Efficiency in combination –
a CSM hybrid system for Otto Bock
With its motto “Best in Foam”, Otto Bock Kunststoff GmbH underlines its competence in manufacturing state-of-the-art PU foams for all areas of application. According to the globally-operating medium-sized firm, its constant principle is to spend on research and development and on new technologies. The decision to invest in a modern and extremely flexible CSM hybrid system for developing raw materials in spray skin and flexible foam applications certainly fits the general picture.
To always conduct research into new possibilities. That was and is Otto Bock Group’s key philosophy. It goes back to 1953 when the search was for a suitable material that could act as an alternative to the poplar wood used in orthopaedic prosthetics. Dr Max Näder, Otto Bock’s son-in-law, recognised the vast potential of plastics and laid the cornerstone for Otto Bock Kunststoff GmbH. Today, the company is one of the most important technology partners for the renowned firm Otto Bock HealthCare and for successful developers and suppliers of PU-based plastics. It is no wonder, then, that the cooperation with Hennecke goes back a long way. The machine manufacturer supplied one of the first continuous slabstock lines for producing ether and ester foams shortly after it had been founded in the 1950s. After 30 years of successful production, the machine was replaced by a considerably larger “UBT” plant, which in 2000 was supplemented with another state-of-the-art slabstock line. Further international projects followed in the area of continuous slabstock manufacture and the production of polyurethane gel.
The two polyurethane specialists’ most recent project is less about manufacturing than about product research and further development. The aim is to find a way of manufacturing spray skins in a flawless and reproducible manner using various Otto Bock raw material systems. The traditional company also wants to test and optimise its in-house raw material systems in the area of moulded foam applications. By using a tailor-made CSM hybrid system, Hennecke can cope with the different requirements in an extremely efficient way. The state-of- the-art laboratory plant is used in the on-site training center and has separate metering lines for spray skin and moulded foam applications, which can also be utilised in combination for certain processes.
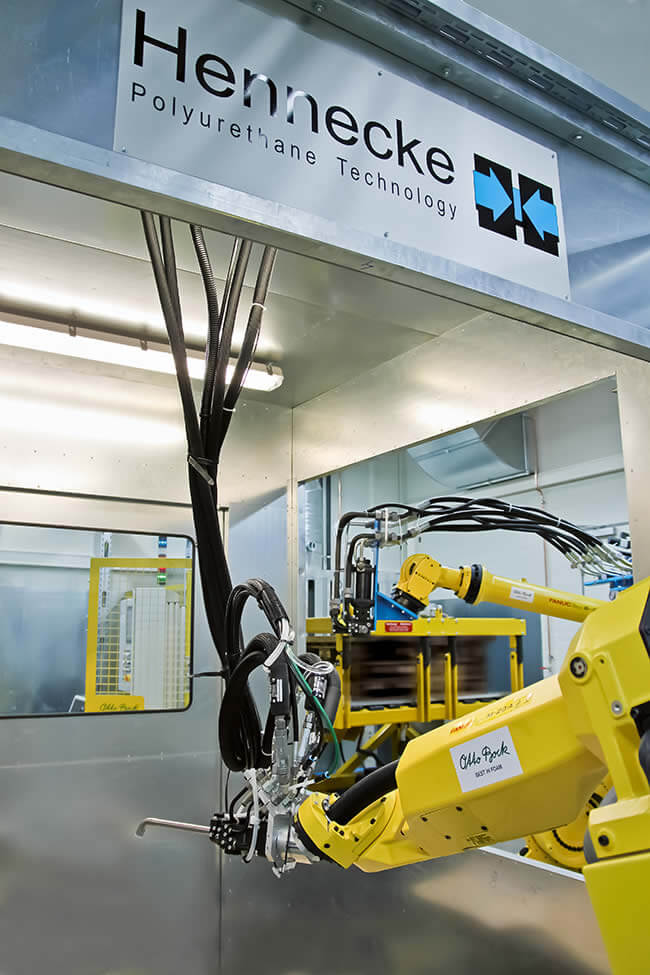
A TOPLINE HK 650 with 60-litre work tanks is used for manufacturing flexible foams. Combined with the latest design of MT 18 mixheads, all common foam systems can be processed without any difficulty. In conjunction with a big-sized industrial robot, the mixhead is mainly used on an automatic mould carrier that is similar in type and design to a Hennecke WKH system for producing car seats. In this way, real production conditions can be exactly simulated. Apart from the fully-automated operation on the mould carrier, the metering line can also be used manually and is available as a stand-alone system for countless laboratory applications. When processing polyurethane spray skins, the observance of all process parameters is as important for the application as the maintenance of a homogeneous surface distribution. The PUR-CSM metering line relies on a MICROLINE 45 CSM metering machine that is equipped with typical laboratory, small-volume tanks so that the components can be switched rapidly. The metering line is ideally suited for the use of different raw material systems, including high-viscosity components as are needed for the production of tear- resistant and heavy-duty spray skins. The MICROLINE also has a specially- fitted temperature control system for high processing temperatures. The MN6 CSM mixhead, equipped with a spray lance and a suitable industrial robot, ensures the optimal mixing of components and injection into the mould. An automated turntable rounds off the design, allowing the mould to be positioned correctly.
The turntable has a further function: Thanks to the possibility of switching positions between the injection robots, the device is literally the pivotal element of the flexible foam and spray skin line. Thus, the laboratory plant can be used to produce back-foamed spray skins, for example. This offers the user real added value, as the Technical Director of Otto Bock Kunststoff GmbH, Dr Marc Herrmann confirms: “The multifunctional CSM technology convinced us right in Hennecke’s spray center. For Otto Bock, the new laboratory plant is an ideal solution with a far-reaching range of applications.“ Those responsible at Hennecke are also convinced by the CSM system’s hybrid design, as Jens Winiarz, the Sales Manager in charge, says: “It is clear that Hennecke is in a position to offer tailor-made laboratory systems for developing demanding and advanced raw material systems. A nice side effect is surely that a long story of trusting cooperation will be continued with success.”
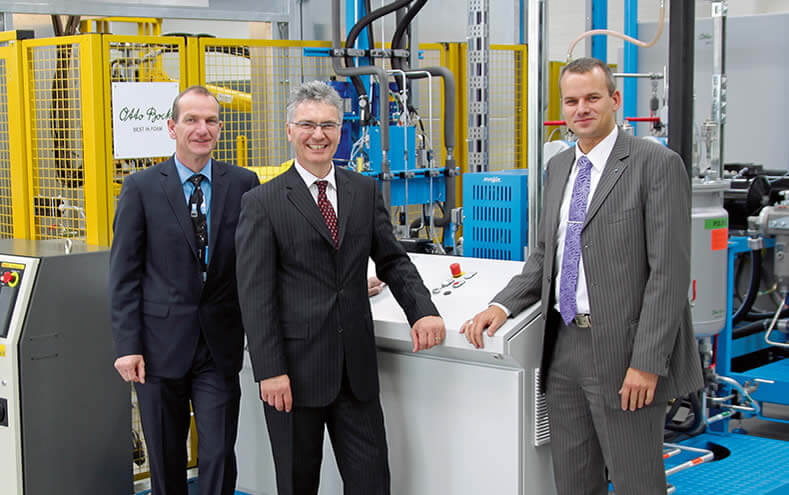