Weiterentwicklung der JFLEX:
Gutes noch besser gemacht
Mit der JFLEX hat Hennecke seine Produktfamilie kontinuierlicher Blockschaumanlagen erfolgreich erweitert und damit gleichzeitig eine Brücke zwischen diskontinuierlichen und kontinuierlichen Blockschaumanlagen geschlagen. Die JFLEX bietet Anwendern mit mittleren Produktionsvolumina sämtliche Vorteile einer kontinuierlichen Produktion. Seit der Vorstellung auf der K-Messe 2013 konnte Hennecke die JFLEX sehr erfolgreich am Markt platzieren. Die aktuelle Anlagen-Generation profitiert nun von verschiedenen Detailverbesserungen, die im Rahmen erweiterter Marktanforderungen sukzessiv integriert wurden.
Die positiven Reaktionen von Blockschaumverarbeitern rund um den Globus haben gezeigt, dass Hennecke mit der neuen JFLEX einen Volltreffer gelandet hat. Der Kapazitätsbereich zwischen der diskontinuierlichen und der kontinuierlichen Blockschaumanlage war bisher auf dem Markt noch nicht abgedeckt. Zielgruppe der JFLEX sind Schaumstoffhersteller, die eine bessere Qualität und eine höhere Rohstoff-Ausbeute erreichen wollen, als es mit diskontinuierlichen Anlagen möglich ist, aber nicht die hohe Investition in herkömmliche kontinuierliche Anlagen tätigen wollen. Die JFLEX bietet bei mittleren Produktionsvolumina sämtliche Vorteile einer kontinuierlichen Produktion.
JFLEX-Anlagen produzieren mit einem Fünftel der üblichen Produktionsgeschwindigkeit herkömmlicher kontinuierlicher Anlagen – und das bei vergleichbarer Blockgröße. Die Maschine ist dadurch nur etwa zwölf Meter lang. Diese extrem kompakte Bauweise stellt einen erheblichen Vorteil dar, denn herkömmliche Blockschaumanlagen sind mit bis zu 50 Metern mehr als viermal so lang. Durch den geringen Platzbedarf spart der Anwender kostbare Produktionsfläche oder kann die Gebäudekosten spürbar reduzieren. Den Längenunterschied ermöglicht Hennecke durch eine neue Gemisch-Austrags-Technologie. Bei herkömmlichen, kontinuierlich produzierenden Blockschaumanlagen bestimmt die Expansionsgeschwindigkeit des Polyurethan-Gemischs die Produktionsgeschwindigkeit. üblicherweise liegt diese bei etwa fünf Metern pro Minute. Die vorgegebene Geschwindigkeit bestimmt damit auch die Länge der gesamten Anlage, da der Schaumstoff in einem definierten Zeitraum ausreifen muss, bevor er geschnitten werden kann.
Die PUR-Spezialisten von Hennecke haben ein – zum Patent angemeldetes – Verfahren entwickelt, mit dem es möglich ist, eine Produktionsgeschwindigkeit von nur einem Meter pro Minute zu fahren und damit die Anlagenlänge entsprechend zu verkürzen. Hauptbestandteil der neuen Technologie ist die Eintragszone der JFLEX: die sogenannte J-PIPE. In dieser wird das flüssige Gemisch auf der einen Seite mithilfe eines Austragsorgans eingebracht. Das expandierende Polyurethan tritt auf der anderen Seite aus, ohne dass es in die Flüssigkeit zurückdrücken kann und expandiert dabei entlang einer Steigplatte. Das System macht sich hierbei den Dichteunterschied von reaktiver Flüssigkeit auf der einen und dem leichteren Schaum auf der anderen Seite zunutze.
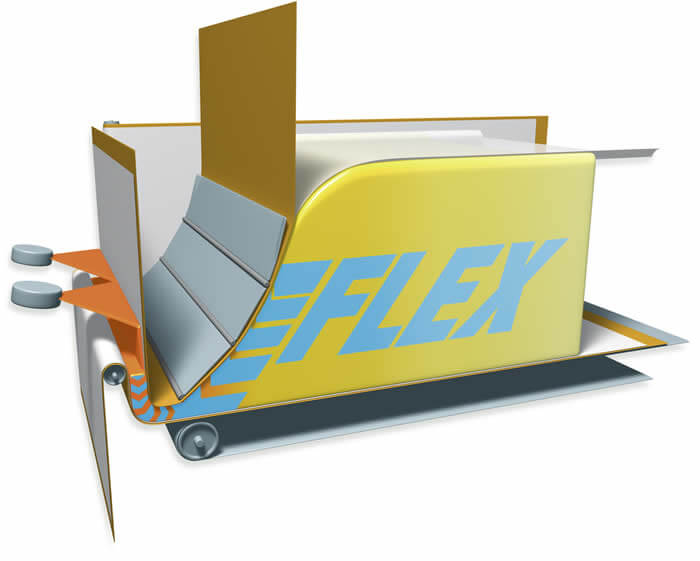
Diesen JFLEX-Prozess haben die Hennecke-Spezialisten durch die gewonnen Erfahrungen im Produktionsalltag weiter optimiert. Mit dem weiterentwickelten Verteildüsen-System „Multiple-Nozzle-System“ lassen sich nun sehr flexibel verschiedene Schäumbreiten im Bereich von 1000 bis 2300 Millimeter realisieren. Die Rohstoff-Verteilung kann der Anwender über die Durchmesser der Austragsdüsen sowie die Entfernung und Positionierung des Austragsorgans vom Papier dabei wesentlich besser beeinflussen als bisher. Dabei wird gewährleistet, dass das Gemisch an jeder Stelle über die Breitenverteilung das gleiche Alter besitzt. Das Austragsorgan der JFLEX beweist seine Fähigkeiten mittlerweile auch in weiteren PUR-Anwendungen, bei denen ein einheitliches Steigprofil des Schaumes im Fokus steht.
Die zweite Optimierung des JFLEX-Prozesses fand im Bereich der Steigplatte statt. Durch die Unterteilung in drei Segmente statt eines starren Elements lässt sich die Geometrie besser an die Schaumkurve anpassen. Zusätzlich ist diese Geometrie jetzt motorisch während des Schäumens einstellbar. Auch eine automatische Einstellung über die Steuerung der Anlage in Abhängigkeit von der Rezeptur ist möglich.
Aber nicht nur im Bereich des JFLEX-Prozesses hat Hennecke die Anlage weiter perfektioniert. Auch die Funktion und die technische Auslegung der Rechteck-Blockeinrichtung wurden optimiert. Durch eine bessere Blockgeometrie erhöht sich somit nochmals die Rohstoff-Effizienz. Dabei sind die Häute des Blocks sehr dünn und tragen so dazu bei, die Schnittverluste zu minimieren. Die Rüstzeiten haben die Hennecke-Techniker ebenfalls unter die Lupe genommen und konnten sie weiter reduzieren. Beispielsweise wird das Seitenpapier nach der Produktion nicht mehr entfernt, sondern verbleibt im Tunnel und ist damit wieder bereit für die nächste Produktion. Im Produktionsbetrieb hat sich auch gezeigt, dass bei der JFLEX bereits nach sieben Metern Produktion der fertige Schaum den Tunnel verlässt und dann vom Operator sofort begutachtet werden kann. Notwendige Rezepturanpassungen können somit ohne nennenswerte Materialverluste erreicht werden. Konventionelle Anlagen produzieren in diesem Zeitraum bereits mehr als 20 Meter. Mit diesen Optimierungen und neuen Erfahrungen ist die JFLEX weiter gereift und kann zuverlässig in der Blockschaumproduktion eingesetzt werden. Damit reiht sich der neue Anlagentyp nahtlos in die Hennecke-Blockschaumanlagen vom Typ QFM und MULTIFLEX ein. Die bewährten Anlagen genießen als Spitzenreiter im Bereich der Blockschaumproduktion weltweit eine hervorragende Reputation.
Typisches Produktionsspektrum der JFLEX
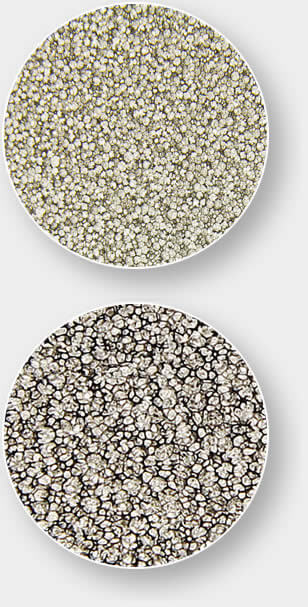
- Standardschaum mit einer Dichte von 15 bis 45 kg/m³
- Einsatz von Füllstoffen mit bis zu 50 Teilen auf 100 Teile Polyol
- Mögliche Zellgrößen von circa 25 bis 50 ppi
Durch eine zusätzliche Hochdruck-Isocyanat-Begasung mit Stickstoff kann eine noch feinere Zellstruktur erreicht werden. Ebenso ist eine noch gröbere Zellstruktur durch Entgasung von Isocyanat möglich.
- Viskoelastischer Schaum auf MDI-Basis und einer Dichte von 50 bis 100 kg/m³
- HR-Schaum mit einer Dichte von 25 bis 50 kg/m³
Beispielhafte Dichte- und Härteverteilung (Standardschaum)
Typische Dichteverteilung
(Standardschaum ohne Füllstoffe, 22 kg/m³)
Typische Härteverteilung
(40 % Compression Set)
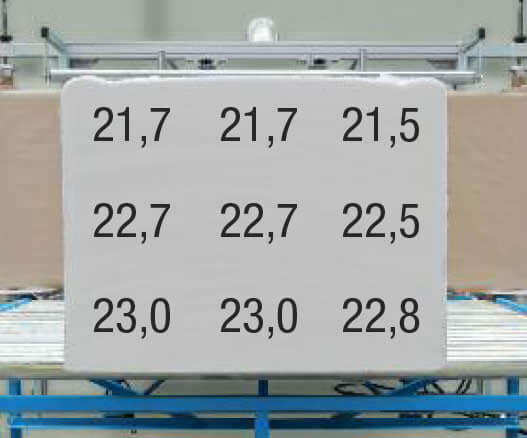
In kg/m3
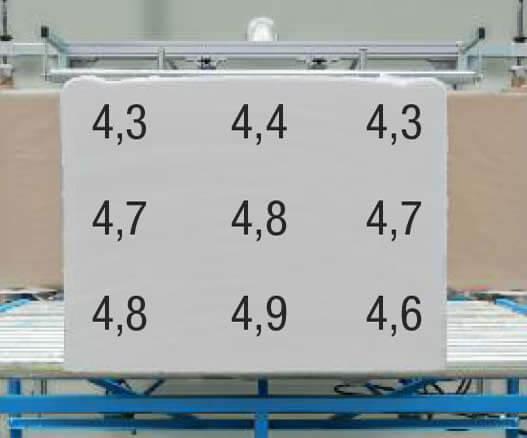
In kPa
Download - Ausgabe 115 (PDF)
Zur Betrachtung benötigen Sie den Adobe® Reader®, den Sie hier kostenlos herunterladen können.