Hennecke presents the 'ZERO AGE APPLICATOR'
Revolutionary discharge system for continuous flexible and rigid foam applications
When it comes to the continuous production of high-quality flexible foams for the furniture industry, Hennecke has been the global market leader for several years. More than 600 plants sold and generations of satisfied customers worldwide speak for themselves. On top of that, plants for the continuous processing of rigid polyurethane foam for the manufacture of sandwich panel insulating elements are also regarded as the undisputed standard on the market for efficient and flexible production. With the new Zero Age Applicator, Hennecke's polyurethane specialists are now presenting a revolutionary distribution system for both rigid and flexible foam applications which offers a convincing alternative to the discharge systems previously available.
In the development of the new discharge system, the focus was placed on the way in which the liquid raw material mixture is dispensed within the production line. This requires a uniform distribution over the entire foaming width combined with a foaming reaction that starts precisely at the same time. Discharge systems used up to now have either used several mixheads or various different mechanical distribution systems to achieve the best possible combination of these two properties.
The Zero Age Applicator, which Hennecke offers in two specially adapted variants, now enables a decisive improvement and moves a step closer to the envisaged ideal in this interplay. With this system, several injectors are used at the same time which are arranged in a semi-circle in the discharge unit. The homogeneously mixed material is thus dispensed onto the bottom sheet in several streams across the entire foaming width. The decisive factor is that the reaction starts at the same time across the entire foam width. More precisely: the foam cells form in one virtual line without any time delay, or indeed with a "zero age difference".
In the area of continuously manufactured sandwich panel insulation elements, this allows for an extremely homogeneous foam structure and therefore an improvement in the rigid PU foam's insulating properties. In addition, the useful life could be optimized in comparison with standard discharge systems. During the manufacture of slabstock foams, the new system ensures improved efficiency of raw materials as well as a significant shortening of transition pieces when changing formulation or colour, ultimately resulting in less waste. Through extensive flow simulations and a range of test runs under real production conditions, also with regard to easy handling, cleaning and reusability, the new system was gradually developed to be market-ready for a wide range of applications. With this, Hennecke is once again proving its full professional expertise in the area of continuous production solutions in the PU sector.
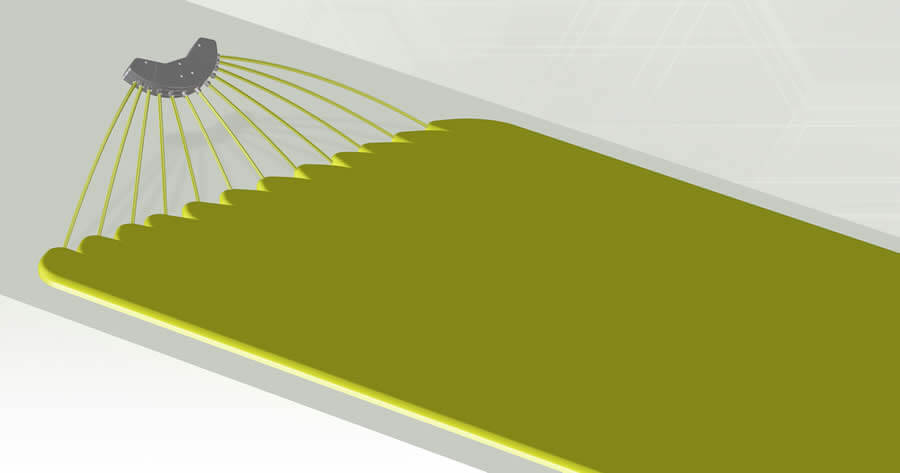
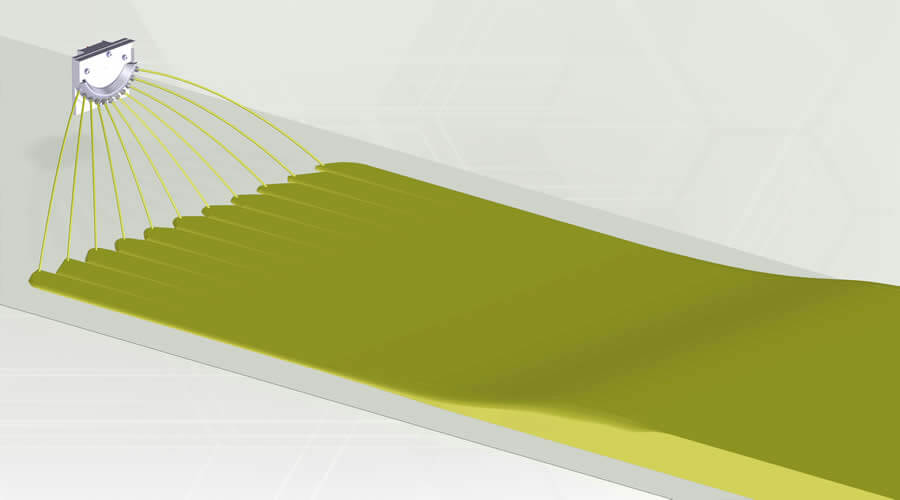
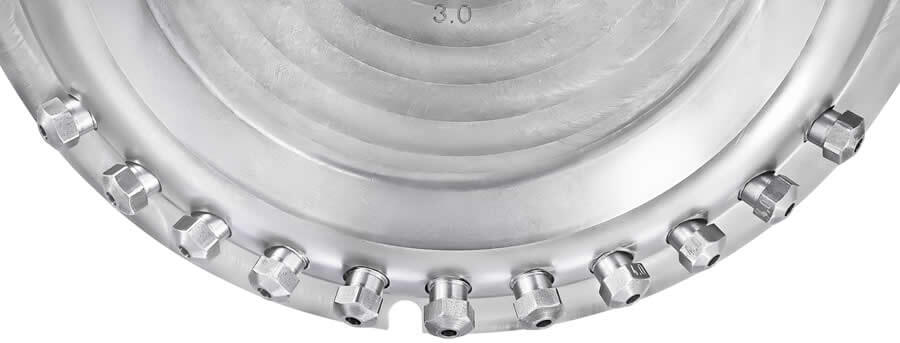