Vollautomatisch, nachbearbeitungsfrei und mit kurzer Zykluszeit
Herstellung thermoplastischer Faserverbundwerkstoffe im Spritzgusswerkzeug
Langfaserverstärkte Kunststoffbauteile mit anforderungsgerichteten Faserverbünden sind ein elementarer Bestandteil der Leichtbautechnologie. Die langen Zykluszeiten bei der Herstellung verhindern jedoch zurzeit die Großserienfertigung dieser Bauteile. Ein Demonstrator-Bauteil, welches nun in einer Spritzgießmaschine mit einem zweistufigen Verfahren hergestellt wurde, zeigt, dass es möglich ist, diese Bauteile vollautomatisch, reproduzierbar, nachbearbeitungsfrei und mit kurzer Zykluszeit herzustellen. Kern des Verfahrens ist eine Dosiermaschine, die ein Polyamid-6-System im Hochdruckprozess vermischt und ein Schiebetisch-Werkzeug mit einer Doppelkavität für den Faserverbundprozess sowie für den Spritzgussprozess.
Die Großserienverarbeitung von Faserverbundwerkstoffen mit Kurzfasern auf Spritzgießmaschinen ist ein etablierter Prozess. Um lang- und endlosfaserverstärkte, flächige Bauteile herzustellen, kommt bisher das Harzinjektionsverfahren Resin Transfer Moulding (RTM) zur Anwendung. Dabei werden ungetränkte Verstärkungsfasern in Form eines vorkonfektionierten und konturnahen Preforms in ein Werkzeug eingelegt. Die Fasern können dabei verwoben oder gerichtet sein. Nach dem Schließen des Werkzeugs wird es mit einem reaktiven Harzsystem geflutet. Nach dem Aushärten des Bauteils lässt sich dieses aus dem Werkzeug entnehmen. Die Zykluszeit dieses Verfahrens hat Hennecke durch die Entwicklung des Hochdruck-RTM-Verfahrens (HP-RTM) deutlich reduziert. Doch ein Nachteil blieb: Die so hergestellten Bauteile benötigen eine abschließende zerspanende Bearbeitung, um die Konturen herzustellen.
Da das Unternehmen als Matrixmaterial für das HP-RTM-Verfahren je nach Anwendung Polyurethan oder Epoxysysteme einsetzt, kann es nicht ohne Weiteres auf eine Spritzgießmaschine übertragen werden. Denn aufgrund der Schwindungs- und Adhäsionseigenschaften lassen sich diese beiden Matrixmaterialien dort nicht verwenden. Daher setzt das Unternehmen bei dem Insitu-Prozess stattdessen Caprolactam ein, da sich dieses Material sowohl reaktiv als auch thermoplastisch verarbeiten lässt. Beim Insitu-Spritzgießen findet das Imprägnieren der Faserverstärkung im Spritzgießwerkzeug statt. Die Verwendung von Caprolactam in Kombination mit einem Aktivator und einem Katalysator ermöglicht eine Polymerisation zu Polyamid 6 im Werkzeug. In dem zweiten Schritt erzeugt das gleiche Werkzeug in einem herkömmlichen thermoplastischen Spritzgießprozess mit Polyamid 6 die endgültige funktionalisierte Formgebung. Das Fasergelege innerhalb des Bauteils ist daher nur an den Stellen notwendig, wo es tatsächlich Kräfte aufnehmen muss.
Die für den Insitu-Prozess ausgelegte Spritzgießmaschine von ENGEL im Hennecke-Anwendungstechnikum „TECHCENTER“ verfügt über zwei Spritzaggregate. Eines ist die Hennecke-Dosiermaschine vom Typ STREAMLINE, das andere ein thermoplastisches Standardspritzguss-Aggregat für das Polyamid 6. Mit der Dosiermaschine bietet Hennecke ein Verarbeitungssystem für alle gängigen Matrixsysteme von Faserverbundbauteilen, wie Polyurethan- oder Epoxid Harz-/Härter- und eben wie in diesem Anwendungsfall auch Polyamid-6-Rohstoffsysteme an, das sich durch den modularen Aufbau an die jeweiligen Bedürfnisse der Produktion anpasst und sich so beispielsweise auch in eine automatisierte Fertigungslinie integrieren lässt.
Die Dosiermaschine verfügt ab Werk über eine Serienausstattung mit selbstreinigendem Hochdruck-Mischkopf und einer Touchscreen- Steuerung auf Basis einer Simatic SPS von Siemens. Durch die effiziente Temperierung für Behälter und Pumpe mittels Heißlufttechnik ermöglicht die Dosiermaschine eine effektive Komponenten-Temperierung und -Vermischung auch bei niedrigen Austragsleistungen. Eine Massedurchflussmessung für die Hauptkomponenten in der Dosiermaschine ermöglicht zudem eine dichteunabhängige Rezepturvorwahl und somit ein präzises Dosieren. Viskositätsschwankungen spielen keine Rolle, weil die kontinuierlich rezirkulierenden Hauptkomponenten homogen bis zu maximal 100 °C temperiert werden. Auch eine Vakuumeinheit ist in der Basisversion enthalten und verhindert Lufteinschlüsse bei der Medienlagerung im Tagesbehältnis. Eine Speisepumpe sichert die unterbrechungsfreie Versorgung des Hauptdosieraggregates – trotz Vakuum. Sämtliche Komponenten sind auf einem fahrbaren Gestell untergebracht, das eine kurzfristige Produktionsverlagerung oder einen flexiblen Betrieb im Technikumsumfeld ermöglicht.Das Hennecke-eigene Schiebetisch- Werkzeug für die Herstellung des Demonstrator-Bauteils besteht aus einer Doppelkavität für die Düsenseite und einer Single-Kavität für die Unterform. Das Werkzeug ist für den HP-RTM-Prozess druckstabil ausgelegt und konturnah variotherm beheizt. Das niedrigviskose Caprolactam stellt dabei besondere Anforderungen an die Dichtungen. Weitere Herausforderungen sind die unterschiedlichen Drücke und Temperaturen der beiden Verfahren.
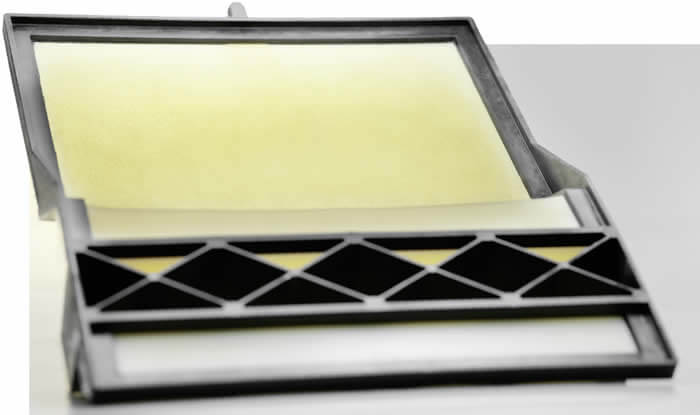
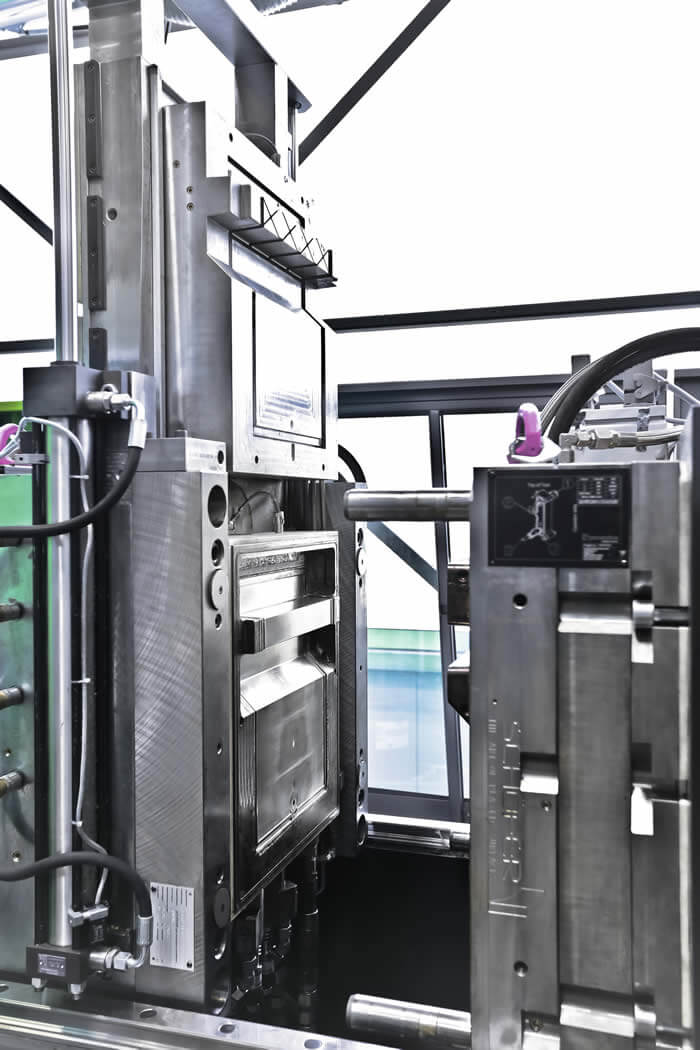
Um das Demonstrator-Bauteil herzustellen, werden in die Unterform zunächst die vorkonfektionierten Trockenfasern eingebracht. Das Werkzeug wird mit der Düsenseite für den HP-RTM-Prozess geschlossen. Im Vergleich zu einer Thermoplastschmelze weist Caprolactam eine geringere Viskosität auf und kann daher auch sehr feine Faserfilamente ohne Schädigung infiltrieren – ohne die Strukturen in der Form zu verschieben. Das Caprolactam reagiert im Werkzeug durch Insitu-Polymerisation zu thermoplastischem Polyamid 6. Das so entstandene Preform verbleibt in der Unterseite des Werkzeugs. Die Düsenseite der Form wird für den zweiten Schritt gewechselt. Nun erfolgt die letztendliche und formfallende Formgebung mithilfe des thermoplastischen Spritzgusses mit Polyamid 6.
Hennecke sieht in dieser Zusammenführung aus reaktivem System und der Großserientauglichkeit der thermoplastischen Welt einen erheblichen Mehrwert für die Anwender. Insbesondere weil das Zusammenspiel von anforderungsgerichtetem Faserverbund einerseits und Kostenoptimierung andererseits der Schlüssel für die Großserienproduktion mit kurzen Taktzeiten beim Trendthema Leichtbau ist. Die wesentlichen Vorteile des Verfahrens sind außerdem die Vielfalt der Verarbeitungsmöglichkeiten und der sehr große Freiheitsgrad bei der Gestaltung von Formteilen. Nun gilt es, die Rohstoffe und die Fasern weiter zu entwickeln, um das Verfahren weiter zu optimieren. Auch können noch nicht alle Faserarten mit dem Rohstoffsystem Caprolactam kombiniert werden.
Hennecke wird die Weiterentwicklung der Insitu-Technologie zusammen mit Anwendern weiter aktiv voran-treiben, um damit kurzfristig die Marktreife für diese vielversprechende Technologie zu erlangen.
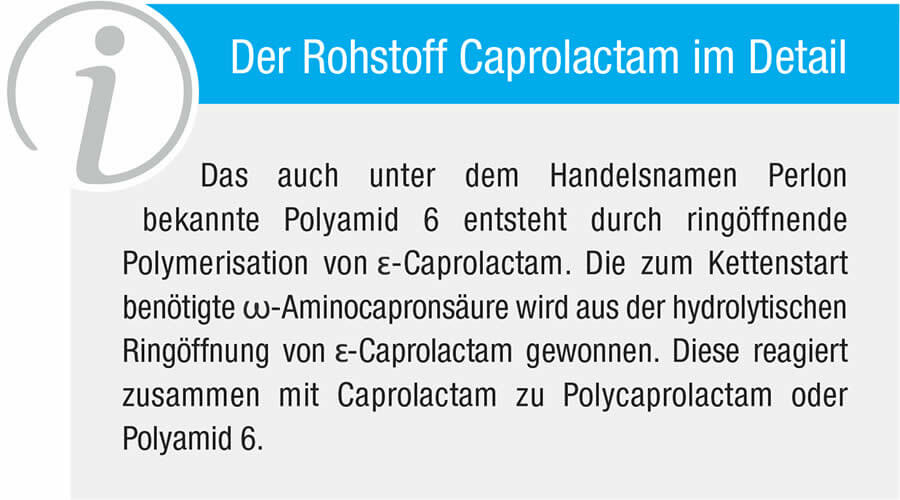
Download - Ausgabe 116 (PDF)
Zur Betrachtung benötigen Sie den Adobe® Reader®, den Sie hier kostenlos herunterladen können.