Fully automatic, with no requirement for post-processing and with short cycle times
Production of thermoplastic fibre composites in the injection mould
Long fibre-reinforced plastic parts with requirements-based fibre composites are an elementary component of lightweight construction technology. However, long cycle times in production currently prevent large-scale manufacture of these parts. A demonstrator component that has now been produced in an injection moulding machine using a two-stage process shows that it is possible to manufacture these components fully automatically, in a reproducible manner, with no requirement for post-processing and with short cycle times. The core of the process is a metering machine that mixes a polyamide 6 system in a high-pressure process and a push trolley mould with a dual cavity for the fibre composite process as well as for the injection moulding process.
The large-scale processing of fibre composite materials with short fibres on injection moulding machines is an established process. Up to now, the resin injection process Resin Transfer Moulding (RTM) has been used to produce long and endless fibre-reinforced flat components. Here, non-impregnated reinforcement fibres in the shape of a prefabricated and contouraligned preform are placed in a mould. The fibres can be interwoven or directional. After closing the mould, it is flooded with a reactive resin system. After the part has cured, it can be removed from the mould. Hennecke has considerably reduced the cycle time of this process by developing the high-pressure RTM process (HP-RTM). But a disadvantage remains: the components produced in this way require final machining to create the contours.
Since the company uses polyurethane or epoxy systems, depending on the application, as a matrix material for the HP-RTM process, it cannot be readily transferred to an injection moulding machine. Due to the shrinkage and adhesion properties, these two matrix materials cannot be used there. So instead, the company uses caprolactam with the in situ process, because this material can be both reactively and thermoplastically processed. With in situ injection moulding, impregnation of the fibre reinforcement takes place in the injection mould. The use of caprolactam in combination with an activator and a catalyst allows polymerisation into polyamide 6 in the mould. In the second step, the same mould creates the final functionalised shape in a conventional thermoplastic injection moulding process with polyamide 6. Fibre laying within the part is thus only necessary at those places where it must actually absorb forces.
The injection moulding machine from ENGEL, which is designed for the insitu process and installed in the Hennecke "TECHCENTER" application centre, has two injection units. One is the Hennecke metering machine of type STREAMLINE, the other is a thermoplastic standard injection moulding unit for the polyamide 6. With the metering machine, Hennecke offers a processing system for all common matrix systems of fibre composite components. These include polyurethane or epoxy resin / hardener systems and – as in this application – polyamide 6 raw material systems. The STREAMLINE adapts to the respective production requirements by its modular structure and can thus e.g. also be integrated into an automated production line. The metering machine comes with standard equipment including a self-cleaning high pressure mixhead and a touch-screen control based on a Simatic PLC from Siemens right from the factory. Thanks to the efficient temperature control system for tank and pump by means of hot air technology, the metering machine achieves effective component tempering and mixing even at low output rates. Mass flow measurement for the main components in the metering machine also allows density-independent formulation preselection and hence precise metering. Viscosity variations do not play a role as the continuously recirculated main components are kept at a homogeneous temperature of up to a maximum of 100°C. The basic machine configuration also includes a vacuum unit to prevent air inclusions from occurring when the components are stored in the day tank. A feed pump ensures uninterrupted supply to the main metering unit – in spite of the vacuum. All subassemblies are mounted on a mobile frame, thus enabling relocation on the production floor at short notice as well as a flexible operation in the technical centre at any time. The in-house Hennecke push trolley mould for production of the demonstrator component comprises a dual cavity for the injector side and a single cavity for the lower mould. The mould is designed to be pressure stable for the HP-RTM process and is contour-aligned with variotherm heating. Here, the low-viscosity caprolactam places particular requirements on the seals. Other challenges are the different pressures and temperatures of the two processes.
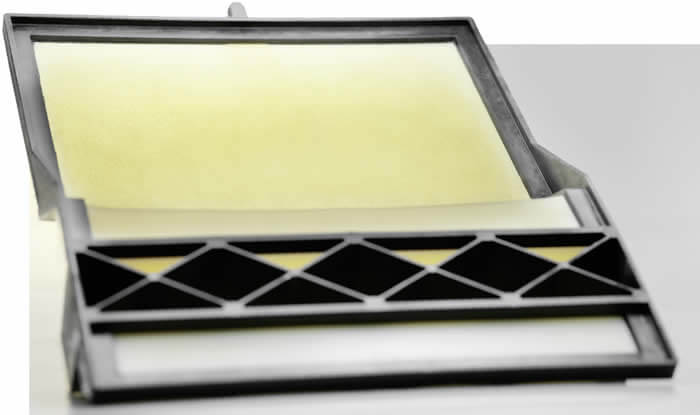
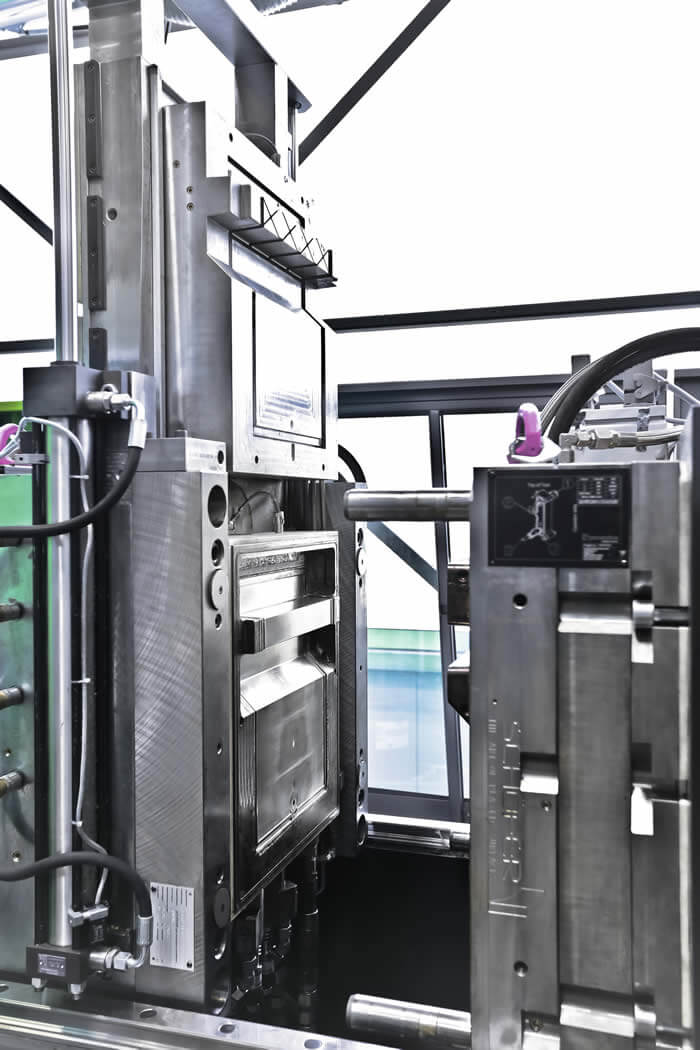
To produce the demonstrator component, firstly the pre-fabricated dry fibres are placed in the lower mould. The mould is closed with the injector side for the HP-RTM process. In comparison with a thermoplastic melt, caprolactam has lower viscosity and can therefore infiltrate even very fine fibre filaments without damage and without displacing the structures in the mould. The caprolactam reacts in the mould via in situ polymerisation to form thermoplastic polyamide 6. The resultant preform remains in the bottom side of the mould. The injector side of the mould is changed for the second step. Now the final and demoulding shaping takes place using thermoplastic injection moulding with polyamide 6.
In this combination of the reactive system and its suitability for largescale series production of the thermoplastic world, Hennecke sees considerable added value for the user. In particular, because the interplay between the requirements-based fibre composite on the one hand and cost optimisation on the other is the key to largescale series production with short cycle times in the trend topic of lightweight construction. The substantial advantages of the process are also the diversity of processing options and the very large degree of freedom in the design of moulded parts. We now need to further develop the raw materials and the fibres to optimise the process. In addition, not all fibre types can be combined with the raw material system caprolactam. Together with users, Hennecke will continue to actively advance the further development of in situ technology so that this promising technology will soon reach market maturity.
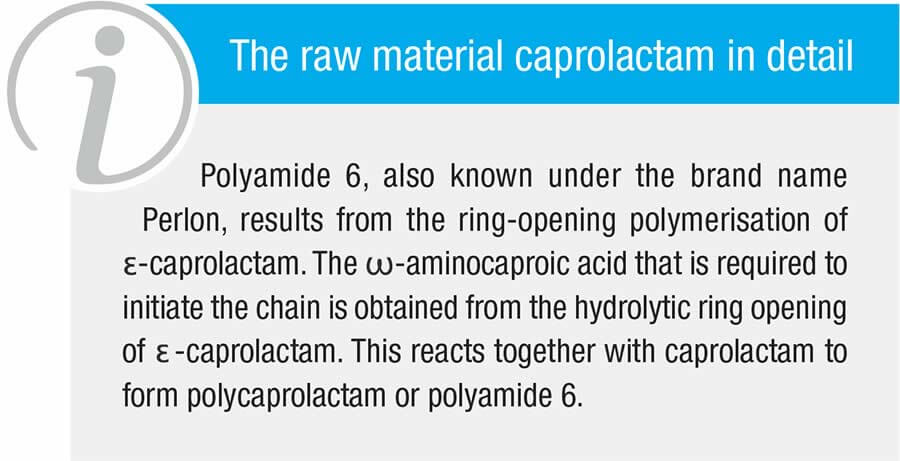