Gut gedämmt
Polyurethan-Hochdrucktechnik optimiert die Dämmeigenschaften von Kunststoffmantel-Verbundrohren
Kraft-Wärme-Kopplung lautet das Schlagwort, wenn es um die Zukunft der Energieerzeugung geht. Um Rohstoffe und CO2 einzusparen, soll die bei der Stromgewinnung anfallende Restwärme nicht mehr ungenutzt in Kühltürmen entweichen, sondern als Fernwärme beziehungsweise Fernkühlung genutzt werden. Damit die Wärme oder Kühlung auch dort ankommt, wo sie gebraucht wird, sind isolierte Rohre notwendig. An diese sogenannten Kunststoffmantel- Verbundrohre werden immer höhere Ansprüche im Bereich der Dämmung gestellt. Hennecke-Hochdruck-Dosiermaschinen für die Verarbeitung von Polyurethan (PUR) stellen die hohe Qualität sicher.
Die PUR-Spezialisten von Hennecke erwarten im Bereich von gedämmten Rohrsystemen in den kommenden Jahren einen stark wachsenden Markt. Dabei gewinnt ein Faktor zunehmend an Bedeutung: der Energieverlust über die Zeit. Auch die Betriebskosten eines Rohrnetzes spielen eine immer größere Rolle. Effiziente Systeme sorgen dafür, dass die beförderte Energie nahezu ohne Verlust ankommt. Deswegen sind Rohre mit sehr hohen Dämmeigenschaften immer gefragter. Zudem werden weltweit diverse Anstrengungen zum Klimaschutz unternommen und Unternehmen können somit gleichzeitig dazu beitragen, die CO2-Emissionen wirksam zu reduzieren. Vorgedämmte Rohrsysteme kommen neben der Fernheiztechnik auch bei On- und Offshore-Anwendungen für den Transport von Trinkwasser sowie bei Öl- und Gasprodukten, in der Prozessindustrie und im Schiffsbau zum Einsatz.
Die europäischen Regierungen und die Europäische Union fördern seit einigen Jahren die Kraft-Wärme-Kopplung. Es ist zu erwarten, dass sich diese Technik auch verstärkt in Osteuropa und anderen Teilen der Welt durchsetzen wird. Moderne Kraft-Wärme-Kopplungs-Kraftwerke beispielsweise in Dänemark haben heute einen Gesamtnutzungsgrad von mehr als 75 Prozent. Viele herkömmliche Kraftwerke in Europa ohne Kraft-Wärme-Kopplung weisen dagegen lediglich einen Nutzungsgrad zwischen 25 und 30 Prozent auf, da hier die Restwärme nicht genutzt wird.
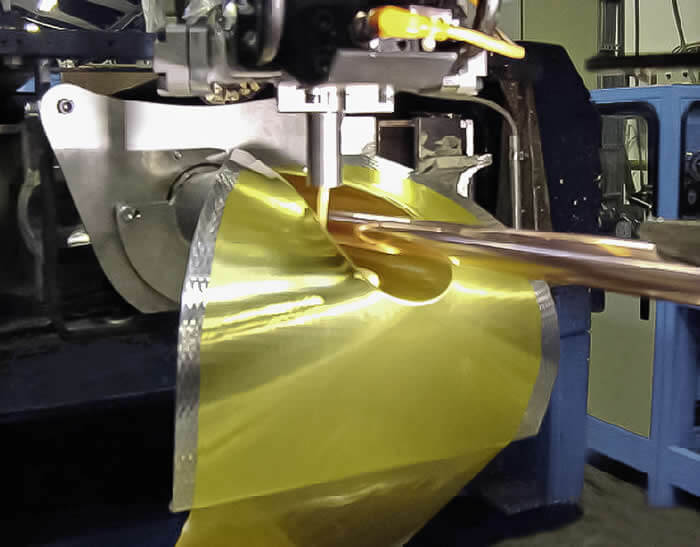
Die für die Fernwärmenetze notwendigen Kunststoffmantel-Verbundrohre gibt es als sechs, zwölf oder sechzehn Meter Stangenware. Sie bestehen aus unterschiedlichen Materialien. Das Medienrohr wird aus Stahl, Kupfer oder Kunststoff gefertigt, die Wärmedämmung aus geschäumtem Polyurethan (PUR) und das Mantelrohr in den meisten Fällen aus Polyethylen (PE). Das Medienrohr reicht auf beiden Seiten über den Mantel hinaus, um die Rohre auf der Baustelle miteinander fügen zu können. Nachdem die Medienrohre verbunden sind, wird eine PE-Muffe über die mantelfreie Stelle geschoben und der Hohlraum mit PUR ausgeschäumt.
Mittlerweile hat PUR bei der Rohrisolierung klassische Materialien wie Mineralwolle verdrängt. Der wichtigste Grund dafür ist der geringe Lambda-Wert. Darunter versteht man die Wärmeleitfähigkeit von Stoffen. Je kleiner die Wärmeleitfähigkeit, desto besser ist die Wärmedämmung. Mit Lambda-Werten von 0,020 bis 0,035 W/(mK) – je nach Treibmittel – ist Polyurethan vielen anderen Dämmstoffen überlegen. Zieht man neben den ausgezeichneten Lambda-Werten auch noch die höhere Langlebigkeit von PUR-gedämmten Rohren in Betracht – sie beträgt durchschnittlich 30 Jahre – kommt im Laufe der Zeit eine beträchtliche Energieeinsparung zusammen. Umgekehrt erlaubt der bessere Dämmwert, die Dämmstärken und damit die Kosten für die Rohrproduktion zu reduzieren. Außerdem ist aufgrund der verringerten Dämmstärken der Transportaufwand geringer und die Rohrverlegung einfacher.
Verschiedene Herstellverfahren
Zur Fertigung der isolierten Rohre kommen kontinuierliche oder traditionelle Verfahren zum Einsatz. Bei den traditionellen Verfahren erfolgt die Rohrproduktion einzeln in festen Längen. Dabei wird das Medienrohr mit Abstandshaltern versehen und anschließend ein PE-Mantelrohr aufgezogen. Danach wird in den Hohlraum zwischen Medien- und Mantelrohr, die sich in einer leicht geneigten Ebene befinden, der PUR-Schaum mit hoher Geschwindigkeit eingetragen, der sich nachfolgend von unten nach oben ausbreitet. Die Herausforderung bei diesem Verfahren besteht darin, eine möglichst große Menge reaktives Gemisch in einer vorgegeben Zeit in das Rohr zu füllen. Gleichzeitig müssen Turbulenzen beim Füllvorgang wirksam vermieden werden, um möglicher Lunkerbildung oder Dichteschwankungen und somit einer ungleichmäßigen Dämmung vorzubeugen. Der Hennecke-MXL-Mischkopf bietet dazu alle Möglichkeiten. Das traditionelle Verfahren kommt meistens bei Kleinserien zum Einsatz, da es das geringste Investitionsvolumen aufweist und gleichzeitig am flexibelsten und zudem einfach um- und aufrüstbar ist.
Um die Qualität in der Einzelfertigung zu verbessern, hat Hennecke die Mischkopfziehtechnik entwickelt. Bei diesem Verfahren wird – ähnlich wie bei der traditionellen Fertigung – der PUR-Schaum in den Hohlraum zwischen Medien- und Mantelrohr eingebracht. Medien- und Mantelrohre werden jedoch nicht mit Abstandshaltern zentriert, sondern ineinander verschoben und statisch fixiert. Danach wird ein Mischkopf, der am Ende eines Lanzensystems befestigt ist, in den Hohlraum eingeführt. Beim anschließenden Herausziehen trägt der Mischkopf ein sehr schnell reagierendes Schaumsystem gleichmäßig über die gesamte Rohrlänge aus. Der Schaum muss keine Längs- beziehungsweise Fließbewegung vollziehen. Durch den laminaren Gemischauftrag wird im Rohr eine gleichmäßige Verteilung der Dichte von 58 kg/m3 und des Lambda-Wertes von bis zu 0,022 W/(mK) erzielt. Diese Homogenität führt gegenüber dem traditionellen Verfahren zu einer Rohstoffeinsparung zwischen 10 bis 15 Prozent. Denn bei der herkömmlichen Fertigung muss – um überall im Rohr eine definierte Kerndichte zu erreichen – entsprechend mehr Schaum eingegossen werden. Heute werden mit der Mischkopfziehtechnik vor allem Rohre mit kleinerer bis mittlerer Nennweite für Fernwärmeleitungen und Pipelines produziert. Der Gemischauftrag bei der Mischkopfziehtechnik erfolgt mit dem speziell entwickelten Hochdruckmischkopf vom Typ MRL, dessen Geometrie an den Rohrquerschnitt angepasst ist.
Die Baureihe MRL wird druckluft-gereinigt und ist mit federgespannten, druckgesteuerten Düsen ausgerüstet. Diese ermöglichen eine variable Gestaltung der Austragsleistung bei laufender Produktion und gleichbleibendem Mischdruck sowie eine abrufbereite Zirkulation der Materialien im Niederdruckkreislauf ohne zusätzliche Schaltelemente am Mischkopf. Beim kontinuierlichen-Verfahren werden die Rohre endlos statt einzeln gefertigt und nach dem Abkühlen auf die gewünschten Längen zugeschnitten. Zunächst werden die Innenrohre endlos fixiert. Parallel dazu wird eine Folie u-förmig vorgeformt. Im nächsten Schritt gießt ein Mischkopf den PUR-Schaum auf die Folie. Anschließend wird die gefüllte Folie geschlossen, sodass sie das Innenrohr ummantelt. Danach durchläuft das Rohr zusammen mit der Folie und dem aufsteigenden Schaum eine Kalibriereinrichtung, in der die Aushärtung erfolgt. Als Nächstes wird das schaumisolierte Rohr durch einen Extruder geführt, in dem es mit Polyethylen ummantelt wird. Während der gesamten Fertigung wird das Rohr gleichmäßig gezogen. Der PUR-Schaum muss lediglich aufsteigen und nicht wie beim traditionellen Verfahren einen Fließweg zurücklegen. Dadurch wird eine gleichmäßige Dichteverteilung und Dämmung erreicht. Um die Dämmqualität noch weiter zu verbessern, passt die Anlagensteuerung die PUR-Rezeptur permanent der Umgebungstemperatur an. Auch die Schaumfront wird überwacht und fließt mit in den Regelkreis der Anlage ein.
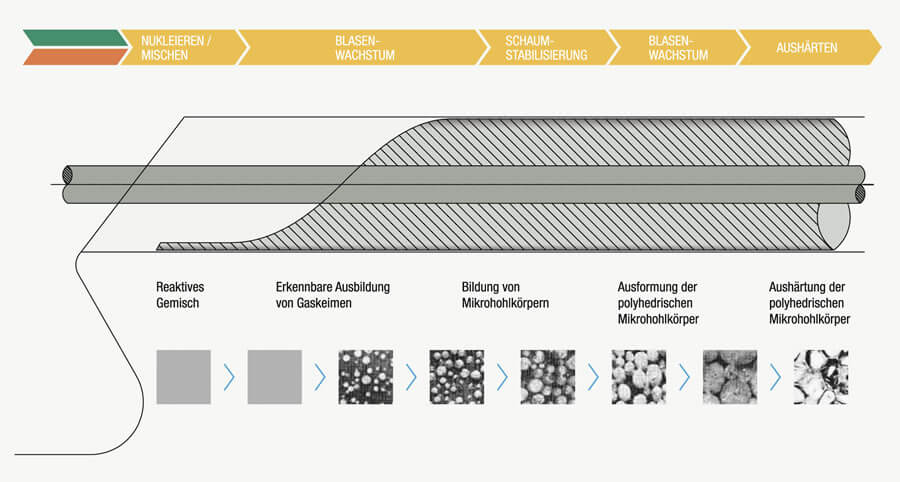
Höhere Vermischungsqualität
In der Vergangenheit wurden die PUR-Komponenten Polyol und Isocyanat beim kontinuierlichen Herstellungsverfahren mit der Niederdrucktechnologie vermischt. Die Vermischung erfolgte in diesem Fall mit einem dynamischen Rührwerk, an dem sich im Laufe der Zeit jedoch Ablagerungen bildeten. Diese reduzierten die Vermischungsenergie und damit auch die Vermischungsqualität. Durch den Austritt von Pentan in der Mischkammer kam es außerdem zu einer ungleichmäßigen Zellstruktur. Weitere Nachteile waren Lufteinschlüsse durch den Rührer, die notwendige Reinigung des Mischkopfs mit Lösemitteln bereits nach kurzer Betriebsdauer sowie die fehlende Möglichkeit, die Austragsleistung während der laufenden Produktion variabel zu gestalten. Bei der Hennecke-Hochdrucktechnologie werden Polyol und Isocyanat dagegen mit hoher Energie nach dem Gegenstrominjektionsprinzip verdüst. Dadurch werden deutlich bessere Vermischungsqualitäten erzielt. Auch Pentan lässt sich hierbei wesentlich exakter zudosieren. Die PUR-Schaumstoffe weisen eine durchgehend homogene Zellstruktur auf.
Die Zellgrößen sind kleiner und besser verteilt als bei der Niederdrucktechnologie. Auch das Betreiben der Anlagen ist wesentlich komfortabler: große Variabilität der Austragsleistungen, einfaches Zudosieren von Zusatzkomponenten wie Aktivatoren, weniger Reinigungsaufwand in der Mischkammer und Wegfall von Lösemitteln.
Hennecke beliefert seit zwei Jahrzehnten führende Rohrproduzenten in ganz Europa mit hochwertigen Fertigungsanlagen und ist mit 14 installierten, kontinuierlich-fertigenden Anlagen der Marktführer in diesem Bereich. Der Spezialist für Polyurethan-Technologie bietet für alle gängigen Verfahren zur Herstellung PUR-gedämmter Rohre das entsprechende Equipment – einschließlich der Verarbeitung von Cyclopentan mit der patentierten Pentane Process Technology (PPT). Je nach Fertigungsverfahren und individuellen Kundenanforderungen stehen Hochdruck-Dosiermaschinen vom Typ TOPLINE HK in unterschiedlichen Baugrößen, mit unterschiedlichen Vormischeinrichtungen sowie verschiedenen Mischkopftypen zur Verfügung.
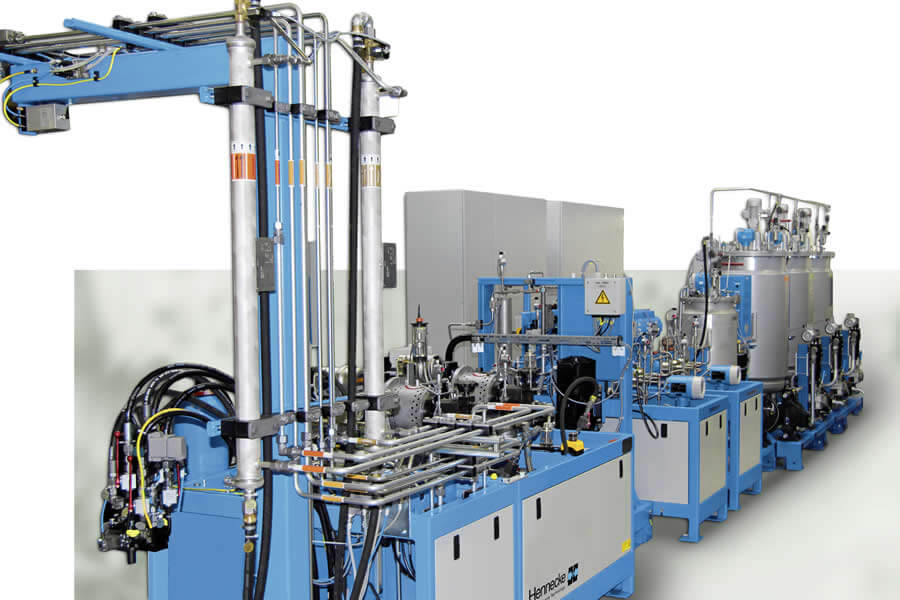
Download - Ausgabe 116 (PDF)
Zur Betrachtung benötigen Sie den Adobe® Reader®, den Sie hier kostenlos herunterladen können.