Extremely energy-efficient prefabricated houses
System expertise from Hennecke and AutoRIM
The company Scotframe with its headquarters in Inverurie, Scotland, is one of United Kingdom’s leading manufacturers of wood-frame structures for building prefabricated houses. Under the brand name Val-U-Therm, the manufacturer sells a wide-ranging system of highly insulating closed timber frame wall, roof & floor panels with polyurethane cores, which also score highly in the areas of environmental friendliness and sustainability. Scotframe has trusted in machine technology from Hennecke and AutoRIM in its manufacturing since 2008. In the newest version, Val-U-Therm "Plus", the company was able to once again considerably improve the already outstanding insulation properties of the building components and, as a result, markedly exceed even the specifications of the passive house standard. This is made possible by the installation of new, highly precise mixing and metering technology, which, among other things, enables processing of the environmentally-friendly blowing agent pentane.
Scotframe Val-U-Therm is a hybrid of wood-frame and Structural Insulated Panels (SIPs) technology. This ‘best of both worlds’ approach uses the structural principle of a wood-frame design consisting of a supporting frame made from wooden beams, which is panelled and reinforced from both sides with OSB plates. In a manner similar to SIPs, the thermal insulation is incorporated into the cavity between the inner and outer planking so that it is level with the supporting structure. This means that the wood frame constructions achieve very good insulation values with comparatively low wall thicknesses. The roof and floor components are manufactured according to the same principle. A great benefit of the wood frame design is the high degree of prefabrication. As the Val-U-Therm components are already prefabricated with high-quality thermal insulation, windows, doors and sometimes façades, all that is left to do at the construction site is put the building components together. Again a special method of connecting the panels allows the shell of the building to be erected within a few days. Due to the dry construction method, there is no need for the otherwise typical drying times during the building phase. Even though top-class building materials are used, the industrial pre-fabrication of the walls and the repeating connection details provide significant cost benefits compared with conventional construction.
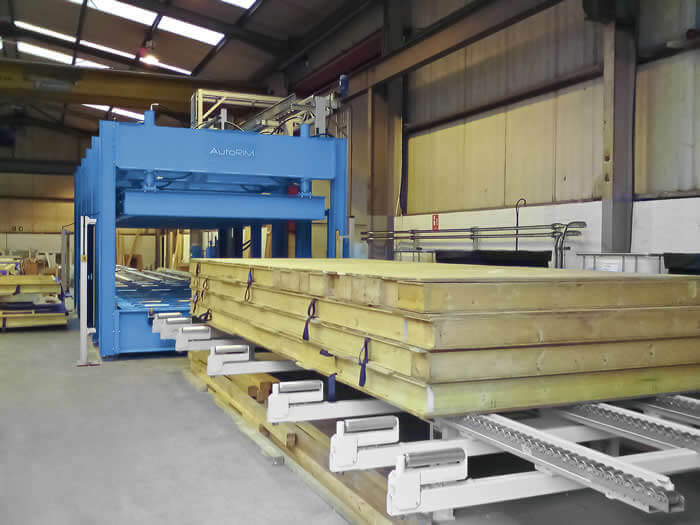
For eight years Scotframe has relied on polyurethane machine technology from Hennecke in the production of Val-U-Therm hybrid Eco SIP building components. The corresponding PANELFORMER model hydraulic press is provided by Hennecke's partner company and specialist in system integration AutoRIM. The press provides over 150 tonnes of closing force and can be used on panels up to 8.1 m x 3.1 m in size.
A hydraulic lifting device developed by AutoRIM itself provides a reliable form of transport for the building components into the PANELFOAMER and out again. In order to be able to lift the components as close to parallel as possible, the presses are equipped with a tooth rack drive system as standard. Despite the high pressure generated during the foaming process, the entire construction is extremely resistant to distortion.
In the production of the Val-U-Therm panels, up to six wall components are stacked on top of one another in the press and stabilised by the press force. An employee uses a hand-operated Hennecke mixhead to pour the quantity of PU mixture that has been precisely calculated beforehand into the predrilled filling holes and into the respective cavities in the wall components. Ventilation holes allow the air to escape out of the cavities as the PU foam expands. The polyurethane entirely coalesces with the cover surfaces and wood frame as it hardens and, as a result, not only insulates but also stabilises the wall. The managing director of Val-U-Therm, Bryan Woodley, is enthusiastic about the machine technology: "The installed system technology from Hennecke and AutoRIM has been working reliably ever since day one."
Due to the increased demand for ever more efficiently insulated houses and designs that are compliant with the passive house standard, the managers at Val-U-Therm decided to extend their product range of hybrid Eco SIP building components with a version featuring even better insulation: Val-U-Therm "Plus". For this, production was modified for the use of pentane as a blowing agent. With pentane, even better insulating properties can be achieved in the manufacture of PU insulation, due to finer cell structure in the hardened foam, while also minimising the impacts on the environment. Along with optimised insulation, the use of pentane as a blowing agent also makes a significant contribution to effectively reducing the specific GWP (global warming potential) of the modern building components. For gas loading using pentane, the prefabricated house specialists rely on the blowing agent metering unit PENTAMAT 30i. Instead of metering blowing agent directly in the mixing chamber, processing using PENTAMAT blowing agent metering units takes place in batch processing within a polyol component. Here, the percentage of blowing agent in the component flow can be varied with great precision, reproducibly and in almost any ratio.
One thing was clear to Woodley from the start in the "pentanisation" of production: "There is no plan B when it comes to processing pentane. You have to do it right from the very beginning. We were impressed by Hennecke's system technology and refined safety concept, as well as AutoRIM's many years of expertise in the installation of systems of this kind." In fact, with Pentane Process Technology (PPT), Hennecke offers its customers superior safety solutions for processing pentane. In the production of the Val- U-Therm "Plus" panels, for example, the development of dangerous concentrations of gas is effectively prevented using nitrogen immediately before the building components' cavities are filled with foam. As before, the system operator only needs to plug the mixhead output pipe into the filling holes to do this. Nitrogen is automatically metered according to the respective output quantity of the reactive mixture before the foam is poured in. This means that nothing has changed in the workflow. The press has also been equipped with reliable pentane sensors by AutoRIM.
Along with the conversion to pentane, the company decided to make a significant update to the metering technology. For this, the AutoRIM specialists installed the top of the range high-pressure metering machine in Val-U-Therm production: a TOPLINE HK 720 with an output rate of up to 1440 cm³/s. The state-of-the-art metering machine is used together with an air-cleaned MXL 14-type mixhead, which enables synchronous switching between shot and recirculation with its hydraulic control piston. Together with an optimised mixing chamber geometry this ensures that the shot weights are adhered to precisely and the product quality remains constant. The package is rounded off with an automated supply station for the raw materials. The sum of the measures is reflected in a thoroughly impressive improvement in the insulation values for the end product. The lambda value compared to the conventional Val-U-Therm components has fallen from 0.025 to a striking 0.023. The first commercial applications of the Val-U-Therm "Plus" building components make their potential clear. One successful example is the Maryville Passive House project in the area of Loch Lomond, Scotland. Here the Val-U-Therm "Plus" building components provide a highly insulated and airtight high-tech outer shell that is free of thermal bridges. In combination with other structural measures the annual energy requirements could be reduced to 69 kWh/m² per year. This means that the heat energy consumption of the Maryville Passive House is 40 per cent lower than the passive house standard (120 kWh/m²a). Another example is the construction of a complex extension to the Meldrum House Country Hotel in Oldmeldrum, Scotland. A ballroom for up to 200 people was erected here in record time, with its outer shell also consisting entirely of Val-U-Therm "Plus" building components and likewise achieving impressive energy-saving potential values.
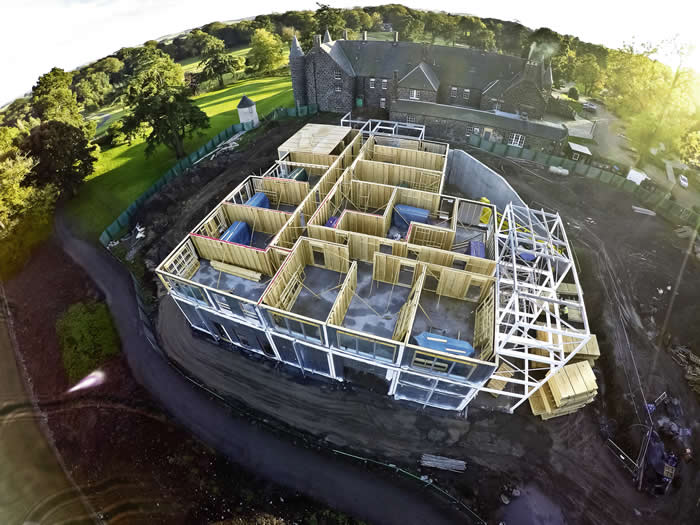
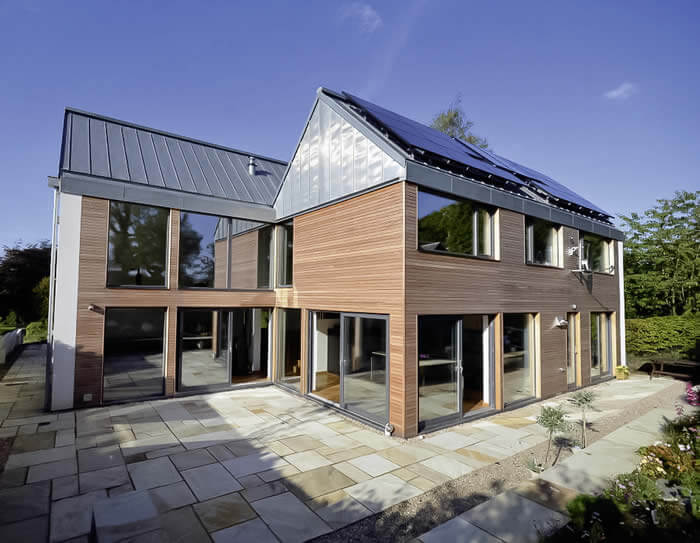