Comprehensive production solutions for Asian customers:
Open House Event for sandwich panel plant technology at Hennecke Machinery Shanghai
The growth rates in China and the entire Asian region are still unbroken in the polyurethane processing sector. The Hennecke group underlines the significance of the steadily growing market with the consistent expansion of the Chinese subsidiary Hennecke Machinery Shanghai (HMS). Local branch representatives were just now able to see the comprehensive performance portfolio in the continuous sandwich panel unit sector for themselves in the framework of an open house event.
Hennecke understood the significance of the Asian market and the Chinese market in particular early on and has been represented with a sales and service location in China since the opening of the market itself. Since the founding of HMS, the production capacities have been successively expanded along with the targeted extension of the engineering and after-sales portfolio. Just recently, the Chinese Hennecke subsidiary was able to double its production area with the inauguration of a new production hall. This is a great competitive advantage in particular in the manufacture and sales of large production lines, because in addition to optimised customer service in all project phases, logistics is also significantly facilitated. In particular in the area of continuous sandwich panel lines of the CONTIMAT series, the Hennecke group is able to offer a comprehensive full system competence in the form of complete production lines - from raw material storage to roll forming machines and packaging installations. HMS answers the unwavering demand for this plant type in the Asian region with an Open House event, which attracted more than 50 customers from China, Singapore, Japan and Korea to the production site in Shanghai in September 2015. The HMS CONTIMAT team proved their technical know-how to the participants in specialised lectures. Along with a general introduction of the company by CEO Andrew Chan, the presentations focused on the comprehensive product portfolio and the far-reaching measures of quality assurance at the Shanghai location, among other things. In addition, Andreas Fischer (head of sales sandwich panel lines, Hennecke GmbH) and Wolfgang Inhof (sales director sandwich panel lines, Hennecke GmbH) were able to present advanced developments in the discharge system as well as Hennecke's competence in profiling metal facings.
In the subsequent visit to the production hall, the HMS representatives presented a CONTIMAT double plate conveyor including foam portal and saw, as well as a complete plant outlet in the form of a cooling section and stacking, and packaging from local production to the interested participants. All the system components convinced the attending experts with their high production quality, because Hennecke makes no compromises on quality in growth markets either. The advanced production capacities were another focus point of the event. The new production hall, whose foundation and cranes are specifically designed for heavy loads as they are needed in CONTIMAT production, shows just how serious HMS is about advancing the market penetration of the CONTIMAT system technology.
The conclusion of the event is positive in every way. All of the visitors were enthusiastic about the quality and performance capability. HMS was able to step up customer contact significantly and the next order conclusion with a large-scale customer from China is pending. Similarly to successful projects in the past, the comprehensive performance portfolio and the well-founded after-sales support of HMS is the centre of this decision to purchase
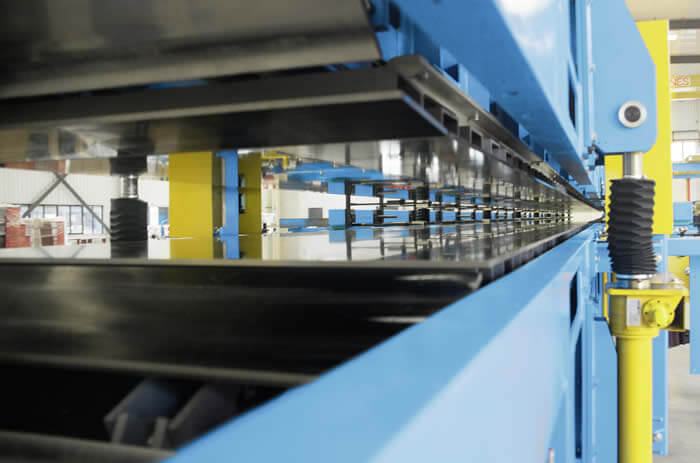
Hennecke Machinery Shanghai – Service and customer vicinity in China
What started in 1994 in Shanghai as a modest agency for different sales activities is one of the most important Hennecke subsidiaries today. After consistent growth, the first activities in production and assembly of Hennecke products commenced in 2005. Today, HMS is able to offer comprehensive solutions, consisting of consulting services, engineering, production and a complete after-sales portfolio to all Chinese customers. In the process, the Hennecke subsidiary acts locally and is therefore able to provide the services as efficiently and cost-effectively as possible. Further tasks of the Hennecke subsidiary include the sales of the entire Hennecke product range as well as a number of marketing activities to increase the awareness of machine and plant technology in Asia. The experienced team around CEO Andrew Chan also takes care of proper final assembly and start-up on customer location, covering everything from metering machines to comprehensive large-scale plants for the automotive, construction or refrigeration industry.
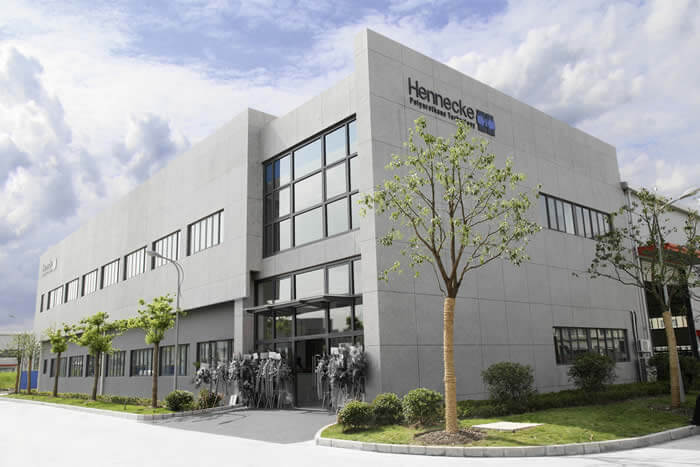
NEW DISCHARGE SYSTEM FOR CONTINUOUS SANDWICH PANEL UNITS
The quality of continuously manufactured sandwich elements is above all determined by the mechanical and isolating properties of the PU hard foam. The focus is on the way the liquid raw material mixture is applied between the cover layers. What is needed here is an ideal interaction of an even distribution over the entire foam width with simultaneously starting foam reaction. Conventional discharge systems use several mixing heads to achieve these two properties. Now, a revolutionary discharge system is enabling a decisive improvement and bringing the desired ideal in this interaction a significant step closer. Extensive flow simulations were used during the construction of the first prototype. The first real experiments were then conducted in Hennecke's own testing facility and served as a basis for the continuous further development towards a practical system. After further optimisations and tests under real production conditions, also regarding simple handling, cleaning and reusability among other things, the new discharge system has now reached market maturity. The aim is to introduce the system for a broad selection of successive applications on the market as early as next year. In this way Hennecke is again proving its abundant professional expertise in the production of sandwich elements with PU cores.
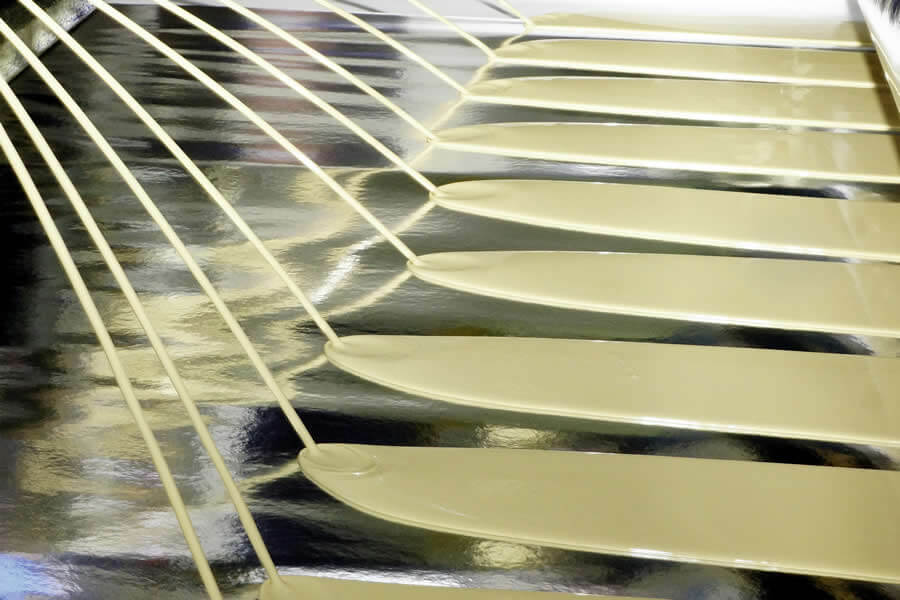