The one-stop solution PANELMASTER STEEL
Economically sustainable production of steel sandwich panels
With more than 150 sandwich panel lines installed worldwide, Hennecke-OMS is a leading supplier in the industry and is known for its innovative strength and reliability. The state-of-the-art PANELMASTER STEEL systems have been established for years in the highly efficient production of steel sandwich panels. These are particularly valued in industrial and cold storage construction due to their excellent insulating properties and durability. The system technology has now been further developed in many areas in order to meet the increasing demands of the market even better.
The Group‘s internal efforts in the run-up to the extensive update go much further than customers would initially expect. Targeted investments in the Hennecke GROUP‘s Sandwich Panel Excellence Center, which is also the headquarters of Hennecke-OMS near Milan, and intensive cooperation with the Hennecke GROUP‘s business units in Germany and China have enabled decisive progress to be made in recent months. This progress not only increases plant performance, but also local production capacities and internal efficiency considerably.
Turnkey solution in the sandwich panel market
What sets Hennecke-OMS apart from other manufacturers is its consistent approach of offering complete turnkey solutions. This means that customers receive a plant system that integrates and coordinates all production steps – from material preparation to the packaging of the finished sandwich panels. PANELMASTER STEEL systems thus form the basis for efficient and highly automated production, in which all the equipment and systems involved are optimally synchronized both mechanically and in terms of automation. In addition, turnkey solutions significantly reduce complexity for the manufacturer and enable a central point of contact for all technical matters. Such a comprehensive production solution is made possible by the bundled know-how within the Hennecke GROUP, whereby the locations in Germany, China and the Excellence Center in Italy each specialize in different core areas of the overall plant. “The close integration between the specialists involved around the globe and within the Excellence Center here in Italy enables us to develop and manufacture the core components of our systems ourselves. This not only gives us full control over quality, but also the flexibility to react quickly to our customers‘ requirements,” emphasizes Andrea Mariani, President of the Business Unit Italy. This approach not only offers a competitive advantage, but also ensures greater independence from external suppliers and significantly speeds up processes once an order has been placed.
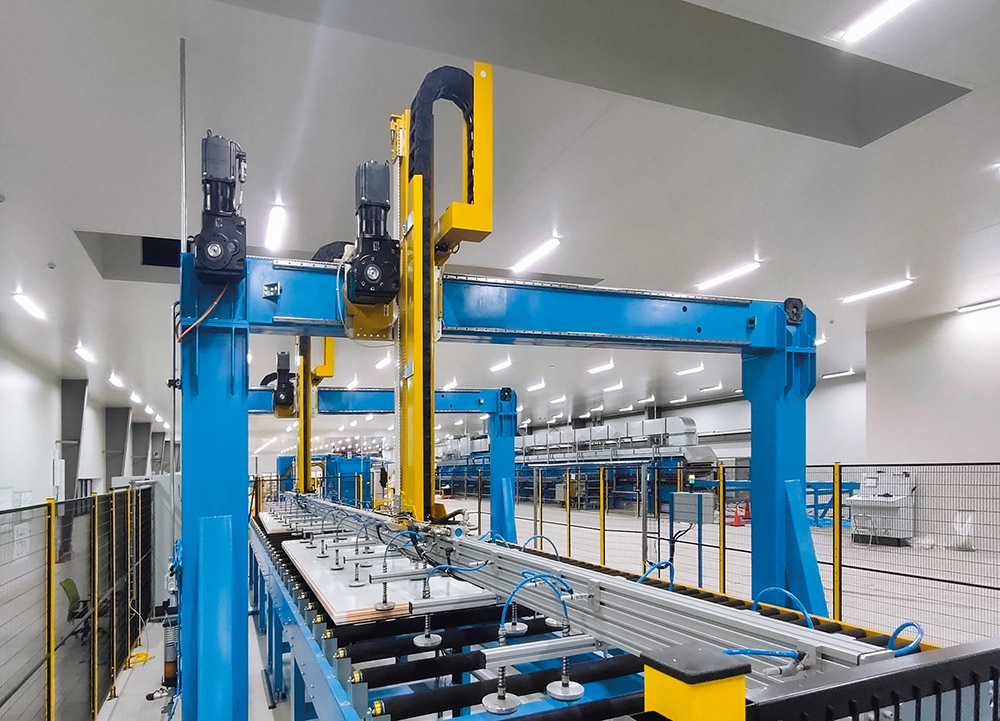
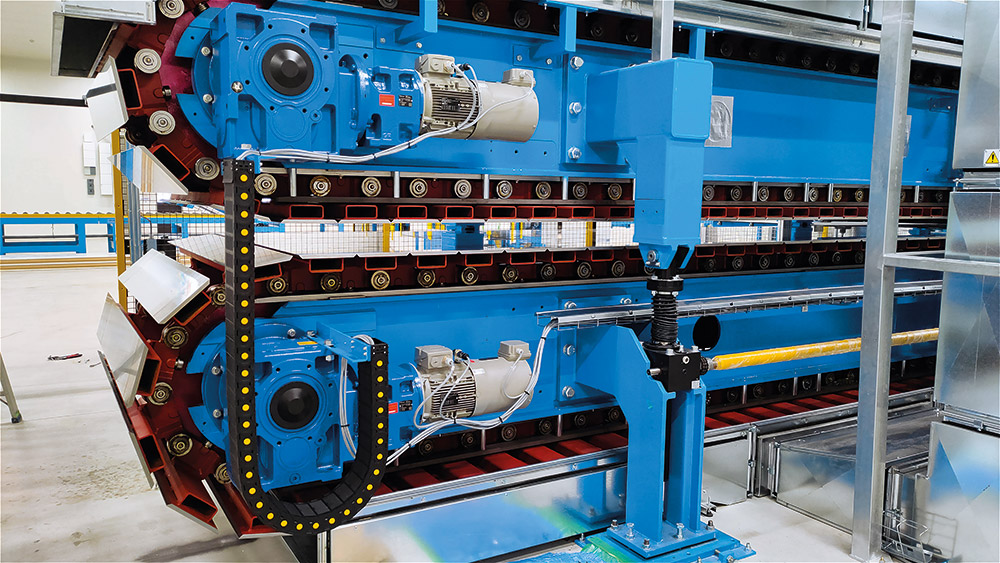
Own task force and far-reaching investments at Hennecke-OMS
As part of the continuous development and optimization of production capacities, the Hennecke Production System (HPS) was successfully implemented at the Hennecke-OMS site: As part of the “Hennecke 2.0” transformation, this involved expanding the production area by a whole 1000 m² and introducing new automated logistics processes. These measures led to a significant increase in efficiency of up to 20 percent and considerably improved the material flow within production. In addition, a dedicated task force was set up. The team consists of experienced experts from all Hennecke GROUP departments involved and coordinates the internal processes within the global group of companies. The task force also ensures that all departments work together efficiently in order to achieve the goals that have been set. Andrea Mariani explains: “As a company, we have invested a lot of time, effort and money to redesign decisive production areas and become more efficient and competitive. We are focusing on strict TCO (Total Cost of Ownership) measures in order to offer our customers lasting added value. The HPS formed the basis for this process and enabled significant efficiency gains and cost reductions.”
“The close integration between the specialists involved around the globe and within the Excellence Center here in Italy enables us to develop and manufacture the core components of our systems ourselves.”
Andrea Mariani,
President of the Business Unit Italy
Technical excellence down to the last detail
The advantages of establishing the HPS and the significantly optimized cooperation of all specialists involved in the sandwich panel product area formed the basis for a fundamental revision of the design of the entire PANELMASTER STEEL line and cover several key areas that are crucial for the highly efficient production of a wide range of sandwich panels with rigid facings. Among other things, the system is characterized by hands-free coil operation, which makes handling much easier and safer. Mixing and metering is carried out by a self-cleaning mixhead with a patented recirculation system, which ensures consistent raw material savings. The double belt conveyor relies on highly flat belt plates from in-house production and a new efficient heating system, which reduces energy consumption. In the outfeed section, vacuum grippers and other protective systems enable maximum gentle handling of the panels. The modernized system control offers flexible batch composition and comprehensive production analyses that improve traceability and ensure quality. Thanks to various internal preliminary tests, commissioning at the customer‘s premises has also been optimized.
Individually adaptable
The modular design of all sections within the PANELMASTER STEEL production line enables Hennecke-OMS to adapt the plant flexibly to a wide range of customer requirements. Whether it is a question of increasing production capacity, specific product specifications or reducing operating costs – PANELMASTER STEEL systems offer solutions for a wide range of challenges. With the optimizations at the site in Italy and the numerous further developments in the field of steel sandwich plant technology, Hennecke-OMS has shown that it continues to set the pace in the market for sandwich panel lines. The combination of technical precision, harmonized automation throughout and fully integrated production makes PANELMASTER STEEL one of the most advanced production solutions on the market. Thanks to the successful implementation of the measures and the resulting increase in efficiency, Hennecke-OMS is not only able to meet the increasing demands of customers, but also to offer future-oriented solutions for the construction industry.