Hennecke goes to a whole new level online
Next generation of metering machines with IoT connection
Hennecke‘s new FOAMATIC control software grasps the opportunities offered by digitalization – connecting next-generation high-pressure metering machines with the Internet of Things (IoT) to optimize production processes. Under the name FOAMATIC-IoT, Hennecke now offers users outstanding options for increasing efficiency and reducing costs.
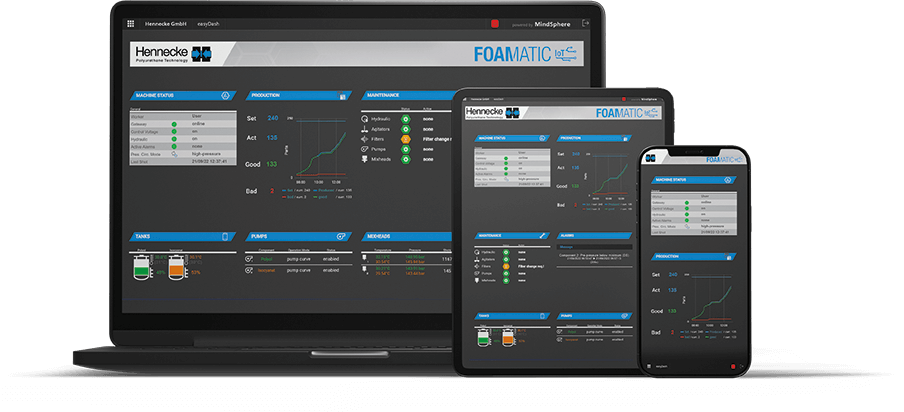
More and more technical devices are connected to the Internet: Who hasn’t forgotten the laundry in the washing machine or not closed the refrigerator door properly? Modern devices report operating states via push messages – making households more effective through digitization while saving valuable energy and much more. These are just some of the ways where the Internet of Things can provide help and support in everyday life. The digitization and networking of devices in specialty mechanical engineering is therefore all the more important and offers numerous new opportunities there: from data analysis to production optimization and predictive maintenance. IoT provides the intelligent connection between people, machines and industrial processes by collecting, storing and analyzing production and process-relevant data. It offers users transparent insights into previously unused amounts of information, which they can harness to make production more flexible, efficient and individualized. Along with the above examples – this offers remarkably practical advantages in day-to-day production applications. Selected metering machines in Hennecke’s Next-Gen series can typically send a push message when the day tank is ready to be refilled or a component needs to be replaced soon.
IoT-ready thanks to FOAMATIC
In order to meet current requirements and future-proof the machine control system, Hennecke has developed the FOAMATIC control software for its Next-Generation metering machines from scratch. FOAMATIC consists of an HMI (Human Machine Interface) – in other words the user interface – and programmable logic controller (PLC). With the FOAMATIC-IoT equipment feature, the prerequisites for important innovations such as WLAN connectivity and IoT connectivity have also been integrated to not only facilitate operation, but also enable advanced digital data storage and evaluation. Best of all, hardware and software IoT integration for information and evaluation of relevant machine data for the FOAMATIC-IoT functional range is already integrated as standard on selected metering machines. This means that customers can also decide at a later date whether they want to take advantage of the digital world at any time.
Simple operation via graphical user interface
The HMI impresses with its modern, graphic design and intuitive operation. Users always have all the relevant data in view – a well thought-out 3-click menu quickly taking them to any desired detailed menu with three clicks. Besides this, the metering machine can not only be controlled via the integrated 12-inch display, but can also be networked with other devices via WLAN. This means that it can also be operated via a smartphone or tablet – or the data can be visualized on a large monitor with network connection. In the control system, special emphasis was placed on integrating the Hennecke Blue Intelligence System for more efficient use of raw materials and energy. This includes numerous intelligent functions such as stand-by timers, innovative pump controller, lead times, temperature control and much more – allowing the relevant settings to be customized to perfectly suit individual needs.
IoT data offers unimagined depth of information
A major advantage is the large amount and depth of information, as numerous production data from the sensor systems of the high-pressure metering machines can be collected and securely stored on a cloud platform. The storage solution means that not only information on the last 100 shots can be retrieved, as before, but also data on the entire production period – thereby providing a much more accurate picture of production and products, machine availability and processes, energy and material usage, and maintenance and servicing. Further support is provided by instant notifications with which the machine can communicate specific operating conditions to the operator via push messages. “Storage in the cloud makes the entire production process more transparent and reliable. All data can also be accessed and analyzed independently of time and place. This allows production managers to gain a clear overview of the machines at any time via the dashboard – giving them access to both live data from current production and all previous production data,” reports Alexander Peters, Director Engineering & Development at Hennecke and responsible for the development of the software. That’s an enormous advantage – not only for companies with several production sites. In addition, the system is future-proof and prepared for the later use of AI and machine learning.
All information available anytime and anywhere
The IoT dashboard, i.e. the user interface, displays all current and historical production data and makes it comparable and analyzable. This typically includes raw material consumption, energy consumption, tank levels, maintenance intervals or good and bad parts counters as well as any fault alarms. The upshot: production processes can be monitored, optimized and efficiently streamlined. All process data is continuously transferred to the cloud and can be selected and compiled using various filters. This allows more reliable planning – for instance when the data indicates that filters need to be cleaned or replaced. That helps to reduce machine downtime and optimize spare parts management. “A major advantage is that all data can be linked and correlated. This is an important step towards predictive maintenance,” says Jens Winiarz, Senior Director Sales Metering & Composites.

Data security has top priority
Hennecke Cloud Services were developed with the highest security standards for sensitive user data in mind. A leading German company was won as a partner, on whose certified and proven infrastructure the platform is based with an AWS backbone. Data storage is based on the General Data Protection Regulation (GDPR), processing is subject to the ISO 27001 cybersecurity standard, and access management meets the requirements of the National Institutes of Standards and Technology (NIST). “It’s vitally important for the customer to remain sole owner and user when it comes to the data,” Alexander Peters affirms. “The secure cloud system gives the user sole access to their data at all times via the network connection – no one else can see or retrieve it.”
Free trial access for users of the HIGHLINE MK2 and TOPLINE MK2
All new generation high-pressure metering machines from the HIGHLINE MK2 platform onwards are prepared for the use of FOAMATIC-IoT. Customers benefit from user-friendly and intuitive application. Hennecke has a special offer ready for the market launch of the new IoT world: For a period of six months, customers can test the IoT offering themselves completely free of charge and receive unlimited access to all currently available IoT functions. “What’s more, we’re continuously expanding the spectrum and developing further applications and new packages, for example in the area of predictive maintenance or ESG,” reports Christian Zahn, who is responsible for Customer Value Service at Hennecke.
In short, the FOAMATIC offers the user numerous new functions and an innovative IoT connection in addition to a new intuitive machine control with WLAN integration. The new machine generation is fit for Industry 4.0 and offers unprecedented optimization possibilities. Continuous data acquisition and storage on the secure cloud platform provide new insights into production processes and thus numerous analysis options. This not only improves production quality, but also enables savings in raw material and energy consumption at the same time – a major benefit for all Hennecke customers.
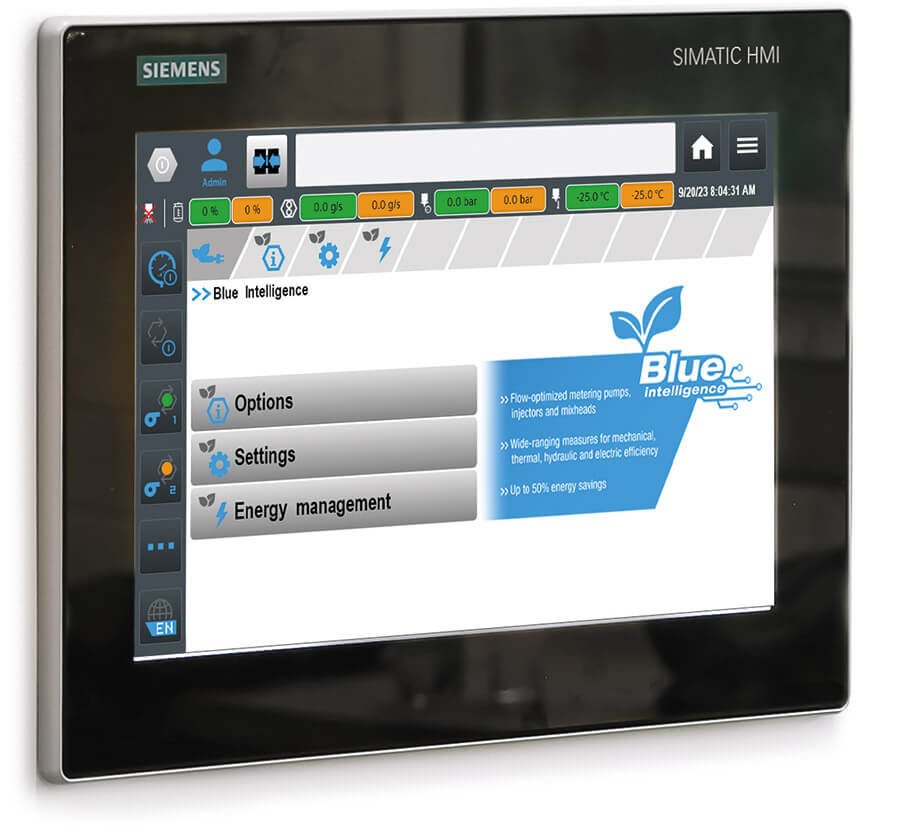
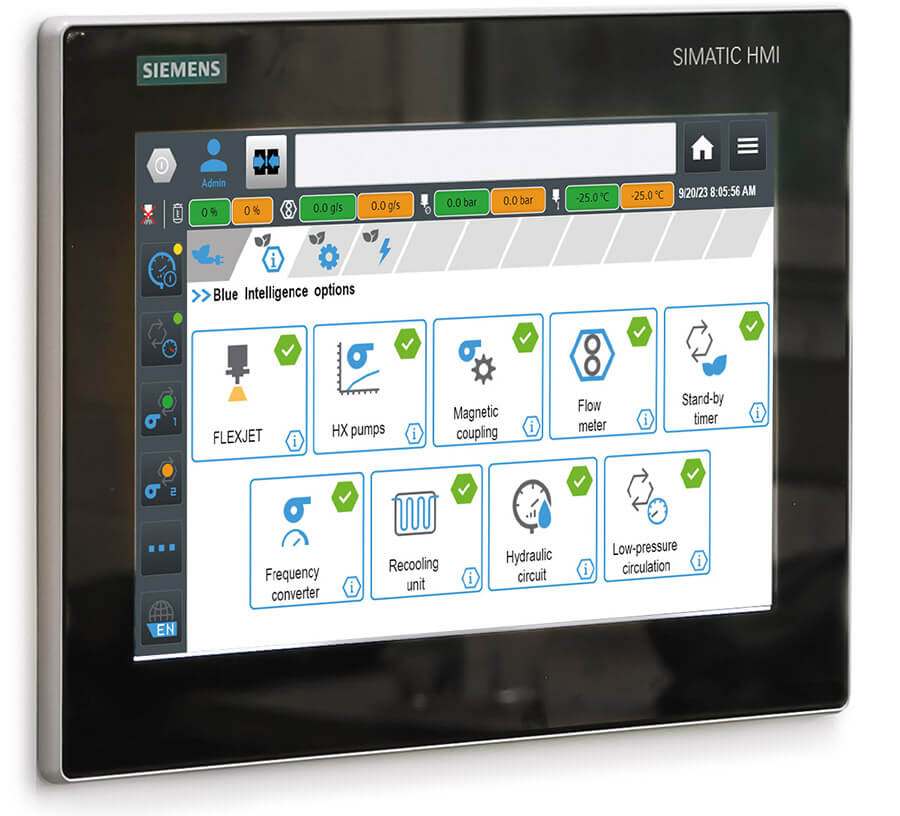