Everything from a single source:
complete production lines for sandwich construction elements
The trend of obtaining complete customised solutions from a single source continues in almost all areas of production. Even manufacturers of roof and facade elements have in the past years increasingly requested overall solutions in the area of continuous sandwich panel production. In order to meet this demand, Hennecke has broadened its product portfolio for customers within this industry sector. The PU specialist is now able to deliver - in addition to reaction technology - complete production lines, from raw material storage to rollforming machines and packaging equipment.
Sandwich elements are mainly used in the construction of halls, industrial buildings, cold and deep-freeze stores as well as in office and residential buildings. They are also applied in the industrial sector for the production of sectional doors and for garage doors in homes. Today, more than 200 million square metres of roof and facade elements are manufactured and installed in Europe each year. In the past five decades, the number of buildings being constructed with sandwich structures has multiplied. An entirely new generation of sandwich elements fulfils not only structural-physical and economical requirements but also individual design demands.
A sandwich panel consists of foam-filled composite elements, for which the facings are produced either from steel or aluminium. These facings can be flexible or rigid, varying in width and profile. Because of the PU foam core, sandwich panels have a very good thermal insulation value. In addition, the prefabricated panels are self-supporting and enable a fast and cost-efficient assembly for the builder. The production of such sandwich panels takes place on continuous sandwich panel plants. Hennecke has been in the market for more than 40 years with the CONTIMAT plant type. CONTIMAT plant technology enables the continuous production of top-quality sandwich panels with various facings, panel thicknesses and profiles. With a usable width of up to 1200 millimetres, element thicknesses of up to 250 millimetres and a production capacity of up to two million square metres per year, the modern system concept covers an extremely wide range of applications.
In order to also offer the customers all peripheral devices from a single source in addition to the reaction technology and to realise complete production lines including rollforming, cooling and stacking systems and finishing, Hennecke has extended the CONTIMAT team to include new employees with many years of know-how in the area of panel-handling technology. With the operational integration of parts of WMG Willwacher Maschinenbauu. Vertriebs GmbH, Hennecke has additionally taken in the competence of more than 40 years of experience in the area of surface and edge profiling of metal elements.
Included in the portfolio of the highly specialised company, which is located in the Siegerland region of Germany, are rollformers and presses, which seamlessly conform to the existing system concept of CONTIMAT continuous sandwich panel plants for metal facings.

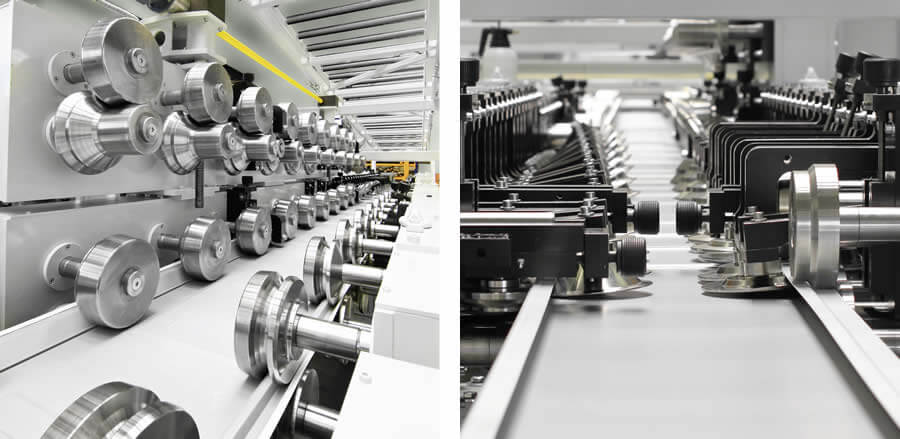
With these measures, the company is in an optimal and comprehensive position to cover all the major areas of continuous panel production:
- Production technology for sandwich panels with a core made of PUR/PIR rigid foam and/or mineral wool with steel facings in all varieties and designs for wall and roof
- Plants for foamed sectional doors
- Complete production lines for insulation panels with PUR/PIR rigid foam core and flexible facings including complete finishing
- Complete production plants for Structural Insulated Panels (SIP) with a PUR/PIR rigid foam core and rigid facings made of, for example, wood materials or inorganic panels
- Efficient and economic production of special products, such as, e.g. foamed doors, trailer walls and prefabricated house components
Hennecke has successfully demonstrated its technological leadership and the sustainable performance of the CONTIMAT plants in many projects. The newly gained complete system capacity is accepted very well in the market.
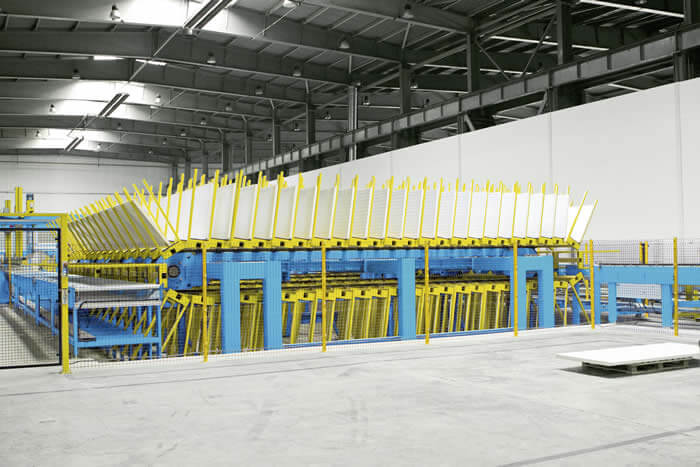
This is also reflected in investments in new plants. In the last year and a half alone, Hennecke was able to supply Eastern Europe and Asia with complete production plants including profiling, cooling, stacking and packaging for the production of garage doors, insulating panels, cold store panels and even for special products like floor heating panels. This also includes a highly flexible system concept that allows various products to be processed on a single plant.
However, the excellent market acceptance is no reason to sit back and rest. Through continuous further development of the CONTIMAT plant technology, Hennecke wants to continue to offer its customers tailor-made solutions for every conceivable application. For that, productivity, plant availability, flexibility and a long lifespan are decisive criteria. With its longtime application experience and market presence in combination with innovative orientation, Hennecke does not set the technology standard in the area of sandwich plants for nothing, and is increasingly becoming the contact worldwide when it comes to efficient production of sandwich elements.
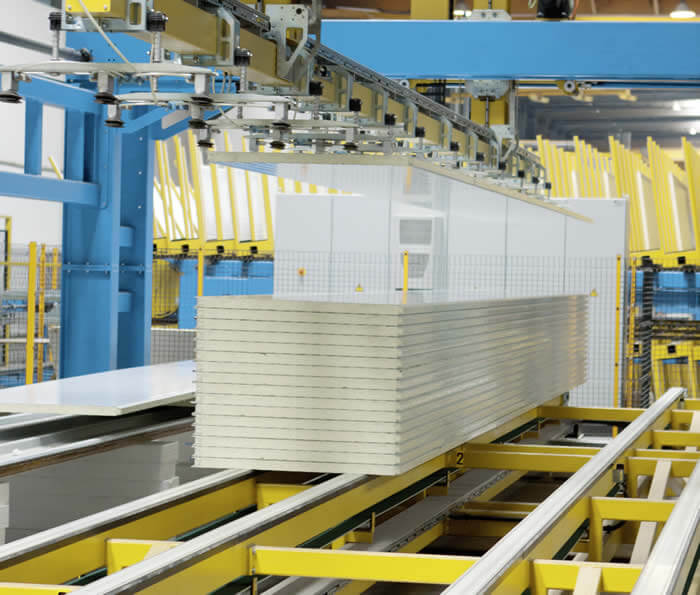
Foam pouring under high speed, mixhead and dispensing systems for the fast-running CONTIMAT
In the production of sandwich panels with flexible facings, often highly reactive PIR systems are used in conjunction with high conveyor speeds. Therefore Hennecke extensively modified the CONTIMAT reaction mixhead. Special recirculation mixheads are used which are equipped with a circulation control so that the material can circulate directly in the mixing chamber via the injectors and recirculation grooves of the control piston. Thanks to hydraulically controlled pistons, the special type of mixhead is also self-cleaning. To ensure optimum mixing quality, the individual injectors are specifically adjusted and designed as constant pressure injectors. The mixing pressure is thus automatically kept at a constant level throughout the entire operating range.
At the same time, output changes can be made over wide ranges without having to adjust or replace the injectors, for example when changing to different insulation thicknesses. The entirely new so-called multiple nozzle system allows the processor an optimal surface distribution over the entire foaming width and simultaneously ensures that the reaction mixture has the same age at every location over the foaming width. An optimal foam quality is thus ensured, with homogeneous thickness distribution and without any voids which often arise from the usual overlaps of foam.