Customized for the efficient production of fiber-reinforced structural components using WCM
The new JETLINE by Hennecke-OMS
HP-RTM technology is the top choice for realizing complex, fiber-reinforced structural components. There is however another cost-efficient process that can be used for producing parts with a more simple and two-dimensional structure - the so-called Wet Compression Moulding (WCM). Compared to the HP-RTM processes, WCM applications score points for their shorter cycle times. Hennecke GROUP customers can now benefit from the growing market and specific advantages of this new processing method with a specially adapted metering machine system using proven low-pressure technology from the Italian PU specialists HENNECKE-OMS: the JETLINE.
WCM technology represents a highly efficient production method for volume production of simple, two-dimensional and fiber-reinforced structural components. In this process, the reactive mixture is applied - either manually or automated - on to the semi-finished part as a fluid film. This takes place either in a separate workstation using a robot-controlled application, or directly in the mould. In a separate workstation, the fiber fabric is guided under the WCM injector of the mixhead by one or more robots and the reactive mixture is applied to the fiber fabric. The robot then places the wetted semi-finished part precisely into the mould. The press closes together with the mould, ensuring that the reactive plastic is distributed evenly. After curing, the finished part can be removed for trimming. Compared to HP-RTM technology, the WCM process places significantly fewer demands on production, particularly with regard to the complexity of the mould. In addition, the time in the press and consequently the cycle time can be reduced.
Up to now, Hennecke's STREAMLINE systems have been used for WCM processes. A thoroughly developed product that has recently undergone a comprehensive update (see infobox) and is precisely adapted to the process availability of serial applications in HP-RTM, CLEARMELT and WCM processes. However, if a metering machine is required only for WCM applications, the STREAMLINE, with its wide range of uses in process technology, becomes quickly oversized. Low-pressure technology can also be used for the open application of the fluid film in WCM processes. And this is where the JETLINE can score points, as the robust machine system has been specially optimized for use in WCM applications.
Focusing on a specific process does not mean that JETLINE customers have to make sacrifices: HENNECKE-OMS have installed exclusively high-quality and proven parts into the metering machines, such as the SIEMENS control system modules including a large touchscreen operator panel. The newest company in the HENNECKE GROUP has decades of experience in the area of low-pressure technology. This expertise is now concentrated in the JETLINE.
The work tank for the A component is housed in a heating cabinet and tempered homogenously using circulating air. The A component recirculation lines to the mixhead are also heated. The auxiliary components are stored in double-walled work tanks. A dynamic ULTIMIX stirrer mixer is used to ensure an optimum mixing result. A 180mm jet nozzle is deployed as a dispenser. Here the nozzle is reliably cleaned after every shot using compressed air and through additional rinsing with the A component. As an option, a solvent station is available for effective cleaning of the mixhead chamber. If release agents are to be used in the production, the JETLINE can additionally be fitted with a release agent station. Furthermore, an automated filling device for the components is supplied so that the machine can produce without interruption. For interested customers, the JETLINE can be closely examined and tested in the Hennecke TECHCENTER at the site in Sankt Augustin.
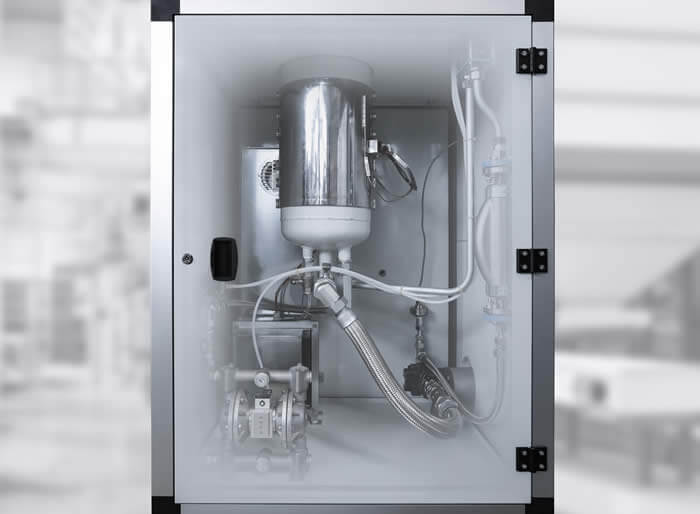
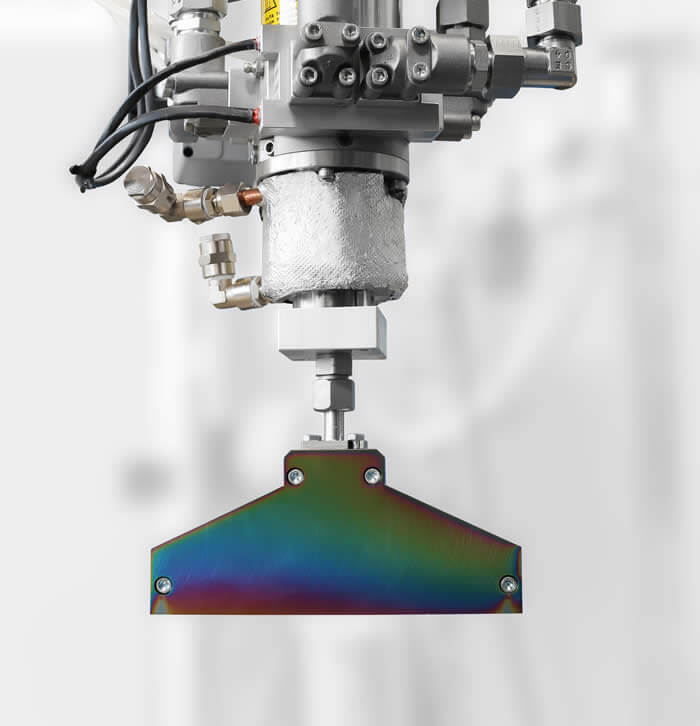

The all-rounder for HP-RTM, CLEARMELT and WCM applications: the STREAMLINE MK2
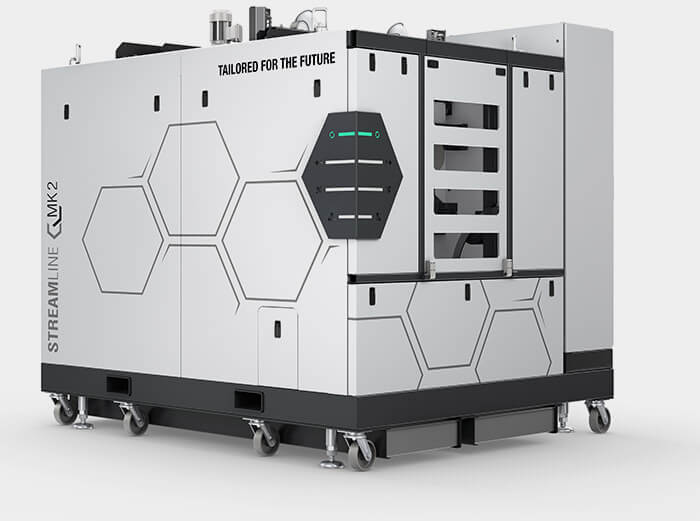
Building on the sale of over 70 STREAMLINE machines in the first generation, developers, manufacturers and raw material suppliers have been able to develop, in many ways crucially, a variety of processes in the manufacture of fiber-reinforced structural components and in efficient surface finishing using polyurethane, leading to diverse serial applications. The second generation of the machines has been significantly enhanced using the experience of dozens of production systems and advance product developments: Production flexibility has increased thanks to the space saving layout of the machine on a mobile frame which can also be lifted by crane. The plant automation is also particularly flexible: The STREAMLINE MK2 is equipped with a wireless operator panel which enables on-the-spot operation of all process parameters, independent of location. The efficient heating configuration is also impressive with its innovative detailed solutions: the heating and metering cabins are joined together using quick-locking mechanisms which allow for easy dismantling. This ensures that all main components such as the high-pressure pumps can be exchanged very quickly. The STREAMLINE MK2 also has a special honeycomb-shaped status panel with integrated LED lights which enable the operator to determine the current status of the machine at a glance.