Mit Sicherheit leicht!
Herstellung von Faserverbund-Motorhauben
Basierend auf den Erfahrungen im Sandwich-Leichtbau mit Ladeböden und Schiebehimmeln sind die drei Partnerunternehmen Magna Steyr, Rühl Puromer und Hennecke nun einen Schritt in die Zukunft gegangen. Ausgelöst durch schärfere Vorschriften für den Fußgängerschutz haben sie eine Motorhaube mit Wabenkern in Honeycomb-Struktur entwickelt, die nicht nur die vorgeschriebenen Tests bestanden hat, sondern auch deutlich leichter ist und eine bessere thermische und akustische Isolation aufweist als herkömmliche Motorhauben aus Stahl oder Aluminium.
Die EU veröffentlichte 2009 die Global Technical Regulation (GTR) Nr. 9 zum Fußgängerschutz, an deren Umsetzung die Automobilhersteller und -zulieferer weltweit arbeiten. Auch bei der Neudefinition des Ratings der Euro NCAP, einem herstellerunabhängigen Crashtest-Programm, nimmt der Fußgängerschutz eine wesentlich stärkere Bedeutung ein. Um weiterhin die begehrten 4- oder 5-Sterne-Ratings für ihre Fahrzeuge zu erhalten, müssen die Hersteller künftig größere Anstrengungen beim Fußgängerschutz betreiben.
Einen Dreh- und Angelpunkt für den Fußgängerschutz stellt die Motorhaube dar. Sie soll so beschaffen sein, dass sie beim Aufprall des Körpers möglichst viel Energie aufnimmt. Dafür wird unter der Haube freier Raum benötigt. Bei aktuellen Fahrzeugen ist jedoch in der Regel der Motorraum bis auf den letzten Kubikzentimeter ausgefüllt. Das hat bisher dazu geführt, dass verschiedene Hersteller Systeme entwickelt haben, welche die Haube bei einer Kollision blitzschnell anheben – zum Teil mit zusätzlichen Airbags versehen – um die vorgegebenen Werte zu erreichen. Der Nachteil dieser Systeme ist der hohe technische und wirtschaftliche Aufwand durch den Einsatz von Sensorik, Steuerung und pyrotechnischen Auslösern sowie ein erhöhter Wartungsbedarf. Außerdem brauchen diese Systeme wiederum zusätzlichen Platz in der Fahrzeugfront. Das führt zwangsläufig dazu, dass Kompromisse im Design gemacht werden müssen.
Die Magna Steyr AG & Co KG aus Graz in Österreich ist ein weltweit führender, markenunabhängiger Entwicklungs- und Fertigungspartner der Automobilhersteller. Das Unternehmen entschied sich, das bereits vorhandene Know-how im Bereich Sandwich-Technologie auf die Entwicklung und Serienfertigung von Fahrzeug-ExterieurTeilen zu übertragen. Am Beispiel einer Faserverbund-Motorhaube wird dies nun erstmals eindrucksvoll zur Schau gestellt. Die Idee war es, eine der ureigensten mechanischen Eigenschaften der verschachtelten Papier-Wabenstruktur zu nutzen: den Aufprallschutz. Prinzipiell handelt es sich dabei um den gleichen Effekt, wie er beispielsweise auch von Stuntleuten genutzt wird, die gestapelte Kartons zum Abbau kinetischer Energie verwenden
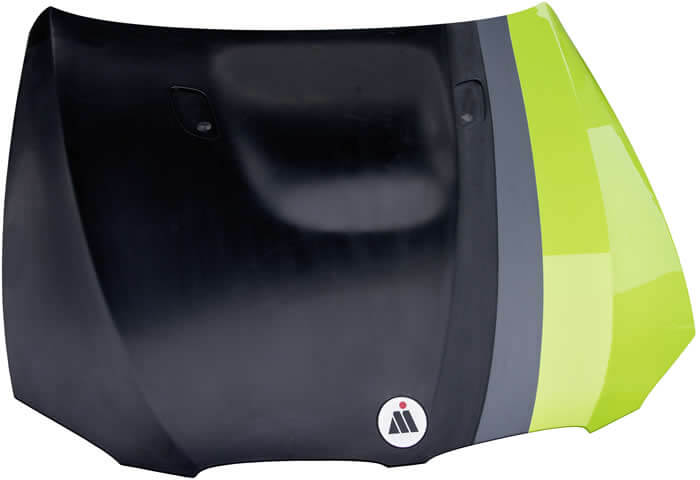
Eine wesentliche Herausforderung stellte dabei die bei Exterieur-Teilen geforderte lackierfähige Class-A-Oberfläche der Motorhaube dar. Die Rühl Puromer GmbH aus Friedrichsdorf gehört zu den weltweit führenden Unternehmen für die Entwicklung und Produktion von PUR-Systemen und GFK-Spezialprodukten. Die Spezialisten haben neben einem auf die Anwendung angepassten puropreg®-System zur Herstellung der Wabensandwich-Trägerstruktur ein purorim®- System auf Basis PUR entwickelt, das – im Reaction-Injection-Molding-Verfahren (RIM) verarbeitet – die geforderte Oberflächengüte sicherstellt und damit die Aufgabenstellung erfolgreich löst.
Bei der Wahl der passenden Misch- und Dosiersysteme für die PUR-Verarbeitung fiel die Entscheidung leicht. Magna Steyr setzt auf PUR-CSM-Verarbeitungsanlagen. Einerseits, weil Hennecke der unangefochtene Marktführer für großserientaugliche Produktionssysteme bei der Herstellung von Leichtbau-PREG-Composites ist und andererseits, weil sich der Automobilzulieferer bei der Verarbeitung von Polyurethan bereits seit vielen Jahren auf die PUR-Spezialisten von Hennecke verlässt.
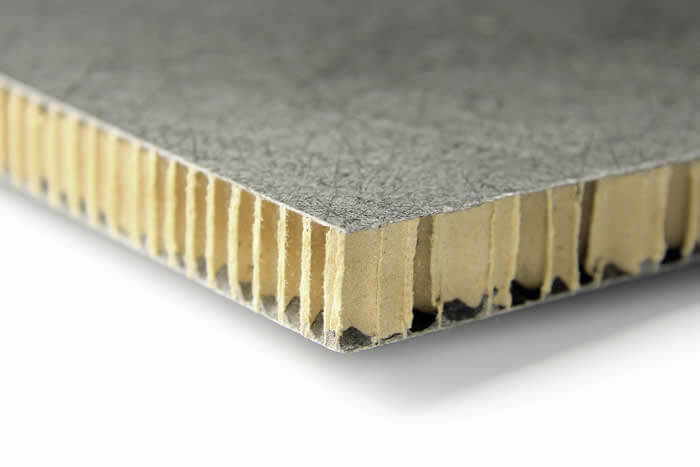
Nach der Entwicklungszeit steht die Serienreife der Motorhaube nun unmittelbar bevor. Vom Prinzip her ähnelt die Sandwich-Bauweise der Haube dabei dem Aufbau eines PREG-Ladebodens für Kofferraum-Systeme. Für die Herstellung der Motorhaube wird ein Wabenkern von oben und unten mit Glasfasergewebe belegt. Um die unterschiedlichen Stauchhärten und die Stabilität, beispielsweise für Scharniere, in der Haube zu erreichen, ist der Wabenkern an den erforderlichen Stellen in speziell verstärkter Bauweise ausgeführt. Im Anschluss folgt der PUR-Matrix-Auftrag im PUR-CSM-Sprühverfahren. Bei diesem patentierten Sprühauftrag werden die Faserhalbzeuge beidseitig mit einem thermisch aktivierbaren PUR-System benetzt. Hierbei ist ein gezielter, stärkerer Materialauftrag in bestimmten Bauteilbereichen möglich. Anschließend wird das Bauteil innerhalb der Form verpresst und ausgehärtet. Als nächster Schritt wird im RIM-Verfahren auf der Außenseite und um die Außenkante der Haube herum die lackierfähige Class-A-Oberfläche hergestellt.
Der Polyurethan-Sprühauftrag stellt eine optimale und dauerhafte Verbindung zwischen Glasfaser und dem Wabenkern her. Das sorgt für eine extrem hohe Stabilität und Drehsteifigkeit. Über die Dicke und den Aufbau des Wabenkerns lässt sich das Crash-Verhalten der Motorhaube definiert einstellen. Gestaltet man die Motorhaube so, dass sie im vorderen Bereich bis zum Kühlergrill hinunter reicht, entspricht auch dieser Bereich den Vorschriften für den Fußgängerschutz und lässt den Designern nahezu sämtliche Freiheiten, den Frontbereich eines Fahrzeugs zu gestalten. Der konstruktive Aufbau beinhaltet noch weitere positive Effekte. Neben dem deutlich geringeren Gewicht hat die Motorhaube durch den Wabenkern sehr gute Dämmeigenschaften. Sie benötigt beispielsweise keine Dämmmatte, auf die herkömmliche Hauben nicht verzichten können. Aber nicht nur die Dämmeigenschaften gegen Lärm sind hervorragend, sondern auch die Wärmeisolierung. Das bringt Vorteile bei der CO2-Bilanz, weil der Motor wesentlich langsamer auskühlt und somit Kaltstarts im Idealfall öfter vermieden werden können.
Die Motorhaube hat die umfangreichen Zulassungstests der Automobilindustrie allesamt bestanden – natürlich auch die neuen Anforderungen an den Fußgängerschutz. Diese neue Bauweise lässt sich zukünftig auch auf viele andere Exterieur-Teile wie Heckklappen, Türen und Dächer übertragen – ein weiterer wichtiger Schritt auf dem Weg zu einer kompletten Leichtbau-Karosserie.
Download - Ausgabe 113 (PDF)
Zur Betrachtung benötigen Sie den Adobe® Reader®, den Sie hier kostenlos herunterladen können.