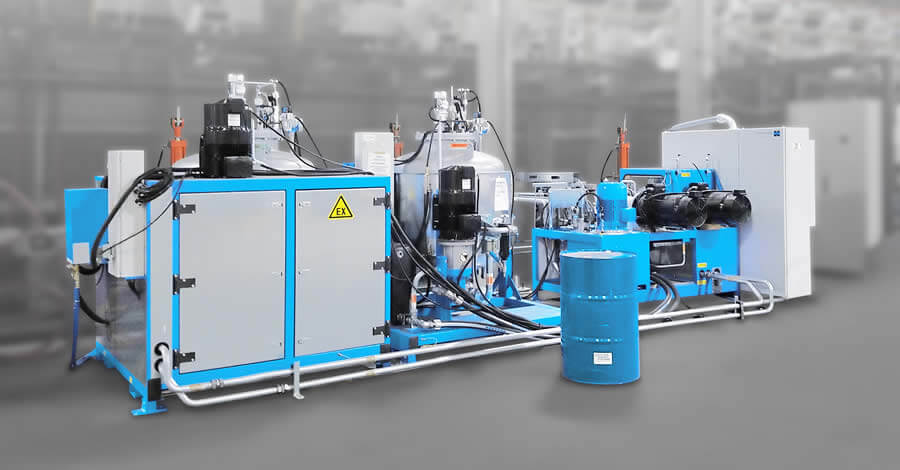