Efficiency and flexibility
How Aadi polymers is expanding its market position through retrofit measures
Aadi Polymers Pvt. Ltd, a leading manufacturer of flexible foams in India, has been relying on innovative technologies and customized retrofit solutions for years to keep its slabstock foam production facilities up to date. These continuous modernizations not only ensure the highest product quality, but also enable Aadi Polymers to react flexibly to changing market requirements. Retrofit measures ensure optimum utilization of the plant technology over its entire service life and make a significant contribution to the sustainability and efficiency of production.
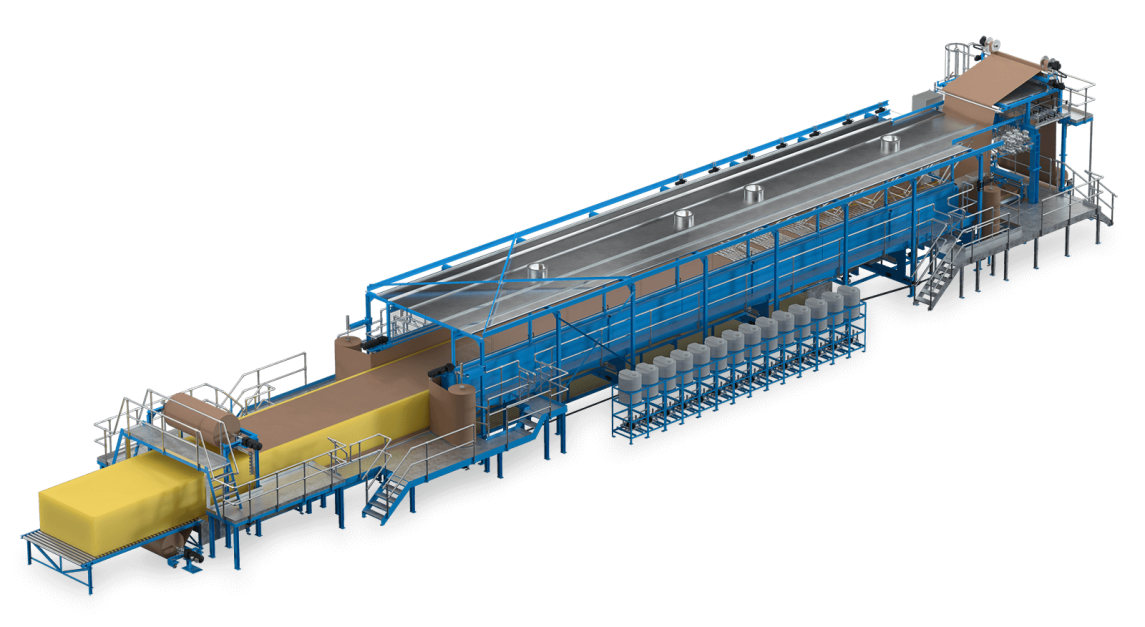
Since its foundation in 2009, Aadi Polymers Pvt. Ltd. based in Greater Noida near New Delhi, has established itself as one of the leading manufacturers of foams in India. The product range includes foams for various industrial applications, especially for the furniture and bedding industry. An in-house laboratory ensures that the quality of the products is continuously checked and further developed. New foam types and densities are developed here to meet the individual requirements of customers.
Strategic investments for the highest quality
In 2015, Aadi Polymers decided to relocate from Sikandrabad to Greater Noida to create more space for expansion. This move was accompanied by significant investments in advanced technology, including a MULTIFLEX production line. “Henneckes high-pressure systems are the first choice for continuous slabstock production and provide me, and therefore my customers, with reliable, consistently high quality. They are also known for their durability and long service life,” says Lokesh Jain, Director Aadi Polymers Private Limited. This investment underlines the company‘s commitment to producing the highest quality – and it has quickly paid off: “The investment in this Hennecke plant has dramatically increased our turnover and production capacity and has allowed us to grow in ways we could not have imagined before. I think the increase in our company‘s efficiency and production level clearly shows whether the investment has paid off or not,” explains the Managing Director.
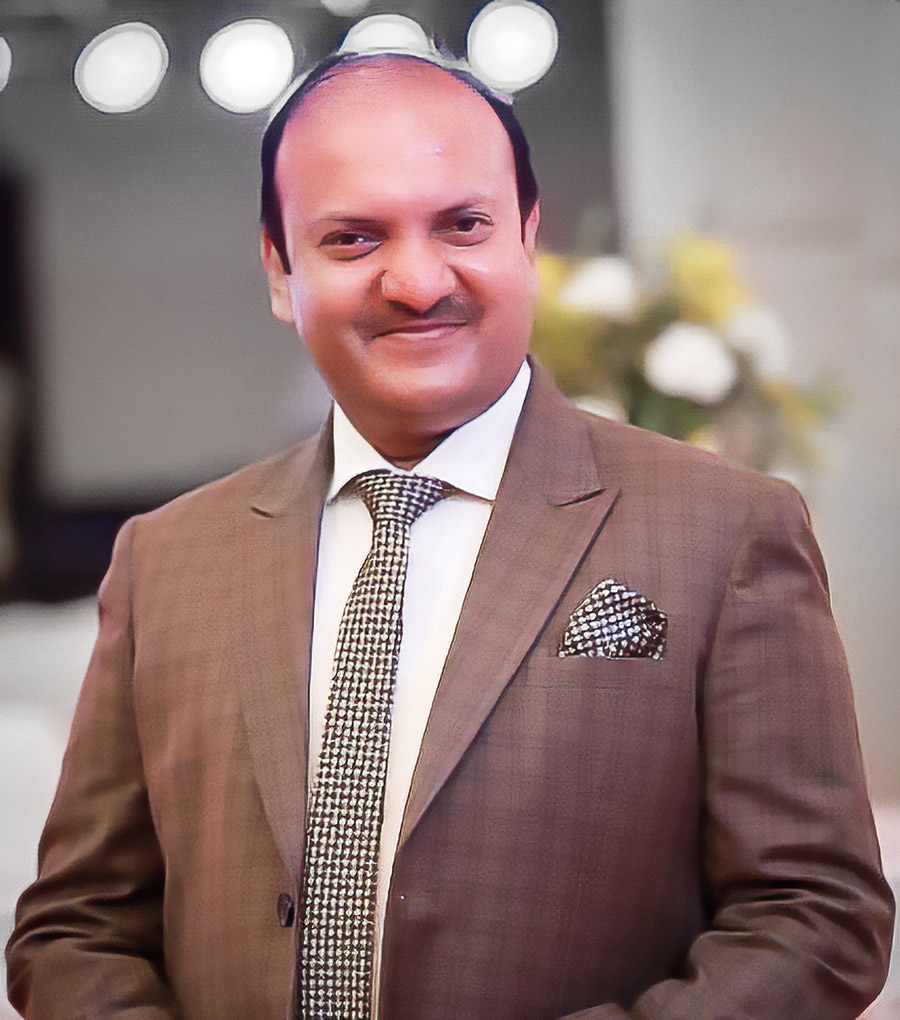
“Henneckes high-pressure systems are the first choice for continuous slabstock production and provide me, and therefore my customers, with reliable, consistently high quality.”
Lokesh Jain,
Director Aadi Polymers Private Limited
Retrofit measures for future-proof plants
Close contact with the Hennecke service team is another success factor for Aadi Polymers. The employees of Hennecke‘s 360°Service accompany the company throughout the entire service life of the machines and provide support in adapting to changing market requirements. This enables Aadi Polymers to adapt its production facilities to new challenges in a targeted manner. Back in 2016, the Managing Director of Aadi Polymers decided on the first of several retrofit measures. First, a block height measuring system was installed. This system uses sensors and lasers to reliably measure the block height and makes a significant contribution to consistent product quality. “The systems can be flexibly adapted to the respective production requirements and are therefore suitable for a wide range of applications. They can also be subsequently optimized through various retrofit measures, so that we retain a high degree of flexibility,” says Lokesh Jain.
Control system upgrade with FOAMWARE
The system received a comprehensive upgrade in 2022 when the control system was upgraded to the modern FOAMWARE. Not only the software was replaced, but also the hardware: the free-standing control panel with a SIMATIC quad-core industrial PC of the latest generation and a 32-inch UHD monitor enables ergonomic working and a good overview of all process parameters at all times. The intuitive FOAMWARE control software combines numerous functions with a user-friendly interface. “The software makes it easier for operators to manage and control production processes without extensive training. It can also be adapted to specific production requirements, which allows us to tailor the software precisely to our own processes and needs.” The clear display of all relevant production data, the extensive calibration modules, the tank level control and the ‘Magic Eye’ function, which immediately detects and visualizes metering deviations and irregularities in the running process, were particularly impressive.
Retrofitting: A solution for the future
The market is constantly placing new demands on manufacturers who have to respond to them. Hennecke offers customized retrofit solutions to keep production plants up to date with the latest technology. In addition, plants can always be adapted to changing market requirements, allowing companies to react flexibly. Retrofitting with an additional metering line, for example, opens up the possibility of expanding the product portfolio at a later date and tapping into new target groups. Ordering, installation and commissioning are carried out in close coordination with Hennecke‘s local sales and service teams. This enables manufacturers to operate older systems economically and sustainably, while at the same time benefiting from new innovations and technical advances. Retrofitting is an ideal solution for ensuring that systems that are characterized by a long service life are always optimally utilized. Both hardware and software upgrades play an important role here. The replacement of individual components and the integration of new technologies help to keep production efficient, safe and sustainable.
Long-term partnerships for optimal results
Hennecke‘s service specialists see themselves as long-term partners of manufacturers and producers in order to achieve optimum results. Continuous developments can be implemented, particularly in the areas of production quality, safety and sustainability, which ultimately also lead to cost savings in raw materials and energy costs. “Even if the plant seems to have been running well for years, there are often new developments and innovations that turn a ‘good’ into a ‘better’ and also enable savings,” recommends Thomas Walterscheid, Hennecke Service Sales, to plant operators.
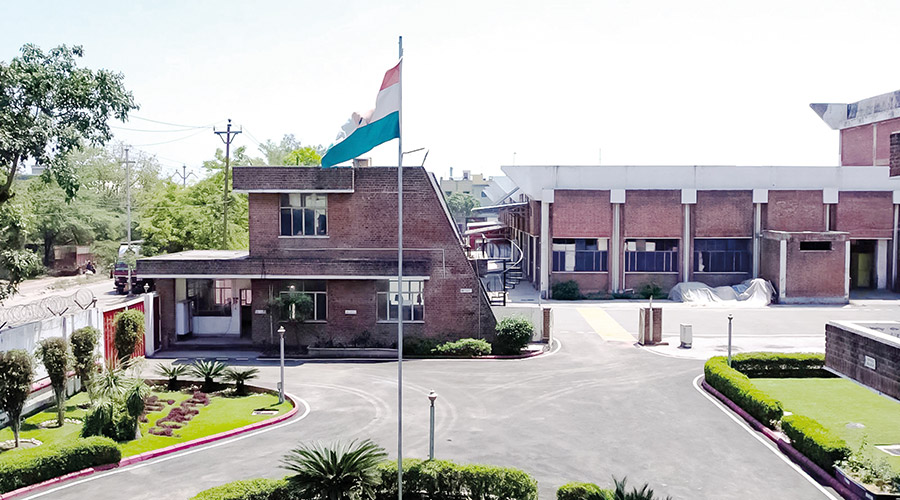