Homogeneous mixing of solid and liquid components
PU- or PIR-based compounds for flame retardancy and sustainable rigid foam production.
2022, Hennecke has introduced the “Environmental Technologies” product line with machines and add-ons for more sustainable production. New is the ECOFILLER PLUS, which enables in-line metering and therefore extremely homogeneous mixing or compounding of liquid with solid components. In this way, shredded cutting residues and production waste can be fed back into the production process, enabling waste-free production. In addition, other solids, such as powdered flame retardants, can also be incorporated absolutely homogeneously into the formulation.
The sustainable Environmental Technologies product area has been a focus of the Hennecke GROUP for two years. It aims to offer customers environmentally friendly technologies and services along the polyurethane processing chain. An important issue here is the avoidance of production waste or the recycling of this waste into the production process. Within this framework, Hennecke-OMS – the sandwich panel specialist within the Hennecke GROUP – has developed the ECOFILLER PLUS with a cross-divisional team, which is now offered as an add-on to the existing metering units. It is suitable for the most common rigid foam applications within sandwich panel production and is the perfect addition to Hennecke-OMS’ PANELMASTER production lines in the Hennecke GROUP product portfolio. “The new ECOFILLER PLUS lets users create decisive added value – while significantly improving the range of properties in their end products when producing polyurethane compounds. For example, in terms of sustainability,” explains Pierpaolo Azzalin, Head of Sales Hennecke-OMS.
Waste-free production possible
Even in the very raw-material-efficient production of sandwich panels, trim waste is produced depending on the shape and type of the end product. This waste not only wastes valuable raw materials, but also has to be disposed of and thus causes avoidable costs. This is where Hennecke’s new development comes in: It makes it possible to return the trimmings to the production process. The ECOFILLER PLUS is able to very quickly combine the liquid components of the polyurethane compound with the recycled solid materials in powder form. “As part of our sustainability strategy, we not only take care to reduce waste ourselves – but also aim to help our customers produce on a more sustainable basis by recycling valuable raw materials in order to protect the environment and save costs,” says Andrea Mariani, President BU Italy.
Fire retardance: simple and safe
Another important application scenario for ECOFILLER PLUS is the improvement of the fire behavior of products based on polyurethane (PU) or polyisocyanurate (PIR). The regulations and requirements for materials – especially in the manufacture of insulation boards – are becoming increasingly stringent and present manufacturers with special new challenges. By using liquid and solid raw material components, ECOFILLER PLUS enables users to develop, test and incorporate flame retardant compounds into the PU or PIR formulation for mass production. Moreover, the process enables manufacturers to decisively improve the fire behavior of the end products with their own and self-developed formulations. One example of this is insulation boards with a flexible face layer for the energy insulation of house walls.
This application should also not be underestimated with regard to the climate crisis. The industry needs sustainable flame retardants that can be tested with ECOFILLER PLUS under the real conditions of mass production. More importantly, in the field of building insulation, there is a greater demand than ever for products that must be highly efficient not only in terms of properties such as stiffness, density and thermal conductivity – but also in terms of fire retardance, regardless of the application. Residential buildings, industrial buildings and cold storage rooms are just a few examples. So far, the strictest regulations apply in Asian countries, but the Western world will also raise the bar in the coming years and demand adjustments from manufacturers.
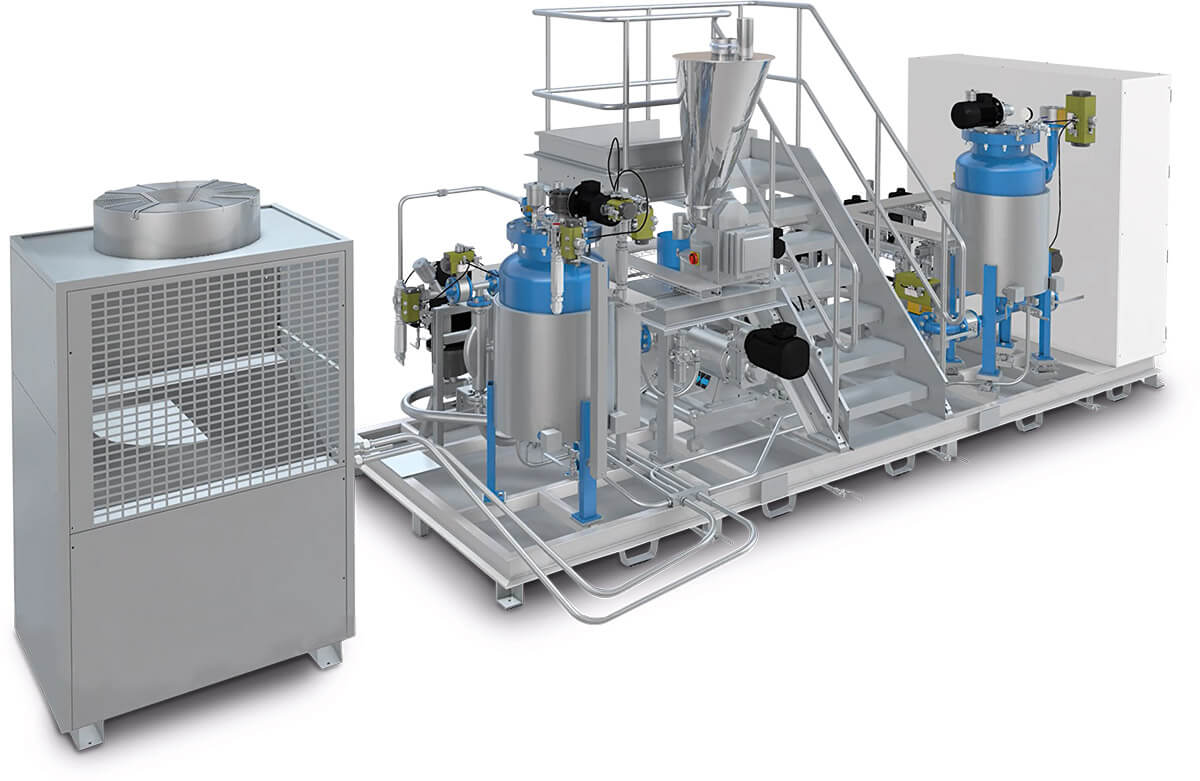
Combining solids and liquids homogeneously
The particular challenge in the development of ECOFILLER PLUS was to achieve a completely consistent homogeneity of the solid and liquid components so that the concentration of the solid components is constant at every point of the end product. This guarantees not only consistently high quality, but also a uniform fire protection effect at all points of the end product. The key to this lies in the different sections of the ECOFILLER PLUS and its innovative mixing system.
The solids metering unit has a capacity of 110 liters. Here, powder metering is carried out in the dynamic mixer by means of an innovative hopper system, a twin screw feeder and a volumetric pump, which is precisely controlled by special electronic load cells underneath the funnel. The polyol is metered by a metering pump, and the individually adjustable flow rate is automatically controlled by special flow meters in a closed circuit – depending on the programmed formulation. As soon as the desired flow rate is reached, the solid and liquid components are transported by a conveyor screw to the actual mixing area. Here, specially arranged pins and counter-pins ensure effective and uniform mixing of the two components.
On the outlet side, the homogeneous mixture now passes almost without pressure into a tank, where a suction diaphragm pump prevents backflow. From there, a conveyor screw transports it to the agitator tank. In this 250-liter double-shell tank made of carbon steel, a special agitator ensures that the solids are permanently well mixed with the liquid – thus ensuring perfect quality until they are used in the next production batch. The integrated temperature control system ensures that the temperatures in both the raw material and the mixing tanks are always kept constant and within an optimum process window, regardless of external conditions.
Versatile
The ECOFILLER PLUS can operate in a flow range of 1.66 to 18.2 l/min and process materials with viscosities from 5,000 to 20,000 mPas and powder sizes from 50µm to 200µm. This allows it to be used for many different solids to be processed and numerous end products. In addition, formulations and the ratio of polyol to powder can be adjusted at any time during production via the HMI. The ECOFILLER PLUS not only guarantees immediate, optimal and uniform mixing of solids and liquids, but also significantly shortens mixing time for faster production.
The process in brief
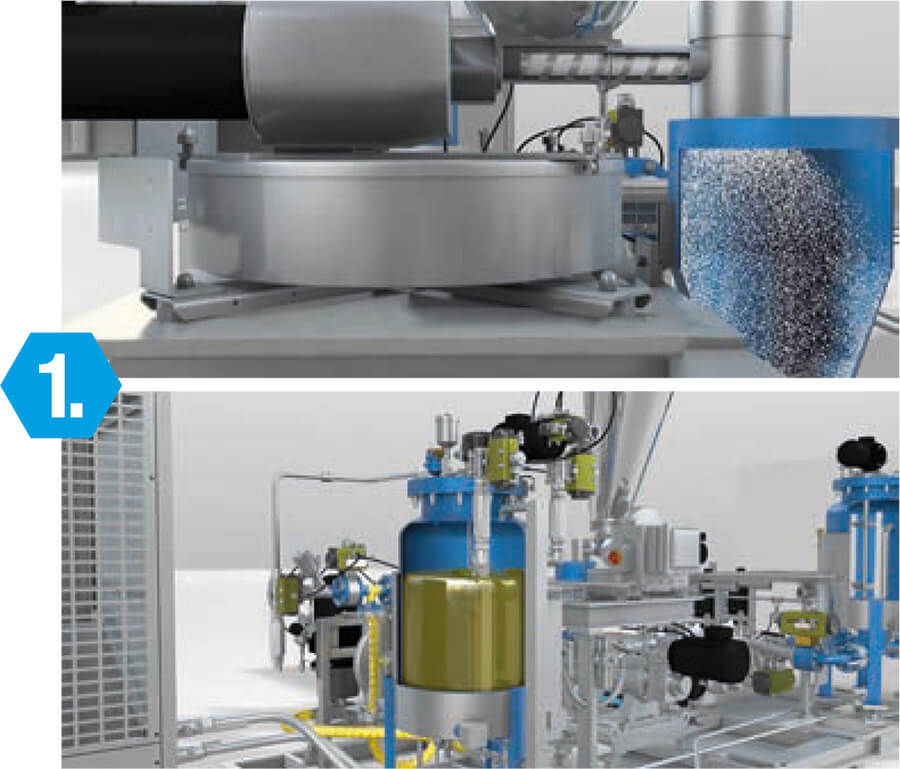
The solids in powder form and the polyol are prepared for the mixing process and then fed into the mixing chamber.
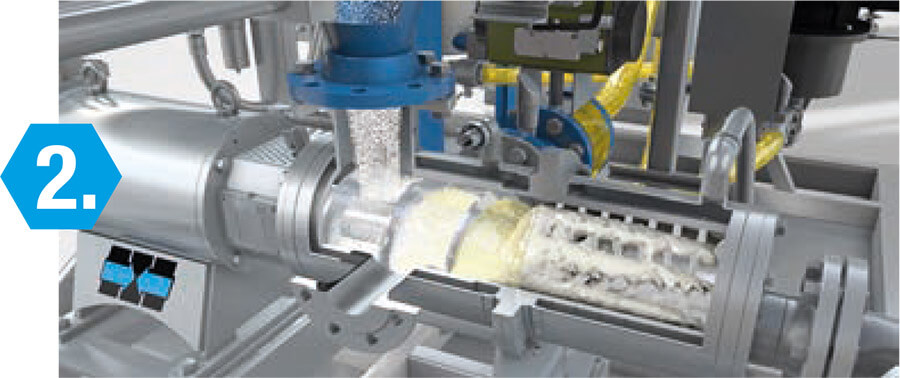
In the mixing chamber, specially attached pins and counter pins ensure fast and uniform mixing of the media.
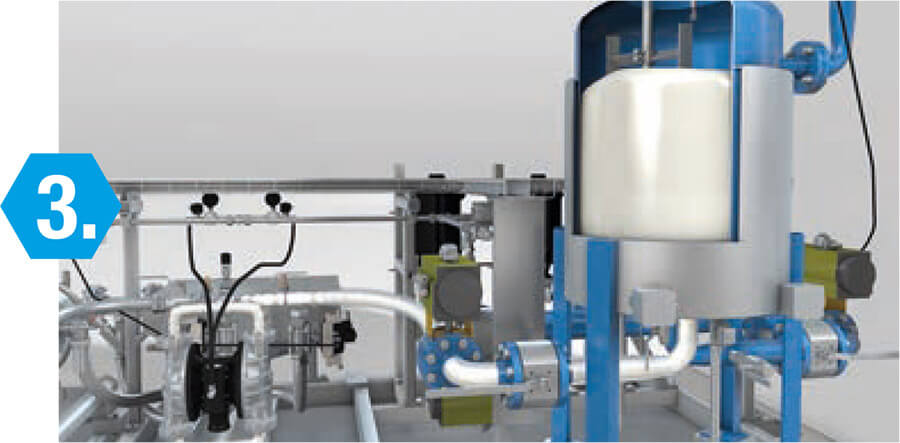
In the “final” tank, the finished mixture is optimally conditioned and stored until it is used in the next production batch.